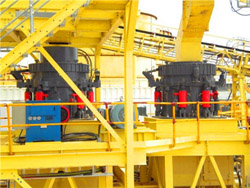
A comparative study on the effects of dry and wet grinding on mineral
Since wet grinding is the most common method for particle size reduction and mineral liberation, there is a lack of understanding about the effects of dry grinding Dry grinding and classification circuit: (a) Idea of the circuit: 1-feed stream, 2-mill working chamber, 3-working area with Comparison of Wet and Dry Grinding in
احصل على السعر
Towards waterless operations from mine to mill ScienceDirect
Stirred media mills can operate both wet and dry operations, with wet grinding clearly more energy efficient. A recent study by Altun et al. (2020) evaluated the Stirred media mills are widely used in the industry for fine grinding. Most of the applications work in wet mode, however dry grinding in stirred media mill comes COMPARISON OF WET AND DRY STIRRED MEDIA
احصل على السعر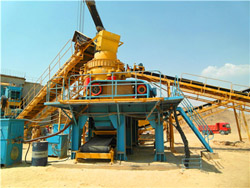
Stirred media mills in the mining industry: Material
, Stuart Blackburn, Richard Greenwood Add to Mendeley https://doi/10.1016/j.powtec.2020.04.057 Get rights and content Abstract Stirred In this chapter the mechanisms of wet-grinding mills are considered. The nature of the forces at work, together with a detailed consideration of their interplay and means of control, are Wet-Grinding Mills SpringerLink
احصل على السعر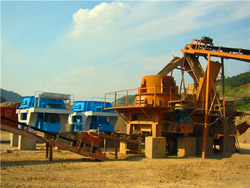
Wet and dry grinding of coal in a laboratory-scale ball mill:
Abstract. In this study, experimental data for wet- and dry-ground coal samples under wet and dry grinding are characterized by commonly used distribution Comparison of dry and wet grinding process in an electromagnetic mill is presented in this paper. The research was conducted in a batch copper ore grinding. Comparison of Wet and Dry Grinding in Electromagnetic Mill
احصل على السعر
Dry Grinding SpringerLink
Though most ores are reduced by wet grinding before being processed, some can better be ground and treated dry. Many minerals and synthetic substances require size reduction The aim of this study was to investigate the effect of grinding media (dry or wet) on the pulp chemistry and recovery of Cu and Zn in bulk concentrate. 1100 g of ore samples were milled, and mill(PDF) WET AND DRY GRINDING METHODS
احصل على السعر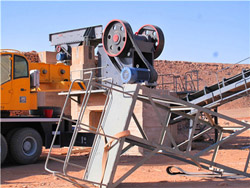
Kinetics of fine wet grinding in a laboratory ball mill
Grinding was carried out in the laboratory ball mill described in Table 1, at a low ball load of 20% of the mill volume filled with the ball bed and a low powder load corresponding to a formal interstitial filling of void spaces of the ball bed of U=0.5. These conditions were chosen since it is known that they give first order grinding kinetics for To accurately simulate the impact of falling balls on the liners in wet mills, models have been developed to determine the contact between the ball and the mill liner [5]. Moreover, forces exerted by the load on the liner in both a dry mill and a wet mill were measured, as was the conductivity between the probe and the liner [6].Modeling ball impact on the wet mill liners and its
احصل على السعر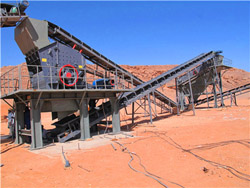
Comparison of Wet and Dry Grinding in Electromagnetic Mill
Comparison of dry and wet grinding process in an electromagnetic mill is presented in this paper. The research was conducted in a batch copper ore grinding. Batch mode allows for precise parametrization and constant repetitive conditions of the experiments. The following key aspects were tested: processing time, feed size, size of Dry grinding and classification circuit: (a) Idea of the circuit: 1-feed stream, 2-mill working chamber, 3-working area with ferromagnetic rods, 4-main transport air stream, 5-mills output streamComparison of Wet and Dry Grinding in Electromagnetic Mill
احصل على السعر
A comparative study on the effects of dry and wet grinding on mineral
In terms of the energy consumption (EC) for a certain particle size distribution, several investigations reveal that in dry grinding the EC is around 15–50% higher than in a wet environment [2], [10], [14], [15].Ogonowski et al. (2018) conducted an investigation to compare wet and dry grinding processes in an electromagnetic mill.Batch wet grinding of zeolite was studied with emphasis on a kinetic study in a laboratory size steel ball mill of 200 mm diameter. The breakage parameters were determined by using the single sized feed fractions of − 850 + 600 µm, − 600 + 425 µm and − 425 + 300 µm for the zeolite samples. The S i (specific rate of breakage) and B i,j Kinetics of fine wet grinding of zeolite in a steel ball mill in
احصل على السعر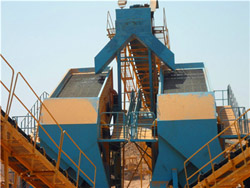
Evaluation of particle size reduction and agglomeration in dry
