
Developments in iron ore comminution and classification
Abstract Hematite and magnetite, the two predominant iron ores, require different processing routes. High-grade hematite direct shipping ores (DSOs) generally The primary crushers are four mobile roller crushers (PF 200–9500) with the feed size between 0.80 m to 1.20 m and a maximum product size of 0.35 m; the crushed ore is transported through a system A Mine-to-Crusher Model to Minimize Costs at a
احصل على السعر
Tribological study of fourth-stage crusher coatings applied in an iron
In the present work, a tribological study was carried out on concave and mantle linings of iron ore microhardness. 1. Introduction. In iron ore processing plants, crushers are used There are several types of primary crushers, including: Gyratory Crushers Jaw Crushers Hammermills Horizontal Shaft Impact Crushers Sizers Roll Crushers Cone Crushers Feeder-Breakers Gyratory What Type of Crusher Is Best for Primary
احصل على السعر
Gyratory and Cone Crusher ScienceDirect
The larger crushers are normally known as primary crushers as they are designed to receive run-on-mine (ROM) rocks directly from the mines. The gyratory Analysis of iron ore crusher. The importance of iron ore crushing process; Before dry selection, the lean iron ore requires millimeter-scale fine crushing by the fine crusher. If the particle size of the iron ore Challenges and opportunities in the iron ore
احصل على السعر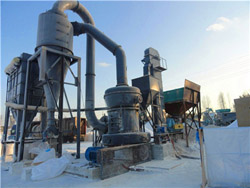
Application of analytical hierarchy process to selection of primary
1. Introduction The primary crusher selection is the key to the success of the mining, quarry or industrial mineral operation that involves the reduction in the size of An optimal crushing process reduces the ore to a desired size more efficiently, economically and safely. The high-capacity, reliable and energy efficient crushing solutions deliver Crushing TON
احصل على السعر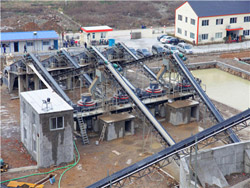
(PDF) Design of Comminution Circuit for Optimum
A Possible Comminution Circuit for the Iron Ore Plant Since the receiving Ajaokuta blast furnace requires coarse concentrate for efficient operation, the fine ore material stored in bins may beThe feed samples of X, Y, and Z iron ores were ground in the BBM (ball mill refers to a BBM of size 300 mm × 300 mm with smooth liners) to identify the PSD, BWI, and RT of each ore. Grinding experiments were conducted according to Bond’s standard test procedure [].For each iron ore sample, the RT taken to produce 250% circulating Investigation on Iron Ore Grinding based on Particle Size Distribution
احصل على السعر
iron ore crushing plant setup cost in nigeria LinkedIn
The primary crushers are engineered for high capacity and efficiency, capable of breaking down large chunks of raw iron ore into manageable sizes. Secondary crushers and screening equipmentThe quality of Indian iron ore resources is generally good with high iron content and high percentage of lumpy ore. More than 85% of the hematite ore reserves are of medium- to high-grade (+62% Fe) and are directly used in blast furnace and in direct-reduced iron (DRI) plants in the form of sized lump ore, agglomerated sinter, and Iron ore beneficiation: an overview ScienceDirect
احصل على السعر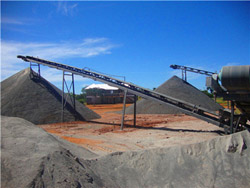
Types of Crushers: What You Need to Know Machinery
The Gates’ gyratory crushers were preferred by the mining industry for almost two decades until the turn of the century, circa 1910, when Blake’s jaw crushers saw a resurgence in popularity. The demand for large-mouthed jaw crushers skyrocketed as the industry began to understand their potential as primary crushers in rock quarries.Sulfur and copper can be removed from iron ore through the beneficiation process, which typically includes a combination of crushing, milling, magnetic separation, flotation and gravity separation.How can sulfur and copper be removed from iron ore?
