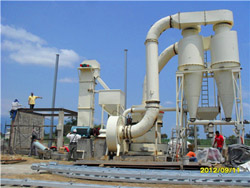
Overview of cement grinding: fundamentals, additives,
Grinding is an essential operation in cement production given that it permits to obtain fine powder which reacts quickly with HOROMILL<sup>R</sup> has introduced in this field an entirely new grinding process to reduce energy consumption with an original design, for both (PDF) Pregrinding technology ResearchGate
احصل على السعر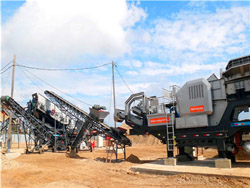
OPTIMIZING THE CONTROL SYSTEM OF CEMENT MILLING:
Abstract Based on a dynamical model of the grinding process in closed circuit mills, efficient efforts have been made to optimize PID controllers of cement milling. The The modular vertical roller mill for grinding cement raw material, cement clinker, and additives with an installed power of up to 12,000 kW was specifically Grinding process optimization IEEE Xplore
احصل على السعر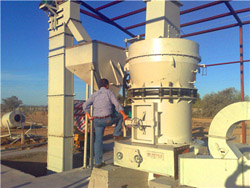
Modeling of energy consumption factors for an industrial cement
Lin, X. & Liang, J. Modeling based on the extreme learning machine for raw cement mill grinding process. in Proceedings of the 2015 Chinese Intelligent To optimise cement grinding, standard Bond grinding calculations can be used as well as modelling and simulation techniques based on population balance Cement grinding optimisation ScienceDirect
احصل على السعر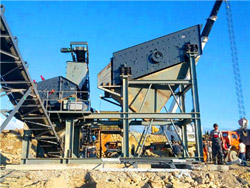
Predictive Controller Design for a Cement Ball Mill
The process model considered in this study is based on first principles which did not exhibit the process dynamics of the real-time scenario. A hybrid model was developed for controlling the cement ball Cement grinding process. The whole workflow of the cement grinding plant is as follows: the cement clinker, gypsum, and mixture in the cement silo are mixed by the belt conveyor in a certain proportion and transported to the cement roller press, cement mill or group of them for grinding.Cement Grinding Plant Overview Cement Grinding Unit AGICO Cement
احصل على السعر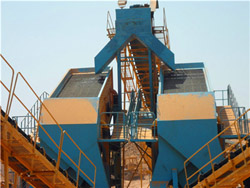
Cement Grinding 911 Metallurgist
This phase of grinding may be either the wet or dry process, the end product going to a kiln. Material ground consists of limestone, High Efficiency Cement Grinding Mill. by David Michaud cement ball mill. Application: limestone, clay, coal, feldspar, calcite, talc, iron ore, copper, phosphate, graphite, quartz, slag. Capacity: 0.65-615T/H. The cement ball mill usually can be applied to raw meal grinding or Raw Mill, Cement Raw Mill, Raw Mill In Cement
احصل على السعر
The Decision Algorithm of Cement Mill Operation Index Based
The cement grinding system consists of a coarse grinding system mainly by roller press and a fine grinding system by ball mill, the energy flow in the grinding process moves along the material and gas paths, as shown in Fig. 2, which shows the equipment composition and production diagram of the cement grinding system, where The cement manufacturing process involves the extraction and processing of raw materials, such as limestone, clay, and shale, which are then heated in a kiln at high temperatures to form clinkerCement Manufacturing Process and Its Environmental Impact
احصل على السعر
11.6 Portland Cement Manufacturing U.S. Environmental
L. Clinker grinding -17 M. Cement silos -18 N. Cement load out -19 O. Raw mill feed belt -24 P. Raw mill weigh hopper -25 Q. Raw mill air seperator -26 R. Finish grinding mill feed belt -27 S. Finish grinding mill weight hopper -28 T. Finish grinding mill air seperator -29 U. Preheater kiln 3-05-006-22Cement production process typically involves: •. grinding limestone (and other raw materials to achieve the right chemical composition) to about 90% passing 90 μm in a dry circuit, •. making cement by the chemical reaction between the components of the ground mixture. This chemical reaction occurs at high temperature in a rotary kiln, •.Cement grinding optimisation ScienceDirect
احصل على السعر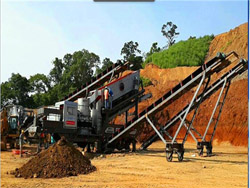
Energy and exergy analyses for a cement ball mill of a
Request PDF Energy and exergy analyses for a cement ball mill of a new generation cement plant and optimizing grinding process: A case study Nowadays, ball mills are used widely in cementincreasing output, lowering breakdowns and optimizing the grinding process which eats almost 60% of power cost. In recent years vertical roller mill (VRM) has proved to be a popular choice for finished cement grinding due to Indicate Contributions from Several Radial VHYHQ4&WRROV
