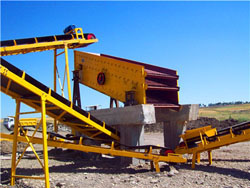
Flue Gas Desulfurization an overview ScienceDirect
Flue gas desulfurization gypsum (FGDG) is an industrial by-product generated during the flue gas desulfurization process in coal-fired power plants. The process involves the wet The end product (FA + SD-FGDS) is a dry powder, which consists of FA and the reaction products of the injected slaked lime and the SO 2 in the flue gases containing CaSO 3, Desulphurisation an overview ScienceDirect Topics
احصل على السعر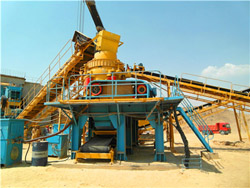
Sulfur dioxide removal: An overview of regenerative flue
Numerous mitigation techniques have been incorporated to capture or remove SO2 with flue gas desulfurization (FGD) being the most common method. Valmet Flue Gas Desulfurization (FGD) is an efficient and reliable solution for SOx removal. You can also get this system combined with NOx removal, making SOx and NOx Valmet Flue Gas Desulfurization for emissions control
احصل على السعر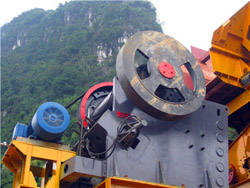
Experimental Study and Mechanism Analysis of Preparation of α
Flue-gas desulphurization (FGD) gypsum is a highly prevalent industrial by-product worldwide, which can be an excellent alternative to natural gypsum due to its Worldwide, FGD technology has proven to be one of the most efficient systems adopted for the removal of SO 2 from flue gas in coal power plants. It is a Spray drying absorption for desulphurization: a review of
احصل على السعر
Emission reduction process for dechlorinating flue‐gas
The FGD gypsum can, after dechlorination, replace natural gypsum in several industrial production processes, decreasing the consumption of natural gypsum Journal of Material Cycles and Waste Management (2022) A facile method to transform flue gas desulfurization gypsum (FGD gypsum) to α- calcium sulfate A facile method of transforming FGD gypsum to α-CaSO
احصل على السعر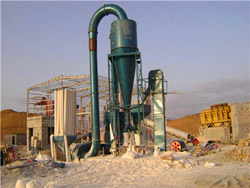
Production and resource utilization of flue gas ScienceDirect
Flue gas desulfurized gypsum (FGD gypsum), mainly originates from thermal power plants, smelters, and large-scale enterprise boilers.This article reviews the production in China and the latest beneficial utilizations of FGD gypsum. China is a large coal-consuming country and has always had serious SO 2 emissions. Therefore, the 29dbe9ef — liach2022 first a month ago. View Rendered; View Source~liagceng2022/sbm: density of limestone powder in fgd.md
احصل على السعر
Flue Gas Desulfurization by Limestone and Hydrated Lime
solid sorbent or a sorbent slurry into the furnace or flue gas duct. In wet FGD systems high degree of SO2 removal is usually achieved with a high level of sorbent utilization (Berman et al., 2000; Song ang Park, 2002; Warych and Szymanowski, 2002). However, dry or semi-dry FGD systems are usually exhibit lower SO2 removal1. Introduction. Flue gas desulfurized gypsum mainly comes from thermal power plants, smelters, and large-enterprise boilers, and contains industrial by-products produced through a wet desulfurization combustion process, where SO 2 gas and lime slurry react under strong oxidation conditions. The main component of this gypsum is Production and resource utilization of flue gas ScienceDirect
احصل على السعر
Preparation and Hardening Performance of Lightweight Gypsum
Flue gas desulfurization (FGD) gypsum is an industrial by-product produced after industrial desulfurization treatment (Cui et al. 2018; Fu et al. 2017; Wang et al. 2013).The main component of FGD gypsum is CaSO 4 2H 2 O, similar to that of natural gypsum. They have the same performance, but the quality of FGD gypsum is higher than Spray drying is a convective drying technique used to transform a feed in liquid or slurry form to a dry free-flowing powder. The quality of spray-dried powders is often defined as a function of their use. (1995) Spray drying as a preparation method of microparticu- late drug systems: an overview. S.T.P. Pharma Sci., 5 (4), 276 290Spray drying and quality changes SpringerLink
احصل على السعر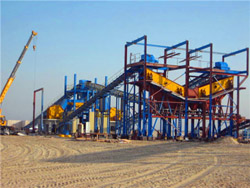
The Key Application Technology of Desulfurized Gypsum in Dry
3.2 The influence of FGD on the performance of cement-fly ash-slag powder composite cementitious system mortar For the freshly mixed mortar mixture, when it reaches the specified consistency (90-100mm), compared with the sample without FGD, when FGD is added to the cement-fly ash-slag powder composite cementing system, theLimestone slurry is prepared mixing fine limestone powder with water in a slurry preparation tank. Sorbent slurry from this tank is then pumped into the absorber reaction tank. The absorber is a counter-flow tower with flue gas flowing upwards, while limestone slurry is sprayed downwards by an array of spray nozzles. In the absorber, SO2 isFlue Gas Desulfurization-FGD AMV