احصل على السعر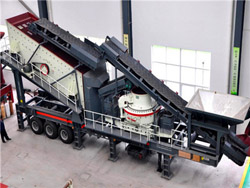
McLanahan Mineral Sizers
McLanahan Mineral Sizers are designed to process a variety of materials, including copper, iron ore, gold, nickel, lithium/spodumene, coal, potash, phosphate and other hard rock and soft, non-coal minerals. They can be used in primary or secondary crushing applications. They excel at handling feeds with clays and other contaminants that areSelection of crusher required a great deal of design based on the mining plan and operation input. Selection of the best primary crusher from all of available primary crushers is a Multi-Criterion Decision Making (MCDM) problem.In this paper, the Analytical Hierarchy Process (AHP) method was used to selection of the best primary crusher for Application of analytical hierarchy process to selection of primary
احصل على السعر
How iron ore is crushed? LinkedIn
In conclusion, iron ore is crushed through a three-stage crushing process involving primary, secondary, and tertiary crushers. The crushing process reduces the size of the ore particles, making itUsing Jaw crusher in Primary Crushing: In the primary crushing of iron ore, Aimix, a professional supplier of any kind of crushers, not only have the best iron ore crusher price but also has the best quality. PE400-600-jaw-crusher. Model: PE-400*600 Feed opening size(mm): 400*600 Max.Feeding size(mm):340 Adjusting range of discharge openingOre Crusher PE Series Jaw Type Ore Crusher AIMIX
احصل على السعر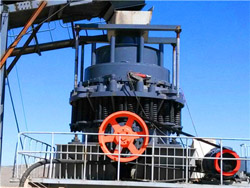
What Type of Crusher Is Best for Primary
Primary crushers reduce large run-of-mine material, such as rocks and ore lumps, into smaller sizes for further processing downstream, whether that be transport to additional crushers or to a wet In the present work, a tribological study was carried out on concave and mantle linings of cone crushers used in the fourth-stage crushing process of an iron ore processing plant. Initially, an analysis of the characteristics over the lifetime of the applied coatings was carried out, and samples of the parts that suffered the most critical wearTribological study of fourth-stage crusher coatings applied in an iron
احصل على السعر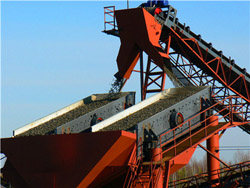
Gyratory Crusher an overview ScienceDirect Topics
Gyratory and Cone Crusher. In Mineral Processing Design and Operations (Second Edition), 2016. 5.1 Introduction. Gyratory crushers were invented by Charles Brown in 1877 and developed by Gates around 1881 and were referred to as a Gates crusher [1].The smaller form is described as a cone crusher. The larger crushers are normally known as primary The main functions of a crusher include: 1.Reduction of size: Crushers reduce the size of larger solid materials into smaller pieces, making it easier to handle. 2.Breaking down materialsWhat is the functions of crusher LinkedIn
احصل على السعر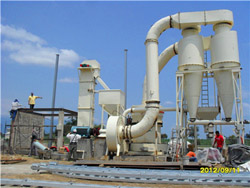
Jaw Crusher VS Cone Crusher (A Comparison From 7 Points)
Jaw crushers: The first choice for primary crushing The jaw crusher is popular because it crushes big rocks into smaller sizes easily. Thus, it proves itself as an effective primary crusher in aggregate, mining, recycling, and concrete industries. While the cone crusher is more suitable for hard rocks and ores, such as iron ore, graniteDiscover the key differences between primary and secondary crushers, their advantages and disadvantages, and the factors to consider when choosing between them. and iron ore. Roll crushers: These crushers use compression force to crush the material. They are designed to handle soft to medium-hard materials such as coal, Primary vs. Secondary Crushers: Understanding the
احصل على السعر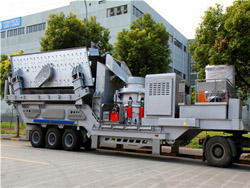
Primary Crusher Selection & Design 911 Metallurgist
Primary Crusher Selection & Design.,degradability and it being prone to dusting or not. The crusher capacities given by manufacturers are typically in tons of 2,000 lbs. and are based on crushing limestone weighing loose about 2,700 lbs. per yard3 and having a specific gravity of 2.6. Wet, sticky and extremely hard or tough feeds will tend toHere are the common processes used for iron ore beneficiation: 1.Crushing and Grinding: The ore is first crushed into smaller pieces by primary crushers. It is then ground to a fine powder in aWhat are the processes of iron ore beneficiation? LinkedIn
احصل على السعر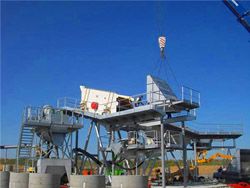
Challenges and opportunities in the iron ore crusher market
Characteristics of global iron ore resource distribution. The global iron ore resources are very abundant, and the long-term supply can be guaranteed. The global iron mine reserves increased from 232 billion tons in 1996 to 370 billion tons in 2006, an increase of 59.5% in 10 years.Option 2 has an additional grinding and magnetic separation stage compared to Option 1 and is considered to be simple for design and operation. The final milling stage is carried out using energy-efficient stirred mills. Steel grinding media usage significantly increases the operating cost. Option 3.Eco-efficient and cost-effective process design for magnetite iron ore
احصل على السعر