
(PDF) Grinding in Ball Mills: Modeling and Process
A ball mill is a type of grinder widely utilized in the process of mechanochemical catalytic degradation. It consists of one or more Abstract. The breakage and liberation of minerals are the key to fluidized mining for minerals. In the ball milling process, steel balls function as not only a grinding action implementer but also energy carrier The Effect of Grinding Media on Mineral Breakage
احصل على السعر
Kinetics of Dry-Batch Grinding in a Laboratory
With ball-mill grinding being one of the most energy-consuming techniques, setting the optimal values of the operational and Mishra B K, Rajamani R K. The discrete element method for the simulation of ball mills. Appl Math Model, 1992, 16(11): 598 doi: 10.1016/0307-904X(92)90035-2 离散元法在磨矿设备及参数优化研究中的应用现状 USTB
احصل على السعر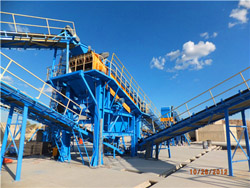
Ball milling A green and sustainable technique for the preparation
Ball milling is a mechanical technique used to grind powders into fine particles [1]. Generally, a ball mill consists of a hollow cylindrical vessel that rotates Mill load is a key parameter for the safety and optimal control of the grinding process in mineral processing. Grinding sound signal is usually used to detect the mill Mill Load Identification Method for Ball milling Process
احصل على السعر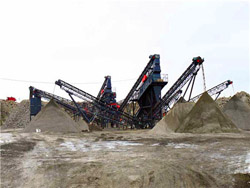
Modeling of Bauxite Ore Wet Milling for the Improvement of Process
This study aimed to model bauxite grinding and assess the optimum material filling volume in a laboratory ball mill in order to improve mill and overall process The use of ball milling to obtain cellulose nanocrystals was also explored by the group of Yu, who extracted CNCs from ball-milled wood via a multi-step process. 40 Douglas-Fir wood chips were firstly hammer-milled to wood Ball milling: a green technology for the
احصل على السعر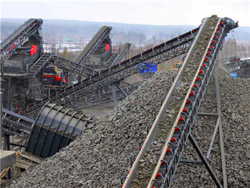
Intelligent Optimal-Setting Control for Grinding Circuits of Mineral
In the process industry, the ball mill is a large-scale basic equipment, which is widely used for material crushing [1]. Due to the limitation of rotating working conditions, it is difficult toAnalysis of process of grinding efficiency in ball and rod mills with various feed parameters D Foszcz1, D Krawczykowski1, T Gawenda1, E Kasińska-Pilut2 and W Pawlos2 1AGH University of Science and Technology, Faculty of Mining and Geoengineering, Department of Environmental Engineering and Mineral Processing, Analiza efektywności mielenia w młynach kulowym i
احصل على السعر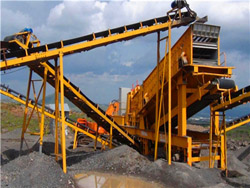
Fine grinding in a horizontal ball mill ScienceDirect
Introduction. As coarse grained, easily processed ore bodies are depleted, more disseminated, fine-grained ores are being treated. Adequate liberation of valuable components within a fine-grained ore is often only achieved once the particle size of the ore has been reduced to levels below the traditional ball mill cut-off of 45. μm.. To aid in the The breakage and liberation of minerals are the key to fluidized mining for minerals. In the ball milling process, steel balls function as not only a grinding action implementer but also energy carrier to determine the breakage behavior of ores and the production capacity of the mill. When ground products present a much coarse or much The Effect of Grinding Media on Mineral Breakage Properties
احصل على السعر
The energy efficiency of ball milling in comminution
Comminution represents up to 50% of the total energy consumption in the mineral production process [2]. Moreover, comminution using ball milling is highly inefficient due to heat and mechanicalBall milling is an energy-intensive unit operation and usually consumes a major proportion of the power drawn by a typical mineral processing plant. Hence, substantial economic benefits can be achieved by optimal design and by operating ball milling circuits under optimum process conditions. This requires an accurate ball mill Modelling the performance of industrial ball mills using
احصل على السعر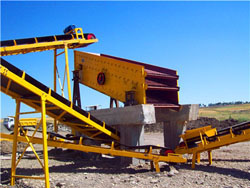
(PDF) Grinding Media in Ball Mills-A Review ResearchGate
Comminution is a very important and result-determining step in mineral processing. This is because further downstream processes in the beneficiation chain depend entirely on it.Mill load is a key parameter for the safety and optimal control of the grinding process in mineral processing. Grinding sound signal is usually used to detect the mill load indirectly. However, the relationship between grinding sound signal and the mill load is really complicated. In this study, a mill load identification method is proposed byMill Load Identification Method for Ball milling Process