احصل على السعر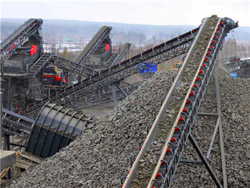
Comprehensive Effect of Oxidant Addition in an FGD Slurry on the
Request PDF On Mar 3, 2022, Qiyu Weng and others published Comprehensive Effect of Oxidant Addition in an FGD Slurry on the Removal and Distribution of Selenium: A Field Study Find, read andWet-Limestone Scrubbing Fundamentals. Stricter environmental regulations are forcing many utilities to install flue gas desulfurization (FGD) systems to control sulfur dioxide (SO2) emissionsWet-Limestone Scrubbing Fundamentals Power Engineering
احصل على السعر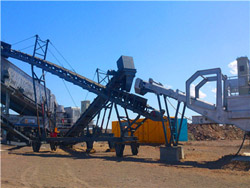
Controlling So2 Emissions: a Review of Technologies US EPA
Limestone slurry is prepared in two consecutive steps. First, limestone is crushed into a fine powder with a desired particle size distribution. This takes place in a crushing station; e.g., ball mill (fine crushing maximizes the dissolution rate of a given limestone). Next, this fine powder is mixed with water in a slurry preparation tank.To make FGD gypsum, the sludge is oxidized by forcing clean, compressed air through it. In the oxidation vessel, calcium sulfite sludge is converted to calcium sulfate (CaSO 4 ), which almost immediately combines with FGD Gypsum Production Process Gypsum Association
احصل على السعر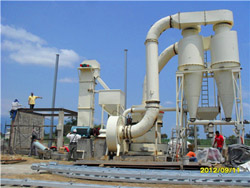
Emission reduction process for dechlorinating flue‐gas
The yield and quality of the FGD gypsum depend on parameters such as operating mode, type of fuel/sulfur content, and the type of absorbent desulfurizer technology used. 20 Since the late 1970s, European coal power plants have produced over 100 million tons of FGD gypsum. 21 In 2003, 17 European countries produced 15.2 To convey this hydrated lime powder without causing any risk of exposure to workers and work environment. Fine Dosing Requirements: 01. Silo Loading Capacity: 2500 Kg/hr. 02. Controlled Discharge to prepare lime slurry: 154 Kg/hr. 03. With specific concentration of Lime vs. Water Slurry. Why is lime dosing required?Lime Dosing System Rieco
احصل على السعر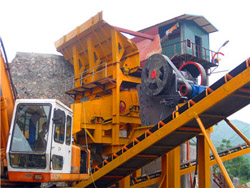
Desulphurisation an overview ScienceDirect Topics
Introducing FGD slurry as a retrofit grout material achieved 35°–45° angle of internal friction—behaving like cohesive soil suitable as an embankment material and liner-like permeabilities ≤10 −5 Then the crushed powder is sent to slurry preparation tank for dissolution with water to form limestone slurry.The main process parameters in a limestone FGD system are the (i) stoichiometric ratio (SR), (ii) the liquid/gas ratio, (iii) the slurry pH, (iv) the relative saturation and (v) other important overall FGD system parameters such as reagent type, water loop, solids dewatering, absorber parameters, reheat, reagent preparation, and fan location Enhancing the recovery of gypsum in limestone-based wet flue
احصل على السعر
A Feasible Route for Preparation of Calcium Sulfate Whiskers from FGD
Calcium sulfate whiskers (CSWs) were synthesized using purified flue-gas desulfurization (FGD) gypsum as raw materials using a hydrothermal method, where the filtrate was recycled back to the reaction slurry. The study investigated the impact of pH and Cu2+ concentration in the reaction solution with or without reagent compensation. The @article{osti_7322160, title = {Evaluation of regenerable flue gas desulfurization processes. Volume II. Final report. [Hydrogen-rich reducing gases]}, author = {Aul, Jr, E F and Delleney, R D and Brown, G D and Page, G C and Stuebner, D O}, abstractNote = {Detailed process descriptions and technical evaluations are given for the following twelve flue-gas Evaluation of regenerable flue gas desulfurization processes.
احصل على السعر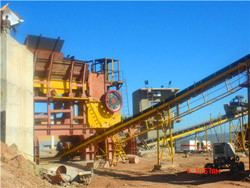
Desulfurization an overview ScienceDirect Topics
In the wet FGD process, the limestone slurry should be prepared initially in two continuous steps. At first, limestone in the crushing station is crushed into fine powder with required particle size distribution (ball mill). Then the crushed powder is sent to slurry preparation tank for dissolution with water to form limestone slurry.The higher the classifier frequency is, the finer the gypsum powder obtained. When the FGD gypsum was subjected to the jet mill with a 45 Hz classifier frequency, the D 50 of the final FGD gypsum powder decreased from 33.810 to 2.667 µm, while the D 50 of normal mechanical ball milled FGD gypsum powder is in the range of Preparation of superfine and semi-hydrated flue gas
احصل على السعر