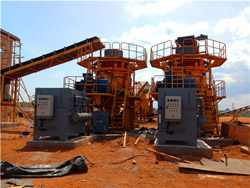
Full article: An overview of alternative raw materials used in cement
Cement production process with waste utilisation areas. Display full size. In stage one, the essential raw materials-limestone, laterite, bauxite, kaolinite, clay, iron ore, sandstone, Table 1. Raw materials are used to produce the main cement elements (Mohsen, 2015) • Quarry The process of obtaining raw (PDF) Cement Manufacturing ResearchGate
احصل على السعر
The cement mill Understanding Cement
Cement clinker is usually ground using a ball mill. This is essentially a large rotating drum containing grinding media normally steel balls. As the drum rotates, the motion of the balls crushes the clinker. The drum rotates The material efficiency values for a raw mill, pyro-processing tower, rotary kiln, clink cooler, and cement mill are determined to be 36.69%, 34.24%, 39.24%, Analysis of material flow and consumption in cement production process
احصل على السعر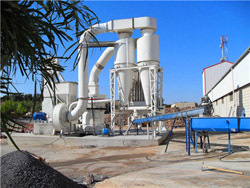
The important role of vertical roller mills in the cement industry
GRMK vertical cement mill has the advantages of compact structure and small volume. It mainly includes high efficiency separator, grinding rollers, grinding table, hydraulic Vertical roller mill has proved to be a popular choice for finished cement grinding over all other machineries due to advantages like low power consumption, Review on vertical roller mill in cement industry & its
احصل على السعر
Review on vertical roller mill in cement industry & its
Vertical roller mill has proved to be a popular choice for finished cement grinding over all other machineries due to advantages like low power consumption, The cement production process. Cement manufacturing is a process consisted of two major steps with generally similar cycle times: the Mill, which grinds The future in cement manufacturing is here: Transforming
احصل على السعر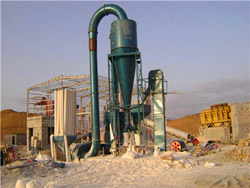
Energy and exergy analyses for a cement ball mill of a new
Nowadays, ball mills are used widely in cement plants to grind clinker and gypsum to produce cement. In this work, the energy and exergy analyses of a cement ball mill (CBM) were performed andAccording to our analyses, the cement plant of the future could reduce emissions by up to 75 percent by 2050 compared with 2017. Around 20 percent will come from operational advances, such as energy-efficiency measures and clinker substitution. An additional 10 percent will come from alternative fuels—however, the availability of Digitization and the future of the cement plant McKinsey
احصل على السعر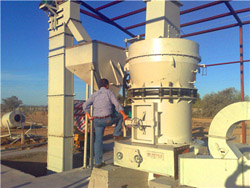
2 Major Roles of Limestone in Cement Manufacturing
The answer is the cement industry. Limestone plays two major roles in the cement manufacturing process, one is used as a raw material for cement clinker, and the other is used as a cement admixture. Limestone is one of the key raw materials of cement clinker. Around 80-90% of the raw material for the kiln feed is limestone.Compared with the cement ball mill, it has a great difference in structure, grinding principle, process layout, automatic control, and energy consumption, which play an important role in the modern cement industry. High Grinding Efficiency. The energy consumption of cement vertical mill grinding system is relatively low, which is 10%-30% lowerRaw Mill Raw Mill In Cement Plant AGICO Cement Raw Mill
احصل على السعر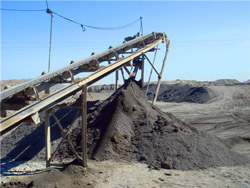
Control in Cement Production ScienceDirect
Cement grinding This process is a multivariable, nonlinear one with an inner feedback and large delays. It has distributed parameters where a lumped parameter approximation is load dependent. The particle size distribution and the grindabili ty of the clinker change stochastically cau sing continuous disturbances to the mill.The vertical roller mill is better to ball mill in respect of overall economy. The final manufacturing stage at a cement plant is the grinding of cement clinker from the kiln, mixed with 4-5%The important role of vertical mills in cement clinker
احصل على السعر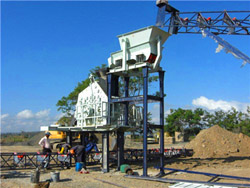
(PDF) Intelligent Modeling of Cement Plant Mill Unit Using
