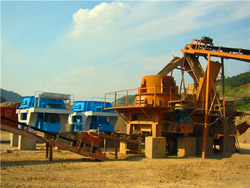
Cement grinding optimisation ScienceDirect
Abstract The current world consumption of cement is about 1.5 billion tonnes per annum and it is increasing at about 1% per annum. The electrical energy consumed in cement production is approximately 110 kWh/tonne, and around 40% of A two-compartment ball mill with a highly efficient separator is still procured for new cement grinding units installation, although the vertical roller mill has now Review on vertical roller mill in cement industry & its
احصل على السعر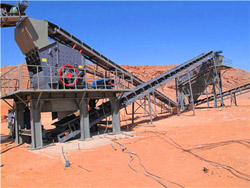
Energy-Efficient Technologies in Cement Grinding
In this chapter an introduction of widely applied energy-efficient grinding technologies in cement grinding and description of the Cement mill also called cement grinding mill, is a cement grinding machine used in cement plant for raw materials, cement clinker, and coal grinding. The cement mill produced by AGICO can be divided into the raw mill, Cement Mill Cement Grinding Machine AGICO
احصل على السعر
(PDF) Pregrinding technology ResearchGate
PDF Cement production is an energy intensive process. Grinding is a high-cost operation consuming approximately 60% of the total electrical energy Find, The modular vertical roller mill for grinding cement raw material, cement clinker, and additives with an installed power of up to 12,000 kW was specifically Grinding process optimization IEEE Xplore
احصل على السعر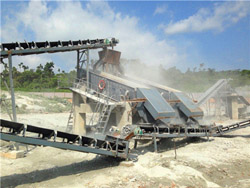
Energy and exergy analyses for a cement ball mill of a new
Nowadays, ball mills are used widely in cement plants to grind clinker and gypsum to produce cement. In this work, the energy and exergy analyses of a cement In this context, the grinding performance of the ball mill in terms of energy consumption, size reduction and the mill inside samplings as well as the performance of Energy and cement quality optimization of a cement grinding circuit
احصل على السعر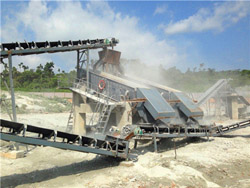
Review on vertical roller mill in cement industry & its
With the grinding capacity of a vertical roller mill and the ability to dry, grind and sort in a single unit, the vertical roller mill offers a definite advantage over the ball In cement production process, about 26% of the total electrical power is used in grinding the raw materials. During grinding process, the energy obtained from the Reducing energy consumption of a raw mill in cement industry
احصل على السعر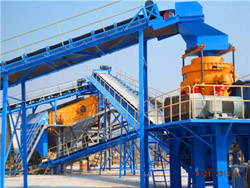
Cement Grinding Unit Cement Grinding Plant
Cement grinding unit cost. Take the annual output of 600,000 tons of large-scale cement grinding station as an example, there are three common options can be recommended: SCHEME 1: roller press + φ 3.2 ×13m The noise levels in some production areas, such as in the cement mill, air compressor, blower or crusher, in the cement grinding station ranged between 89 and 105 dBA and exceeded the Vietnamese permissible exposure limit At the three cement grinding plants (S2, S3, S4), the equivalent noise level ranged between 68.8 dBA and Noise Pollution and Its Correlations with Occupational Noise
احصل على السعر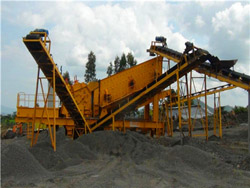
Reducing energy consumption of a raw mill in cement industry
Several grinding methods are available in cement industry depending upon the material to be ground. In cement production process, about 26% of the total electrical power is used in grinding the raw materials. During grinding process, the energy obtained from the rotary burner is consumed. In this study, the first and second law analysis of a The cement factory where the measurements were made was located in Romania’s center-north and had a final section with two cement mills. Cement grinding was performed inside the cement mill workshop. This manufacturing phase’s product was cement—a powdery, finely ground material in closed-loop tubular ball mills . The monthly Dust Emission Monitoring in Cement Plant Mills: A Case
احصل على السعر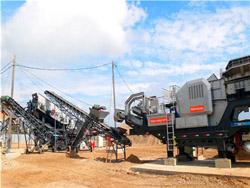
(PDF) Dust Emission Monitoring in Cement Plant Mills: A
Distribution of dust emissions at bag filters in the cement mill section no.1 (mill filterpoint A and separator filter-point B, Figure 1) of the analyzed cement plant.The energy consumption of the total grinding plant can be reduced by 20–30 % for cement clinker and 30–40 % for other raw materials. The overall grinding circuit efficiency and stability are improved. The maintenance cost of the ball mill is reduced as the lifetime of grinding media and partition grates is extended. 2.5.Energy-Efficient Technologies in Cement Grinding IntechOpen
احصل على السعر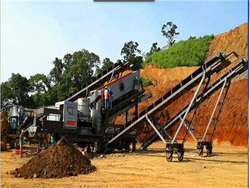
Latest trends in modular cement grinding plants Cement
