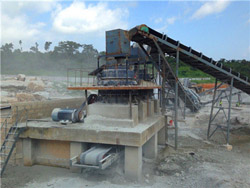
Wet-milling
Wet-milling is a process in which feed material is steeped in water, with or without sulfur dioxide, to soften the seed kernel in order to help separate the kernel’s various components. For example, wet-milling plants can separate a 56-pound bushel of corn into more than 31 pounds of cornstarch (which in turn can be converted into corn syrups or corn ethanol), 15 pounds of corn gluten meal for use in animal feed, and nearly 2 pounds of corn oil. As the name suggests, wet milling involves size reduction of drug particles suspended in a liquid medium that may be aqueous or non-aqueous in nature. Overview of milling techniques for improving the
احصل على السعر
Everything You Need to Know About Wet Media Milling,
Wet grinding — also called wet media milling — is often the preferred process for particle size reduction to a very fine scale, down to the micrometer and even nanometer range. Historical rotor–stator wet mill technologies are generally capable of achieving particles sizes down to ∼25 μm. Newer high-shear wet mills allow for a reduction of particle size High-Shear Rotor–Stator Wet Milling for Drug Substances:
احصل على السعر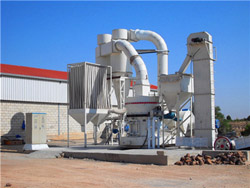
Wet Media Milling: An Effective Way to Solve Drug Solubility Issue
Wet media milling is a frequently used technique in pharmaceutical industry. It operates at both low and high energies. The particle-size reduction is mainly Wet-milling is a method of reducing the particle size of an API in suspension. It can readily achieve particle sizes (10-15 microns of mean volume) near to those of jet-mill micronization without many of The Advantages of Wet Mill Micronization in
احصل على السعر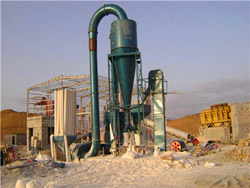
Enhanced Wet Milling Technology for API Size
Enhanced Wet Milling Technology for API Size Reduction 7 April 2021 Background Requirements For Milling API API Milling is a key step in many drug development processes. Advantages of milling vs. ABSTRACT: This study compares the use of wet milling and indirect ultrasound for promoting nucleation and controlling the particle size during the continuous Investigation of Wet Milling and Indirect Ultrasound as Means for
احصل على السعر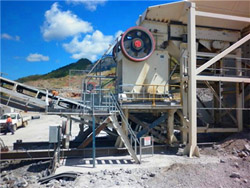
Mechanical Particle-Size Reduction Techniques
Wet-milling, also known as slurry milling, is a particle-size reduction process in which the solid particles are suspended in a liquid medium. As such, wet You've already forked mill 0 Code Issues Pull Requests Packages Projects Releases Wiki Activitymill/sbm ball milling method wiki.md at master mill
احصل على السعر
Mechanical Particle-Size Reduction Techniques SpringerLink
4.3.2 Wet-Milling. Wet-milling, also known as slurry milling, is a particle-size reduction process in which the solid particles are suspended in a liquid medium. As such, wet-milling has a number of advantages over dry-milling, thermal control over the process being one of the most prominent.The raw corn for wet milling should contain 15-16 per cent moisture and it should be physically sound. Insect and pest infested, cracked and heat damaged corns (treated at temperature around 75ᵒC during drying) are unsuitable for wet milling. The heat damaged corn affects the quality of oil extracted from its germ.PROCESSING TECHNOLOGY OF CEREALS ASFE 2201 Centurion
احصل على السعر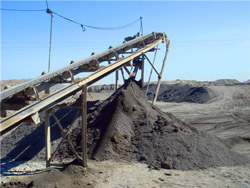
Ball milling as a synthesis method Solid State Chemistry @Aalto
Reactive ball milling can utilize this to produce i.e., oxidized end-products. [1, p.72–75] [4] Milling environment. Milling environment is an important factor that refers to ball milling mode: wet or dry. Wet mode utilizes the already mentioned PCAs that prevents excessive cold welding during the milling process.Size reduction is a necessary operation in mineral processing plants and provides the desired size for separation operations and the liberation of the valuable minerals present in ores. Estimations on energy consumption indicate that milling consumes more than 50 % of the total energy used in mining operations. Despite the fact Modeling of Bauxite Ore Wet Milling for the Improvement of
احصل على السعر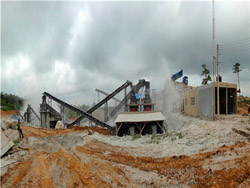
Foods Free Full-Text The Effect of Wet Milling and Cryogenic
Cryogenic milling on a large scale and wet milling on laboratory and large scale resulted in a particle size reduction to a d50 of 28–38 µm. In the milled samples, the wheat bran structure was broken down, and almost all cells were opened.Our conical mills are perfectly suited to both wet and dry applications. The versatility of the Uni-Mill means that the same machine can be used to mill wet and dry powders providing a cost effective solution for many manufacturers.. Dry Milling. Conical mills are most commonly used for the particle size reduction and de-agglomeration of Wet and Dry Milling Equipment Size Reduction Hanningfield
احصل على السعر
Wet Milling vs. Dry Milling in the Pharmaceutical Industry
Milling is used across a number of different industries and can be broadly divided into two types: wet milling and dry milling. When it comes to the manufacturing of pharmaceuticals, the particle size of ingredients is critical to a drug’s performance and efficacy, so the stakes are much higher than when milling foods or other consumer goods.Hockmeyer Equipment Corporation has been providing process solutions for over 80 years. We are a leader in the Wet Grinding and Dispersion Industry and offer custom designed processing equipment for mixing, blending, dispersing, and What’s the Difference Between Mixing, Dispersing, and Milling?
