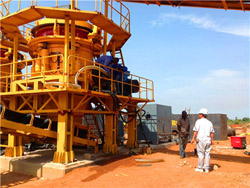
Energy-Efficient Technologies in Cement Grinding
In this chapter an introduction of widely applied energy-efficient grinding technologies in cement grinding and description of the Cement production process with waste utilisation areas. Display full size. In stage one, the essential raw materials-limestone, laterite, bauxite, kaolinite, clay, iron ore, sandstone, Full article: An overview of alternative raw materials used in cement
احصل على السعر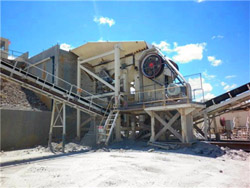
The influences and selection of grinding chemicals in cement grinding
As reported earlier, the grinding chemicals have two applications, which are; the modification of the surface charge of particles and the improvement of the There are more than twenty types of cement used to make various specialty concrete, however the most common is Portland cement. Cement manufacturing is a complex process that begins with mining and The Cement Manufacturing Process Thermo
احصل على السعر
Process technology for efficient and sustainable cement production
While vertical roller mills (VRMs) are predominantly used for raw material grinding, different types of grinding systems are used for the finish grinding of cement. The increasing demand for “finer cement” products, and the need for reduction in energy consumption and green house gas emissions, reinforces the need for Cement grinding optimisation ScienceDirect
احصل على السعر
Minerals Free Full-Text The Challenge of
There are different types of grinding aids such as aliphatic amines (triethylenetetramine (TETA)) and tetraethylenepentamine (TEPA)) and alcoholamines (diethanolamine (DEA), triethanolamine (TEA) and 11.6 Portland Cement Manufacturing 11.6.1 Process Description1-7 Portland cement is a fine powder, gray or white in color, that consists of a mixture of 11.6 Portland Cement Manufacturing U.S.
احصل على السعر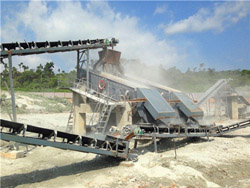
Grinding SpringerLink
The grinding media size should be 2–10 mm. They are usually made of zircon-based compounds, ceramic materials, or aluminum oxide in order to reduce wear. 50–80% of milling chamber volume is filled by grinding media, and the media are fluidized when impeller rotation reaches an optimum value.Cement is a fine, soft, powdery-type substance, mainly used to bind fine sand and coarse aggregates together in concrete. Cement is a glue, acting as a hydraulic binder, i.e. it hardens when water is added. Everyone The story of cement manufacture Cembureau
احصل على السعر
Manufacturing Of Cement: Stages To Follow
The production of cement involves six crucial stages in its manufacturing process that are: 1. Raw material extraction. To produce cement, various raw materials are required, including limestone (which is Raw materials used for cement manufacturing. Cement manufacturing is an energy and resource intensive process. It involves closely controlled chemical reactions between calcium silicate minerals at high temperatures of above 1400 degree Celsius. In this process, chemical bonds of key raw materials limestone, shell, chalk, sand, claysCMA
احصل على السعر
2 Process Of Manufacture Of Cement Civil Giant
Wet process. Dry Process of Manufacture of Cement: Crushing of limestone and clay in crushers and stored in silos. Grinding of crushed materials and storing in hoppers. Mixing of materials by compressed air in the right proportions to form a raw mix. Burning of raw mix in a rotary kiln to form clinkers.1 天前The most important properties of high alumina cement are summarized below: (i) It is resistant to the corrosive action of acids and salts of seawater. (ii) The ratio of alumina to lime is kept between 0.85 and 1.30. (iii) It gains compressive strength of 400 kg/sq.cm within 24 hours and 500 kg/sq.cm after 72 hours.15+ Different Types of Cement Their Definition, Properties
احصل على السعر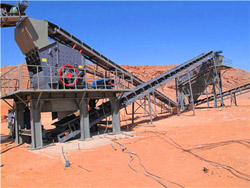
Cement Industry Glossary PDF Cement Mill (Grinding)
