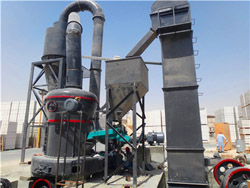
Design, fabrication and performance analysis of mini ball miller
The mixing of the constituent material in the development of composite can be done by using a ball miller. Grinding the powders in a ball miller is a process to PDF In the pursuit of achieving zero emissions, exploring the concept of recycling metal waste from industries and workshops (i.e., waste-free) is Find, read and cite all the research you(PDF) Producing Metal Powder from Machining
احصل على السعر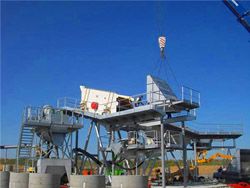
Ball Milling an overview ScienceDirect Topics
Ball milling is a mechanical technique that is broadly used to grind powders into fine particles [134–141]. The reactants are generally broken apart using solvent molecules in the A ball mill is a type of grinder widely utilized in the process of mechanochemical catalytic degradation. It consists of one or more (PDF) Grinding in Ball Mills: Modeling and Process
احصل على السعر
Particle morphology control of metal powder with
Abstract. The morphology evolution of copper powder was studied under various ball-milling experimental conditions, such as low and high rotation speeds and a Nevertheless, parameter factors, such as the type of ball milling, ball-to-powder ratio (BPR), rotation speed, grinding period, size and shape of the milling media, Producing Metal Powder from Machining Chips Using Ball
احصل على السعر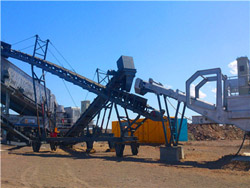
Powder Milling an overview ScienceDirect Topics
Powder milling process, using ball or rod mills, aim to produce a high-quality end-product that can be composites and nanocomposites, and nanocrystalline powder particles of The balls to powder ratio (BPR) and powder type were investigated in relation to the particle size. The study showed that the combination of the BPR and The design and optimization process of ball mill to reduce
احصل على السعر
Choosing the right strategy: cryogrinding vs. ball milling comparing
The grinding was performed in a dry state using a cryogenic grinder 6970EFM Freezer/Mill® (6970 EFM, SPEX SamplePrep, Metuchen, NJ, USA) which The grinding speed describes the rotation speed of the grinding container, which affects the kinetic energy of the grinding balls and the effect energy of the powder . Hussain et al. [ 129 ] extensively investigated the impact of different ball milling speeds while keeping the milling time constant at 30 h on the particle size of Ni70Mn30 samples.Producing Metal Powder from Machining Chips Using Ball
احصل على السعر
Design, fabrication and performance analysis of mini ball miller
The ball milling design significantly depends on the size of mill jar, required particle size distribution of powder and grinding media (balls) [13], [14], [15]. The main purpose of milling process is to obtain required particle size of the powder without any contamination, increasing the output of the milling circuit and overall reduction inThese forces are generated due to particle movement in the mill jar, the motion of balls and contact zones. The ball milling design significantly depends on the size of mill jar, required particle size distribution of powder and grinding media (balls) [13], [14], [15]. The main purpose of milling process is to obtain required particle size of the powder Design, fabrication and performance analysis of mini ball miller
احصل على السعر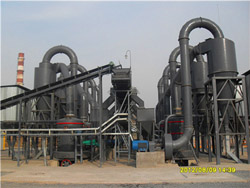
Facile synthesis of hierarchically structured MIL-53(Al) with
MIL-53(Al) characterization. The XRD pattern of the synthesized MIL-53(Al) is presented in Fig. 1.These patterns are very similar to 18.The XRD pattern of the UAS and CS MIL-53(Al) in this studyBall milling is a mechanical technique widely used to grind powders into fine particles and blend materials. 18 Being an environmentally-friendly, cost-effective technique, it has found wide application in industry all over the world. Since this mini-review mainly focuses on the conditions applied for the preparation and functionalisation ofBall milling: a green technology for the preparation and
احصل على السعر
(PDF) Grinding in Ball Mills: Modeling and Process Control
A ball mill is a type of grinder widely utilized in the process of mechanochemical catalytic degradation. It consists of one or more rotating cylinders partially filled with grinding balls (madeBall-to-powder weight ratio. Ball-to-powder weight ratio (BPR) ranges between 10:1 and 20:1. Higher capacity mills usually have higher BPR. With higher BPR less milling time is needed due to increased weight proportion of balls. This leads to higher energy transfer to powders as the number of collisions increases. [1, p.76–80] [4] MillingBall milling as a synthesis method Aalto University Wiki
