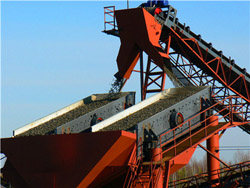
Review on vertical roller mill in cement industry & its
The cooled clinker is fed to deep metal pan conveyor and it is sent to the clinker storage pile (CSP). The clinker cools further naturally in CSP and extracted and The evaluation of grinding aid (GA) effect on clinker processing in laboratory grinding mills is relatively simple. Yet, the results Industrial versus Laboratory Clinker Processing
احصل على السعر
Quantifying the effect of clinker grinding aids under laboratory
The effect of clinker grinding aids (GAs) on mill performance and cement properties is currently quantified in real-scale grinding plants. In fact, laboratory-grinding this paper, the method was used to study the collisions between grinding media and grinding media and walls in ball mills, which is the most used unit operation in Experimental study of clinker grinding in a ball mill and
احصل على السعر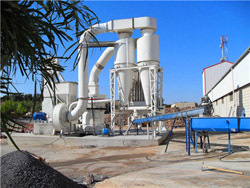
Design of clinker grinding system; mill and
Figure 1 presents the design of the clinker grinding system (closed circuit), which consists of a two-chamber ball mill and the separator (Plasari and T heraska, 19 81). Cement clinker...The proposed model correlates the specific grinding energy, the clinker work index and the specific surface (Blaine) of a cement produced through fine-grinding (PDF) CONVENTIONAL CLINKER GRINDING -A NEW
احصل على السعر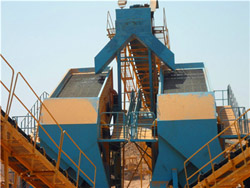
IOP Conference Series: Materials Science and
grinding . are . closed c. ircuit. ball mills. These type of . ball mills. in the coming decades will remain the basic units for grinding cement clinker and additives [3]. Discrete Element Methods (DEM) is a numerical tool consolidated to the simulations of collisions in particulate systems. In this paper, the method was used to Experimental study of clinker grinding in a ball mill and the
احصل على السعر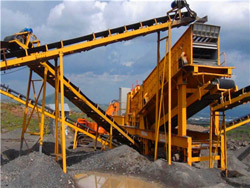
The influence of grinding technique on the liberation of clinker
Ball mill grinding was carried out by using a laboratory scale mill, since it was impossible to get clinker only samples from an industrial ball mill because of gypsum Abstract and Figures. Radiotracer Residence Time Distribution (RTD ) method was used to investigate the process of clinker grinding in Ghana Cement Plant (GHACEM) at Tema with the objective Radiotracer Investigation of Clinker Grinding Mills
احصل على السعر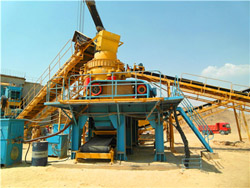
(PDF) CONVENTIONAL CLINKER GRINDING -A NEW
Conventional clinker-grinding ball mills with a dia phragm (Source: Jankovic et al., 1995). The coarse clinker is ground in the first compartment where larger balls (80, 60, 50 mm)For closed circuit mills grinding OPC as well as CEM II type products, the FLSmidth default CII media charge is 40% 25 mm, 40% 20 mm and 20% 15mm (~38 m^2/t). ball mills, the impact force of the grinding media is so great, that a high material surface unbalance prevails in the mill when grinding all types of clinker, thus requiring aEverything you need to know about clinker/cement Grinding
احصل على السعر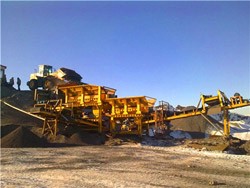
An industrial comparative study of cement clinker grinding
The clinker grinding stage accounts for approximately 40% of the electric energy consumed in cement production. Because of such a high level of energy demand and the inherent energy inefficiency of conventional ball mill grinding, the cement industry has continually searched for new grinding mill designs and/or grinding system For a ball mill grinding OPC to a fineness of 3200 to 3600 cm2/g (Blaine) the cost of wear parts (ball, liners and mill internals) is typically 0.15-0.20 EUR per ton of cement. For an OK mill grinding a similar product, the cost of wear parts depends on the maintenance procedures, i.e. whether hardfacing is applied.Cement grinding Vertical roller mills VS ball mills
احصل على السعر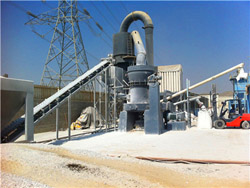
Breakthrough in Clinker Grinding Massachusetts
grinding seeks to reduce materials from roughly one meter cubes of blasted stone to a size where at least 80 percent of the raw material is less than 75 microns. Finish grinding of clinker and other cement ingredients reduces 25 mm clinker balls to particle sizes optimally ranging from 3 to 30 microns. TheThe effects of balls and cylinders on the clinker's specific rate of breakage were investigated. The results showed that the specific rate of breakage provided by cylinders is higher than that of balls. − 2.00 + 1.70 mm is an optimum feed size for 20 mm diameter balls and 20 × 20 mm diameter cylinders.At that feed size, the value of Si is The effects of grinding media shapes on the grinding kinetics
احصل على السعر
Loesche Mills for Cement and Granulated Blast Furnace
1985 Mills for grinding cement and granulated blast furnace slag were installed in Asia under licence from Loesche. 1994 The 2+2 technology, which was specially developed for grinding clinker and granulated blast furnace slag, was used for the first time in an LM 46.2+2 for cement grinding in the Pu Shin mill works of Lucky Cement, Taiwan.As a result, a change in the behaviour of clinker movement would occur inside the cement mill, that is, the fineness clinker penetrates the grinding balls, and thus reducing the grinding(PDF) IMPROVING PRODUCTIVITY BASED ON THE
احصل على السعر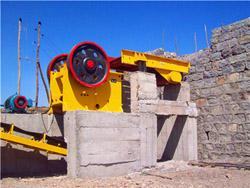
What is Cement Clinker?
