
What is a cement grinding unit and what processes are involved
The main processes involved in a cement grinding unit are: 1.Clinker grinding: This is the main process in a cement grinding unit, where clinker is ground into The article describes the theoretical concepts underlying the technology of material grinding. The main factors affecting energy Overview of cement grinding: fundamentals, additives,
احصل على السعر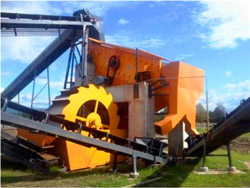
Process technology for efficient and sustainable cement
The grinding of raw materials and cement has been in the focus of better energy utilisation, but product quality is also of the highest importance. In terms of 1. Introduction For all dry grinding applications, cement production is certainly the most important. The estimate for the world energy consumption for cement Cement grinding optimisation ScienceDirect
احصل على السعر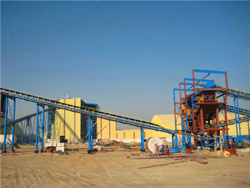
An Insight into the Chemistry of Cement—A Review
From the energetic viewpoint, the grinding process consumes ca. 60% of the total electrical energy involved in a standard cement plant (high cost). In a conventional cement making process, the Cement manufacturing is a complex process that begins with mining and then grinding raw materials that include limestone and clay, to a fine powder, called raw meal, which is then heated to a sintering The Cement Manufacturing Process Thermo Fisher
احصل على السعر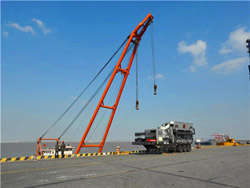
Effect of Grinding Aids in Cement Grinding IOPscience
Grinding aid or grinding additives refer to substances which when mixed into the mill contents cause an increase in rate of size reduction and flowability. Grinding There are several steps involved in the production of cement. Each of these steps provide distinctive characteristics that can be used to identify the production Global database of cement production assets and upstream
احصل على السعر
Production of cement and its environmental impact ScienceDirect
Blended cements are produced by mixing different supplementary cementitious materials (SCMs) such as flyash, metal slag, silica fume and limestone powder individually or a combination of two or more SCMs at the final grinding stage of the product. Cements in which a portion of Portland cement is replaced by mineral admixtures/SCMs Step 3: Grinding,homogenization and Clinkerization. Next in cement manufacturing process, the crushed rock is combined with other ingredients such as iron ore or fly ash and ground, mixed, and fed to a Cement manufacturing process: Step-by-step guide
احصل على السعر
(PDF) Mining Activities, Cement Production Process and
Cement has hydraulic properties like slaked lime and hardens when mixed with water. Compressive strength increases in time and reaches its practical top limit after 28 days. Mixing crushed stoneThe vertical roller mill is better to ball mill in respect of overall economy. The final manufacturing stage at a cement plant is the grinding of cement clinker from the kiln, mixed with 4-5%The important role of vertical mills in cement clinker grinding
احصل على السعر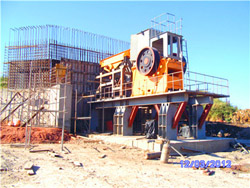
2 Major Roles of Limestone in Cement Manufacturing
Limestone plays two major roles in the cement manufacturing process, one is used as a raw material for cement clinker, and the other is used as a cement admixture. Limestone is one of the key raw materials of cement clinker. Around 80-90% of the raw material for the kiln feed is limestone. Limestone is also a favored mineral Table 1. Chemical formula and cement nomenclature for major unhydrated OPC phases. The composition of cement is varied depending on the application. A typical example of cement contains 50–70% C3S, 15–30% C2S, 5–10% C3A, 5–15% C4AF, and 3–8% other additives or minerals (such as oxides of calcium and Introductory Chapter: Properties and Applications of Cement
احصل على السعر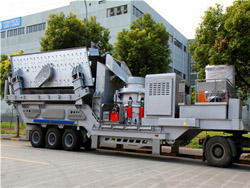
Manufacture Of Portland Cement Process Flow chart civil
Following are the important operations involved in the manufacture of portland cement: 1) Mixing of raw materials. 2) Burning. 3) Grinding. 4) Packing of cement. Flow chart for manufacturing of cement. Table Of Contents.invention in France which involved a tube mill with a charge of steel balls or flint pebbles for fine grinding of sand or cement. F.L.Smidth acquired the rights to his patent and started selling an improved version of this mill all over the world. For the cement industry the ball mill was really an epoch-making breakthrough as for almostCement grinding Vertical roller mills versus ball mills