CMBI Sinoma, the other supplier for modular cement grinding plants, uses one ball mill type with a grinding capacity of 35 t/h or 0.25 Mt/a as well as a VRM with a capacity of up to 70 t/h or 0.5 Mt/a in its MMG concept (Modular & Mobile Grinding). While the specific power consumption of the ball mill is stated to be < 35 kWh/t, the one for theThe energy consumption for comminution processes in the cement plant are divided into the four main stages: Raw material crushing (1-2 kWh/t of clinker) Raw material grinding (5-15 kWh/t of clinker)Cement Finish Milling (Part 2: Comminution) LinkedIn
احصل على السعر
Cement grinding optimisation ScienceDirect
Cement grinding simulation. To optimise cement grinding, standard Bond grinding calculations can be used as well as modelling and simulation techniques based on population balance model (PBM). Mill power draw prediction can be carried out using Morrell’s power model for tumbling mills. The case study. Potential benefits of using the cement ball mill. Application: limestone, clay, coal, feldspar, calcite, talc, iron ore, copper, phosphate, graphite, quartz, slag. Capacity: 0.65-615T/H. The cement ball mill usually can be applied to raw meal grinding or cement grinding. Besides, the cement ball mill also can be used for metallurgical, chemical, electric power, other miningRaw Mill, Cement Raw Mill, Raw Mill In Cement Plant Cement
احصل على السعر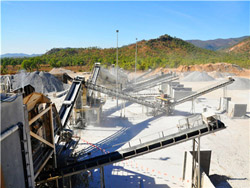
Cement Plant, Cement Equipment Cement Plant
Our Production Equipment. AGICO Cement is a cement plant manufacturer with production capacity of 30,000 tons of equipments and structure parts and 20,000 tons of casting parts.own production equipment of Φ8m BIGBOSS Cement is the result of that dream. The plant itself is located in Porac, in Pampanga, Luzon. It is around 100km north of Manila, the capital of the Philippines, in the north of the country. It uses an unusual production process that makes use of a volcanic material, lahar, which resulted from a major eruption of the nearby Plant report: BIGBOSS Cement, Philippines Global Cement
احصل على السعر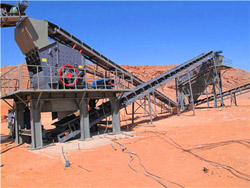
Review on vertical roller mill in cement industry & its
Now a days Cement plants are producing 75–80% PPC & 20–25% OPC due to high market demand of PPC. Production of PPC is cheaper and it's market rate is also lower than OPC by nearly 25 rupees per bag, so general consumer are attracted towards PPC cement. Cement companies also want to produce more and more PPC grade.The cement industry is highly energy-intensive, consuming approximately 7% of global industrial energy consumption each year. Improving production technology is a good strategy to reduce the energy needs of a cement plant. The market offers a wide variety of alternative solutions; besides, the literature already provides reviews of Technological Energy Efficiency Improvements in Cement Industries
احصل على السعر
Cement Grinding Mill Ball Mill, Vertical Cement Mill, Cement
Cement grinding mill play vital role in cement grinding plant, including cement ball mill, vertical mill, cement roller press, AGICO CEMENT supply all types cement grinding mill with competitive price, Ask now! Skip to content +86 13683722138. info@cement-plants. about.Girth gear is a large ring gear that is mounted on the outer circumference of the mill shell in cement making machinery. Its primary purpose is to transmit torque from the motor to the mill, which is responsible for grinding raw materials into fine powder. The girth gear meshes with a smaller gear called a pinion, which is mounted on theGirth Gear and Pinion in Cement Industry Rotary Kiln & Cement Mill
احصل على السعر
Cement grinding optimisation ScienceDirect
The “work horse” of the cement grinding plant is the two-compartment ball mill, commonly called the tube mill. Significant advances in model development were achieved in recent years ( Benzer et al., 2001,Benzer et al., 2003 ) through research on industrial scale.Abstract The results of industrial tests of ShKh15steel grinding balls with diameters of 25, 30, and 35 mm of 5th hardness group as per GOST (State Standard) 7524–2015 at AO Kharkiv Pilot Cement Plant during grinding of cement in the second chamber of a cement mill are presented. It is shown that the use of ShKh15 steel Efficiency of Using Small Diameter Grinding Balls for Cement Grinding
احصل على السعر
Energy and exergy analyses for a cement ball mill of a new
Nowadays, ball mills are used widely in cement plants to grind clinker and gypsum to produce cement. In this work, the energy and exergy analyses of a cement ball mill (CBM) were performed andLin, X. & Liang, J. Modeling based on the extreme learning machine for raw cement mill grinding process. in Proceedings of the 2015 Chinese Intelligent Automation Conference 129–138 (2015).Modeling of energy consumption factors for an industrial cement
احصل على السعر