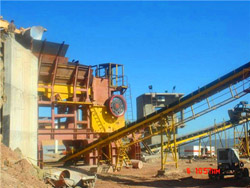
Analysis of hold-up and grinding pressure in a spiral jet
Here, the spiral jet mill is studied using a four-way coupled CFD-DEM scheme [20–23] to analyse the effect of grinding pressure and hold-up on particle behaviour and the fluid flow field. The basis for the mill is the Hosokawa Micron AS-50 (Runcorn, UK).There is a large pressure drop in the classifier zone. The flow is accelerated in this zone, due to the constriction, but the pressure drop is not recovered, Effect of grinding nozzles pressure on particle and fluid flow
احصل على السعر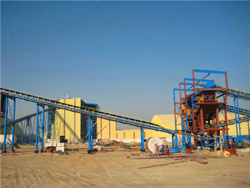
Analysis of grinding in a spiral jet mill. Part 1: Batch grinding
We studied by means of experiments, the influence of grinding pressure, holdup and milling time on the performance of a spiral air jet-mill operating in a batch The fixed components which include the grinding media, air inlet system, mill and classifier internal areas are responsible for the larger fraction of the pressure Steady state inferential modeling of temperature and pressure in an air
احصل على السعر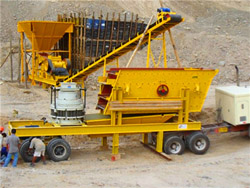
Effect of grinding nozzles pressure on particle and fluid flow
Introduction Mechanistically simple in its design, the spiral jet mill is the equipment of choice for many industries that process fine powders. The mill has no A spiral jet mill was simulated using Discrete Element Method modelling and Computational Fluid Dynamics. The particle behaviour and fluid motion were analysed as Analysis of hold-up and grinding pressure in a spiral jet mill
احصل على السعر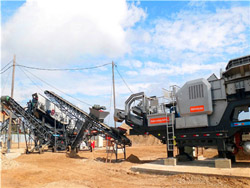
Analysis of grinding in a spiral jet mill. Part 1: Batch grinding
We studied by means of experiments, the influence of grinding pressure, holdup and milling time on the performance of a spiral air jet-mill operating in a batch The effects of grinding pressure and holdup on the normalized mean size of product and mill material are shown in Fig. 11 for a fixed time of grinding. The particle Analysis of grinding in a spiral jet mill. Part 2: Semi-batch grinding
احصل على السعر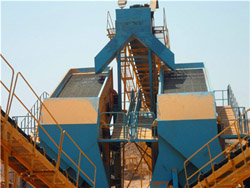
Chapter 10 Selection of Fine Grinding Mills ScienceDirect
The fine grinding mills are classified often into five major groups: (1) impact mills, (2) ball media mills, (3) air jet mills, (4) roller mills, and (5) shearing attrition mills sbm differential pressure and grinding in a raymond millMining Industry: What’s the difference between Raymond, Telephone:0086 371 67666667 Contact Person:MrZhao 0086 13523465141 Fax:00086 371—68125111 Raymond mill and high pressure micro powder mill are commonly used milling equipment,mainly used for sbm/sbm differential pressure and grinding in a raymond mill
احصل على السعر
Effect of grinding nozzles pressure on particle and fluid flow
There is a large pressure drop in the classifier zone. The flow is accelerated in this zone, due to the constriction, but the pressure drop is not recovered, and the air flows up over the classifier ring and proceeds to exit the mill to atmospheric pressure. Download : Download high-res image (197KB) Download : Download full-size image; Fig. 5.The fixed components which include the grinding media, air inlet system, mill and classifier internal areas are responsible for the larger fraction of the pressure drop. The variable components include the effect of raw coal and pulverized fuel i.e. the concentration of the pulverized fuel that is suspended within the air stream affects theSteady state inferential modeling of temperature and pressure in an air
احصل على السعر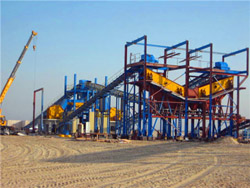
Stationary inlet for ball mills FLSmidth
the mill to ensure proper ratio of mill feed and air is passed in to the mill. The feed chute is lined with bolted-on wear plates slopes down through the air duct to the mill inlet opening. The inlet can easily be prepared for internal water injection in inlet end if needed. We also offer inlet prepared for drying gases from hot gas generatorAn increase in mill demand would result in an increase in air flow rate in order to achieve the desired pulverized fuel flow to the boilers. It is. Conclusions. This paper has shown that the temperature of the fuel stream at the mill outlet and the pressure drop in the mill circuit can be predicted fairly well by an energy balance model.Steady state inferential modeling of temperature and pressure in an air
احصل على السعر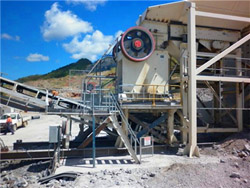
Preheater In Cement Plant Cyclone Preheater AGICO
Cyclone preheater, also known as suspension preheater, is the main cement equipment commonly used in the new dry process cement production line. It is the main gas-solid reaction unit of the cement raw meal pre-decomposition system, which makes full use of the high-temperature exhaust gas discharged from the kiln tail and the high-temperature flue A gas speed of 4-5 m/s exit drop-out box and a mill speed of 1.5 m/s generally gives a blaine of the aspirated dust of ~3000 cm²/g (Beat Stocker). A gas speed of 2-2.5 m/s exit drop-out box (mill speed 0.5 m/s) gives a blaine of ~4000 (Beat). 5.2.1.4 Discharge Duct Typically we find that the discharge vent duct is sized for about 10 to 15 1 Ball Mills 1 PDF Mill (Grinding) Gases Scribd
