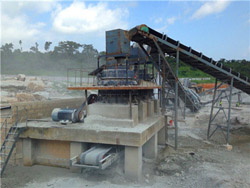
Energy-Model and Life Cycle-Model for Grinding
By stirred ball grinding of 20 min, the median particle size of the limestone products was 1.76 μm. The specific energy value was determined from the stirred ball mill power of 178 Nm/s by filling ratio of PDF The effect of ball size and interstitial filling on the performance of dry ball mill grinding was investigated for a limestone-type brecciated Find, read and cite all the research you(PDF) Optimization of Ball Mill Grinding of a Limestone
احصل على السعر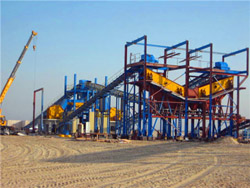
Optimization of Ball Mill Grinding of a Limestone-Type
The effect of ball size and interstitial filling on the performance of dry ball mill grinding was investigated for a limestone-type brecciated uranium ore. The optimum grinding was obtained with the combination of different balls (12.7–37.5 mm) and interstitial filling of 50% (20% ball filling ratio at fixed material filling ratio = 4%).This quantity is small compared to the power used by a semi-autogenous mill and a ball mill in a primary grinding circuit; a ball mill can have an installed power of up to 15 MW, while installed power for a SAG mill can go up to 25 MW.Energy Use of Fine Grinding in Mineral Processing SpringerLink
احصل على السعر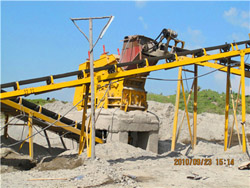
A study of the grinding of magnetite/limestone mixture in a
1. Introduction The grinding process, providing the desired size of particles and the desired degree of liberation, is the preparation for separation in the mineral processing industry.the performance of dry ball mill grinding was investigated for a limestone-type brecciated uranium ore. The optimum grinding was obtained with the combination of dierent balls (12.7–37.5 mm) and interstitial lling of 50% (20% ball lling ratio at xed material lling ratio= 4%). The net power consumption in a ball mill is proportional to theOptimization of Ball Mill Grinding of a Limestone-Type
احصل على السعر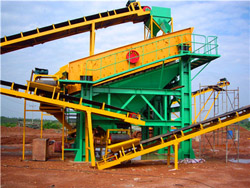
A Technical and Economic Comparison of Ball Mill Limestone
Request PDF A Technical and Economic Comparison of Ball Mill Limestone Comminution with a Vertical Roller Mill Wet flue gas desulfurization (WFGD), using limestone with forced oxidation (LSFOIntroduction The majority of pulverised coal boilers use flue gas treatment processes involving limestones that is prepared using horizontal tumbling mills such as ball mills for limestone grinding.A new model between the Bond and Hardgrove grindability
احصل على السعر
Design, Construction and Performance Analysis of a 5
The laboratory ball mill was designed for grinding limestone, meaning that the work index required for the specific power calculation was assumed to be the work index of limestone, which is 11.6 KWh/t, with a specific gravity of 2.6 g/cm. 3. or 2600 kg/m. 3. The feed size (F. 80) of the ball mill was assumed to be 2 mm (2000 microns).However, the faster processing speed of an TY-type mill comes at a cost of high power demand, as seen in Table 7. Mucsi & Racz (2017) Grinding in ball mills: modeling and process control. Cybern Inf Technol, 12 (2) (2012), pp. 51-68, 10.2478/cait-2012-0012. View in Scopus Google ScholarComparative comminution efficiencies of rotary, stirred and
احصل على السعر
Scale-up procedure for continuous grinding mill design