These bricks exhibit greater refractoriness and better resistance to chemical attack by slags and metallic oxides than the alumina or silica types. BAUXITE A reddish rock composed primarily of hydrous aluminium oxides together with silica and ferric oxide. It is a raw material for the manufacture of calcium aluminate cement. Plant To combat environmental challenges—such as the depletion of natural resources and a high carbon footprint—and contribute to the effort of achieving zero-waste technology and sustainable development, the use of agricultural and industrial wastes in the cement industry has created a research interest. This study explores the potential of two Materials Free Full-Text Effects of Grinding Methods and
احصل على السعر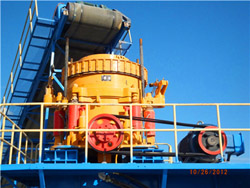
Cement Types, Composition, Uses and
We first discuss cement production and special nomenclature used by cement industrialists in expressing the composition of their cement products. We reveal different types of cement products, their compositions, The main difference between co-grinding and separate grinding of a multicomponent cement is that during inter grinding the different components interact with each other. The interactions between the components are mainly due to the relative difference in grind-ability [20,21]. These interactions can help or hinder the grinding The Challenge of Grinding Ternary Blends Containing
احصل على السعر
Cement Mill for Sale Buy Cement Ball Mill & Vertical Roller
Cement mills are the milling machines used in cement plants to grind hard clinker into fine cement powders. Cement ball mill and vertical roller mill are two most widely used cement mills in today’s cement grinding plants and are also the main types of cement mill we produce.. As a professional cement equipment manufacturer, AGICO has rich The clinker from the pyro-processing area is ground in ball mills or roll press + Ball mill combination or vertical roller mills to form cement. Commonly used separators are in closed circuit grinding are: O –sepa, Sepol and Sepax separators to achieve a finish cement fineness of 3000 4000 Blaine surface (cm2/gm).cement manufacturing Cement Plant Optimization
احصل على السعر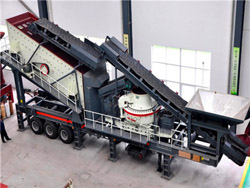
Low cost treatment and reuse of grinding sludge ISCA
could be recycled to in-line grinding operation. Amongst the various surfactants only Nonylphenyl polyethoxylate (NPE-10) and Tergitol 15-S-7 and 15-S-9 were found most effective4. The feasibility of grinding sludge in manufacturing of Portland cement has been studied. They used 1%, 2% and 3% grinding sludge by weight.A raw mill is a type of grinding machine used to crush material into a fine powder. It is an essential component in cement plants because it is used to grind down raw materials such as limestoneHow does a raw mill work in a cement plant? LinkedIn
احصل على السعر
How Cement is Made Cement Manufacturing Process
Stage 2: Grinding, Proportioning, and Blending The crushed raw ingredients are made ready for the cement-making process in the kiln by combining them with additives and grinding them to ensure a fine homogenous mixture. The composition of cement is proportioned here depending on the desired properties of the cement. This cement is mainly used for grouting anchor bolts and prestressed concrete ducts. 13. Hydrographic cement. Hydrographic cement is prepared by mixing water-repelling chemicals and has high workability and strength. It has the property of repelling water and is unaffected during monsoon or rains.13 Types of Cement and their Uses in Concrete Construction
احصل على السعر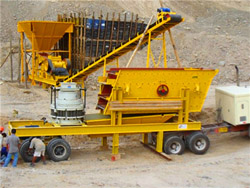
Understanding the Manufacturing Process of Cement and its
The manufacturing of Portland cement is the most common type of cement formation which is used in the construction sector. It is a type of hydraulic cement invented by Joseph Aspdin of England in 1824. It was produced from a mixture of limestone and clay. It got its name due to its high resemblance to the Portland stone in England.Types 1A, 2A, and 3A, which are variants of type 1, 2, and 3 cements. These types of cement have air-entraining materials mixed in to make them resistant to moisture damage. Types IL (Portland-limestone), IS (Portland-slag cement), IT (ternary blended), and IP (Portland pozzolana) cement, which are hydraulic and have special properties.Types of Cement Used in Construction and Civil Engineering
احصل على السعر