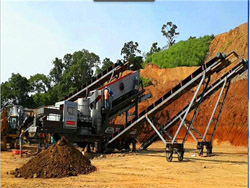
Grinding Mill an overview ScienceDirect Topics
The principle objective for controlling grinding mill operation is to produce a product having an acceptable and constant size distribution at optimum cost. To achieve grinding tools which can lead to a considerable deterioration of the mill's performance. Therefore, it is necessary to sepa-rate the metal components before grinding (e.g. with The Art of Milling Metrohm
احصل على السعر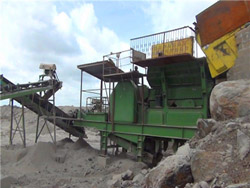
Fine grinding in a horizontal ball mill ScienceDirect
Fine grinding in a horizontal ball mill T. Partyka,D. Yan Add to Mendeley https://doi/10.1016/j.mineng.2006.12.003 Get rights and content Abstract The fine 1.1. Fine grinding in the mining industry It has been estimated that approximately 2% of the world's energy usage is applied to mineral comminution, and Stirred media mills in the mining industry: Material
احصل على السعر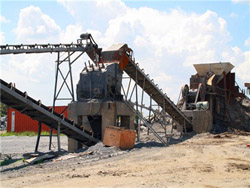
Analysis of grinding in a spiral jet mill. Part 1: Batch grinding
The jet mill comprises a cylindrical grinding chamber, grinding nozzles at the periphery and a central tube as an outlet for air. Particles are prevented from leaving The General Kinematics VIBRA-DRUM® Grinding Mill is a high-energy vibratory drum mill that can be used to grind various materials, including cement, iron Industrial Grinding Machines: How it Works General
احصل على السعر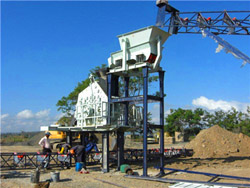
Minerals Free Full-Text Grinding Media Motion and
Product fineness during grinding in stirred media mills is mainly influenced by the specific energy input, the stress energy transferred by the colliding grinding media and the stress frequency. The stress the mill surfaces (improving grinding efficiency), and to assist in handling the ground product. The latter reason is of particular importance in continuous flow grinding. In this case the mill forms part of an ore processing circuit; the material is fed into one end of the mill, and after being ground it is discharged by means of a scoop, orINFLUENCE OF VISCOSITY ON GRINDING IN BALL-MILLS. A thesis
احصل على السعر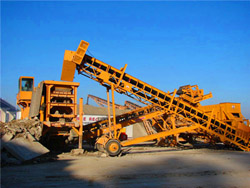
AMIT 135: Lesson 6 Grinding Circuit Mining Mill
Grinding takes place in more “open” space which makes the retention time longer and adjustable compared to crushers. Theoretical size reduction and power ranges for different grinding mills [image: (135-6-1)] AG/SAG Abstract The grinding of material in a vibrational mill is considered. Grinding is regarded as a random process consisting of a series of uniform events. The process is assumed to be steady, simple, and ordinary. We interpret grinding in a vibrational mill as a random Markov process. The calculation is based on the Pulverization Kinetics in a Vibrational Mill SpringerLink
احصل على السعر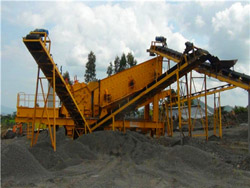
The effect of grinding conditions on the flotation of a sulphide
Grinding in ceramic mill (ceramic balls) and lined steel mill (stainless steel rods) yielded positive values of the pulp rest potential, approximately +200 mV, the oxidising environment being caused dissolved oxygen. This. Conclusions. The grinding conditions affect significantly the subsequent flotation stage of this sulphide copper ore.The pebble mill is the name associated with a mill in which the grinding bodies are natural pebbles or possibly ceramic bodies; the general proportions of the mill being as for a “ball mill”. It will be noticed that the differentiation between ball mill and the tube mill arises only from the different length to diameter ratios involved, and not from Grinding Mills Common Types 911 Metallurgist
احصل على السعر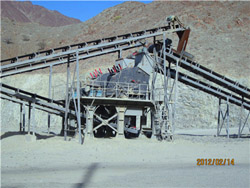
Analysis of grinding in a spiral jet mill. Part 2: Semi-batch grinding
The focus of the present study is on grinding and classification in a spiral air jet mill (Andrews, 1936), shown schematically in Fig. 1. Particles in the mill are accelerated by high speed tangential jets and are pulverized by interparticle collisions and collisions with the mill walls. The ground particles exit the mill from the centralThis work concentrates on the energy consumption and grinding energy efficiency of a laboratory vertical roller mill (VRM) under various operating parameters. For design of experiments (DOE), the response surface method (RSM) was employed with the VRM experiments to systematically investigate the influence of operating parameters on Minerals Free Full-Text Analysis and Optimization of Grinding
