
A comparative study on the effects of dry and wet grinding
Abstract Water scarcity dictates to limit the use of water in ore processing plants particularly in arid regions. Since wet grinding is the most common method for Dry milling typically uses particle-on-particle contact to reduce materials’ size, while wet milling involves dispersing the material in a liquid and using solid, grinding elements to reduce size. Products can be Wet Milling vs Dry Milling: The Differences,
احصل على السعر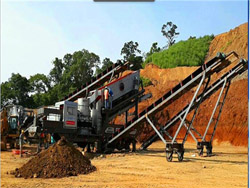
High-Performance Dry Grinding SpringerLink
High-Performance Dry Grinding, Table 1 Advantages and disadvantages of high-performance grinding according to VDI 3411 and Kopac and Krajnik Full size table PDF Grinding is a manufacturing process which significantly contributes in producing high precision and durable components required in numerous Find, read and cite all the research you...(PDF) A comprehensive review on the grinding
احصل على السعر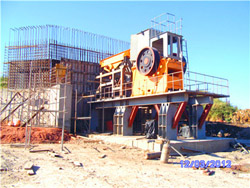
A comparative study on the effects of dry and wet grinding
Deniz et al. [34] and Bu et al. [35] studied the effect of wet and dry grinding of coal and observed that the wet grinding method is a more efficient methodology for the Due to the demand for environmental friendly machining process, the dry grinding has lately become a subject of special interests. Despite its ecological and Evaluation of thermal damages and residual stresses in dry grinding
احصل على السعر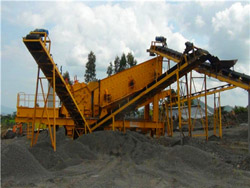
Comparison of Wet and Dry Grinding in
Only in case of the shortest processing time, equal to 5 s, are the dry grinding results better . This is most likely due to higher friction that needs to be overcome by the grinding media in the material-water The 3C-SiC nanopowder obtained by dry grinding of the formed free nanoporous layer (see Section 11.2) was directly dispersed in a Krebs buffer solution.The formed suspension Dry Grinding an overview ScienceDirect Topics
احصل على السعر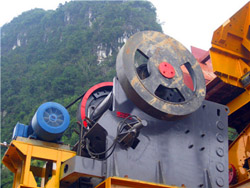
A comparative study of Dry milling vs Wet milling Senieer
Lower operating temperatures are achieved by the liquid slurry, which dissipates heat from the mill since it has a far greater heat capacity than the solid. The disadvantages of dry-micronization are avoided by wet-milling. Dry-micronization frequently adds disorder into the milled crystalline API, primarily in the form of amorphous material.Wet and Dry Grinding Operation; Buffing and Polishing Process: Definition, Advantages, Disadvantages, Application, Differences Explained in detail [Notes & PDF] Er. Amrit Kumar Amrit Kumar is a Grinding Machine: Definition, Parts, Working
احصل على السعر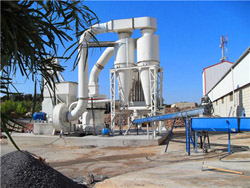
Everything you need to know about a grinding
A grinding machine which is popularly known as a grinder is a power tool or machine tool used for grinding. Just like other machine tools, it is a type of machining process that uses an abrasive wheel as the cutting tool. The Stirred Mills Ultrafine Grinding. In Mineral Processing Design and Operations (Second Edition), 2016. 10.2.4 Operation of Vertical Mills. Vertical stirred mills are usually charged with media occupying 80% of the mill volume which is in sharp contrast to tumbling mills that are seldom charged more than 40% of their volumes to allow space for the tumbling Stirred Mill an overview ScienceDirect Topics
احصل على السعر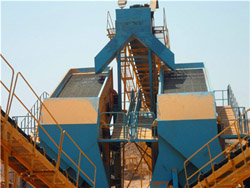
Dry Milling an overview ScienceDirect Topics
Dry milling and wet milling of cereal grains are used to produce ethanol and to partition the grains into an array of feed components (Figure 2).Wet milling is a more complex process and requires high-quality grains to produce high-value products suitable for human use. Some of the co-products, such as maize gluten meal, may be marketed in In summary, dry grinding produces fine particles and is best suited for hard, abrasive materials. Wet grinding produces smaller particles and is ideal for softer, more delicate materials. Both processes have their own unique advantages and disadvantages, and it is important to choose the right method for your application to achieve the desiredWhat Is the Difference Between Dry and Wet Grinding? ball
احصل على السعر
Ball Milling an overview ScienceDirect Topics
Ball milling is a mechanical technique that is broadly used to grind powders into fine particles [134–141]. The reactants are generally broken apart using solvent molecules in the traditional method; but in ball milling, reactants are broken by using mechanical forces. The term mechanochemistry has been introduced very recently [142].Cryogenic (C2) 7.06 2 Cause Energy requirement − 1.85 6 Effect. Dry ice (C3) 3.89 Cause Grinding time − 0.21 Effect. Chilling (C4) 3.47 Cause Grinding loss − 0.25 Effect. Grinding zone(PDF) Key issues and challenges in spice grinding
احصل على السعر
A comparative study on the effects of dry and wet grinding
Dry grinding consumes higher energy and produces wider particle size distributions compared with wet grinding. It significantly decreases the rate of media consumption and liner wear; thus, the contamination of pulp for flotation separation is lower after dry grinding. Using HPGR has several advantages such as energy savings (i.e. The main difference between wet and dry sanding is that wet sanding uses a lubricant, like water, along with the abrasive. As a result, it is more time-consuming but results in fewer scratches and a smoother finish. In contrast, dry sanding is faster and preferred for removing surface material quickly. This article compares the wet and dryWet Sanding vs Dry Sanding: What's the Advantage?
