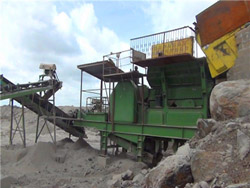
Process of Cement Manufacturing -A Brief into Dry and
Dry mixing of Cement refers to the process of blending dry Cement with other dry materials, such as aggregates and additives, without the addition of water. What are the stages of Cement drying? This grinding is done wet or dry, depending on the process in use, but for dry grinding the raw materials first may need to be dried in cylindrical, rotary dryers. Soft materials are Cement Extraction, Processing, Manufacturing Britannica
احصل على السعر
Cement grinding optimisation ScienceDirect
grinding the cement clinker nodules to 100% passing 90 μm in a dry circuit. Grinding occurs at the beginning and the end of the cement making process. Herein, we evaluate experimentally the interactions among clinker, limestone and gypsum during the final grinding stage in Portland cement production. Resistance to Grinding and Cement Paste Performance of
احصل على السعر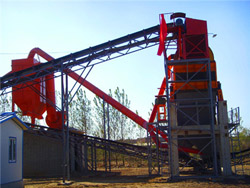
11.6 Portland Cement Manufacturing U.S. Environmental
11.6.1 Process Description1-7 Portland cement is a fine powder, gray or white in color, that consists of a mixture of hydraulic cement materials comprising primarily calcium In this study, the thermoeconomic and environmental assessment was performed to identify key energy efficient opportunities and technical improvement Thermoeconomic and environmental analyses of a dry
احصل على السعر
state grinding of cement in dry process
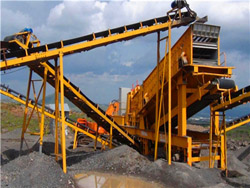

Cement Manufacturing Process CivilEngineer.Guru
The manufacturing process of Cement. The manufacturing process of Cement involved grinding raw materials, mixing them according to certain proportions and burning them in a kiln at a Cement grinding process is the reduction of clinker produced in rotary kilns to a fine form. The clinker has to be ground with the addition of gypsum to get the finish product, cement. The objective is to increase the specific surface of the cement component with a proper particle size distribution and to provide convenient reactivity of cement A Review on Pyroprocessing Techniques for Selected Wastes
احصل على السعر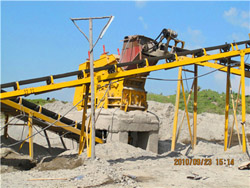
11.6 Portland Cement Manufacturing U.S. Environmental
cement plants with wet process kilns is 3-05-006, and the six-digit SCC for plants with dry process kilns is 3-05-007. Portland cement accounts for 95 percent of the hydraulic cement production in the United States. The balance of domestic cement production is primarily masonry cement. Both of these materials are2.1.3 Blending and grinding of cement clinker There are four main process routes for the manufacture of cement dry, semi-dry, wet and semi-wet processes. In the dry process the raw materials are ground and dried to raw meal in the form of a flowable powder. The dry raw meal is fed to the preheater or precalciner kiln,EMEP/EEA air pollutant emission inventory guidebook 2016
احصل على السعر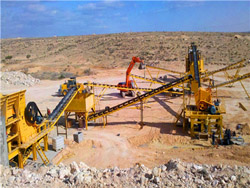
I03 cement June 2010 GS-gct IEA-ETSAP
that of dry powders. The wet process also enables an easier control of the chemical composition of the raw mix. However, the wet process is more energy intensive and Fig. 1 Simplified cement production process[5] Tab. 1 Cement EU Standard and Composition [5] Types of cement Clinker Other Constituents CEM I Portland 95-100 CEM IIThe cement by this process can be prepared by using the following operations:-. Mixing of raw materials. Burning and Grinding. Mixing of Raw Materials: The raw materials i.e. argillaceous and calcareous materials undergo the following stages:-. Crushing: The raw materials, first of all, are broken into crushers into small fragments that vary inManufacturing of Cement By Dry and Wet Process Expert Civil
احصل على السعر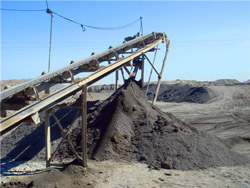
Preparation of polymer-based cement grinding aid and their performance
Introduction. Cement world production currently increases up to approximately 4 billion tons/year. The electrical energy consumed in cement production is 110 KW/tone and about 30% of which is used for raw material preparation and about of 40% for final cement clinker grinding [1], [2], [3].This leads to important cost increase of the This set of Concrete Technology Multiple Choice Questions & Answers (MCQs) focuses on “Wet Process”. 1. What is wet process? a) Grinding and mixing of the raw materials in their dry state. b) Grinding and mixing of the raw materials in their medium state. c) Grinding and mixing of the raw materials in their wet state.Concrete Technology Questions and Answers Wet Process
