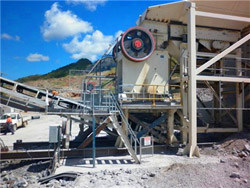
Coal ball mill, ball mill for coal crushing process sbmcn
During coal processing, we need coal crusher, coal mill, coal feeder, coal conveyor and other coal processing equipments. Coal ball mill or ball coal mill is the key grinding One such innovation is the ball mill, which has become a vital component in coal crushing operations. This article will explore the applications and benefits of using ball mills to The Role of Ball Mills in Coal Crushing Processes
احصل على السعر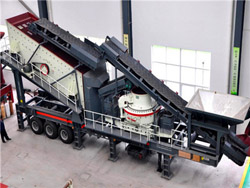
How coal gets crushed in ball mills? LinkedIn
ball mills Mining: Coal is first extracted from underground or surface mines. Crushing: The mined coal is transported to a coal preparation plant (also known as a coal Ball mill is the key equipment for secondary grinding after crushing. And it is suitable for grinding all kinds of ores and other materials no matter wet grinding or dry Sinogomine Industrial Technology Co.,Ltd-Ball mill machine
احصل على السعر
Coal Pulverizer Power Plant Pall Corporation
The four most common coal pulverizers types are: Ball-Tube Mills. This type of mill consists of a rotating tube filled with cast alloy balls. Coal is introduced through two hollow trunnions on each side of the Ball Mill Equipment, Rotary Dryer, Sand Making Machine manufacturer / supplier in China, offering Wet Ceramic Ball Mill Machine Price From China Manufacturer, Heavy China Ball Mill Manufacturer, Rotary Dryer, Stone Crushers
احصل على السعر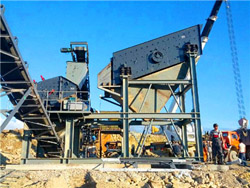
Impact energy of particles in ball mills based on DEM simulations
Ball mill is one of the most commonly used mills for the crushing and grinding of mineral ore. It is generally used to grind material down to the particle size of The original grinding circuit at Los Bronces is an example: the pebbles generated in the two SAG mills are crushed in a satellite pebble crushing plant, and then are conveyed to the Grinding Mill an overview ScienceDirect Topics
احصل على السعر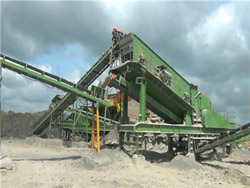
Performance optimization of an industrial ball mill for
The ball mill was operating at 45 t/h during the audit period. Conventionally, a ball mill is preferred for fine grinding, whereas a rod mill is for coarser grinding (Napier-Munn et al., Either during the processing of the mined coal or usually before the utilization of the coal, the coal undergoes secondary crushing where the top size is reduced to the range of 2'' to 1 1/4''.more variation of feed rate and coal types--on the ball and race mill were continued. The wet ball mill grinding system was operated in open circuitCoal grinding technology: a manual for process engineers.
احصل على السعر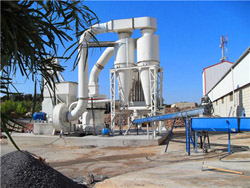
Effect of Intensive Abrasion Breakage on
In order to investigate the breakage behavior of the feed in industrial secondary ball mills, the breakage characteristics of fine magnetite were analyzed. Magnetite particle breakage produces a bimodal particle Vipeak Heavy Industry is the manufacturer of Jaw Crusher,Stone Crusher,Cone Crusher,Grinding Mill,Ball Mill,etc.With the latest manufacturing technology, the unique structural design,we produce the high standard, qualified stone crushers and grinding mills, we provide you the detailed information of Jaw Crusher,Stone Crusher,Cone Grinding Mill, Ball Mill // Vipeak Heavy Industry Crusher
احصل على السعر
sbm sample agreement for crushing contract in indiasample agreement for crushing contract in india India Free Lease Agreement Samples Welcome to India free lease contract website.in this site you will find samples for contract,agreement,contracts and agreements regarding lease contract,lease FRANCHISE AGREEMENT Guidance Clinic India Both Step 2: Start the ball mill device; debug the test ball mill to test whether it is running nor-mally, and then according to the ball mill crushing experiment plan table (Table 2), weigh the designed grinding medium and gangue of the corresponding quality using an electronic bal-ance, mix them evenly, and fill the barrel with them. 3), GrainGrain size and shape fractal characteristics of gangue in
احصل على السعر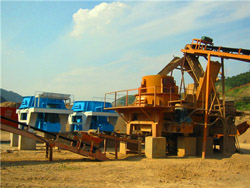
(PDF) Improving the efficiency of the coal grinding process in ball
Average particle size of coal dust in terms of the rotational speed of the ball drum mill at R = 0.15 m, f = 0.3, r = 0. 027 m, ρ d = 2100 kg/m 3,ρ b = 4850 kg/m 3,j 1 = 0 . 31, j 2 = 0 . 33It is believed that the line load on particles in rod mills helps to break hard materials (Gupta and Yan, 2016). By comparison, the point load on the particles in ball mills is conducive to theWet and dry grinding of coal in a laboratory-scale ball mill: Particle
احصل على السعر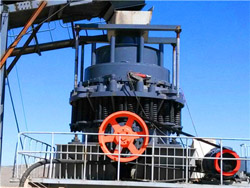
Impact energy of particles in ball mills based on DEM simulations
