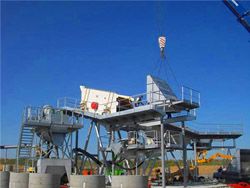
(PDF) Induction Furnace -A Review ResearchGate
Induction furnaces are systems where the heat is generated by induced currents by the electromagnetic field. Every The first phase of steelmaking using induction furnace melting is the scrap charging which could be done manually or by mechanical systems depending on the size and type Melting Time Prediction Model for Induction Furnace Melting
احصل على السعر
Electric Furnace Processes SpringerLink
The process in which steel is produced using scrap/sponge iron/pig iron is known as secondary route of steelmaking. The main furnaces that are used to produce When MBF was not in operation, the production of steel depended solely on induction furnaces. But, the scrap available in the country was found to be mixed Iron making in induction furnace for casting steel billets
احصل على السعر
Melting and treatment of steel for casting ScienceDirect
Charge materials The composition of steel melted in the induction furnace changes little during melting so that careful selection of charge materials is necessary. Aim: The aim of the research is to automate the calculation of the furnace charge for obtaining a melt with a given set of physical, mechanical and operational Melting of large steel scrap in induction furnaces ResearchGate
احصل على السعر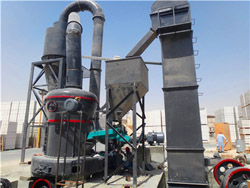
Studies on direct reduced iron melting in induction
The induction heating model of two-phase melt in the iron removal process in an electromagnetic induction furnace was established, in which the real-time coupling of electromagnetic fieldfurnace copper scrap charging melting refining Prior art date Legal status (The legal status is an assumption and is not a legal conclusion. Batch charge conveying US20150159954A1 System and Method for Charging a Furnace
احصل على السعر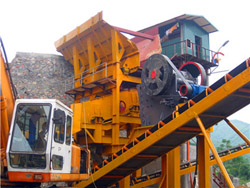
Simulation and Techno-Economic Performance of a Novel Charge
quired for induction furnace melting of scrap, this study presents a parametric and validation study to understand the charge balancing, furnace bath melt op-timization, and ferroalloys savings possible with induction furnace melting. 2. Materials and Method The numerical model is developed using the principle of materials balance andFig 1 Major thermal losses in induction furnace. The factors which affects the consumption of electrical energy in the furnace (Fig 2) include (i) dirt going in the furnace with scrap, (ii) rusty charge Production of Steel in Induction Furnace IspatGuru
احصل على السعر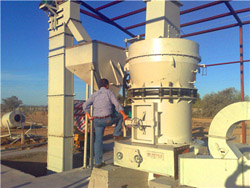
Iron making in induction furnace for casting steel billets
To avoid off grades, hot metal was produced by melting the mixed scrap. In this method, the charge mix was so designed that, the metal tapped from induction furnace contains carbon in the range of 3.0–––3.5%, which was then converted into steel in EOF and was subsequently cast into billets to cater to the needs of Syria. 4)The usual practice is to charge a basket of scrap which representing from 20 to 50% of total charge, to melt that scrap partially to create a molten pool and then to feed sponge iron at a particular rate. 100% sponge iron charge is achieved by keeping a heel of molten metal (about 20–25%) in the furnace after tapping and then feeding Electric Furnace Processes SpringerLink
احصل على السعر
Studies on direct reduced iron melting in induction furnace
In the last two decades, the use of a combination of scrap and high-quality scrap substitutes (Direct Reduced Iron (DRI) and Pig Iron) by the steelmakers has been steadily increasing due to theThe results validate the suitability of the developed model as a functional system of induction furnace melting for combined charge calculation and melt optimization Techno-economic evaluation results showed that 0.98% 0.25% ferroalloy saving per ton of melt is possible using the model.Simulation and Techno-Economic Performance of a Novel Charge
احصل على السعر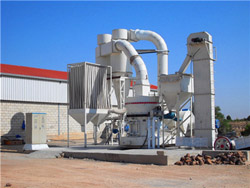
Molten Metal Splash and Furnace Refractory Safety
