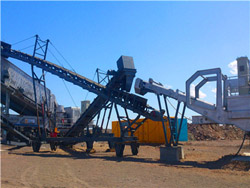
Comparison of energy efficiency between ball mills and
The practical limit to ball mill product fineness is considered to be 40–45 μm ( Gao and Weller, 1994 ). Although ball mills can still be found in the regrind circuits in a number of mineral processing plants, their energy consumption is high, and size Schellinger's calculated ball mill efficiency, in dry or wet ball mill grinding, ranges between 10% and 19%, with the higher figure occurring at the optimal The energy efficiency of ball milling in comminution
احصل على السعر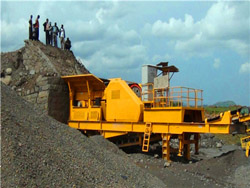
(PDF) Energy Efficiency Analysis of Copper Ore Ball Mill
One method for increasing the energy efficiency of ball mills is to optimize their drive systems. This article looks at two variants of drive systems with creasing the energy efficiency of ball mills is to optimize their drive systems. This article looks at two variants of drive systems with efficiencies higher than the already existing...Energy Efficiency Analysis of Copper Ore Ball Mill Drive Systems
احصل على السعر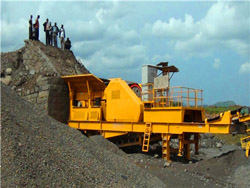
Energy Efficiency Analysis of Copper Ore Ball Mill Drive Systems
The first variant is a low-speed synchronous motor with permanent magnets without a gearbox, and the second variant is an asynchronous high-efficiency One method for increasing the energy efficiency of ball mills is to optimize their drive systems. This article looks at two variants of drive systems with efficiencies higher than Energy Efficiency Analysis of Copper Ore Ball Mill Drive Systems
احصل على السعر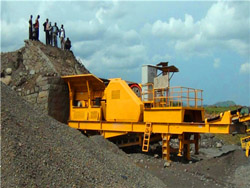
The energy efficiency of ball milling in comminution
The purpose of this paper is to review approaches that have been taken to assess the energy efficiency of comminution processes and to further delineate factors Tumbling mills are notorious for their low energy efficiency because they only use up to 10% of installed power for grinding action. A feature of ball mills is their high specific A Comparative Study of Energy Efficiency in Tumbling Mills with
احصل على السعر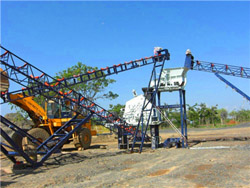
Ball mill
A ball mill, a type of grinder, is a cylindrical device used in grinding (or mixing) materials like ores, chemicals, ceramic raw materials and paints. Ball mills rotate around a horizontal If the ball mills are in connection with hydrocyclones then the ball mills can't be evaluated by themselves but they need to be assessed as part of the grinding It has to be converted to power at the mill pinionshaft. Quantifying Grinding Efficiency Grinding &
احصل على السعر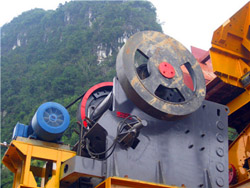
How to Measure Grinding Efficiency 911 Metallurgist
Grinding Efficiency in % 82.6; Ball mill feed micrometers 1300; Ball mill product micrometers 115; Ball mill ratio of reduction 11.3; Power per metric tonne motor input Kw 9.2; Calculated operating work Energies 2021, 14, 1786 4 of 14 (a) (b) Figure 2. Ball mill drive system with low‐speed SAS motor without intermediate gearbox: (a) prior to modernization, (b) after modernization on the right [34].Energy Efficiency Analysis of Copper Ore Ball Mill Drive Systems
احصل على السعر
Ball Mill SpringerLink
Ball mill is a type of grinding equipment that uses the rotary cylinder to bring the grinding medium and materials to a certain height and make them squeeze, impact, and grind and peel each other to grind materials. Ball mill is the key equipment for crushing materials after they are crushed. It is widely used in cement, silicate products, One method for increasing the energy efficiency of ball mills is to optimize their drive systems. R.M.; Gray, D.J. Solution of a Serious Repetitive Vibration Problem on a 4500-hp Single-Pinion Synchronous Motor Ball Mill Drive. IEEE Trans. Ind. Appl. 1985, IA-21, 1039–1046. [Google Scholar]Energy Efficiency Analysis of Copper Ore Ball Mill Drive Systems
احصل على السعر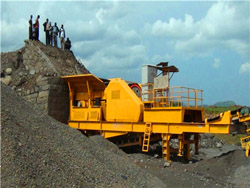
Ball Mills 911 Metallurgist
CERAMIC LINED BALL MILL. Ball Mills can be supplied with either ceramic or rubber linings for wet or dry grinding, for continuous or batch type operation, in sizes from 15″ x 21″ to 8′ x 12′. High density ceramic linings of uniform hardness male possible thinner linings and greater and more effective grinding volume.The better mills on the market have an efficiency of about 8-9 % which means that only 8-9 % of the energy results in grinding and the majority is converted mainly into heat. The ball mill has the worst efficiency of all types of mills on the market. Just 4 % of the energy is used for comminution. Nevertheless when grinding is required the ballProcess Training Ball Mill INFINITY FOR CEMENT EQUIPMENT