The design production rate for the circuit is to be 100 TPH at 250% circulating load. For the scale-up design the following steps were required: (1) Perform batch grinding experiments in a reference ball mill. In this example limestone was stage crushed to minus 6.35 mm and screened to ob- tain an 8 10 mesh feed material.China Limestone Mill manufacturers Select 2023 high quality Limestone Mill products in best price from certified Chinese Milling Machine, Grinding Machine suppliers, wholesalers and factory on Made-in-ChinaChina Limestone Mill, Limestone Mill Manufacturers,
احصل على السعر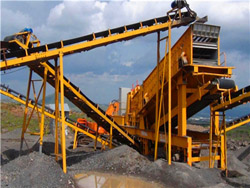
Ball Mills 911 Metallurgist
CERAMIC LINED BALL MILL. Ball Mills can be supplied with either ceramic or rubber linings for wet or dry grinding, for continuous or batch type operation, in sizes from 15″ x 21″ to 8′ x 12′. High density ceramic linings of uniform hardness male possible thinner linings and greater and more effective grinding volume.The laboratory ball mill was designed for grinding limestone, meaning that the work index required for the specific power calculation was assumed to be the work index of limestone, which is 11.6 KWh/t, with a specific gravity of 2.6 g/cm. 3. or 2600 kg/m. 3. The feed size (F. 80) of the ball mill was assumed to be 2 mm (2000 microns).Design, Construction and Performance Analysis of a 5
احصل على السعر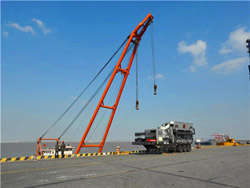
A new model between the Bond and Hardgrove grindability
The majority of pulverised coal boilers use flue gas treatment processes involving limestones that is prepared using horizontal tumbling mills such as ball mills for limestone grinding. However, it would be much more logical to replace such plants using ball mills for grinding of limestones with plants based on vertical mills characterized byThe laboratory ball mill was designed for grinding limestone, meaning that the work index required for the specific power calculation was assumed to be the work index of limestone, which is 11.6 KWh/t, with a specific gravity of 2.6 g/cm. 3. or 2600 kg/m. 3. The feed size (F. 80) of the ball mill was assumed to be 2 mm (2000 microns).Design, Construction and Performance Analysis of a 5
احصل على السعر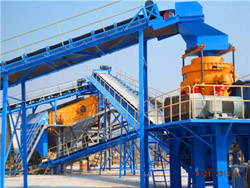
Optimization of Ball Mill Grinding of a Limestone-Type
The effect of ball size and interstitial filling on the performance of dry ball mill grinding was investigated for a limestone-type brecciated uranium ore. The optimum grinding was obtained with the combination of different balls (12.7–37.5 mm) and interstitial filling of 50% (20% ball filling ratio at fixed material filling ratio = 4%). The net power Mill Type Overview. Three types of mill design are common. The Overflow Discharge mill is best suited for fine grinding to 75 106 microns.; The Diaphram or Grate Discharge mill keeps coarse particles within the mill for additional grinding and typically used for grinds to 150 250 microns.; The Center-Periphery Discharge mill has feed reporting from both AMIT 135: Lesson 7 Ball Mills & Circuits Mining Mill
احصل على السعر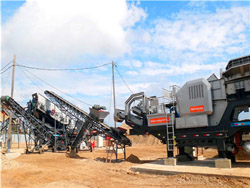
(PDF) SIZE REDUCTION BY GRINDING METHODS
Ball mills are used for wet grinding iron ore, g old/copper ore, nickel ore and other ores, as wel l as lime/limestone for flue gas desulphurisat ion systems, coal and other raw materials. Rod mill :Moreover, optimizing ball filling ratio and mill speed appropriately by the AR method, the residence time of feed in the grinding chamber could be reduced and the mass fraction of the desired size was improved during the grinding process [14, 15]. More recently, Chimwani et al. [16] investigated the influence of feed size on ball grinding. AsA study of the grinding of magnetite/limestone mixture in a
احصل على السعر