Ball mill is one of the most commonly used mills for the crushing and grinding of mineral ore. It is generally used to grind material down to the particle size of 20 to 75 μm and can vary in size from a small batch mill up to a mill with outputs of hundreds of tonnes per hour. Flow patterns in ball mills with different sizes: (a) 127 mmThis study shows the performance of a currently running vertical roller coal mill (VRM) in an existing coal-fired power plant. In a power plant, the coal mill is the critical equipment, whoseAn investigation of performance characteristics and
احصل على السعر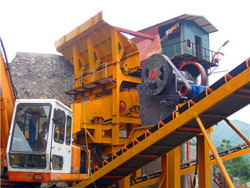
Grinding Mill an overview ScienceDirect Topics
The SAG mill was designed to treat 2,065 t h −1 of ore at a ball charge of 8% volume, total filling of 25% volume, and an operating mill speed of 74% of critical. The mill is fitted with 80 mm grates with total grate open area of 7.66 m 2 ( Hart et al., 2001 ). A 4.5 m diameter by 5.2 m long trommel screens the discharge product at a cut sizeAn increase of over 10% in mill throughput was achieved by removing the ball scats from a single -stage SAG mill. These scats are non- spherical ball fragments resulting from uneven wear of balls(PDF) Performance optimization of an industrial
احصل على السعر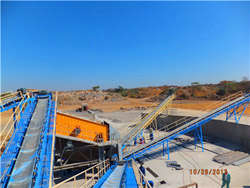
Performance optimization of an industrial ball mill for
The energy consumption in the ball mill was found to be 6.5 kWh/t of ore with a targeted product size below 1 mm. The BWI of the ores varied from 5.8 to 7.8 kWh/t to reduce the particle size below 100 μ m, but in real time, the energy consumption is very high compared with the reported value of 6.5 kWh/t.Investigation of Breakage Behavior of Coal in a Laboratory-Scale Stirred Media Mill. International Journal of Coal Preparation and Utilization 2010, 30 (1 The kinetics of fine grinding in an annular ball mill. Powder Technology 1992, 73 (2 A generalized transfer parameter treatment of crushing and grinding circuit simulation.Determination of Selection-for-Breakage Functions in the
احصل على السعر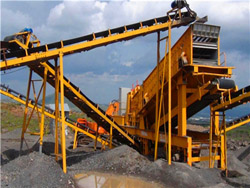
Operational parameters affecting the vertical roller mill
Vertical roller mills (VRM) have found applications mostly in cement grinding operations where they were used in raw meal and finish grinding stages and in power plants for coal grinding. The mill combines crushing, grinding, classification and if necessary drying operations in one unit and enables to decrease number of equipment in grindingThe utility model discloses a ball mill for coal powder processing, which comprises a first connecting frame and a second connecting frame, wherein material barrels are arranged on the inner walls of the first connecting frame and the second connecting frame, a crushing mechanism is arranged in the center of each material barrel, and a front base arranged CN216654784U Ball mill for coal dust processing Google
احصل على السعر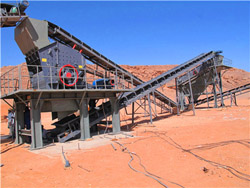
disadvantage of using ball mill in coal grinding LinkedIn
While ball mills are widely used for coal grinding in various industries, they do come with certain disadvantages. dust control equipment operating principle in crushing plant Aug 22, 2023Grinding was carried out in the laboratory ball mill described in Table 1, at a low ball load of 20% of the mill volume filled with the ball bed and a low powder load corresponding to a formal interstitial filling of void spaces of the ball bed of U=0.5. These conditions were chosen since it is known that they give first order grinding kinetics for Kinetics of fine wet grinding in a laboratory ball mill
احصل على السعر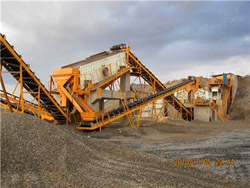
Modeling on the Effect of Coal Loads on Kinetic Energy of Balls
This paper presents a solution for the detection and control of coal loads that is more accurate and convenient than those currently used. To date, no research has addressed the use of a grinding medium as the controlled parameter. To improve the accuracy of the coal load detection based on the kinetic energy of balls in a tubular ball SAG mill compared to crusher and ball mill product size distributions (Powell et al 2014) (Lane et al., 2002). Lane (2012) also points out that pre-crushing may allow the SAG mill to be .(PDF) FULL PRE-CRUSH TO SAG MILLS ResearchGate
احصل على السعر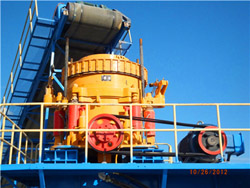
How it Works: Crushers, Grinding Mills and Pulverizers
Crushers, grinding mills and pulverizers are types of grinding equipment used to transform or reduce a coarse material such as stone, coal, or slag into a smaller, finer material. Grinding equipment can be classified into to two basic types, crushers and grinders. Industrial crushers are the first level of size reducer; further granularization
احصل على السعر