
Research of iron ore grinding in a vertical-roller-mill
One reason is the dry in-bed grinding principle. Results of extensive test works with two types of magnetite iron ores in a Loesche VRM are presented here. Within these test works, mill parameters like grinding pressure, separator speed and dam ring The results show that increasing the grinding pressure increases the production rates, but this trend levels out at pressures higher than 65% of the maximum Research of iron ore grinding in a vertical-roller-mill
احصل على السعر
(PDF) Research into the crushing and grinding
Research into the crushing and grinding processes of iron ore with its simultaneous effect by mechanical load and electric field of ultra-high frequencyPublished: 28 May 2020 Investigation on Iron Ore Grinding based on Particle Size Distribution and Liberation Harish Hanumanthappa, Harsha Vardhan, Govinda Raj Investigation on Iron Ore Grinding based on Particle Size Distribution
احصل على السعر
THE EFFECTS OF PROCESS VARIABLES ON THE GRINDING OF IRON ORE
The results of the analyses clearly show that using a sieve of +180µm and its bottom-180µm, the best time for grinding 0.5kg of Itakpe iron ore with 3kg of Iron ore pellet production requires a fine mineral particle distribution to lead to good agglomerate densification, a smooth surface, and controlled growth in the Development of a Novel Grinding Process to Iron Ore
احصل على السعر
Development of a Novel Grinding Process to Iron Ore
pected after only a single grinding step [3, 11]. The HPGR pellet feed product can deliver the BSA within the needs required for pelletizing, but the size fraction This chapter reviews current iron ore comminution and classification technologies and presents some examples of flowsheets from existing operations. New Comminution and classification technologies of iron ore
احصل على السعر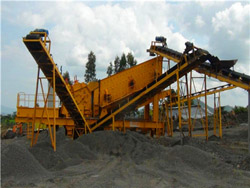
Study on the Characterisation and Processing of
The dry and simultaneously iron-free ore grinding by VRM or high-pressure grinding roll (HPGR) could be considered as an advantage for the further selective flotation [49]. Phosphoric acid estersSince grinding constitutes a bulk of operating cost in mineral processing,it has become necessary to take recourse to efficient grinding machines. Most common Potential of High-Pressure Grinding Roll (HPGR) for Size
احصل على السعر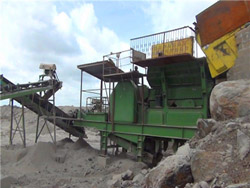
Comminution and classification technologies of iron ore
Most of the high-grade hematite iron ores are typically subjected to simple dry processes of crushing and classification to meet the size specifications required for direct shipping ore (DSO). This involves multistages of crushing and screening to obtain lump (−31.5 + 6.3 mm) and fines (approximately −6.3 mm) products.The modification of magnetic properties of siderite ore by microwave energy resulted in increasing the efficiency of their magnetic separation. Pre-treatment in a microwave oven with maximum power of 900 W of weakly paramagnetic ore (25.1% Fe, 9.6% SiO 2) was realized with the samples (100 g) of iron spathic ore of particle size Iron ore grindability improvement by microwave pre-treatment
احصل على السعر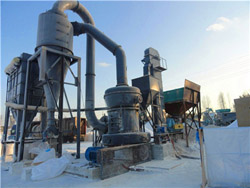
(PDF) Iron ore pelletization ResearchGate
Arrium Australia 0.810 0.810 0.440. 440 Iron Ore. The pelletizing process involves the preparation of ra w materials; the proportioning. and mixing of raw materials; the formation, preheating, andIron ore tailings (IOTs) are a form of solid waste produced during the beneficiation process of iron ore concentrate. In this paper, iron recovery from IOTs was studied at different points during a process involving pre-concentration followed by direct reduction and magnetic separation. Then, slag-tailing concrete composite admixtures Minerals Free Full-Text Recovering Iron from Iron Ore
احصل على السعر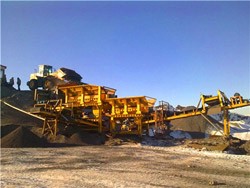
ball mill for iron ore LinkedIn
A ball mill is a grinding machine that is used to grind and blend materials for use in mineral processing, such as ores, pyrotechnics, ceramics, and paints. For iron ore, the grinding process isprises but also increases the ore grade and lessens the grinding cost and tailings production. However, long-term research on intelligent ore strong anti-interference capability, and high speed of these factors guarantee the separation efficiency of intelligent ore sorting equipment. Color ore sorter, X-ray ore transmission sorter, dualA review of intelligent ore sorting technology and
احصل على السعر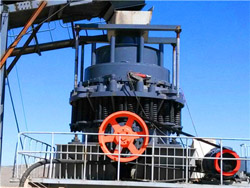
High-Pressure Grinding Roller Presses for Minerals