احصل على السعر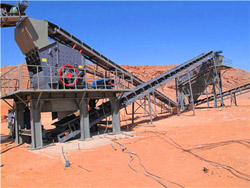
Study and Review of Ordinary Portland Cement Web UPI Official
grinding is done wet or dry, depending on the process in use, but for dry grinding the raw materials first may need to be dried in cylindrical, rotary dryers. Soft materials are broken down by vigorous stirring with water in wash mills, producing a fine slurry, which is passed through screens to remove oversize particles. 3.3. BlendingHowever, the manufacturing process is known as energy intense since the energy utilization is about 110–150 kW h per tonne of cement varying with the process modernization and raw materials used [2]. Broadly, the process is composed of many sub operations including raw meal preparation and grinding, pyrometallurgical process, The influences and selection of grinding chemicals in cement grinding
احصل على السعر
Production of cement and its environmental impact ScienceDirect
Considering cement manufacturing process, CO 2 emissions have been evaluated due to the use of electrical energy for (i) Initial grinding of raw materials (ii) mixing of raw materials in the silos before preheating (iii) final grinding of clinker with gypsum & other substitutes (e.g., flyash, slag, pozzolan etc.).Classification Code (SCC) for portland cement plants with wet process kilns is 3-05-006, and the six-digit SCC for plants with dry process kilns is 3-05-007. Portland cement accounts for 95 percent of the hydraulic cement production in the United States. The balance of domestic cement production is primarily masonry cement. Both 11.6 Portland Cement Manufacturing US EPA
احصل على السعر
AVAILABLE AND EMERGING TECHNOLOGIES FOR REDUCING
There are three major variations of dry-process kilns in operation in the U.S.: long dry (LD) kilns, preheater (PH grinding to ensure a uniform surface area of the final product. (Coito et al Thermal Units (lb/MMBtu) for fuels combusted at cement kilns in the United States. 6 . Gas 1. cement . emissions. emissions cement,and 2Most studies conducted worldwide state that cement plants emit many pollutants into the atmosphere, bag filters in the dry process show that 45% of the escaped particles are smaller than 2.5 μm, the grinding of cement in the cement mill/mills generates an appreciable amount of dust.Dust Emission Monitoring in Cement Plant Mills: A Case Study in
احصل على السعر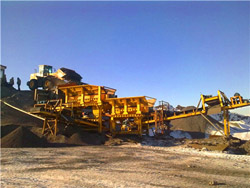
An Insight into the Chemistry of Cement—A Review MDPI
Even if cement is a well-consolidated material, the chemistry of cement (and the chemistry inside cement) remains very complex and still non-obvious. What is sure is that the hydration mechanism plays a pivotal role in the development of cements with specific final chemical compositions, mechanical properties, and porosities. This In dry and semi-dry processes for cement manufacturing, the raw materials will be crushed and then fed in the correct proportions. It is then added to the grinding mill. Then, the raw material will be dried and reduced in size to a fine powder in there. The dry powder you will get there will be called the raw meal then, the raw meal will beDry Process of Cement Manufacturing Semi-dry Process
احصل على السعر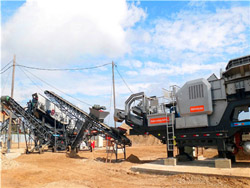
Thermoeconomic and environmental analyses of a dry process cement
In this study, the thermoeconomic and environmental assessment was performed to identify key energy efficient opportunities and technical improvement potentials of the production of dry cement in Nigeria. The process was divided into ten basic unit operations, which are: drilling, explosive charging, mucking and hauling, crushing, raw In this chapter an introduction of widely applied energy-efficient grinding technologies in cement grinding and description of the operating principles of the related equipments and comparisons over each other in terms of grinding efficiency, specific energy consumption, production capacity and cement quality are given. A case study Energy-Efficient Technologies in Cement Grinding IntechOpen
احصل على السعر