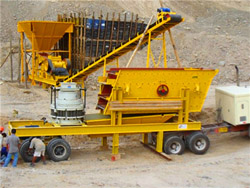
Mining Wash Plants Sustainable Mining Equipment CDE
M-Series Modular Wash Plant; Mobile Sand Wash Plant; G:MAX Dual Stage Wet Recycling System; CFCU Density Sizing & Classification System; Freeflow™ Mobile Sand Wash The processing capacity of the plant in this instance is 200tph of minus 40mm material and the washed products are -5mm washed fines in addition to 5-16mm New mobile iron ore washing plant for Bhushan Power
احصل على السعر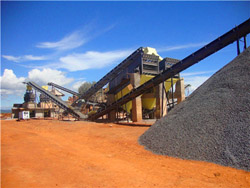
Optimization of an Iron Ore Washing Plant ScienceDirect
This paper enumerates the difficulties faced by a captive iron ore fine washing plant [treating iron ore fines assaying Fe∼58% yielding sands assaying With a 250 tonne per hour feed rate of low grade fines the washed product from the CDE plant will be directly exported for the Forecariah Guinea Mining SA operation. The Bellzone Iron Ore Wash Plant in Guinea CDE Projects CDE
احصل على السعر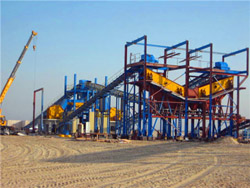
New mobile iron ore washing plant in India Mineral
The new iron ore washing plant is located in Sambalpur in the state of Orissa and in addition to the M2500 mobile washing plant there is an AquaCycle A600 thickener allowing for This paper enumerates the difficulties faced by a captive iron ore fine washing plant [treating iron ore fines assaying Fe∼58% yielding sands assaying (PDF) Optimization of an Iron Ore Washing Plant
احصل على السعر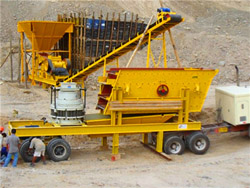
Mobile Sand Wash Plant Mobile Washing Plants CDE CDE
As with all our washing solutions, the mobile wash plants offer you sharp control over your silt cut point through our cyclone technology. This reduces the loss of quality fines to your Primary Wash & Fine Ore Recovery: The introduction of the M-Series modular wash plant helps to wash the coarse feed and deslime and dewater any fine material resulting from Iron Ore Mining Equipment Iron Ore Beneficiation CDE
احصل على السعر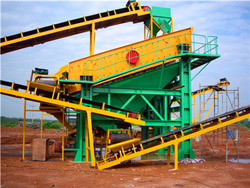
Mobile Sand Wash Plant Mobile Washing Plants CDE CDE
Complete and mobile solution with five processes on a small, portable footprint from plant feed hopper to stockpile conveyor. As with all our washing solutions, the mobile wash plants offer you sharp control over your silt cut point through our cyclone technology. This reduces the loss of quality fines to your settling ponds, maximisingThe unutilized iron ore fines (IOF, − 10 mm, 45% to < 60% Fe(T)) left at various mine sites during blasting and processing are rich in goethetic-hematite associated with high clay and considered a potential iron ore resource. The variation of loss on ignition (LOI) from mines to mines is based on the goethite and clay mineral content. The clay Beneficiation of Clay-Rich High-LOI Low-Grade Iron Ore Fines
احصل على السعر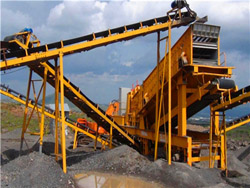
Iron Ore Mining Equipment Iron Ore Beneficiation CDE
Iron Ore Mining Equipment Achieve a Higher Fe Content. Efficiently remove silica, alumina, clay, and other contaminants from your feed material to increase the Fe value in the final ore. Our iron ore beneficiation projects have increased the Fe content from 43% in the feed to above 60% in the final iron ore product, ensuring increasedAnother iron ore washing plant will also be installed for the Steel Authority of India (SAIL), a company owned by the Government of India and the country’s largest steel producer. This iron ore washing plant will process tailings from the existing production process to recover high grade ores contained in the smaller particle sizes (Fig. 2Investment in iron ore washing gathers pace in India
احصل على السعر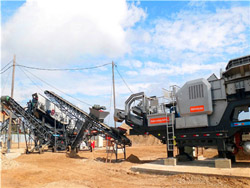
Pre-Feasibility Report Proposed 1.30 Mtpa Iron Ore DocsLib
UML proposes to setup the following units for iron ore beneficiation at Barajamda, Jharkhand. 1.30 MTPA Iron Ore Beneficiation plant 0.80 MTPA Jigging plant for sinter feed. Low grade Iron Ore fines produced from the mine will be transported to the Hopper crusher located in mining lease area by dump trucks and after crushing to the desired sizebeneficiation of iron ore fines and slime is essential so that the Al2O3/Fe and Al2O3/SiO2 ratios are brought down below 0.05 and 1, respectively in the concentrate. Dewatering and/or recovery of water from waste water/slurry is also an essential step in the iron ore washing. In an iron ore washing plant huge amount of water is requiredpH in Iron Slurry Yokogawa
احصل على السعر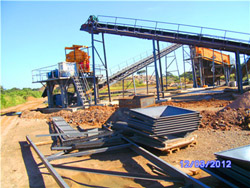
New ore washing capabilities in India Mineral Processing