The important role of vertical mills in cement clinker grinding station Feb 13, 2020 The difference between level-3 and level-2 flaw detection of steel castings Nov 26, 2019Nowadays, ball mills are used widely in cement plants to grind clinker and gypsum to produce cement. In this work, the energy and exergy analyses of a cement ball mill (CBM) were performed andEnergy and exergy analyses for a cement ball mill of a new
احصل على السعر
Radiotracer Investigation of Clinker Grinding Mills for
RTD, MRT and grinding efficiency of the clinker mill using radioactive tracer. The RTD is used for reactor troubleshooting like paral lel flows, de ad space, bypass or hold-up.The effect of clinker grinding aids (GAs) on mill performance and cement properties is currently quantified in real-scale grinding plants. In fact, laboratory-grinding mills operated for given time interval do not consider the effect of circulating load, thereby leading to increased specific energy consumption (Ec) with excessively wide cement Quantifying the effect of clinker grinding aids under laboratory
احصل على السعر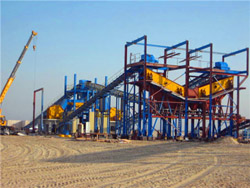
Investigation of flow dynamics of porous clinkers in a ball mill
The NCCL has three clinker grinding ball mills, all operating in closed circuit configuration. The schematic diagram of the mill investigated and experimental setup is shown in Fig. 1. The mill consists of a cylindrical vessel containing grinding media usually in the form of metallic balls, an elevator and a separator.Comparison between grinding of cement clinker with and without grinding aid (after Fuerstenau, 1990) Figure 1 shows the typical comparison between grinding of cement clinker with and without a grinding aid in a laboratory mill. As discussed in the literature [1,2,4], there was significant effect of using grinding aid in cement grinding.Journal of Physics: Conference Series PAPER OPEN
احصل على السعر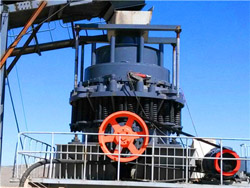
Cement grinding optimisation ScienceDirect
The cement clinker grinding circuit reduces the feed from 80% passing size between 10 and 20 mm to 100% passing 90 μm.The size reduction takes place in a two- compartment tube mill; the first compartment of the mill The evaluation of grinding aid (GA) effect on clinker processing in laboratory grinding mills is relatively simple. Yet, the results obtained cannot be directly transposed to industrial mills, given the fundamentally different operational modes and grinding parameters. This paper seeks to evaluate the scale effect by comparing the Industrial versus Laboratory Clinker Processing Using Grinding
احصل على السعر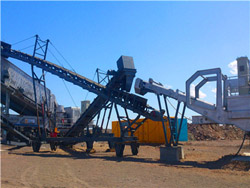
(PDF) A study on the action mechanisms of grinding aids
In cement industry, clinker grinding in steal tumbling mills is energy-consuming, and it has a very low energy efficiency. The use of a small quantity of products called grinding aids can improveThe grinding elements and mill settings are modified to grind harder materials such as clinker and granulated blast-furnace slag. Power use is between 26 and 29 kWh/t when grinding to a Blaine area 3,300 cm 2 /g using a VRM [ 28 ].A Review on Pyroprocessing Techniques for Selected Wastes
احصل على السعر