احصل على السعر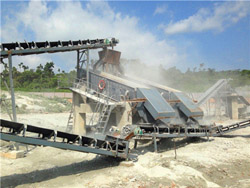
Ball Mill an overview ScienceDirect Topics
Mechanical Crushing and Grinding. Oleg D. Neikov, in Handbook of Non-Ferrous Metal Powders, 2009 Tumbling Ball Mills. Tumbling ball mills or ball mills are most widely used in both wet and dry systems, in batch and continuous operations, and on a small and large scale.. Grinding elements in ball mills travel at different velocities. Therefore, collision Wet process. Dry Process of Manufacture of Cement: Crushing of limestone and clay in crushers and stored in silos. Grinding of crushed materials and storing in hoppers. Mixing of materials by compressed air in the right 2 Process Of Manufacture Of Cement Wet
احصل على السعر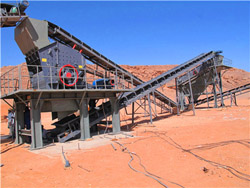
Vibration Mill: Components, Advantages and
Advantages of Vibration Mill. 1. Suitable for hard abrasive grinding stocks. 2. Unlike tumbling mills, the porcelain in the vibrating mills move only a few millimeters through a complex path, shearing and Feeding a total mixed ration (TMR) that contains all the feeds and nutrients the cow needs is an effective, efficient and profitable way to feed dairy cows. Managing TMR daily can make sure your cows receive enough nutrients for good health, milk production and reproduction. Proper nutrition leads to healthy and high-performing dairy cows.Feeding total mixed rations Extension at the University of
احصل على السعر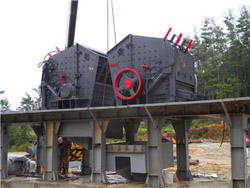
Synthesis of nanomaterials using various top-down and
Advantages. There are various advantages to laser ablation [75]. • The ability to generate ligand-free noble NPs in a range of solvents is one of the major benefits of LA synthesis in solution. • Low loss of energy. 4.2.3.3. Disadvantages. Laser ablation also possess afew disadvantages given below [74]. •Now that we have a basic understanding of the industrial milling process, let’s examine the difference between wet milling and dry milling. Dry milling typically uses particle-on-particle contact to reduce materials’ size, while wet milling involves dispersing the material in a liquid and using solid, grinding elements to reduce size.Wet Milling vs Dry Milling: The Differences, Advantages
احصل على السعر
Grinder Machine Working, Types, Applications, Pros & Cons
A grinding machine consists of the following parts: 1. Base The base of the grinding machine supports the other parts of the machine. It is made of cast iron and rests on a flat foundation. 2. Column The column is a vertical structure that supports the grinding wheel and the grinding head. It is made of cast iron and has a dovetail slide on Contribute to chengxinjia/sbm development by creating an account on .sbm/sbm disadvantage of excess grinding of cement.md at
احصل على السعر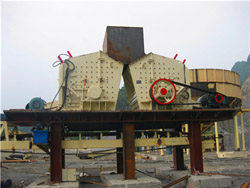
Dry Machining an overview ScienceDirect Topics
Dry machining or machining without using any CF is becoming increasingly more popular keeping in view of the environmental and health problems related to their use in conventional machining. Advantages of dry machining include (1) elimination of harmful effects of CFs on the environment and human health; (2) elimination of disposal, filtration, and cleaning Dry pressing, also known as pressing molding, is a commonly used method for ceramic molding. By putting ceramic powder into a metal mold and applying pressure, the pressure is about 160 tons, and the powder particles are fixed and formed by friction. Various shapes, generally suitable for forming ceramic plates, ceramic discs and other productsCeramic Dry Pressing Ceramic Machining
احصل على السعر