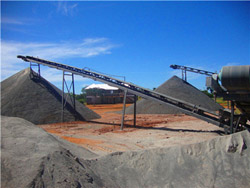
Avoided energy cost of producing minerals: The case of iron ore
Thus, the total specific energy for concentrating iron ore at the average ore grade (∼ 50% iron) from Thanatia (3.63% iron) was considered as the sum of the energy This chapter reviews current iron ore comminution and classification technologies and presents some examples of flowsheets from existing operations. New Comminution and classification technologies of iron ore
احصل على السعر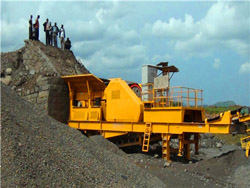
Mineral Commodity Summaries 2022 Iron Ore USGS
uses. Seven open pit iron ore mines (each with associated concentration and pelletizing plants) and four iron metallic plants—one direct-reduced iron (DRI) plant Cite Advertisement Advertisement Abstract The iron ore production has significantly expanded in recent years, owing to increasing steel demands in developing countries. However, the content of iron in Iron Ore Pelletizing Process: An Overview
احصل على السعر
IRON ORE1 USGS Publications Warehouse
Tariff: Item Iron ores and concentrates: Concentrates Coarse ores Other ores Pellets Briquettes Sinter Roasted iron pyrites Depletion Allowance: 15% (domestic), Seven open-pit iron ore mines (each with associated concentration and pelletizing plants), and three iron metallic plants—one direct- reduced iron (DRI) plant in 88 IRON ORE USGS Publications Warehouse
احصل على السعر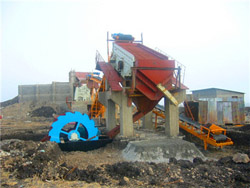
Plants Free Full-Text A Review on Remediation
A greenhouse trial to investigate the ameliorative properties of biosolids and plants on physicochemical conditions of iron ore tailings: Implications for an iron ore mine site remediation. J. Environ.In this paper, a novel iron ore agglomeration process is presented that utilizes concentrated solar energy instead of carbon intensive coke and natural gas used Evaluation of concentrated solar thermal energy for iron ore
احصل على السعر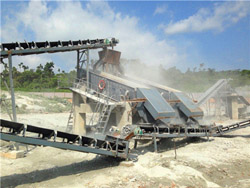
Iron Concentrate Particles MDPI
Iron ore concentrate is an output product from processed iron ores that have been milled (crush, grind, magnetic separation, flotation) to separate deleterious elements and produce a high-quality product. Sintering and pelletizing are economic and widely used agglomeration processes to prepare iron ore fines/iron concentrate for Washable ore beneficiation plants depended on local surface water sources for two main purposes. First, the surface waters themselves were essential for iron ore concentration, and second, surface waters provided mining companies with a sink to deposit the continual flow of tailings produced during ore concentration.A spatial evaluation of historic iron mining impacts on
احصل على السعر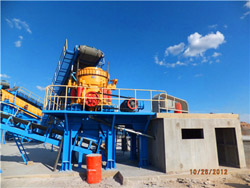
Size recovery curves of minerals in industrial spirals for processing
The ore is mined in an open pit and contains 29 to 31% Fe carried mainly by hematite with some magnetite. Quartz is the main gangue mineral. The concentration of other gangue minerals is less than 5%. The ore is crushed and autogenously ground to −0.850 mm. The ground ore feeds two identical parallel lines of rougher, cleaner and re Introduction of a-priori data on iron ore concentration as constraints for model parameters is a promising trend of further research, since it enables increased accuracy of identification despite limited availability of experimental data. Key words: iron ore, Rosin–Rammler, fuzzy model, separation characteristics 1. INTRODUCTIONMODELLING OF IRON ORE PROCESSING IN
احصل على السعر
Spirals in Australia mineral processing Multotec
Minerals mined in Australia include iron ore, coal, gold, copper, nickel and zinc. Spiral concentrators are used in mineral processing for separating minerals. Multotec Australia has a range of gravity concentration equipment for effective mineral concentration. The range comprises end-to-end spiral solutions, from process audits and test workAbstract The present article describes the extensive characterization and stabilization of concentrated iron ore suspension having size $$\\le 75~\\mu$$ m by various bench-scale tests. The rheological characteristics of iron ore in the concentration range of 60–80% (by wt.) have been investigated with and without the addition of Sapindus Influence of Natural Additive on Slurryability and Flowability of Iron Ore
احصل على السعر
Upgradation of Iron Ore Fines and Slime by Selective
Washing of iron ore fines and slime (10% and 25% w/v, slurry concentrations) with two types of surface-active agents (sodium humate (synthesized) and AD 200 (commercial)) at varying concentrations at pH 8 was conducted for ascertaining the efficacy of dispersants in beneficiating the low-grade iron ores. The beneficiation process The haematite ore in South Africa is processed in a dry process to a HQ lump ore with 64 % iron content and a sintered fine ore with 63.5 % iron content. For fine ore beneficiation, wet processes are used. Capacity at the Minas Rio is to be increased from 26.5 Mta capacity to 28 Mta in the forthcoming years.Dry beneficiation of iron ore Mineral Processing
