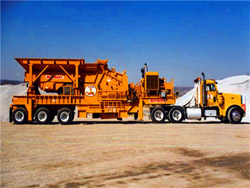
Future Grinding Technologies
In 2014 the European Cement Research Academy (ECRA) started its cross-sectoral research project “Future Grinding Technologies” in order to optimise and develop The increasing demand for “finer cement” products, and the need for reduction in energy consumption and green house gas emissions, reinforces the need for Cement grinding optimisation ScienceDirect
احصل على السعر
Modernizing cement manufacturing in China leads to substantial
The cement manufacturing process mainly includes four steps: resource extraction, raw material preparation, clinker calcination, cement grinding 17,18, and Grinding is an essential operation in cement production given that it permits to obtain fine powder which reacts quickly with water, sets in few hours and hardens over a period of weeks....Overview of cement grinding: fundamentals, additives,
احصل على السعر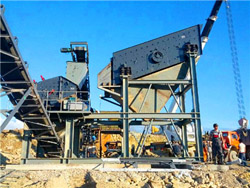
Grinding process optimization IEEE Xplore
Abstract: As a world-wide leader in grinding solutions for the cement industry and understanding the changing needs of cement producers and how to tailor Dominican Republic: Germany-based Gebr. Pfeiffer has received an order for an MVR 3750 C-4 vertical roller mill from Estrella Group subsidiary Cemento Grinding mill Cement industry news from Global Cement
احصل على السعر
Review on vertical roller mill in cement industry & its
All grinding processes in the cement industry are operated dry. The capacities of grinding mills range from 300 − 1000 TPH for Limestone and for cement Controlling grinding aid in cement industry. Oct 13, 2022. A major cement producer chose Flowrox™ metering pumps to control grinding aid in cement Controlling grinding aid in cement industry Valmet
احصل على السعر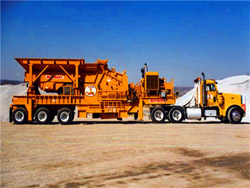
Cement grinding optimisation ScienceDirect
Cement production process typically involves: •. grinding limestone (and other raw materials to achieve the right chemical composition) to about 90% passing 90 μm in a dry circuit, •. making cement by the chemical reaction between the components of the ground mixture. This chemical reaction occurs at high temperature in a rotary kiln, •.have higher production capacities and greater fuel efficiency compared to other types of cement kilns. Table 1 shows typical average required heat input by cement kiln type. Table 1. Typical Average Heat Input by Cement Kiln Type Kiln Type Heat Input, MMBtu/ton of cement Wet 5.5 Long Dry 4.1 Preheater 3.5 Preheater/Precalciner 3.1AVAILABLE AND EMERGING TECHNOLOGIES FOR REDUCING GREENHOUSE GAS
احصل على السعر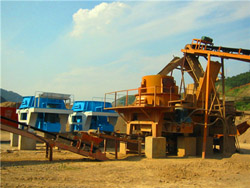
Review on vertical roller mill in cement industry & its
All grinding processes in the cement industry are operated dry. The capacities of grinding mills range from 300 − 1000 TPH for Limestone and for cement grinding it varies from minimum 50 TPH while larger installations are up to 450 TPH [8].There are four stages in the manufacture of portland cement: (1) crushing and grinding the raw materials, (2) blending the materials in the correct proportions, (3) burning the prepared mix in a kiln, and (4) grinding the burned product, known as “ clinker ,” together with some 5 percent of gypsum (to control the time of set of the cement).Cement Extraction, Processing, Manufacturing Britannica
احصل على السعر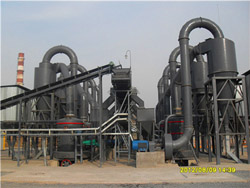
AN INTRODUCTION TO THE CEMENT MANUFACTURING
The course’s first objective is to give an overview of the process chain within the cement industry. All the main processes involved during cement production will be discussed, including the extraction and processing of raw materials, the combustion process, cement grinding, quality control and storage, and cement distribution.Cement grinding aid is a kind of material which can promote cement grinding, and it is an important part of energy-saving development of industry at present. It can not be ignored in improving cement technology. Based on this, this paper analyzes the influencing factors of grinding aid effect in cement grinding process. 1. PrefaceVLVRQ,QIOXHQFLQJ)DFWRUVRI*ULQGLQJ$LG Condition
احصل على السعر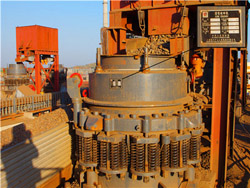
Digitization and the future of the cement plant McKinsey