احصل على السعر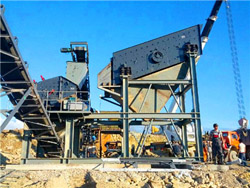
crusher/sbm pressure high pressure grinding roll instruction
Contribute to yunan88/crusher development by creating an account on .Stronger pellets were produced from the HPGR products, with a lower binder requirement (Ehrentraut and Rao, 2001) The pellets generally are more uniform in size; for example nearly 90% of the pellets were between 8.0 and 12.5 mm, compared to about 55% in case of the ball mill products.Therefore a higher loading on the grate may Pellet feed grinding by HPGR ScienceDirect
احصل على السعر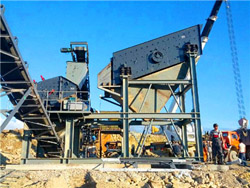
Jet Milling of Low-Density Products PCI
Deagglomeration Makes High Grinding Pressure Unnecessary. To disperse such bulk materials, lower grinding energy levels are enough in most cases. As a result, a high grinding pressure is no longer a “must” for the jet milling process. The higher the grinding pressure, the lower the efficiency of compressed air generation (Figure 1).In this work one focus is on the grinding process in the spiral jet mill with different milling nozzle numbers but constant mass flow rate of the total air supply. The differences between the flow conditions of solid particle-loaded (barium sulfate micro particles) and solid particle-unloaded (liquid diethylhxyl sebacat tracer droplets) spiralVisualization of flow conditions inside spiral jet mills with
احصل على السعر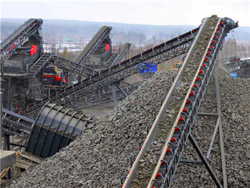
Analysis of grinding in a spiral jet mill. Part 2: Semi-batch grinding
A schematic view of the spiral jet mill used in the experiments is shown in Fig. 1, which includes the dimensions. Fig. 2 shows a schematic view of all elements of the apparatus. Air is supplied from a large capacity compressor (capacity: 225 l, pressure: 7 bar, flow rate: 18 cfm) through Ball valve-0, a moisture separator and a pressure regulator to A 1.5 mio t/a cement plant is having a closed circuit ball mill for cement grinding: The mill has been − The low vent volume through the bag filter is mainly due to very high pressure drop across (180-200 mmWG). The actual flow measured is only 4% of the total separator air. • Mill was crash stopped for collection of chamber samplesPROCESS DIAGNOSTIC STUDIES FOR CEMENT MILL
احصل على السعر
Performance of the vertical roller mill in a mineral processing
Vertical roller mill products of three target grinds, typical to primary, secondary and tertiary grinds in PGM circuit, were generated with the VRM operated in the standard airflow mode, with the internal dynamic air classifier, for a variety of grinding pressures (an online control used for maintaining product quality), and dam ring heights (aThe grinding process is carried out on the surface of the polyurethane material to remove the damage on the surface of applicator (Roller) and because of which the air pollution takes place. We have designed this dust collection machine for collecting the dust of polyurethane material which is removed during the grinding operation.Design and fabrication of cyclone dust collector for industrial
احصل على السعر
FABRICATION, TESTING AND EVALUATION OF A DUST
SYSTEM FOR SMALL-SCALE SPICE GRINDING MILLS D. A. N.Dharmasena 1., D. N. Power required for blowing air = Pressure drop x Air Velocity x Cross sectional area of duct (1)attrition where pressure has a less marked effect. 3.1.3. Fluidised bed air jet mill with integral classifier This mill has a cylindrical grinding chamber of diameter 100 mm fitted in its lower part with a cone having three 2 mm air jets pointing at each other. Fragmented particles are carried to a bsquirrel cageQComparison of Various Milling Technologies Accueil
احصل على السعر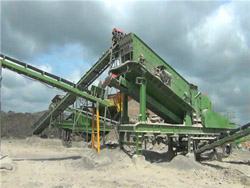
Study on the Effect of Grinding Pressure on Material
Passive grinding is a new rail grinding strategy. In this work, the influence of grinding pressure on the removal behaviors of rail material in passive grinding was investigated by using a self-designed passive grinding simulator. Meanwhile, the surface morphology of the rail and grinding wheel were observed, and the grinding force and 2.2 Grinding Studies. Two kinds of mills, BBM and LBM, were used to achieve the desired P 80 passing percentage of 150 μm with an acceptable range of hematite liberation (> 75%) at optimum grinding time. The BBM is a standard ball mill having a length and diameter of 300 mm × 300 mm with smooth liner as shown in Fig. 2.A Estimation of Grinding Time for Desired Particle Size
احصل على السعر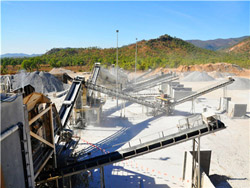
High Speed Hammermills For Fine Grinding: Part 5 Feeders, Air
A good rule of thumb for the amount of air required to assist product and control dusting is 1.25- 1.50 CFM/In2 of screen area. Pressure drop across the mill may range from 2-5" W.C., depending on system operating conditions. In order to make an air assist system work, several items must be considered including the air flow into the mill, paths
احصل على السعر