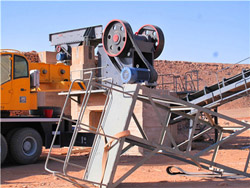
(PDF) Grinding in Ball Mills: Modeling and Process
A ball mill is a type of grinder widely utilized in the process of mechanochemical catalytic degradation. It consists of one or The energy consumption of ceramic medium stirring grinding was calculated, and a feasibility evaluation was conducted on the ball mill, which provided a Energy conservation and consumption reduction in grinding operations
احصل على السعر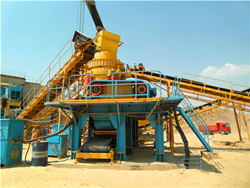
Ceramic Grinding Kinetics of Fine Magnetite Ores in the Batch Ball Mill
Ceramic grinding is a grinding process that uses ceramic balls instead of steel balls as the grinding medium of ball mills. The crystal structure of a ceramic ball Ceramic balls as media can reach twice the specific surface area of steel balls with the same total weight, which provides a strong theoretical support for the application of ceramic balls in Effect of Slurry Concentration on the Ceramic Ball
احصل على السعر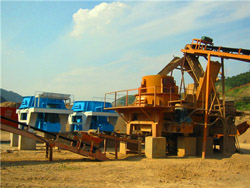
Process of fine milling for ceramic materials ScienceDirect
1. Processing of technical ceramics by wet mechanical beneficiation. 0921-5093/89/$3.50 Elsevier Sequoia/Printed in The Netherlands ticles and produce a slip or a Introduction to Ceramic Grinding Balls. Ceramic balls have been used in grinding operations since the 1980s, however, their use was discontinued due to failures and lost productivity in ball mills.Welcome to Ceramic Grinding Ball CGB
احصل على السعر
Ceramic Grinding Kinetics of Fine Magnetite Ores in the
in magnetite processing, we propose the use of ceramic grinding in the secondary ball mill. Ceramic grinding is a grinding process that uses ceramic balls PDF Results of studies on the determination of ceramic body grinding kinetics in a ball mill with reference to the effect of the number of grinding Find, read and cite all the research you(PDF) MODELLING OF COMMINUTION RATE OF
احصل على السعر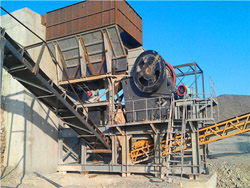
Ball Mills 911 Metallurgist
CERAMIC LINED BALL MILL. Ball Mills can be supplied with either ceramic or rubber linings for wet or dry grinding, for continuous or batch type operation, in sizes from 15″ x 21″ to 8′ x 12′. High density ceramic linings of uniform hardness male possible thinner linings and greater and more effective grinding volume.As shown in Figure 4, the breakage rate fluctuated between 0.17 min −1 and 0.23 min −1, which is in proximity to the steel ball grinding, with the highest value of 0.224 min −1 for −0.425 + 0.300 mm and the lowest value of 0.165 min −1 for −0.150 + 0.106 mm. Figure 4. Breakage rate function of ceramic ball grinding with the sameCeramic Grinding Kinetics of Fine Magnetite Ores in the Batch Ball Mill
احصل على السعر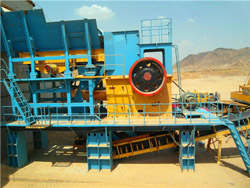
A comparative analysis of steel and alumina balls in fine
Fig. 2 shows the timewise evolution of the cumulative PSD experimentally obtained from the laboratory batch ball mill with different single ball sizes (i.e., d B = 20, 30, and 40 mm) using steel balls and alumina balls. As milling progressed and finer particles were generated by breakage, the PSD shifted to the left monotonically even in the fine In Figure 11b, when compared w the 25% charge volume of 12 × 12 mm cylpebs, it only demands that the ratio of the m of ceramic balls to cylpebs be 0.77:1, and a charge volume larger than 38.5% (1The first attempt of applying ceramic balls in industrial tumbling mill
احصل على السعر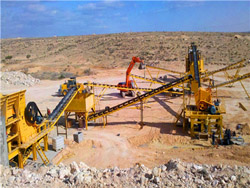
Ball milling: a green technology for the preparation and
Ball milling is a simple, fast, cost-effective green technology with enormous potential. One of the most interesting applications of this technology in the field of cellulose is the preparation and the chemical modification of cellulose nanocrystals and nanofibers. Although a number of studies have been repo Recent Review Articles Nanoscale Advances Most Popular Grinding represents the most energy-intensive operation in a mineral processing plant, accounting for 60% of the total energy consumption. [2,3]. In order to reduce the energy consumption in magnetite processing, we propose the use of ceramic grinding in the secondary ball mill. Ceramic grinding is a grinding process that uses Ceramic Grinding Kinetics of Fine Magnetite Ores in the
احصل على السعر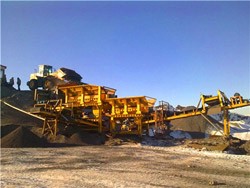
Energy-Efficient Technologies in Cement Grinding IntechOpen
