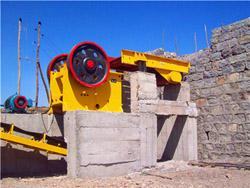
Energy and cement quality optimization of a cement grinding circuit
For the modelling of a ball mill, r/d function is back calculated by using the breakage function, the feed and the product size distributions of a given operating In this chapter an introduction of widely applied energy-efficient grinding technologies in cement grinding and description of the Energy-Efficient Technologies in Cement Grinding
احصل على السعر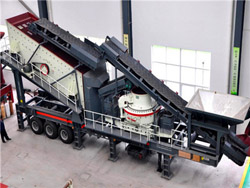
Reducing energy consumption of a raw mill in cement industry
The study indicates that for a dry type cement production process, the carbon dioxide emission intensity for kiln feed preparation process is about 5.4 kg CO 2 This study aimed at optimizing both the energy efficiency and the quality of the end product by modifying the existing flowsheet of the cement grinding circuit. As a Energy and cement quality optimization of a cement grinding circuit
احصل على السعر
Modeling of energy consumption factors for an
Cement production is one of the most energy‑intensive manufacturing industries, and the milling circuit of cement plants consumes around 4% of a year’s Utlu et al. ( 2006) also assessed the energy and exergy efficiency of a cement raw mill in the sector. Atmaca and Atmaca ( 2016) summarised the cement production process in terms Evaluation of optimization techniques for predicting exergy efficiency
احصل على السعر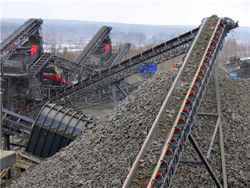
Technological Energy Efficiency Improvements in
To pursue greater energy efficiency in the cement manufacturing plants, for each operation forming the production process, a wide variety of technological solutions has been developed. For instance, In this study, the first and second law analysis of a raw mill is performed and certain measures are implemented in an existing raw mill in a cement factory in order to Reducing energy consumption of a raw mill in cement industry
احصل على السعر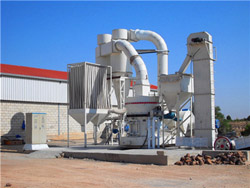
Energy efficiency of cement finish grinding in a dry batch ball mill
Energy utilization versus specific energy for batch grinding of (2–1.4 mm) cement with 20 mm ball diameter. Other experiments using crude cement clinker (Table The simulator was used for the thermodynamic performance of a raw mill (RM) and raw materials preparation unit in a cement plant in Nigeria using actual operating data. The raw mill has a capacity(PDF) Thermodynamic Analysis of Raw Mill in Cement
احصل على السعر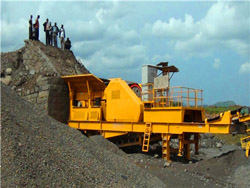
Minerals Free Full-Text Analysis and
This work concentrates on the energy consumption and grinding energy efficiency of a laboratory vertical roller mill (VRM) under various operating parameters. For design of experiments (DOE), the The design of large gear tooth systems for drives in the cement industry. A variety of methods of calculation can be used for designing large drives for tube mills, rotary kilns or dryers. With(PDF) Design of cement plant waste heat recovery
احصل على السعر
How to choose proper grinding media for your ball mill
Steel balls are one of the most widely used grinding media in cement ball mills, their diameters can range from 20mm to 120mm according to different grinding requirements. In a cement ball mill, generally, φ50–100mm steel balls are used in the coarse grinding chamber, φ20–50mm steel balls are used in the fine grinding chamber. 2.Utlu et al., [3] study on the raw mill sub-system reported that the energy efficiency of the cement was 84.3% but without consideration of the precalcining rotary kiln. Fellaou and Bounahmidi [4] examined the energy efficiency opportunities of a typical Moroccan cement plant.Evaluation of energy efficiency opportunities of a typical
احصل على السعر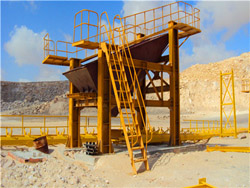
(PDF) Water and power consumption reduction by gas
Gas conditioning tower (GCT) is a vital equipment in cement industries. The main principle in this equipment is evaporative cooling, i.e. reducing the temperature of the hot flue gas byThe cement industry is the main supplier of raw materials for the production of concrete and reinforced concrete. For grinding cement, two types of mills are used ball and roller.(PDF) Performance Evaluation of Vertical Roller Mill in Cement
احصل على السعر
Analysis of material flow and consumption in cement