احصل على السعر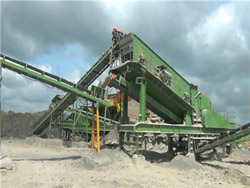
Fine grinding in a horizontal ball mill ScienceDirect
Fine grinding in traditional ball mills has not been utilised in the past due to the following perceived disadvantages: • The mill speed has to be lower than the centrifugal speed of the mill otherwise the whole charge will rotate with the mill body and no grinding will occur. This speed limit fixes the maximum electrical power the mill canComparison of various milling technologies for grinding pharmaceutical powders Mostafa Nakacha, Jean-Rene´ Authelina, Alain Chamayoub,*, John Doddsb aAventis Pharma, 13 Quiai Jules Guesde, 94400 Vitry sur Seine, France bEcole des Mines d’Albi-Carmaux, Campus Jarlard, 81013 Albi, France Abstract This paper examines fine grinding Comparison of Various Milling Technologies Accueil
احصل على السعر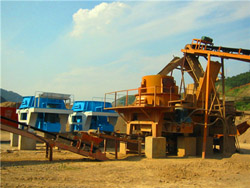
Minerals Free Full-Text Effect of Grinding Media Size
The aim of this study is to evaluate the effect that the size of grinding media exerts on ferronickel slag milling efficiency and energy savings. A series of tests were performed in a laboratory ball mill using The alumina powder was wet ground in a planetary mill (Pulverisette-5, Fritsch GmbH, Germany) consisting of four stainless steel pots, each of 250 ml volume, and zirconox media supplied by Jyoti Ceramics (Nasik, India). Grinding balls of four different sizes 2.8–3.3 mm, 1.7–2.4 mm, 0.7–1.2 mm and 0.4–0.7 mm were used.Modeling and Simulation of Ultrafine Grinding of Alumina in a
احصل على السعر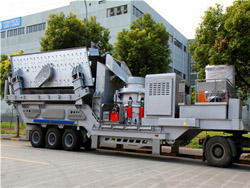
Optimization of the SAG Grinding Process Using Statistical
2. Background. The SAG grinding process has been modeled by various authors, either generating explanatory models of the grinding process, with the aim of modeling, simulating, and optimizing the individual process, as well as integrating it into aggregate processes, such as the mine-to-mill (M2M) paradigm, a practice that has 13.1.1.2 Medium-speed mill. Medium-speed mills are smaller than low-speed units and are generally of the vertical spindle construction. The speed of the grinding section of these mills is usually 75–225 rpm. They operate on the principles of crushing and attrition. Pulverization takes place between two surfaces, one rolling on top of the other.Mill Speed an overview ScienceDirect Topics
احصل على السعر
Grinding in Ball Mills: Modeling and Process Control Sciendo
on mill dimensions, the type of the mill (overflow or grate discharge), the speed of rotation, the mill loading, the final product size required from a given feed size (coefficient of reduction), the work index of the material, the mill shaft power and the specific gravity of the material. These parameters are thoroughly studied inThis review paper is mainly going to focus on the effect of grinding media on ball mill performance. Grinding media directly affects energy consumption, product size and consequently the grinding costs [11]. Proper selection of the grinding media reduces energy and material consumption in a ball mill. Different performances are achieved whenGrinding Media in Ball Mills-A Review Preprints
احصل على السعر
Impact of grinding aids and process parameters on dry stirred media
The dry fine grinding experiments were carried out in a self-constructed batch-wise operated vertical stirred media mill shown in Fig. 1. The agitator is driven by a Dispermat AE-06 by VMA-Getzmann, Germany. The mill consists of a 1.6 L stainless steel grinding chamber (2). The chamber was designed with rounded edges to ensure a Grinding Mill Circuits A Survey of Control and Economic Concerns. In: Proceedings of the 17th World Congress of the International Federation of Automatic Control, Seoul, Korea, 6-11 July 2008, 1000-1005. 10.3182/20080706-5-KR-1001.00171 Search in Google Scholar. 49. Wills, B. A., T. J. Napier-Munn.Grinding in Ball Mills: Modeling and Process Control Sciendo
احصل على السعر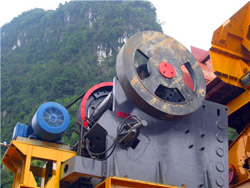
Grinding in Ancient and Modern Palestine on JSTOR
Gustaf Dalman, Grinding in Ancient and Modern Palestine, The Biblical World, Vol. 19, No. 1 (Jan., 1902), pp. 9-18grinding tools which can lead to a considerable deterioration of the mill's performance. Therefore, it is necessary to sepa-rate the metal components before grinding (e.g. with mag-netic forces). If required, they have to be evaluated sepa-rately. Embrittlement (with liquid nitrogen or dry ice) Cooling the sample material oftenThe Art of Milling RETSCH
احصل على السعر