
Energy survey of the coal based sponge iron industry
A survey is made on a typical coal based Indian sponge iron plant of capacity 500 t/d in order to identify the largest energy losses and find ways to increase Electrotherm E&T is the foremost manufacturer of Coal Based Rotary Kiln for Sponge Iron (100 TPD, 350 TPD). Download Rotary Kiln PDF to get more product information.Rotary Kiln Manufacturers Electrotherm E&T
احصل على السعر
(PDF) Operation of Coal-Based Sponge Iron Rotary Kiln to
Operation of Coal-Based Sponge Iron Rotary Kiln to Reduce Accretion Formation and Optimize Quality and Power Present work deals with two design modifications proposed for sponge iron plant. First design accounts for preheating of kiln air using waste gas exiting from ESP. Recovery and utilization of waste heat in a coal based
احصل على السعر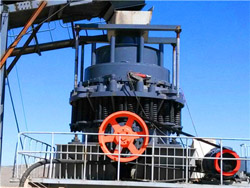
Development of energy conservations scenarios for
This paper presents an approach to find the best modification in the coal-based sponge iron process with an aim to integrate energy in it. For this purpose Conventional sponge iron plant flow diagram Coal injector, Air: 2500m3/h, Injection coal:6.13 t/h, all at 300C Rotary Kiln (10200C) 8 shell air fan at 48000 m3/h, 300C Flue Generation of Energy Conservation Measures for Sponge Iron Plants
احصل على السعر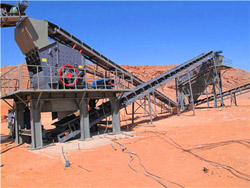
Sponge Iron SpringerLink
Processes that produce iron by reduction of iron ore in solid state are generally classified as direct reduction (DR) processes and the products also referred to Present work deals with two design modifications proposed for sponge iron plant. First design accounts for preheating of kiln air using waste gas exiting from ESP. Recovery and utilization of waste heat in a coal based sponge iron
احصل على السعر
Profitability analysis of power generation using waste heat of
The heat of waste gas can be utilized in various ways in the sponge iron process as suggested by many investigators. Bandyopadhyay et al. [3] found coal as 4.1 Direct Reduction of Iron Production Using Solid Coal 39 4.2 Direct Reduction of Iron Production Using Coal Gasification 43 4.3 Direct Reduction of Iron Production Using Gas Route 49 4.4 Hydrogen Use in Indian Iron and Steel Sector 54 5.0 Conclusion 57 Technology Vendors Energy-efficient Equipment and Systems 60 References 65ENERGY-EFFICIENT TECHNOLOGY OPTIONS FOR DIRECT REDUCTION OF IRON
احصل على السعر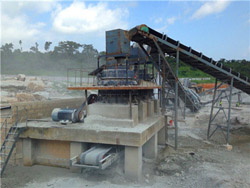
SAFETY GUIDELINES FOR IRON & STEEL SECTOR
SAFETY GUIDELINES FOR IRON & STEEL SECTOR MINISTRY OF STEEL, GOVT. OF INDIA Direct Reduction Plant ( Gas Based) Doc. No: SG/33 Rev no. : 00 Effective Date: -- 1. OBJECTIVE : The entire process of making Sponge Iron by coal based DRI process is associated with various Safety hazards like Fire, Explosion, Radiation, Burns hit /Overview of Sponge Iron sector . 33 ; 3.3 Inventorization of Sponge Iron plants 34 4.0 . Process Description of Sponge Iron Plant ; 40 . 4.1 Brief description of sponge iron plant process 40 4.2 Technological options for coal based plants 42 5.0 Status of Sponge Iron Plants in India 67 5.1 Questionnaire Survey 67Good Practices Manual
احصل على السعر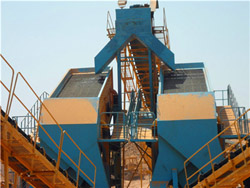
TSLP Sponge Iron TATA Steel Long Product Limited
Coal based DRI making process. Iron Ore and non-coking coal are the prime raw materials for the production of sponge iron. Jharkhand which comprises a pellet plant, sinter plant, oxygen plant, lime kiln plant, coke oven, sponge iron plant consisting of five kilns, two blast furnaces and a steel melting shop. READ MORE . WIRE RODS .Thus, the sector depends mostly on coal-based sponge iron and nearly 80% of the total coal-based sponge iron plants are located in India. 1 About 60% of this production comes from small-scale industries in the unorganised sector with poor pollution control facilities. 1 During the past decade, these sponge iron plants have rapidly grown Health-related quality-of-life of coal-based sponge iron plant
احصل على السعر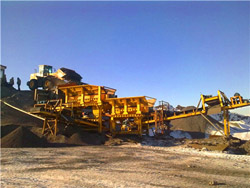
Bureau of Energy Efficiency (BEE) : Manual On Energy Scribd
2.5 Equipments and Machinery in sponge Iron manufacturing In 100 TPD coal based sponge iron plants, during the process at least 24000 m3/hr flue gases are generated and having the temperature of 900-1000C. The heat from the flue gas is recovered using Waste Heat recovery Boiler and generates at least 2.2 MW power.Ashoka’s state-of-the-art plant has expert manufacturing facilities. Quality control measurements and inspection is undertaken at every stage of manufacturing. For More details about Cement Plant Consultation, Projects, Budget, Machines, AMC, Up-gradation etc, Please contact Us @ + 91 9811141400 or Send Business Query. Sponge Iron PlantSponge Iron Plant Manufacturers and Sponge Iron Equipment