First HPGR delivered for iron ore pellet feed 2014 New HPGR machine sizes introduced ranging from 1.0m to 2.54m roller diameter 2018 More than 880 roller presses supplied to 68 countries destined for grinding. The machines can be equipped with different roller surfaces. They are connected to the centralThe grinding method and its associated parameters strongly affect the physical properties of the iron ore concentrate. Ball milling (BM) and High-pressure grinding rolls (HPGR) are commonly employed for grinding iron ore concentrate [18], [19], [20]. In BM, the particle size was decreased by impact and attrition breakage, whereas size Mechanism of magnetite iron ore concentrate morphology
احصل على السعر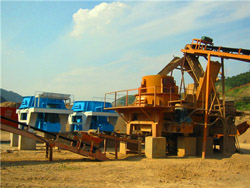
Beneficiation of Magnetically Separated Iron-Containing
size with 52 percent average iron grade was crushed and ground to ( 0.1) mm size. The required quantity of 60 percent iron concentrate was produced by a multi-stage cleaner separation using the laboratory magnetic separator being studied. We note that this ore is difficult to process, and a finer grinding is required to increase Fe grade. 2.1 Energy. Rock drilling, blasting, and comminution (crushing and grinding) consume a vast amount of energy in hard rock mines. As mentioned in Sect. 1, statistics from hard rock mines indicates that drilling and blasting consumes 2% and comminution does 53% of the total energy input in the whole production chain from Reduction of Fragment Size from Mining to Mineral
احصل على السعر
Iron Ore Processing, General SpringerLink
Iron ore handling, which may account for 20–50% of the total delivered cost of raw materials, covers the processes of transportation, storage, feeding, and washing of the ore en route to or during its various stages of treatment in the mill.. Since the physical state of iron ores in situ may range from friable, or even sandy materials, to monolithic lumps in total iron ore production has been about T he Iron Ore Crusher & Ball Mil wet Grinding unit will be Ball mill (300 TPH), Balling Disc (140 TPH X 6), Indurating machine (600(PDF) Iron Ore Pelletization Technology and its
احصل على السعر
Iron ore pelletization ScienceDirect
Abstract. A brief introduction to recent developments in iron ore pelletizing is provided in this chapter, including the world output of fired pellets, pellet production processes, preparation of pellet feed, inorganic and organic binders, and new additives. Throughout the chapter, the authors have used a difficult pellet feed, that is, aBentonite, an inorganic binder, has been the main binder used in the iron ore pelletizing. process since the beginning of pellet production in the 1950s. Bentonite promotes the forma-. tion of(PDF) Iron Ore Pelletizing Process: An Overview ResearchGate
احصل على السعر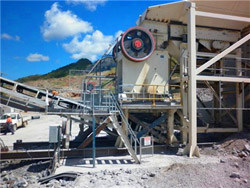
Introduction: Overview of the global iron ore industry
As evident in Fig. 1.2, the world’s production of usable (processed) iron ore has increased from about 970 million tons in 2000 to 2.45 billion tons in 2019. Australia is the largest iron ore producing country, producing approximately 919 million tons of usable ore in 2019, equivalent to about 37% of the world’s iron ore production.Contribute to crush2022/mill development by creating an account on .mill/sbm ball mill for grinding iron ore crusher screen
احصل على السعر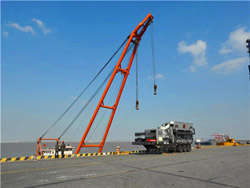
Investigation on Iron Ore Grinding based on Particle Size Distribution
The feed samples of X, Y, and Z iron ores were ground in the BBM (ball mill refers to a BBM of size 300 mm × 300 mm with smooth liners) to identify the PSD, BWI, and RT of each ore. Grinding experiments were conducted according to Bond’s standard test procedure [].For each iron ore sample, the RT taken to produce 250% circulating The results of the analyses clearly show that using a sieve of +180µm and its bottom-180µm, the best time for grinding 0.5kg of Itakpe iron ore with 3kg of grinding media and a mill speed of 92THE EFFECTS OF PROCESS VARIABLES ON THE GRINDING OF IRON ORE
احصل على السعر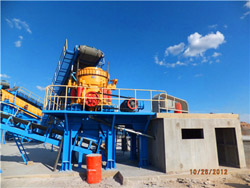
From Micro to Nano: Grinding Natural Magnetite Ore for
A high iron content of up to 72.4% makes it very attractive as a raw material for steel production and the electric industry, as the average global spot price for iron ore products is approx. USD 117 per ton (end 2022) . However, during processing, the initial natural properties—especially magnetism—are lost.The chemical composition of the selected iron ore samples is shown in Table 2. In the crushing machine, all the three iron ore samples were crushed to − 3 mm and analyzed for the desired P 80 passing (− 150 μm) and percentage of hematite liberated in the three feed iron ore samples. The 150-μm feed size fractions were selected toEstimation of Grinding Time for Desired Particle Size
احصل على السعر