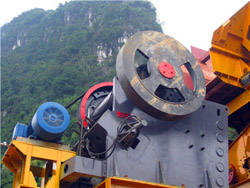
Raw Mill Raw Mill In Cement Plant AGICO Cement Raw Mill
Cement ball mill and cement vertical mill are two raw mills commonly used in cement plants. As the main cement equipment in the cement production line, the two cement A raw mill is the equipment used to grind raw materials into "rawmix" during the manufacture of cement. Rawmix is then fed to a cement kiln, which transforms it into clinker, which is then ground to make cement in the cement mill. The raw milling stage of the process effectively defines the chemistry (and therefore physical properties) of the finished cement, and has a large effect upon the effRawmill
احصل على السعر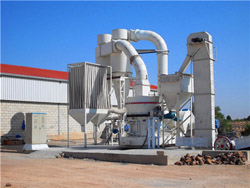
FL Smidth Atox® Raw Mill, Animation For Raw Grinding
5.4K views 6 years ago. FL Smidth Atox® Raw Mill, Animation For Raw Grinding. FL Smidth Atox® Raw Mill, Animation For Raw Grinding. Indonesian Cement Knowledge Share. 1.68K Customer stories Vertical roller mills offer supreme grinding with high energy-efficiency Whether grinding raw coal, clinker, cement and/or slag, we have a VRM solution to suit Vertical Roller Mills FLSmidth
احصل على السعر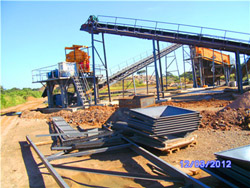
Reducing energy consumption of a raw mill in cement
Cement Raw mill Energy Exergy Efficiency Specific energy consumption 1. Introduction Cement production in the world is currently about 1.6 billion ton per year. The study indicates that for a dry type cement production process, the carbon dioxide emission intensity for kiln feed preparation process is about 5.4 kg CO 2 Reducing energy consumption of a raw mill in cement industry
احصل على السعر
Energy and exergy analyses of a raw mill in a cement
Energy and exergy analyses of a raw mill in a cement production Zafer Utlu a 1,Ziya Sogut a 2,Arif Hepbasli b 3,Zuhal Oktay c 4 Add to Mendeley The material efficiency values for a raw mill, pyro-processing tower, rotary kiln, clink cooler, and cement mill are determined to be 36.69%, 34.24%, 39.24%, Analysis of material flow and consumption in cement
احصل على السعر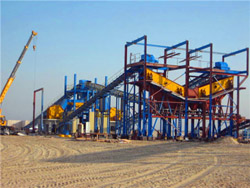
QCX® Automated Samplers FLSmidth
Our range of specialised sampling devices service all the routine sampling programs across the cement plant. They are designed to operate at frequent intervals (every ½, 1, 2, 4, 8 hours or longer) during normal operation. These samplers are permanently installed at designated locations and usually operate fully or semi-automatically.The ultimate ball mill with flexibility built in. You can’t optimise cement grinding with a one-size-fits-all solution. That’s why our ball mills are designed to adapt to your requirements, with a high degree of flexibility built in. You decide whether to operate the mill in open or closed circuit, with or without a pre-grinder and withBall mill for cement grinding FLSmidth
احصل على السعر
Review on vertical roller mill in cement industry & its
Now a days Cement plants are producing 75–80% PPC & 20–25% OPC due to high market demand of PPC. Production of PPC is cheaper and it's market rate is also lower than OPC by nearly 25 rupees per bag, so general consumer are attracted towards PPC cement. Cement companies also want to produce more and more PPC Figure 2.8: Showing the raw mill at stationary, Shayona cement factory. The raw mill has capac ity of 50 tons per hour and takes 300KW of electricity. The mill’s main(PDF) Mining Activities, Cement Production Process and
احصل على السعر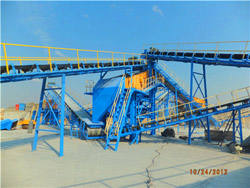
Parametric Studies of Cement Production Processes Hindawi
The cement industry is one of the most intensive energy consumers in the industrial sectors. The energy consumption represents 40% to 60% of production cost. Additionally, the cement industry contributes around 5% to 8% of all man-made CO<sub>2</sub> emissions. Physiochemical and thermochemical reactions involved in simulator was used for the thermodynamic performance of a raw mill (RM) and raw materials preparation unit in a cement plant in Nigeria using actual operating d ata. The raw mill has a capacity of 240,000 kilogram- material per hour. Also, both exergy and exergetic efficiency of raw mills from8VLQJ$VSHQ 3OXV6LPXODWRU IOPscience
احصل على السعر
Brooksville Cemex Plant Florida Department of Environmental
The site certification includes a woody biomass-fired electric generating unit, and associated support facilities including an on-site substation and approximately four miles of transmission line. Fuel Type. Woody biomass. Nominal Rating. 80 MW. Address/Location. 10311 Cement Plant Road. Brooksville, FL 34601. County.cement mill operations in four ways: • More consistent quality (grade). The continual monitoring of the mill loading and the adjustment of the feed and separator results in reduced variations in cement grade. This has the added benefit of a more consistent product quality. The control strategy is designed to respond to disturbances in theIndustrial : Optimization for the Cement Industry ABB