1. Introduction. Over the last century, Portland cement-based concrete has become the highest manufactured product on Earth in terms of volume. Concrete is used worldwide as a building material and is the most consumed substance on Earth after water (Sakai, 2009).The volume of concrete produced globally is approximately 5.30 billion m 3 A ball mill is a type of grinder widely utilized in the process of mechanochemical catalytic degradation. It consists of one or more rotating cylinders partially filled with grinding balls (made(PDF) Grinding in Ball Mills: Modeling and Process Control
احصل على السعر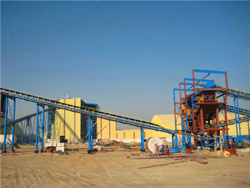
Energy and cement quality optimization of a cement grinding
The calculations implied that the production rate increased by 4.45% that corresponded to energy saving of 4.26%. analyses of a cement ball mill (CBM) were performed and some measurements wereRapid urbanization generates an ever increasing cement demand. In 2012, global cement productions was estimated at 3.77 billion tons, China accounting for about half of this figure and maintain its position of the world's largest consumer [5].At the national level, statistical studies have shown that the cement industry has experienced a Evaluation of energy efficiency opportunities of a
احصل على السعر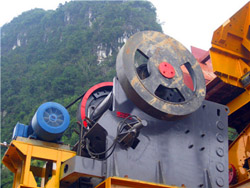
Different Possible Ways for Saving Energy in the Cement
In terms of absolute consumption, the cement industry occupies a front position in the ranks of energy consumed industries. The total energy costs (thermal and electrical) make up about 30 to 40 percent of the total production costs of cement. This is why efficient energy utilization has always been a matter of priority in the cement industry.The results show that approximately 2.48 t, 4.69 t, and 3.41 t of materials are required to produce a ton of the product in raw material preparation, clinker production, and cement grinding stages, and their waste rates are 63.31%, 74.12%, and 78.89%, respectively. The recycling rate of wastes during clinker production is remarkably higher Analysis of material flow and consumption in cement
احصل على السعر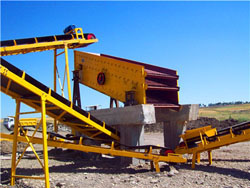
(PDF) Increase productivity of vertical roller mill
Specific Power consumption of Vertical Roller Cement Mill for pre-improvement phase. Data of last 6 [10] G. Amudha Ganesan,June-2016, "A Study on the Operat ing Efficiency of Major Cement .In this study, the analyses of energy and exergy were implemented for an industrial-scale vertical roller mill (VRM) of Kerman Momtazan Cement Company (KMCC) of Iran. The energy and exergy analyses demonstrated the first law efficiency of the VRM is 62.1%, while the second law efficiency of the VRM is 34.6%.A case study on energy and exergy analyses for an industrial
احصل على السعر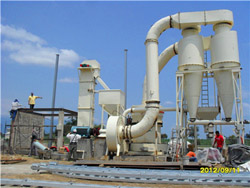
Guidebook for Using the Tool
2 •, the production of clinker (in tonnes per year) from each kiln by kiln type; •, the amount of raw materials, coal and clinker that is ground by mill type (in tonnes per year); •, the amount of production of cement by type and grade (in tonnes per year); •, the electricity generated onsite; and, •, the energy used by fuel type; and, the amount (in Contribute to crush2022/mill development by creating an account on .mill/sbm calculation for cement mill pdf.md at main crush2022/mill
احصل على السعر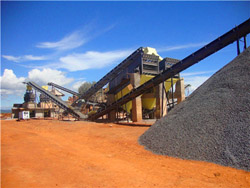
Sources of False Air INFINITY FOR CEMENT EQUIPMENT
False air is mostly present in the following areas of a cement plant: * Raw mill grinding area * Kiln area [10] Worrell E., Martin N., and Price L.,” Potentials for energy efficiency improvements in the US cement industry”, Energy, 2000,Vol.25, No.12, 1189-1214.Table 1 shows the design parameters used for the Aspen Plus process modeling, while the plant's operating data was used to simulate the energy efficiency of the cooler clinker grate. Based on the thirty (30) days steady state plant operating data simulated in Aspen Plus, a steady state energy analysis of the streams was performed Evaluating the thermodynamic efficiency of the cement grate
احصل على السعر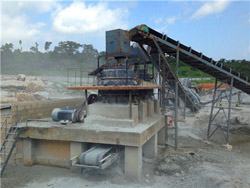
Energetic assessment of a precalcining rotary kiln in a cement
This study assessed the energetic efficiency of a precalcining rotary kiln process in a cement industry. • Energetic efficiency was estimated as 61.30 % using Aspen Plus process simulator and artificial neural network (ANN) model predict with correlation coefficient (R 2) of 0.991.. Optimal energy efficiency of 61.5 % was established for the
احصل على السعر