Intelligent Modeling of Cement Plant Mill Unit Using Artificial Neural Networks and Real Data. 10.1109/SIBCON50419.2021.9438907. Conference: 2021 International Siberian Conference on Control andCement has hydraulic properties like slaked lime and hardens when mixed with water. Compressive strength increases in time and reaches its practical top limit after 28 days. Mixing crushed stone(PDF) Mining Activities, Cement Production Process and
احصل على السعر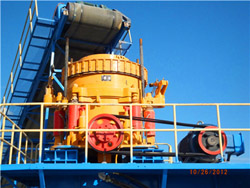
Q&A- AI in the Cement Industry Cement industry solutions
It will allow cement producers to hit key performance indicators around sustainability, process performance, asset performance, connected workers and operational excellence. Here are some examples. AI can play a vital role in reaching environmental sustainability targets, and not just around reducing emissions, but also energy optimization andTherefore, producing cement with less energy is becoming a key element of profitability: as the grinding process consumes about 60 per cent of the total plant electrical energy demand and about 20 per cent of cement production variable cost. So efficient grinding unit selection impacts profitability of cement manufacturing.Efficient grinding unit selection impacts profitability Indian Cement
احصل على السعر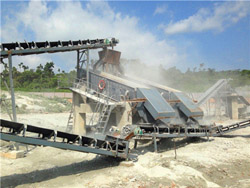
Cement Manufacturing Process Phases Flow
Cement Manufacturing Process Phase 1: Raw Material Extraction. Cement uses raw materials that cover calcium, silicon, iron and aluminum. Such raw materials are limestone, clay and sand. Limestone 1. Introduction. India is the second-largest cement producer in the world. Cement production is around 330 million tonnes per year & turnover is approximately 30,000 crores [1].In India, the cement industry is the second largest industry in the development and growth of the Indian economy [2].Pyro processing plays a significant role in cement A comprehensive review on Advanced Process Control of cement
احصل على السعر
Clinker grinding technology in cement manufacturing
Clinker grinding technology is the most energy-intensive process in cement manufacturing. Traditionally, it was treated as "low on technology" and "high on energy" as grinding circuits use more than 60 per cent of total energy consumed and account for most of the manufacturing cost. Since the increasing energy cost started burning the benefits ABB provides complete turn-key analysis systems. Continuous gas analyzer system is the perfect fitting solution for emission monitoring, process gas measurements and specific applications in the cement industry. Also a complete solution for rotary kiln and calciner. The specialty is the hot sampling with a reliable rugged probe system that isInstrumentation for cement plants Systems and solutions
احصل على السعر
Cements ground in the vertical roller mill fulfil the quality
C. Obry. Karl-Heinrich Zysk. Vertical roller mills are the mills traditionally used for processing granulated blastfurnace slag and for grinding composite cements. From the energy aspect they areThe raw mill machine functions as a main material grinder in the initial milling process such as limestone, silica stone, clay, and iron sand to become raw mix. To find out the frequency of damage(PDF) Analysis of Raw Mill Machines Maintenance in Cement Industry
احصل على السعر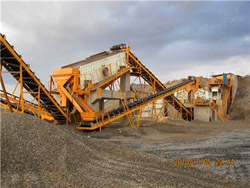
Improving cement production through Artificial Intelligence
This process consumes approximately 40 kWh per ton of cement, accounting for the most electrical power consumption in the production of cement. CEMEX is using “Model-Based Optimization”, which consists of using machine learning to generate models that predict the performance of the mill. The factors that must be considered In the cement manufacturing process, kiln process fans play a vital role. This article presents an extensive investigation into the prediction of Raw Mill Fan vibrations using machine learning models.Energy consumption assessment in a cement production plant
احصل على السعر
Towards a business case for CO2 mineralisation in the cement
For the process, jaw crushers and ball mills are considered due to their low costs and the wide usage in the cement industry to this point. The role of cement in the 2050 low carbon economy.
احصل على السعر