By diligently examining and treating scrap, following induction furnace safety procedures, properly training and retraining personnel, and use of automated melt shop equipment, founders can be confident their operations are as safe as possible. Wet charge materials are a serious safety hazard in all foundries.The induction stirring accelerates the transfer of heat and promotes the melting of DRI. The effect of partial replacement of scrap by DRI on various melting parameters has been studied.STUDIES ON DIRECT REDUCED IRON MELTING IN INDUCTION FURNACE
احصل على السعر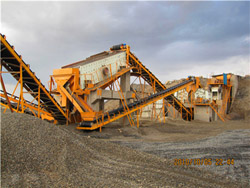
(PDF) Modeling the Effect of Scrap on the Electrical Energy Consumption
The melting time of scrap is a factor that affects the Electrical Energy (EE) consumption of the Electric Arc Furnace (EAF) process. The EE consumption itself stands for most of the total energyThe first phase of steelmaking using induction furnace melting is the scrap charging which could be done manually or by mechanical systems depending on the size and type of the induction furnace [2]. To achieve the desired final melt composition, initial charge preparation must have been done prior to scrap charging.Melting Time Prediction Model for Induction Furnace Melting
احصل على السعر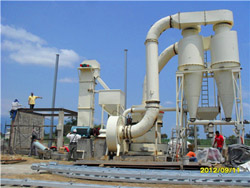
Phosphorous Control in Induction Furnace Steel Melting using
The extent of dephosphorization in the induction furnace with available DRI and steel scrap is in the range of 24.44% to 54.44% by using LD slag. Experimental result it shows that the aluminium and silicon level in the final product have increased. The acidic lining of the induction furnace may be responsible for it.Process algorithm, numerical model and techno-economic assessment of charge calculation and furnace bath optimization for target alloy for induction furnace-based steelmaking is presented in this study. The developed algorithm combines the make-to-order (MTO) and charge optimization planning (COP) of the steel melting shop in the production of target Simulation and Techno-Economic Performance of a Novel Charge
احصل على السعر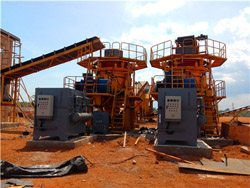
Melting Time Prediction Model for Induction Furnace
The first phase of steel making using induc tion furnace melt ing is the scrap charging which c ould be done manu ally or by mec hanical systems de pending on the size and type of the indu ctionInduction Furnace Manipulator for 60 Tons Induction Furnace Pushing Scrap Steel US $17,800-19,800 / Piece Scrap Steel Charging Machinery for 90t Induction Furnace ManipulatorMeltshop Induction Furnace Hydraulic Feeding Car
احصل على السعر
IS 12668 (1989): Melting characterstics of sponge iron/direct
( DRI 1 in electric arc furnace, in basic oxygen furnace when used as coolant, in cupola furnace and in induction furnace. 1.2 This standard should be read in conjunction with IS 10812 : 1984. 2 REFERENCES 2.1 The following Indian Standards are necessary adjuncts to this standard: IS 5842 : 1986 IS 10812 : 1984 IS 11348 : 1985 IS 11896 : 1986induction furnace. The charge mixes used are cast iron, sponge iron and steel scrap. Amount of sponge iron in the charge mix is considered 50 %. Degree of dephosphor-ization is discussed in terms of phosphorous distribution ratio. In subsequent work, phosphate capacity and chemical equilibria of dephosphorization reaction will be discussed.Removal of Phosphorous from Steel Produced by Melting Sponge
احصل على السعر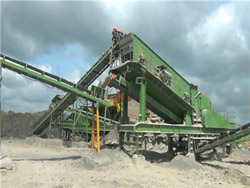
Iron making in induction furnace for casting steel billets
ES is producing 130 mm 2 mild steel billets to cater to the needs of rolling mills in Syria. An induction furnace is an electrical furnace in which the heat is applied by induction heating of metal for the production of steel [1]. Since no arc or combustion is used, the temperature of the material is no higher than required to melt it; this canfurnaces directly. For electric induction furnaces, however, the scrap metal added to the furnace charge must first be pretreated to remove grease and oil. Scrap metals may be degreased with solvents, by centrifugation, or by preheating to combust the organics. 12.10.2.2 Metal Melting The furnace charge includes metallics, fluxes, and fuels.12.10 Gray Iron Foundries U.S. Environmental Protection Agency
احصل على السعر
Simulation environment for Charge Optimization (Tros Version
The induction furnace steel which contributes about 70% of secondary steelmaking operates by charging of cold scrap into it and melting takes place by the energy resulting from electromagnetic
احصل على السعر