احصل على السعر
Modeling of Bauxite Ore Wet Milling for the Improvement of Process
Size reduction is a necessary operation in mineral processing plants and provides the desired size for separation operations and the liberation of the valuable minerals present in ores. Estimations on energy consumption indicate that milling consumes more than 50 % of the total energy used in mining operations. Despite the fact that ball Ball mill is the key equipment for crushing materials after they are crushed. It is widely used in cement, silicate products, new building materials, refractories, chemical fertilizer, ferrous and nonferrous metals mineral processing, powder metallurgy, glass ceramics, and other production. Dry grinding or wet grinding can be carried out forBall Mill SpringerLink
احصل على السعر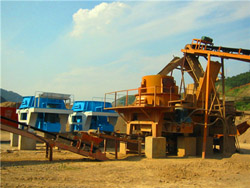
Tubular Rod Mills ScienceDirect
The design characteristics of industrial rod mills are similar to ball mills. Most rod mills used in mineral processing are of the overflow discharge type as illustrated in Figure 7.2 a. Centre peripheral (Figure 7.2 c) and end peripheral discharge mills (Figure 8.1) are also in use. The feed end is generally fitted with spout feeders, scoopOne of the important parameters in mineral processing is particles morphology, which is a function of the comminution mechanism. Particles morphology has considerable impacts in flotation process.(PDF) Effect of wet ball milling on copper ore flotation by
احصل على السعر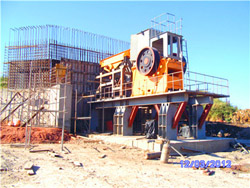
Assessing load in ball mill using instrumented grinding media
Grinding is an important unit operation in mineral processing, which aims for sufficient particle size reduction and mineral liberation for downstream separation processes. the high-dimensional mechanical signals of multi-source modes are difficult to map the characteristic parameters of the ball mill, which leads to low fusion efficiencyIn mineral processing, ball mill is generally coupled with a hydrocyclone. Figure 3 gives a flow diagram where ball mill receives hydrocyclone underflow and sometimes(PDF) MATERIAL BALANCE IN FROTH FLOTATION USING
احصل على السعر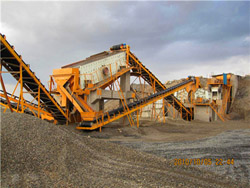
Minerals Free Full-Text Rod Mill Product Control and Its
Energy consumption and pollution are current strategic issues that need to be addressed in the mining industry. Both have an economic and environmental impact on production, so their optimization, control, and mitigation are, at the very least, mandatory. Although rod milling has fallen into disuse in recent decades, some companies still use it The key to a successful separation in mineral processing is the preparation of particles with adequate liberation under the correct pulp chemical conditions . Wet milling in ball mills followed by flotation is the general practice employed in the beneficiation of copper sulphide ores in which the major minerals of commercial significanceGalvanic Interaction between Chalcopyrite and Pyrite with
احصل على السعر
MINERAL PROCESSING MILLING United Diversity
The process can be wet or dry but is more commonly carried out wet. Maximum rod length is about 6 to 7 metres, otherwise there is a risk of the rods bowing. The drum diameter is limited to 0.6 or 0.7 times the length of the mill. Characteristics Rod mills are used for grinding hard minerals. This type of mill is usually used as the first stageCrushing and grinding processes are typically used by crushers and mills to liberate minerals, which are energy-intensive processes (especially fine grinding by mill). Meanwhile, ball mills are known for their lowest energy efficiency. The efficiency of ball mills is about 1.0% and, in some cases, less than 1.0% based on energy consumption.A process mineralogy approach to study the efficiency of
احصل على السعر
Consumption of steel grinding media in mills A review
In mineral processing, ceramic balls have first been applied in secondary mill of the two-stage grinding circuit, showing great positive effect on the grinding process. This study evaluated the impact of replacing steel cylpebs with ceramic balls on the grinding effect, circulating load, classification effect, and the change of the particle
احصل على السعر