احصل على السعر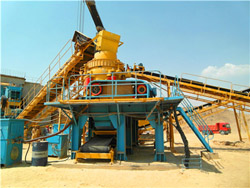
Grinding process optimization IEEE Xplore
Abstract: As a world-wide leader in grinding solutions for the cement industry and understanding the changing needs of cement producers and how to tailor solutions to meet those needs. Optimizing output, improving efficiency, and reducing CO2 emissions while keeping investment costs to a minimum are common challenges that the Fine grinding in general is extremely inefficient. The better mills on the market have an efficiency of about 8-9 % which means that only 8-9 % of the energy results in grinding and the majority is converted mainly into Process Training Ball Mill INFINITY FOR CEMENT
احصل على السعر
Cement Ball Mill Cement Grinding Machine
The cement ball mill is a kind of cement grinding mill.It is mainly used for grinding the clinker and raw materials of the cement plant, and also for grinding various ores in metallurgical, chemical, and electric power Therefore, producing cement with less energy is becoming a key element of profitability: as the grinding process consumes about 60 per cent of the total plant electrical energy demand and about 20 per cent of cement production variable cost. So efficient grinding unit selection impacts profitability of cement manufacturing.Efficient grinding unit selection impacts profitability Indian Cement
احصل على السعر
Ball Mill & Roller Press for Cement Grinding Process
The combined grinding system of roller press and ball mill. With the invention of V-type separator, the combined grinding system composed of roller press and ball mill has been developed to further reduce the energy consumption of the cement grinding process. In this system, the ground materials from the roller press is first processed by theCement grinding process is the reduction of clinker produced in rotary kilns to a fine form. The clinker has to be ground with the addition of gypsum to get the finish product, cement. The objective is to increase the specific surface of the cement component with a proper particle size distribution and to provide convenient reactivity of cement A Review on Pyroprocessing Techniques for Selected Wastes
احصل على السعر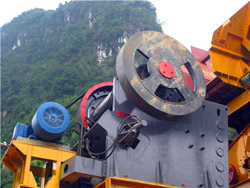
Cement Grinding Mill Ball Mill, Vertical Cement Mill, Cement
The ball mill is a key piece of equipment for grinding after the material is crushed. Regardless of its specific type, a ball mill typically consists of five main components: feeding device, support device, rotating part, discharge device, and transmission device. By understanding the main stages and equipment involved in the The vertical roller mill (VRM) is a type of grinding machine for raw material processing and cement grinding in the cement manufacturing process.In recent years, the VRM cement mill has been equipped in more and more cement plants around the world because of its features like high energy efficiency, low pollutant generation, small floor area, etc.. Vertical Roller Mill Operation in Cement Plant
احصل على السعر
An industrial comparative study of cement clinker grinding
Cement Grinding Office (2016) reported that small percent of the total energy supplied to the mill systems is used efficiently, while the rest is converted to heat; the energy produced heats up the ground cement in the mill and can cause the ambient temperature of the mill to rise depending on the initial temperature of the clinker and the Clinker is extracted from our clinker tank and transported to the cement mill hopper by belt conveyors. A measured quantity of clinker and gypsum is fed into our closed-circuit ball mill which incorporates with a high-efficiency separator. OPC is produced by the inter-grinding and blending of 95% clinker with 5% gypsum to a fineness of 280 m 2 /kg.Cement Grinding Cement manufacturing process Priya Cement
احصل على السعر
How can we improve cement mill production? LinkedIn
To improve cement mill production, consider increasing the mill's capacity, optimizing operating parameters, improving the grinding process, enhancing separator efficiency, and implementing online
احصل على السعر