احصل على السعر
Cements ground in the vertical roller mill fulfil the quality
In the past, high pressure grinding rolls (HPGR), vertical roller mills (VRM) had positive effects on the overall energy utilization of cement grinding however some quality issues had also beenThe most important first step in controlling energy consumption is to be aware of the relative importance of the process areas where most energy is consumed. Figure 2 shows a typical breakdown of electrical energy consumption at a cement plant. The most obvious area for attention is that of grinding, both raw and cement.Best energy consumption International Cement Review
احصل على السعر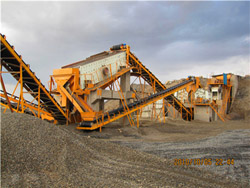
The Cement Manufacturing Process Environmental and Social
The raw cement ingredients are heated and clinkers or hard, spherical nodules are produced as a result. Cement Kiln processing involves the following stages: drying or preheating, calcining, and clinker cooling. Calcination is the process of burning the raw mix at a high temperature so that clinkers are formed.obtained in 1824 by Joseph Aspdin, an English mason. fThere are four stages in the manufacture of Portland cement: (1) crushing and. grinding the raw materials, (2) blending the materials in the correct proportions, (3) burning the prepared mix in a kiln, and (4) grinding the burned product, known as.Methods, Processes and Equipment Involved in Manufacturing Cement
احصل على السعر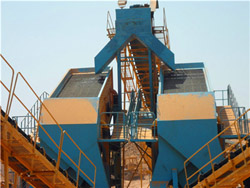
Thomas Holzinger, Holzinger Consulting, grinding system
Cement grinding In Table 1, three common cement grinding systems are compared on their electrical consumption for a typical 3500 Blaine ordinary portland cement (OPC). Roller press finish‑grinding systems, due to lower fan power demand compared to a VRM, exhibit a lower specific energy consumption.Finally, during the cement grinding and distribution process, firstly the cooled clinker is ground with around 5% of gypsum and other 17 JRTE-2020 cementitious materials to form the final cementTypical cement manufacturing process flow diagram [4].
احصل على السعر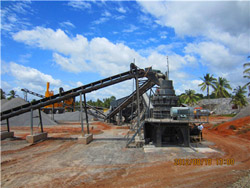
PROCESS CONTROL FOR CEMENT GRINDING IN VERTICAL ROLLER MILL
The power ingesting of a grinding process is 50-60% in the cement production power consumption. The Vertical Roller Mill (VRM) reduces the power consumption for cement grinding approximately 30-40% associated with other grinding mills. The process variables in cement grinding process using VRM are strongly nonlinear and having large time Download scientific diagram Closed circuit grinding system. from publication: Optimizing the control system of cement milling: Process modeling and controller tuning based on loop shapingClosed circuit grinding system. Download Scientific Diagram
احصل على السعر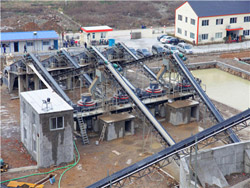
The Optimization of Calcareous Fly Ash-Added Cement Containing Grinding
This is an experimental study which explores the physical, mechanical, and economic factors involved in the production of type CEM II A-B/W cement. In this context, 4 cement additives were used in two different dosages (200 and 800 g/t). Class C fly ash was used for composite cement production at ratios of 5%, 20%, and The majority of grinding aids used in powder production before the 1990s were purified chemicals, such as ethylene glycol, propylene glycol, tri-isopropanol amine, triethanolamine (TEA), sodiumDetails of PCE-based grinding aids Download Scientific Diagram
احصل على السعر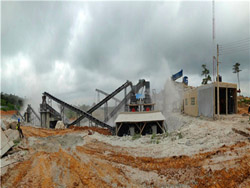
Cement Manufacturing Process Phases Flow Chart Cement
Cement Manufacturing Process Phase II: Proportioning, Blending & Grinding. The raw materials from quarry are now routed in plant laboratory where, they are analyzed and proper proportioning of limestone and clay are making possible before the beginning of grinding. Generally, limestone is 80% and remaining 20% is the clay.For a ball mill grinding OPC to a fineness of 3200 to 3600 cm2/g (Blaine) the cost of wear parts (ball, liners and mill internals) is typically 0.15-0.20 EUR per ton of cement. For an OK mill grinding a similar product, the cost of wear parts depends on the maintenance procedures, i.e. whether hardfacing is applied.Cement grinding Vertical roller mills VS ball mills
احصل على السعر