احصل على السعر
Wet Media Milling: An Effective Way to Solve Drug Solubility Issue
The wet mechanical size reduction of powder in agitated grinding media is used as a technique to prepare nanosuspension and was developed by In scale-up studies, similar particle size distribution was obtained. Milling resulted in superior size reduction yet keeping crystalline nature intact (Shegokar et al. 2011). LovirideComminution is the process where ore particles are liberated from gangue material through progressive size reduction in the form of crushing, grinding, cutting or vibrating. The costs associated with power supply, Gold extraction QueensMineDesignWiki
احصل على السعر
Mechanical Particle-Size Reduction Techniques SpringerLink
Due to the limitations found in either wet ball milling or high-pressure homogenization such as the need of a micronized suspension as the starting material, and the long runtimes required for particle-size reduction, new strategies that combine top-down and bottom-up approaches have been recently described (Moeschwitzer and Mueller To assess the performance of terminal wet milling, size distribution profiles are overlaid in Figure 4 in terms of seed/reference CSD and crystals produced from the same crystallization procedure but with different terminal wet milling conditions. It narrowed the size distributions by performing size reduction through wet milling,Effective Control of Crystal Size via an Integrated Crystallization
احصل على السعر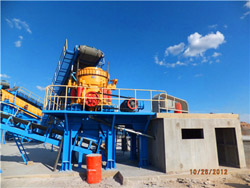
Modern Wet Milling and Material Processing PCI
November 1, 2012. The world of material processing and size reduction demands faster and more efficient methods to yield increasingly smaller sizes and narrower particle size distributions. Processes in a variety of industries now routinely demand particle sizes with an absolute maximum well below 1 micron.Wet ball milling. At first, wet ball milling process was used to segment the larger graphite particles into small size. Then, researchers have discovered that wet ball milling process can be used to produce graphitic sheets with a thickness of less than 10 nm. However, this milling approach was not used in order to producing graphene until Recent advances of the graphite exfoliation processes and
احصل على السعر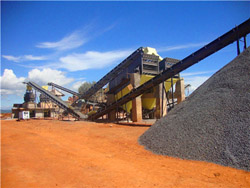
High-Shear Rotor–Stator Wet Milling for Drug Substances:
Wet milling is robust, relatively easy to use, broadly applicable, and offers both financial and API physical property advantages over dry milling. Historical rotor–stator wet mill technologies are generally capable of achieving particles sizes down to ∼25 μm. Newer high-shear wet mills allow for a reduction of particle size down to ∼10A schematic of possible mechanisms occurring during the wet media milling of drugs is shown in Figure 2.Particle size during milling generally depends on (i) process-equipment parameters; (ii) mechanical and physico-chemical properties of drug particles; and (iii) physical stability of the milled suspension, i.e., mitigation of aggregation Nanomilling of Drugs for Bioavailability Enhancement: A Holistic
احصل على السعر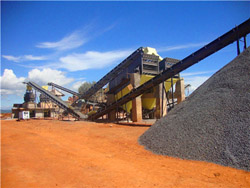
Overview of milling techniques for improving the solubility of
As the name suggests, wet milling involves size reduction of drug particles suspended in a liquid medium that may be aqueous or non-aqueous in nature. Wet milling is particularly suited for potent drugs and drugs which possess high residual moisture contents (>50% moisture) because dry milling may be problematic for drugs of Sizing (size reduction, milling, crushing, grinding, pulverization) is an important step in the process of tablet manufacturing. In manufacturing of compressed tablets, the mixing or blending of several solid pharmaceutical ingredients is easier and more uniform if the ingredients are about the same size. This provides a greater uniformity of dose.Tableting
احصل على السعر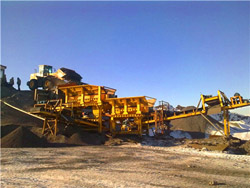
The Effect of Wet Milling and Cryogenic Milling on the Structure
With wet milling on a laboratory scale, particle size reduction was slower, and the d 50 only reached a plateau at 40 µm after 53 min of milling. This trend was also reflected in the d 90,meaning that the proportion of large particles still decreased until, respectively, 30 and 53 min, after which a plateau was reached, and 90% of the particles
احصل على السعر