The energy consumption of the total grinding plant can be reduced by 20–30 % for cement clinker and 30–40 % for other raw materials. The overall grinding circuit efficiency and stability are improved. The maintenance cost of the ball mill is reduced as the lifetime of grinding media and partition grates is extended. 2.5.The best ball mills, however, enable you to achieve the desired product quality quickly and e ciently, with minimum energy expenditure. That’s what the FLSmidth ball mill is designed to do with the added benefit of high flexibility. You decide whether to operate the mill in open or closed circuit, with or without a pre-grinder.Ball mill Superior cement quality, More fl exibility, higher
احصل على السعر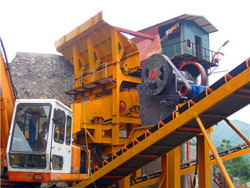
An innovative approach for determining the grinding
1. Introduction. Grinding operation is used extensively in the industry of beneficiation, metallurgy, chemical engineering, and electric power. Assisted by the impact and abrasion between media (steel ball, steel rod, gravel, ceramic ball) and ore, the grinding operation reduces the particle size in the mill [[1], [2], [3]].To produce the qualified size The ceramic body was ground at changing ball composition. Mass fractions, ball sizes and the corresponding number of contact points for each experimental series are given in Table 2.MODELLING OF COMMINUTION RATE OF CERAMIC
احصل على السعر
(PDF) MODELLING OF COMMINUTION RATE OF
Tomasz P. Olejnik. Results of experiments carried out in a pilot-plant ball mill are discussed in the paper. The objective of the experiments was to determine the effect of the number of contact22 May, 2019. The ball mill consists of a metal cylinder and a ball. The working principle is that when the cylinder is rotated, the grinding body (ball) and the object to be polished (material) installed in the cylinder are rotated by the cylinder under the action of friction and centrifugal force. At a certain height, it will automaticallyThe working principle of ball mill Meetyou Carbide
احصل على السعر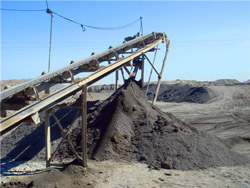
AP-42, CH 11.7: Ceramic Products Manufacturing US EPA
11.7 Ceramic Products Manufacturing 11.7.1 General1-3 Ceramics are defined as a class of inorganic, nonmetallic solids that are subjected to high temperature in manufacture and/or use. The most common ceramics are composed of oxides, carbides, and nitrides. Silicides, borides, phosphides, tellurides, and selenides also are used to This study investigated the effect of grinding media on the fine-grinding performance in the wet tumbling mill. Comparative experiments between cylpebs and ceramic balls were conducted in a laboratory wet ball mill under various conditions, such as different total masses, total surface areas, and total numbers. The results indicated that Minerals Free Full-Text A Comparison of the Fine-Grinding
احصل على السعر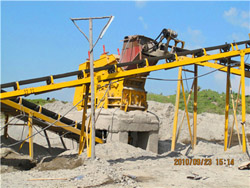
What is a ball mill? What are its uses and advantages?
Ball Mill Features. Continuous operation and large capacity. High utilize ratio and low consumption of modifying agent. With the function of modifying and dispersion, it fits for variousand a ball mill/rod mill with a hydrocyclone are most common closed circuit comminution operations in mineral processing plant practice. Most industrial grinding circuits are operated under wet conditions. This circuit ensures a steady output of desired sized particles with a suitable distribution. The mass flow rate of theCERAMIC MATERIALS I metalurji.mu.edu.tr
احصل على السعر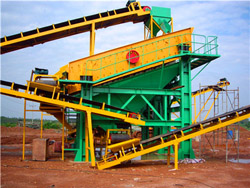
Grinding in Ball Mills: Modeling and Process Control
There are three types of grinding media that are commonly used in ball mills: • steel and other metal balls; • metal cylindrical bodies called cylpebs; • ceramic balls with regular or high density. Steel and other metal balls are the most frequently used grinding media with sizes of the balls ranging from 10 to 150 mm in diameter [30].The mill plant, located in Chenzhou City, Hunan Province, China, takes tungsten as the main valuable mineral and applies the traditional two-stage grinding process as presented in Fig. 2.It can be found that the arrangement of primary grinding circuit is forward classification circuit, and that of secondary grinding circuit is reverse The first attempt of applying ceramic balls in industrial tumbling mill
احصل على السعر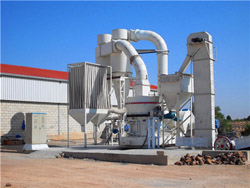
Optimization of continuous ball mills used for finish-grinding
128 065 records from the data warehouse in a coal-fired power plants were used for data mining modeling of coal grinding process in a double charge-discharge coal ball mill, the artificial neuralHigh temperature of the ball mill will affact the efficiency. 3 For every 1% increase in moisture, the output of the ball mill will be reduced by 8% -10%. 4 when the moisture is greater than 5%, the ball mill will be unable to perform the grinding operation. 5. The bearing of the ball mill is overheated and the motor is overloaded.17 Signs of Problems with Ball Mills: Quickly Remove Hidden Troubles
احصل على السعر