احصل على السعر
Sponge Iron Plant Complete Project & Equipment Technical
Sponge iron plant rotary kiln and cooler list of machinery spare parts and casting and forging technical procurement specifications budgetary cost for coal based, gas based, electric based sponge iron plant for 50 TPD, 75 TPD, 100 TPD, 150 TPD, 175 TPD, 200 TPD, 300 TPD, 350 TPD, 500 TPD, 600 TPD (Tons per day).Context in source publication. balance around the main equipment, such as rotary kiln and ABC of a typical sponge iron plant of 500 t / day capacity, carried out on per hour basis, is shown inMass balance around main components of the plant on per
احصل على السعر
Analyses of Different Modifications Proposed for the Sponge Iron
Coal-based sponge iron plants have very high average heat to power ratios, often in the range of 25:1 to 31:1 (Choudhury 2014). This reflects that coal-based sponge iron plants use mostly thermal energy in comparison to electrical energy. So, all these studies are aimed to reduce the coal consumption in these plants which is the plants of Orissa, India” A lot of sponge iron manufacturers with rotary kiln are operating in India, and waste heat gas is disposed to the air. Electric generation utilizing this gas is very beneficial to improve. Anil Kumar Prasad, Department of Mechanical Engineering, NIT . A tremendous amount of heat is generated in the coal based spongeWaste Heat Recovery Steam Generator in Sponge Iron Plant
احصل على السعر
Energy survey of the coal based sponge iron industry
In conventional coal based sponge iron plant, Fig. 1, kiln feed (Stream no. 1), which consists of iron ore, feed coal and dolomite, is fed to the rotary kiln (RK).A separate conveyor collects different size fractions of coal (Stream no. 5) for injection into the kiln with the help of pressurized air (Stream no. 4) from discharge end side.The coal consumption ranges from 950 to 1,000 kg/metric ton DRI as charged. This is equivalent to an energy consumption of 21 to 23 GJ/metric ton DRI, using 23 GJ/metric ton of Indian sub-bituminous coal. Coal consumption at ISCOR is reported to be 800 to 900 kg/metric ton of DRI using 28 GJ/metric ton for South African sub Energy Conservation In Coal Based Dri Plant Electrical India
احصل على السعر
Development of energy conservations scenarios for sponge iron
Coal based sponge iron plant: a conventional process. The process flow diagram of conventional coal-based sponge iron plant is shown in Fig. 1. The operating data shown in Fig. 1 is taken from a typical Indian sponge iron plant. In the conventional process kiln feed, which consists of iron ore, feed coal, and dolomite, is fed to the rotary Sep 01, 2015 In conventional coal based sponge iron plant, Fig 1, kiln feed (Stream no 1), which consists of iron ore, feed coal and dolomite, is fed to the rotary kiln (RK) A separate conveyor collects different size fractions of coal (Stream no 5) for injection into the kiln with the help of pressurized air (Stream no 4) from discharge end sideThe sponge iron is al based sponge iron plant machinery equipment
احصل على السعر
Design Modifications for Energy Conservation of Sponge Iron Plants
During the operation in the coal based sponge iron plant, a tremendous amount of heat is generated and significant part of this heat, associated with the waste gas, remains unutilized. It appears worth interesting to modify the process that facilitates the integration of heat available with the waste gas. In the present paper, for the utilization of ITECHC Metals Private Limited. Establishment of Sponge Iron unit (2,25,000 TPA), Induction Furnace with matching LRF & CCM (Billets / Ingots / Hot Billets) (2,40,000 TPA), Rolling Mill (TMT Bars / Structural Steel) (2,25,000 TPA), Brick manufacturing unit 25,000 bricks/day, WHRB based Power Plant 18 MW (3 x 6 MW), Establishment of Sponge Iron unit in Chhattisgarh ProjectX India
احصل على السعر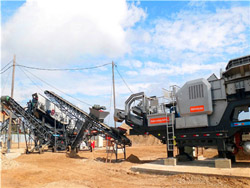
sponge iron industry –past-present-future SIMA Yumpu
Coal based DRI plants often experience problems<br /> with respect to formation of accretion resulting in<br /> reduced production rate & shorter campaign life,<br />Borah et al., “Quality Prediction And Control In Coal-Fired Rotary Sponge-Iron Kilns At TATA Sponge”, un published work (paper to ap pear in proceedings of the curre nt A ISTech 2019). 8.(PDF) Operation of Coal-Based Sponge Iron Rotary Kiln to
احصل على السعر
Mathematical Modelling of Sponge Iron Production in a Rotary
P.V. Natekar. India is the largest producer of sponge iron or direct reduced iron (DRI) in the world. The important step in the manufacture of DRI is direct reduction of iron ore by coal or
احصل على السعر