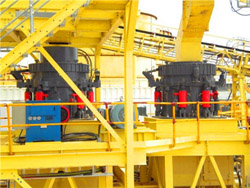
Manufacturing of aluminum flake powder from foil scrap by
Aluminum flake powder can be produced using aluminum foil scrap in the dry ball milling process. During the ball milling the foil is laminated, micro-forged, cracked continuously, and then finally formed into a flake shape powder.The process of ball milling involves the grinding and mixing of metal particles within a ball mill, which is a type of equipment used for grinding, with the aim of producing a fine powder . This method has been Producing Metal Powder from Machining Chips
احصل على السعر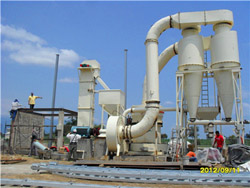
Role of Ball Milling of Aluminum Powders in Promotion of Aluminum
Effect of ball milling (BM) of an aluminum powder on hydrogen generation through a reaction with hot water was investigated. BM increased surface area of the A numerical dynamic-mechanical model of a planetary ball-mill is developed to study the dependence of process efficiency on milling parameters like ball size and Modeling of the planetary ball-milling process: The case
احصل على السعر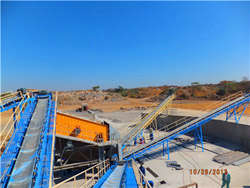
Manufacturing of aluminum flake powder from foil scrap by dry ball
The dry ball milled powder from atomized powder is used mainly in aerated light-weight concrete, fingerprint detection and fireworks [1]. One of the applications of The aluminum flake powder produced by the dry ball milling of aluminum foil scrap can be applied to fingerprint detection or to aerate light-weight concrete.Manufacturing of Aluminum Flake Powder From Foil Scrap by Dry Ball
احصل على السعر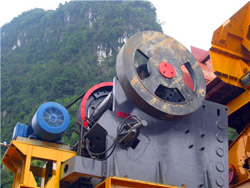
Effect of ball size on steady state of aluminum powder and efficiency
A scanning electron microscope and X-ray diffractometer were used to analyze the copper powder particle size, morphology, structure, and crystallite size. The High-energy ball milling is a manufacturing technique used to reduce, mix, and alloy particles in the ceramic and powder processing industries ( Koch, 1993 ), Dynamic stress-strain response of high-energy ball milled aluminium
احصل على السعر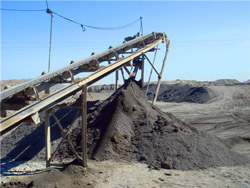
The influence of wet milling of aluminum and aluminum alloys powder
Materials Engineering Aluminum Alloys The influence of wet milling of aluminum and aluminum alloys powder screenings on the characteristics of the The effects of high energy milling on the shape, size and low temperature sinterability of plate-like alumina powder was studied. The milling effects were studied Effect of high energy ball milling and low temperature
احصل على السعر
Particle morphology control of metal powder with
Mechanical milling was performed by using a planetary ball mill (PBM) under various experimental conditions. Copper powder (99.0% purity, median particle size x 50 = 45 μm, Aldrich chemistry) was used as shown in Fig. 1.Mechanical alloying (MA) was carried out at two types of rotation speeds: low (10, 50, and 100 rpm) and high (300, 500, We are having 8 Dry ball mills of various sizes. Its having a installed capacity of 150 Metric Tons per month. Wet ball mill is a type of grinder used to grind Atomized Aluminium Powder with White spirit and Coating material for use in Industrial Roof Coating, Anti corrosive, Heat Resistant, Hammer Tone, Aerosols etc. We are having 2 Wet ballInfrastructure Sri-Kaliswari Metal Powders (P) Ltd
احصل على السعر
Research in the Area of Preparing Activated
Results of studying preparation of activated finely dispersed alpha-alumina by dry milling in a ball mill are presented. The α-Al2O3 refinement mechanism is considered. It is shown that the powder The effects of high energy milling on the shape, size and low temperature sinterability of plate-like alumina powder was studied. The milling effects were studied under three different processing conditions, designed by varying the charge ratio and the milling medium. 10:1 and 20:1 ball to powder charge ratios were considered in wet and dry Effect of high energy ball milling and low temperature
احصل على السعر
Study on Preparation, Application and Modification of Flake Aluminium
Aluminum powder (Al) is an important raw material in solid propellants [1,2,3,4,5].As fuel, Al is an important component of solid propellant [6,7,8], which shows significant advantages, such as high combustion calorific value, low oxygen consumption and high measured specific impulse etc. [9,10,11].The ignition and combustion reactivity A feasibility study for producing aluminum flake powder from aluminum foil scrap by dry ball milling under an inert argon with a few % of oxygen was carried out. It was found that the pieces ofManufacturing of Aluminum Flake Powder From Foil Scrap by Dry Ball
احصل على السعر
Modeling of the planetary ball-milling process: The case