There’s never been a more important time to build resilience into the core of the cement value chain: the cement plant. The cement industry is being hit hard by the COVID-19 pandemic, with global demand for cement expected to decline by 7 to 8 percent in 2020—though these declines have been unevenly distributed across regions. 1 Paul Cement Manufacturing Process Phase II: Proportioning, Blending & Grinding. The raw materials from quarry are now routed in plant laboratory where, they are analyzed and proper proportioning of limestone and clay are making possible before the beginning of grinding. Generally, limestone is 80% and remaining 20% is the clay.Cement Manufacturing Process Phases Flow Chart Cement
احصل على السعر
POWERING THE CEMENT INDUSTRY CEMBUREAU
POWERING THE CEMENT INDUSTRY . Cement is an energy-intensive industry, but currently, electricity accounts for circa 12% within (25% each), then 43% for cement grinding and the remaining for raw material extraction, fuel grinding and for packing and loading. Both the relative share in the energy mix and the us ages are expected to Founder Director, World Cement Association, at Indian Cement Review 2023. The 3-in-1 event comprising Indian Cement Review (ICR) Conference, Awards and Cement EXPO 2023 scheduled on 14-15th December 2023 at Manekshaw Centre in Delhi is expected to attract cement industry captains, plant heads, over 100 exhibitors and Milestone Trends in Indian Cement Industry
احصل على السعر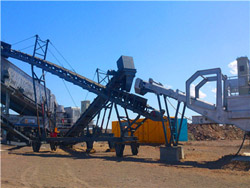
Modeling of energy consumption factors for an industrial cement
Cement production is one of the most energy-intensive manufacturing industries, and the milling circuit of cement plants consumes around 4% of a year's global electrical energy production. It isCement grinding with our highly efficient ball mill. An inefficient ball mill is a major expense and could even cost you product quality. The best ball mills enable you to achieve the desired fineness quickly and efficiently, with minimum energy expenditure and low maintenance. With more than 4000 references worldwide, the FLSmidth ball mill isBall mill for cement grinding FLSmidth
احصل على السعر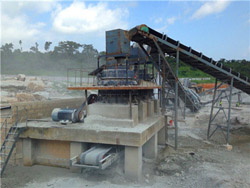
Towards a business case for CO2 mineralisation in the cement industry
The cement industry, an industry characterised by low margins, While the pre-treatment of the minerals (crushing and grinding) can be seen as mature (technology readiness level (TRL) 9),Christian Pfeiffer develops equipment for cement grinding since 1925. en Englisch. en Englisch de Deutsch. Navigation. Home; Industries. Cement; Because we don’t just want to keep pace, we want to move ahead, to make a contribution to shaping the cement industry with our ideas. We do that by constantly improving our: Engineering expertiseChristian Pfeiffer cement industry Christian Pfeiffer
احصل على السعر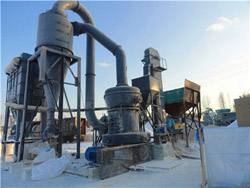
A Review on Pyroprocessing Techniques for Selected Wastes
Grinding systems in the cement industry play an important role in the distribution of the particle size and particle shape . The size and shape of the cement particles affect the reactivity of the clinker. They also affect the dependence on temperature of dehydrating gypsum that is ground together with the clinker.The increase in CL due to GA additions is a common phenomenon in the cement grinding industry, mostly attributed to a decrease in MRT and improved cement flowability [11, 18, 26]. In other words, the use of GA makes coarser the product that leaves the mill (B1), thereby requiring increased number of passages through the system to Industrial versus Laboratory Clinker Processing Using Grinding
احصل على السعر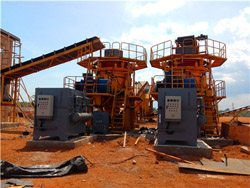
Grinding process optimization IEEE Xplore
As a world-wide leader in grinding solutions for the cement industry and understanding the changing needs of cement producers and how to tailor solutions to meet those needs. Optimizing output, improving efficiency, and reducing CO2 emissions while keeping investment costs to a minimum are common challenges that the modular vertical 3 WATERPROOFING BASEMENT WATERPROOFING WITH Sikaplan® SHEET MEMBRANES CEMENT SOLUTIONS FOR THE CEMENT INDUSTRY CONTENTS 04 Cement Industry 06 Solutions for Cement Plants 08 Small but with Huge Impact 10 Efficient Grinding Processes 14 Cement Additives 16 Additives as Enablers of Brochure Solutions for Cement Industry Sika
احصل على السعر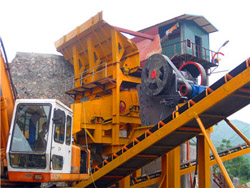
Cement grinding optimisation ScienceDirect
Grinding occurs at the beginning and the end of the cement making process. Approximately 1.5 tonnes of raw materials are required to produce 1 tonne of finished cement. The electrical energy consumed in the cement making process is in order of 110 kWh/tonne and about 30% of which is used for the raw materials preparation and
احصل على السعر