Optimization of Ball Mill Grinding of a Limestone-Type
the performance of dry ball mill grinding was investigated for a limestone-type brecciated uranium ore. The optimum grinding was obtained with the combination of dierent balls (12.7–37.5 mm) and interstitial lling of 50% (20% ball lling ratio at xed material lling ratio= 4%). The net power consumption in a ball mill is proportional to theThe sequence to evaluate the vertical roller mills consisted of a laboratory jaw crusher, a rod mill and two ball mill stages with differing grinding media. The dimensions and settings of the laboratory mills are given in Table 1 and are illustrated in details in (Boehm and Flachberger, 2006). The jaw crusher used is a standard jaw crusherAn energy based comparison of vertical roller mills and tumbling mills
احصل على السعر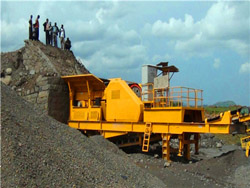
China Mill For Dolomite, Mill For Dolomite Manufacturers,
Motor Power : Small Mining Ore Fine Powder Grinding Wet Stone Grinder Ball Mill Price for Iron Tin Manganese Lead Aluminum Coal Gold Copper Dolomite. US$ 5000-14000 / Set. Small Mining Use Fine Powder Grinding Mill Limestone Ball Mill for Gypsum Barite Dolomite Powder Machine . US$ 2000-8000 / Piece. 1 PieceThe CL-5 Stirred Vertical Ball Mill for Limestone Grinding is a smaller version of the production sized CL Series Mills. It is ideal for research, scale-up and small-scale production. This mill will process in the range of 200-500 pounds of limestone per hour and is equipped with a variable frequency drive (VFD) and a 15 horsepower inverterBall Mill Particle Grinding Union Process
احصل على السعر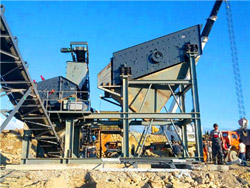
Mechanistic modeling and simulation of a batch vertical stirred mill
Snapshot of DEM simulations of vertical stirred mill charged with 86.8 kg of 20 mm grinding media and screw shaft rotating at 3 m/s (a), 2.5 m/s (b) and 2.0 m/s (c). Grinding media are colored by their velocity. The collision energy spectra of the mill can be observed in Fig. 5, showing the normal, tangential and the total energy dissipated行星式球磨仪 PM 100 Wet and nano-scale grinding with the PM 100. Wet grinding is used to obtain particle sizes below 5 µm, as small particles tend to get charged on their surfaces and agglomerate, which makes further grinding in dry mode difficult. By adding a liquid or dispersant the particles can be kept separated.行星式球磨仪PM100--德国RETSCH(莱驰)研磨仪粉碎仪
احصل على السعر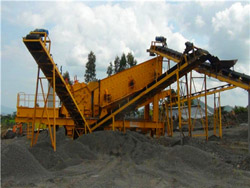
Review on vertical roller mill in cement industry & its
Following are advantages of VRM over Ball Mills with reference to these issues: • Strong drying ability Inlet hot air from Kiln can dry materials with 20% water content. (max moisture 20% vs. 3% in ball mill) [15], [16]. • Big feed size The vertical roller mill can grind the material of particle size of 5% of the grinding roller diameter.Stirred Mills Ultrafine Grinding. In Mineral Processing Design and Operations (Second Edition), 2016. 10.2.4 Operation of Vertical Mills. Vertical stirred mills are usually charged with media occupying 80% of the mill volume which is in sharp contrast to tumbling mills that are seldom charged more than 40% of their volumes to allow space for the tumbling Stirred Mill an overview ScienceDirect Topics
احصل على السعر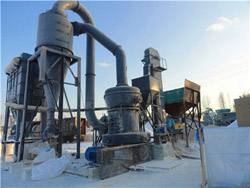
A Technical and Economic Comparison of Ball Mill Limestone
The size reduction is achieved by attrition, abrasion, and impact between the ore itself and between the ore particles and grinding media [8]. According to Swart et al. [9], ball mills are mostly
احصل على السعر