احصل على السعر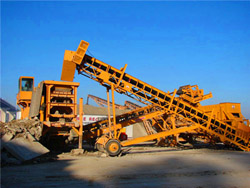
Energy and Environmental Profile of the U.S. Mining
4.1.2 Iron Ore Beneficiation Iron ore occurs naturally in a variety of forms, from sand-like iron fines to solid rock masses. Crude ore, or ore mined in the natural state, seldom occurs in a pure state and requires some form of beneficiation. Crude ore is commonly mixed with other minerals (gangue), which reduce the iron content. Vale will provide iron ore fines to three concentration plants in Saudi Arabia, UAE and Oman. This will be agglomerated into green briquettes of a grade high enough to be used in DRI furnaces. Vale stated that its “green briquette production is expected to feed the HBI and other steel products plants that will be constructed in the MENA, a potential new hub for green steel and green iron
احصل على السعر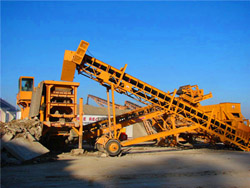
Size recovery curves of minerals in industrial spirals for
The mineral size recovery curves of roughing, cleaning and re-cleaning spirals from two Canadian iron ore processing plants are estimated using the results of several sampling campaigns. A similar behavior of the spirals is observed in both plants in spite of the fact that the plants use different types of spirals.of steel. Fifteen iron ore mines and fifteen ore concentration plants together withdrew annually about 89,000 million gallons to produce 15 million tons of iron ore concentrate, or 5,900 gallons per ton of concentrate. About 97 percent of the water used in the steel plants came from surface sources, 2.2 percent wasWater Requirements of the Iron and Steel Industry
احصل على السعر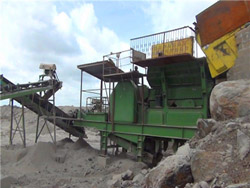
Water requirements of the iron and steel industry
Twenty-nine steel plants surveyed during 1957 and 1958 withdrew from various sources about 1,400 billion gallons of water annually and produced 40.8 million tons of ingot steel. This is equivalent to about 34,000 gallons of water per ton of steel. Fifteen iron ore mines and fifteen ore concentration plants together withdrew annually about 89,000 million In this study, a novel technology for the comprehensive utilization of low-grade iron ore is presented. For the iron ore with a Fe content of 24.91%, a pilot-scale study of pre-concentration, suspension magnetization roasting, grinding, and low-intensity magnetic separation was conducted, and an iron concentrate with a grade of 62.21% and Novel Technology for Comprehensive Utilization of Low-Grade Iron Ore
احصل على السعر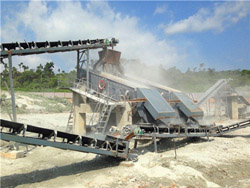
Mineral Commodity Summaries 2022 Iron Ore USGS
a 23% increase from $3.5 billion in 2020. The remaining 2% of domestic iron ore was produced for nonsteel end uses. Seven open pit iron ore mines (each with associated concentration and pelletizing plants) and four iron metallic plants—one direct-reduced iron (DRI) plant in Louisiana and three hot-briquetted iron (HBI) plants in The concentration of low grade iron ore resources was evaluated by washing and reduction. The advanced concentration methods for low grade limonite and hematite iron ores of South Eastern Anatolian resources required such specific methods. The followed column flotation and magnetic separation, microwave radiated reduction of Concentration and Microwave Radiated Reduction of
احصل على السعر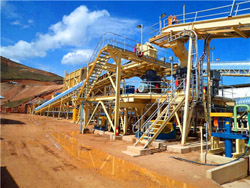
New perspectives in iron ore flotation: Use of collector
In phosphate ore concentration processes, amidoamines are more tolerant toward sulphate ions. They are also inexpensive and have fewer complications due to possible overdosage (Friedli, 1990). There are very few studies reporting the use of amidoamine molecules in iron ore flotation.Iron ore tailings (IOTs) are a form of solid waste produced during the beneficiation process of iron ore concentrate. In this paper, iron recovery from IOTs was studied at different points during a process involving pre-concentration followed by direct reduction and magnetic separation. Then, slag-tailing concrete composite admixtures Minerals Free Full-Text Recovering Iron from Iron Ore Tailings
احصل على السعر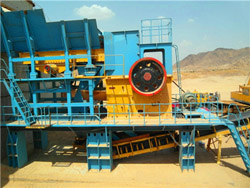
Increasing efficiency of iron ore magnetic separation by
Power consumption of iron ore concentration methods, developing and substantiating methods to processes and equipment substantially depends on properties enhance efficiencof ore simultaneously at Kryvyi Rih mining and concentration plants [2, 7]. It is worth noting that each mineral and technological type of iron ore demands such grinding
احصل على السعر