احصل على السعر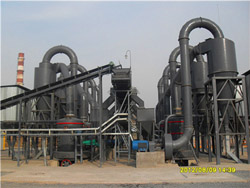
DETAILED PROJECT REPORT SAMEEEKSHA
The ball mill are in operations in refractory Industries are daily about 14 hrs for making unshaped refractory material. The environment in ball mill area is dusty and wet which will affect the efficiency of motors and other parts of machinery. If the ball mill motor is inefficient the power consumption will be high.The following are factors that have been investigated and applied in conventional ball milling in order to maximize grinding efficiency: a) Mill Geometry and Speed Bond (1954) observed grinding efficiency to be a function of ball mill diameter, and established empirical relationships for recommended media size and mill speed that Factors Affecting Ball Mill Grinding Efficiency 911 Metallurgist
احصل على السعر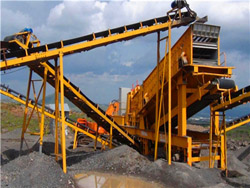
Ball Mill: Operating principles, components, Uses, Advantages and
Advantages of Ball Mills. 1. It produces very fine powder (particle size less than or equal to 10 microns). 2. It is suitable for milling toxic materials since it can be used in a completely enclosed form. 3. Has a wide application. 4. It can be used for continuous operation.To choose a motor for a ball mill, it is important to consider the torque and power requirements of the mill. It is also important to consider the speed of the motor and the efficiency of the motor.How to choose a motor for a ball mill? LinkedIn
احصل على السعر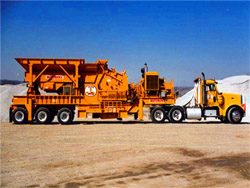
How Steel Charge affects Ball Mill Power Draw
Motor output power KW = Motor input power x Rated motor efficiency Motor output power KW = 0.001 x (1.73 x amperage x voltage x power factor) x Rated motor efficiency/ Our power factor is 0.99 electricians A brief introduction of 3 common mill types: Ball Mills a horizontal rotating cylinder containing a charge of steel balls. The balls tumble as the mill turns and material caught between the balls is ground A Comparison of Mills Used for Phosphate Rock
احصل على السعر
(PDF) DESIGN AND FABRICATION OF MINI BALL MILL.
This project is to design and fabricate the mini ball mill that can grind the solid state of various type of materials into nano-powder. The cylindrical jar is used as a mill that would rotate theThe subject of this paper is a synchronous drive of grinding ball mills 4 MW, 150 rpm, these machines are efficient prime movers for large mill applications. Both in motor efficiency and in(PDF) Evaluation of synchronous motors on grinding mills
احصل على السعر
Energy Efficiency Analysis of Copper Ore Ball Mill Drive Systems
One method for increasing the energy efficiency of ball mills is to optimize their drive systems. R.M.; Gray, D.J. Solution of a Serious Repetitive Vibration Problem on a 4500-hp Single-Pinion Synchronous Motor Ball Mill Drive. IEEE Trans. Ind. Appl. 1985, IA-21, 1039–1046. [Google Scholar]One method for increasing the energy efficiency of ball mills is to optimize their drive systems. R.M.; Gray, D.J. Solution of a Serious Repetitive Vibration Problem on a 4500-hp Single-Pinion Synchronous Motor Ball Mill Drive. IEEE Trans. Ind. Appl. 1985, IA-21, 1039–1046. [Google Scholar]Energy Efficiency Analysis of Copper Ore Ball Mill Drive Systems
احصل على السعر
Electromagnetic design and thermal analysis of module combined
Because of its massive volume, the gearless ball mill is difficult to manufacture and maintain. Therefore, a novel module combined permanent magnet motor with wrapped type for mine ball mill (MBMWT-MCPMM) is proposed, eliminating the gear and reduction box in the traditional drive mode and significantly improving transmission To increase efficiency, designers of mining equipment tried to improve all the elements of ball mills, such as the geared mechanical drives, bearings, their lubrication systems, and electric motors. Moreover, efforts have been made to optimize the size of the grinding bodies, control the filling level of the drum with the material, and stabilize the Tumbling Mills Encyclopedia MDPI
احصل على السعر
The Effect of Ball Size Diameter on Milling Performance
the other mills, as previously mentioned ball mills have a very low efficiency in terms of utilizing the energy generated towards particle size reduction. The diameter of the balls used in ball mills play a significant role in the improvement and optimization of the efficiency of the mill [4]. The optimum rotation speed of a mill, which is the
احصل على السعر