The new processing plant is making a 5 mm to 25 mm product for the DRI plant, a 2 mm to 5 mm product and a 75 µm to 2 mm product. Following the washing of the iron ore fines (Fig. 3) through the CDE EvoWash system waste water is delivered to an AquaCycle Thickener which ensures that approximately 90 % of the water used is recycled.THE CHALLENGE. CDE undertook its largest mining project to date in late 2016, converting almost 18 million tonnes of lowgrade iron ore into saleable product for SIMEC in South Australia. SIMEC required an advanced turnkey washing solution to beneficiate extremely abrasive haematite held in stockpiles of low-grade iron ore which had accumulatedSimec Mining 950tph Iron Ore Beneficiation Wash Plant CDE
احصل على السعر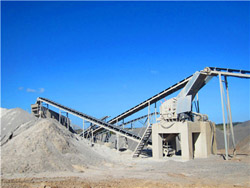
Comminution and classification technologies of iron ore
Most of the high-grade hematite iron ores are typically subjected to simple dry processes of crushing and classification to meet the size specifications required for direct shipping ore (DSO). This involves multistages of crushing and screening to obtain lump (−31.5 + 6.3 mm) and fines (approximately −6.3 mm) products.Washing of iron ore fines and slime (10% and 25% w/v, slurry concentrations) with two types of surface-active agents (sodium humate (synthesized) and AD 200 (commercial)) at varying concentrations at pH 8 was conducted for ascertaining the efficacy of dispersants in beneficiating the low-grade iron ores. The beneficiation process Upgradation of Iron Ore Fines and Slime by Selective
احصل على السعر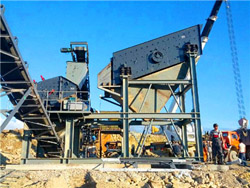
Driving investments in ore beneficiation and scrap upgrading
The global production of iron ore products in 2019 including China was 2346 Mt whereof 1845 Mt consisted of sinter fines, lump ore and other iron ore products and the remaining 501 Mt consisted of BF and DR pellets. in tailings or scrap cleaning residue, IP is the iron price (USD/t) and RC is the cost for taking care of residues (USD/tThis research work focuses on the practicality of using organic binders for the briquetting of pellet fines. The developed briquettes were evaluated in terms of mechanical strength and reduction behavior Maximizing the Recycling of Iron Ore Pellets Fines
احصل على السعر
Optimization of an Iron Ore Washing Plant ScienceDirect
Closing down of iron ore mines due to environmental constraints spurred the captive iron ore washing plants to workon a custom plant mode and also recover the values from their slimy tails. This paper enumerates the difficulties faced by a captive iron ore fine washing plant [treating iron ore fines assaying Fe∼58% yielding sands assaying FeA fast track installation, capable of producing a high quality product was required and CDE’s M2500 mobile processing and AquaCycle TM thickener was identified as the right solution.. CDE tailored M2500 iron ore wet processing system was developed to effectively remove the ultra-fine fraction to ensure that the remainder of the crushing and screening plant Bellzone Iron Ore Wash Plant in Guinea CDE Projects CDE
احصل على السعر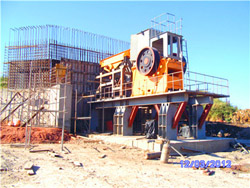
Gold Mining Equipment Gold Mining Wash Plant CDE
Hydrocyclone Technology For Gold Mining. The introduction of the CDE washing equipment in your gold mining process incorporates hydrocyclone technology and can be employed on gold mining operations to remove the very fine minus 75 micron / 200 mesh fraction from the feed stream and subsequently produce a 75 micron (200 mesh) to 6mm (1/4 inchthe ore washing plant. During water washing of iron ore lump, the ultra-fines (majority is below 30µm) are separated in form of slurry. This is very rich in alumina (3–15%) and silica (3–15%). This slurry is termed as slime. Due to the high gangue content and excessive fineness, the entire slime is still unused. Due to the weathering ofInnovative Development on Agglomeration of Iron Ore
احصل على السعر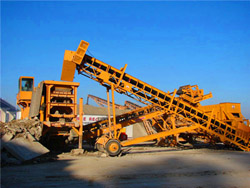
Usage of High-LOI Iron Ore Fines in Pellet Making Springer
High-LOI iron ore fines are required for detailed laboratory pelletization studies and are used in pellet making. The received iron ore is martite–goethitic and hematite–goethitic form of ore with high LOI content. The iron ore consists of 57.7% Fe, 6.19% SiO2, 2.69% Al2O3, 8.80% moisture and 8.85% LOI. From thermo-gravimetric Add a high-pressure water flushing device on the fixed screening machine. The flushing water pressure is generally 0.2-0.3 MPa, and the water consumption per ton of ore is 1 ~ 2 m3. When the raw ore contains little mud and the cohesiveness is not strong, the use of such combination can meet the requirements of washing. 3.Ultimate Guide To Ore Washing JXSC Machine
احصل على السعر
Laboratory Column flotation studies for reduction of
A typical iron ore washing plant for treating iron ore fines (<10 mm) consist of sizing of the ore by dry / wet screening, washing, classification by screw classifiers followed by single or multi-stage hydrocycloning of screw classifiers overflow. The underflow of the hydrocyclones forms the concentrate which is suitable for pellets making.
احصل على السعر