Among high-energy ball mills, the planetary is a mechanically simple and versatile device for efficient grinding. It is usually made of two or more jars, rotating at an angular velocity ω around their axis (see Fig. 1), installed on a disk rotating at angular velocity Ω.Grinding occurs by impact among the milling media (balls and jars), driven by The mill vessel was made of polyurethane (0.5 l), and the milling balls were made of zirconia (1, 3 and 5 mm in diameter). The weight ratios of ball-to-powder and 3 kinds of milling balls are 5:1 and 1:1:1, respectively. The rotation speed of the mill vessel is 140 rmin −1. Reduction was carried out in hydrogen atmosphere for DBM powders atDry ball milling and wet ball milling for fabricating copper–yttria
احصل على السعر
Role of Ball Milling of Aluminum Powders in Promotion of Aluminum
A planetary ball mill (Torrey Hills- ND2L) with stainless steel cups (285 mL capacity) and balls (28 of 16 mm and 6 of 18 mm diameter) milled the powders in an argon (Ar) atmosphere. Ball to powder ratio was 30:1, and the mill speed was maintained at 200 RPM for durations of 0.25, 0.5, 1, 2, 4, 7, 11, and 19 hours. Particles Size MeasurementsQuestion. 2 answers. Sep 15, 2023. if a 5gm of copper selenide in grinded to nanoparticles by a planetary ball mill by 550rpm, 250 ml cylinder, 50 balls (10mm diameter), with ball to powder ratio245 questions with answers in BALL MILLING Science topic
احصل على السعر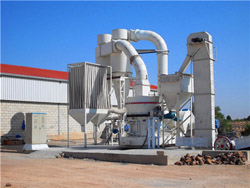
Wet Ball Milling Vs Dry Ball Milling Orbis
A ball mill is a grinder which is used to grind, blend and mix materials like chemicals, ores, pyrotechnics, paints, mineral dressing process, paint and ceramic raw materials. Its working principle is impact and attrition. Ball Ball mill is a kind of widely used engineering machinery with low working efficiency [1,2]. Effect of ball size on steady state of aluminum powder and efficiency of impacts during milling. Powder Technol. Energy absorption and specific breakage rate of particles under different operating conditions in dry ball milling. Powder TechnologyA novel approach of evaluating crushing energy in ball mills
احصل على السعر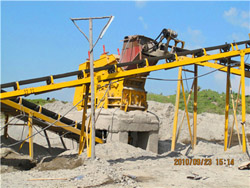
An innovative approach for determining the grinding
1. Introduction. Grinding operation is used extensively in the industry of beneficiation, metallurgy, chemical engineering, and electric power. Assisted by the impact and abrasion between media (steel ball, steel rod, gravel, ceramic ball) and ore, the grinding operation reduces the particle size in the mill [[1], [2], [3]].To produce the qualified size For the milling process, 40.12 g of the as-received Nb powder were loaded into two separate hardened steel containers of 125 ml volume with steel balls of 0.4 mm diameter, in a ball-to-powderWet ball milling of niobium by using ethanol, determination
احصل على السعر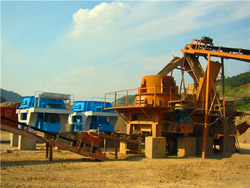
Effect of Different Milling Media for Surface Coating on
Figure1. The mechanical dry coating process was performed using a traditional ball mill (TBM) and a stirred ball mill (TY) with a stainless-steel pot and a Teflon (PTFE) coated pot, respectively. TY is vertical type and high-speed ball mills, are the mills in which large quantities of powder. TBM typeA high-energy mill was designed and built with the purpose of processing magnesium (Mg) powders. The main characteristics of the mill are grinding capacity of 1 kg and demolition elements of 10 kg; it has a distributed form to the interior ten blades of similar geometry, six of which are of the same size and four of them were increased in length in Design, Construction, and Operation of a High-Energy Mill
احصل على السعر
(PDF) Production of Aluminum Flake Pigments by Ball Mill
The specific rate of breakage of aluminum particles in bench scale ball mill is described by the function Si = 0.072 xi1.4716 where the experimental data for specific rate of breakage of aluminumVarious devices have been used for processing B powder, including attritor mills, conventional planetary mills, tumbler mills/mixers, vibratory mills, shaker mills, and uni-ball mills [161][162(PDF) Process Engineering with Planetary Ball Mills
احصل على السعر
Mechanical-dry coating of wax onto copper powder by ball
The gas-atomized copper particles (Fukuda Metal Foil & Powder) with spherical shape were used as a core particle as shown in Fig. 1(a). The median diameter and the true density are 69.1 μm and 8930 kg m −3, respectively. The mechanical dry coating process was carried out using a conventional horizontal ball mill of 400 ml The effects of the ball-to-powder diameter ratio (BPDR) and the shape of the powder particles on EDEM simulation results and time in the planetary ball mill was investigated. BPDR was varied from 1 to 40/3 by changing Modeling of the planetary ball-milling process: The case
احصل على السعر