احصل على السعر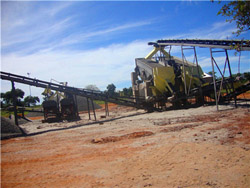
Reducing energy consumption of a raw mill in cement industry
While total electrical energy consumption for cement production is about 100 kWh/ton of cement, roughly two thirds are used for particle size reduction [2]. About 65% of the total electrical energy used in a cement plant is utilized for the grinding of coal, raw materials and clinker Fig. 1. The cement industry one of the worst pollutantVertical raw mill for sale! AGICO CEMENT is a cement equipment manufacturer offers raw mill used in cement plant, and other kinds of cement making machines. Customization service and 20+ years' experience. FREE Quotation now! Skip to content +86 13683722138. [email protected] Raw Mill Cement Raw Mill Raw Mill In Cement Plant
احصل على السعر
Raw Mill Feeding Cement Plant Optimization
Raw Mill Feeding. In the value stream map of cement manufacturing the raw mill feeding is an intermediate activity between Pre-homogenization and raw milling, and has not been discussed separately by most of the Distribution of dust emissions at bag filters in the cement mill section no.1 (mill filterpoint A and separator filter-point B, Figure 1) of the analyzed cement plant.(PDF) Dust Emission Monitoring in Cement Plant Mills: A
احصل على السعر
Reducing energy consumption of a raw mill in cement industry
About 2% of the electricity produced in the whole world is used during the grinding process of raw materials [1]. While total electrical energy consumption for cement production is about 100 kWh/ton of cement, roughly two thirds are used for particle size reduction [2]. About 65% of the total electrical energy used in a cement plant is utilizedThis paper presents aspects of monitoring material dust emissions from stationary emission sources (monthly dust measurements performed on cement mill stacks—mill outlet and separator outlet). Additionally, the Portland cement mill technological process (its component parts), as well as the solutions regarding the IJERPH Free Full-Text Dust Emission Monitoring in Cement Plant
احصل على السعر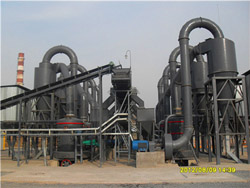
Analysis of Raw Mill Machines Maintenance in Cement Industry
The raw mill machine functions as a main material grinder in the initial milling process such as limestone, silica stone, clay, and iron sand to become raw mix. To find out the frequency of damageTable 5: Simulation results for the Mass balance of the local raw mill Mass Balance of Raw mill Input Output Material Unit Plant data Simulation Material Unit Plant data Simulation Raw feed kg/h 240000 240000 Raw meal kg/h 235300 231977 Moisture in raw feed kg/h 48000 48000 Gas kg/h 555260 558487 Hot gas from kiln kg/h 477086 477086 moisture (PDF) Thermodynamic Analysis of Raw Mill in Cement Industry
احصل على السعر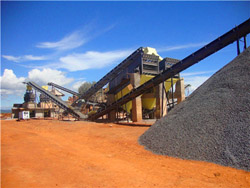
Digitization and the future of the cement plant McKinsey
There’s never been a more important time to build resilience into the core of the cement value chain: the cement plant. The cement industry is being hit hard by the COVID-19 pandemic, with global demand for cement expected to decline by 7 to 8 percent in 2020—though these declines have been unevenly distributed across regions. 1 Paul The cement industry is highly energy-intensive, consuming approximately 7% of global industrial energy consumption each year. Improving production technology is a good strategy to reduce the energy needs of a cement plant. The market offers a wide variety of alternative solutions; besides, the literature already provides reviews of Technological Energy Efficiency Improvements in Cement Industries
احصل على السعر
Know All About Cement Manufacturing Process in India mycem cement
Mining of limestone. Raw material preparation / raw mix preparation. Crushing. Homogenization. Proportioning of raw materials. Grinding. Storing and Blending. Burning of raw mix. Clinker grinding along with gypsum Cement.The raw mill is either a Ball mill with two chambers or Vertical roller mill with inbuilt classifier. Rashmi cement limited environmental pre feasibility report for Expansion of existing cement grinding plant from 0.96 MTPA to 1.11 MTPA by enhancing capacity of 2000 TPD VRM base grinding units to 2500 TPD, 2015. Google Scholar.Review on vertical roller mill in cement industry & its
احصل على السعر