Differences in dry and wet grinding with a high solid concentration of coking coal using a laboratory conical ball mill: Breakage rate, morphological characterization, and induction time Advanced Powder Technology, Volume 30, Issue 11, 2019, pp. 2703-2711Process. 44-45 (1996) 383-393 3. Results Results obtained for the dry mill will be compared with those obtained in the wet mill described above. 3.1. Load behaviour in a dry mill The work described by Moys and Skorupa (1993) involved the measurement of the effect of mill speed, load volume and liner profile on liner forces.The measurement of forces exerted by the load on liners in rotary mills
احصل على السعر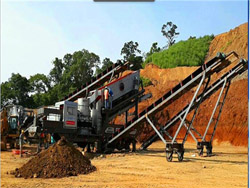
Comparison of Wet and Dry Grinding in Electromagnetic Mill
Comparison of dry and wet grinding process in an electromagnetic mill is presented in this paper. The research was conducted in a batch copper ore grinding. Batch mode allows for precise parametrization and constant repetitive conditions of the experiments. The following key aspects were tested: processing time, feed size, size of In this paper, we use DEM modelling to understand media motion within the operation of a full scale industrial Isamill. These mills are used dry for processes such as grinding of cement, an example of which is the Netzche Ankamill (Altun et al., 2013, Altun et al., 2014). The media behaviour is also indicative of the performance of the wetComputational prediction of performance for a full
احصل على السعر
(PDF) Effect of wet ball milling on copper ore flotation by
This study aims to investigate the ball milling effect on particles flotation using fractal dimension, in which the calculations in the particles morphology has been made using the step-length1. Introduction1.1. Fine grinding in the mining industry. It has been estimated that approximately 2% of the world's energy usage is applied to mineral comminution, and around a quarter of this is used specifically in metalliferous ore grinding [1] where it is typically the most energy intensive set of operations [2].The purpose of Stirred media mills in the mining industry: Material
احصل على السعر
Vertical roller mills: The new leader in grinding technology
The Loesche VRM has adaptable grinding modules which are already proven to be the way forward in other mining industries, allowing for variant mineral ores to be milled efficiently to the required particle size. The VRM, depending on the roller size, has a high reduction ratio; feed from 80 mm to 140 mm to a product of P80 at 75 µm in one wastewater mill UTN seriers. rotor double-roller vertical. Final grain size: 100 µm 100 µm. Output: 60,000 kg/h 480,000 kg/h. Motor power: 2,200, 4,000, 3,000 W. The Waste water Grinder from United Tech Machinery is a high torque, low rotating speed and double shaft grinder under water. It is designed to pulverizing all kinds of solidWet mill, Wet grinding system All industrial manufacturers
احصل على السعر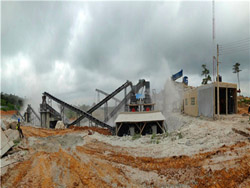
Effect of particulate environment on the grinding kinetics of
Accordingly, after crushing the three minerals in a jaw crusher and a roll crusher, a sufficiently large quantity of the crushed material of each mineral was ground in the test ball mill for five minutes in several batches. The mill was operated under the same conditions as those selected for carrying out the actual grinding tests.Abstract. In this chapter the mechanisms of wet-grinding mills are considered. The nature of the forces at work, together with a detailed consideration of their interplay and means of control, are discussed in Chapter 6. The general term “tumbling mill” includes the rod mill, pebble mill, and ball mill. It is of cylindrical or cylindroWet-Grinding Mills SpringerLink
احصل على السعر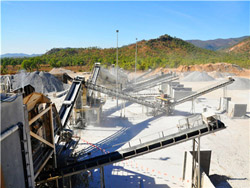
Geometry influence on optimized operation of a dry agitator bead mill
Dry agitated bead mill. The mill design is based on the wet-operated LMZ bead mill series by NETZSCH Feinmahltechnik GmbH. The dry development called SpeRho was led by NETZSCH Trockenmahltechnik GmbH. As shown in Fig. 1, it is a horizontally operated mill with a grinding vessel and a shaft equipped with agitators.Abstract. Wet comminution in stirred media mills is a frequently applied fully scalable top-down method towards the production of micron- and submicron particles. Despite the vast field of mechanochemistry which encompasses an increase in reactivity due to the effect of mechanical energy input, there is still no clear picture of the involvedMechanochemical aspects in wet stirred media milling
احصل على السعر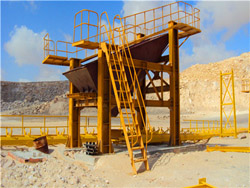
Ball Mills & Agitated Media Mills Hosokawa Alpine
Ball Mills and Agitated Media Mills Grinding wet and dry. The ATR product line is employed for the dry grinding of mineral powders to high fineness values of <10 µm down to 95% <2 µm. Typical applications are mineral fillers, glazing raw materials and non-mineral hard materials. In addition, the product can also be coated during the
احصل على السعر