احصل على السعر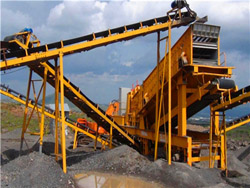
Grinding process within vertical roller mills: experiment and
This paper describes the simulation of the grinding process in vertical roller mills. It is based on actual experimental data obtained on a production line at the plant and from lab experiments. Sampling and experiments were also carried out in a power plant that has four ball-mill circuits used for coal grinding so that different equipmentBall milling is a simple, fast, cost-effective green technology with enormous potential. One of the most interesting applications of this technology in the field of cellulose is the preparation and the chemical modification of cellulose nanocrystals and nanofibers. Although a number of studies have been repo Recent Review Articles Nanoscale Advances Most Popular Ball milling: a green technology for the preparation and
احصل على السعر
Dry ball milling and wet ball milling for fabricating copper–yttria
The mill vessel was made of polyurethane (0.5 l), and the milling balls were made of zirconia (1, 3 and 5 mm in diameter). The weight ratios of ball-to-powder and 3 kinds of milling balls are 5:1 and 1:1:1, respectively. The rotation speed of the mill vessel is 140 rmin −1. Reduction was carried out in hydrogen atmosphere for DBM powders atThe powder-to-ball mass ratio was 1:50 with a powder mass of 100 g. Figure 10 shows micrographs of (a) as received powder observed by SEM and (b) 100 h ball-milled Fe 2 O 3 by TEM. Their results revealed that the prolonged milling remarkably reduced particle size from 1 mm in as received powder to about 15 nm in 100 h ball procedures grinding powder with a ball miller
احصل على السعر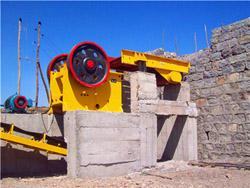
procedures grinding powder with a ball miller
quartzite high eficiency ball miller grinding machine Aug 11, 2017 quartzite high eficiency ball miller grinding machine. Mtw Raymond Grinding Mill For Making Powder 130tph,Mtw138 And Mtw175 Mill, Find .Filling ratio of grinding material or ball to powder ratio. Both compounds can be prepared using the slow evaporation method or mechanochemical synthetic procedures. Single-crystal structure(PDF) Process Engineering with Planetary Ball Mills
احصل على السعر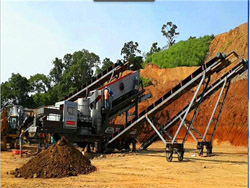
Differences in dry and wet grinding with a high solid
Grinding was performed using a XMQ-Φ240 × 90 laboratory-scale conical ball mill (Wuhan Exploring Machinery Factory, Wuhan, China). The diameter and length of the intermediate cylinder part of mill were 240 and 90 mm, respectively (Fig. 2).The operational speed was kept at 96 rpm (68% critical speed) according to the literature Ball milling is a mechanical technique that is broadly used to grind powders into fine particles [134–141]. The reactants are generally broken apart using solvent molecules in the traditional method; but in ball milling, reactants are broken by using mechanical forces. The term mechanochemistry has been introduced very recently [142].Ball Milling an overview ScienceDirect Topics
احصل على السعر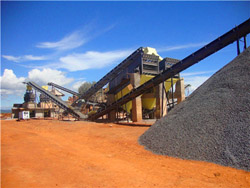
Grinding in Ball Mills: Modeling and Process Control
The Effect of Ball Size on the Energy Efficiency of Hybrid High-Pressure Roll Mill/Ball Mill Grinding. Powder Technology, Vol. 105,1999, 199-204. 10.1016/S0032-5910(99)00138-2 Google Scholar 23.Research Highlights The classifier velocity does not influence the flow near the impact elements. The flow in the grinding zone has no influence on the classification. The velocity profile at the front side of the impact elements is constant with time. Characteristic velocity profiles are observed at the front side of the impact elements. The Grinding in an air classifier mill ScienceDirect
احصل على السعر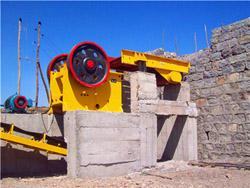
procedures grinding powder with a ball miller
According to the material, ranging from 0.4 mm to 3 mm for small media mills, up to 3mm to 20mm for planetary ball mill, and up to 20mm to 50mm for ball mills: Grinding Ball Types: High precision ball, Semi-precision ball, sintered rough ball: Brand: Miller ™ Precision Ball Classes: G5,G10,G25,G50,G100: Applications(Equipment) Learn The grinding ball diameters used for soil remediation ranged from 5 to 40, with 10 mm being the most selected grinding ball and 10 mm paired with 5 mm or 15 mm the most when results from powder and polarized extended X-ray absorption fine structure spectroscopy. Geochem. Cosmochim. Acta, 66 (15) (2002), pp. 2639-2663. View PDF Recent advances in the treatment of contaminated soils by ball
احصل على السعر