
PROCESSING AND PELLETIZING OF LOW GRADE
Table 2.2 Iron ore minerals and gangue mineral 21 Table 2.3 Typical pellet chemical composition 31 Table 2.4 Typical pelletizing feed material size analyses 34In a DR process, iron ore pellets and/or lump iron ores are reduced by a reducing gas to produce DRI or hot briquetted iron (HBI). Depending on the generation of Quality requirements of iron ore for iron production
احصل على السعر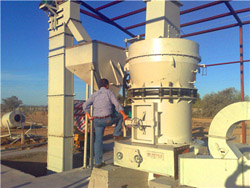
Direct reduction of fluxed iron ore pellets made from coarse iron ore
The preparation of finer iron ore particles which can be used suitably in pelletization, decreases the binder requirement in the process, but increases the energy consumption The pelletizing process has lower energy consumption and less pollution emission compared with iron ore sintering process. Its superiority made it a significant Improvement on the thermal cracking performance of pellets prepared
احصل على السعر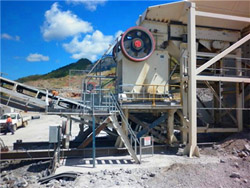
A novel iron ore pelletization for increased strength under
A novel process to produce iron ore pellets of strength surpassing the indurated pellets under ambient conditions owing to the interfacial chemical bonding In this study, the effect of adding limestone on the metallurgical properties (reducibility, swelling, cracking, softening temperature, Low-Temperature Disintegration, Effect of adding limestone on the metallurgical properties of iron ore
احصل على السعر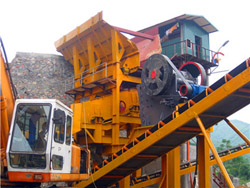
Effect of Sintering and Porosity Development on Direct
The experiences gained in various methods of reducing iron ore by gas have shown that this is most effectively done when the ground ore is compacted into Iron ore pellets not only have excellent metallurgical and mechanical properties but are also essential raw materials for improving iron and steel smelting in the context of the Cold crushing strength of pellets at medium tem- perature
احصل على السعر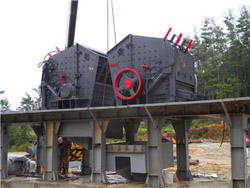
Rungta Steel Leading Iron Pellets Manufacturers
Rungta Mines Ltd produces iron pellets with cold crushing strength (CCS) of 210+ and porosity of 24+. For More Specifications, Call us at 18008905121 The company specializes in the production of iron pellets, which are small, solid balls of iron ore that are used as a key raw material in the steel industry. These iron pellets possessSection snippets Materials. Acid iron ore pellets with 4.6 wt.% SiO 2 manufactured by Severstal Resources in Karelia were used in the investigations. Both test pellets were produced in a laboratory-scale pelletizing drum and fired in sample baskets set in the middle of the sintering belt on the same production line as commercial blast Effect of adding limestone on the metallurgical properties of iron ore
احصل على السعر
Effect of Iron Ore Pellet Size on Metallurgical
Iron ore pellets are small and hard spherical particles agglomerated from a fine iron ore concentrate. They are used in the blast furnace process to produce hot metal. The diameter of blast furnace iron ore pellets are very critical for their handling and use. Cold crushing strength (CCS) of iron ore pellets varies widely from as low as 80 Kgf / pellets to as high as 350 Kgf /pellets depending upon the input material quality and the process variables. The most preferred range of CCS of iron ore pellets is 180-240 Kg f /Study and Implementation of Quality Improvement
احصل على السعر
Amenability of Reduced Iron Ore Pellets to Mechanical
iron ore pellets that results from weakening of the micro-scopic structure during reduction. In this study the authors analyzed the hardness and cold crushing strength of pellets under different levels of reduction. That study demonstrated that a sharp drop in both crushing strength and hardness occurs at reductions as low as 10%. It also5.1 The size range for iron ore pellets at the point of dispatch shall be as follows. Requirements for the iron ore pellets at the point of dispatch is applicable to this clause only, as degradation of iron ore pellets may occur during transportation: +19 mm 5 percent, Max –19 +9 mm 85 percent, Min –9 +5 mm 5 percent, Max –5mm 5 percent, MuxIS 11092 (2001): Iron Ore Pellets for Direct Reduction
احصل على السعر
Microstructure and phase analysis of indurated iron ore pellets
Binding mechanisms in wet iron ore green pellets with a bentonite binder. Powder Technol., 169 (3) (2006), pp. 147-158. View PDF View article View in Phase and microstructural characterization of iron ore pellet and their relation with cold crushing strength test. Miner. Process. Extr. Metall. Rev., 37 (5) (2016), pp. 295-304. CrossRef The use of microstructural characteristics as a quality control tool has been increasingly employed in iron ore agglomeration processes. In the production of the pellets, phase identification for(PDF) Phase and Microstructural Characterization of Iron Ore
احصل على السعر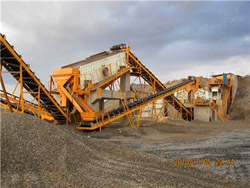
Driving investments in ore beneficiation and scrap upgrading
Another example has been presented by RioTinto, where the silica content in DR pellets was decreased from 4.5 to under 1% through the implementation of silica flotation (Chaigneau 2015).However, the benefits of obtaining a higher iron content in the ore product must be weighed against the iron losses due to the separated gangue, the tailing 3.3.1 Crushing and Grinding 48 3.3.2 Iron Ore Concentration 49 4.4 Carbothermal Reduction Behaviors of Iron Ore Pellets 89 4.4.1 Nonisothermal Experiment 89 4.4.2 Design of Experimental for Isothermal Experiment 94 REDUCTION OF MALAYSIAN IRON ORE PELLET BY USING COAL AS REDUCTANT ),i. reduction. . .REDUCTION OF MALAYSIAN IRON ORE PELLET BY
احصل على السعر
OPTIMIZATION OF IRON ORE PELLETS PRODUCTION IN
Then the iron ore pellets will sent through metallic conveyor into the furnace to undergo heating process at 1200 degrees. After the heating process, the heated base mix will converted into a semi liquid cake. Using a sinter breaker machine the cake is break into small pellets. Finally these iron ore pellets under goes cooling in the cooling The committee responsible for this document is ISO/TC 102, Iron ore and direct reduced iron, Subcommittee SC 3, Physical testing. This fourth edition cancels and replaces the third edition ( ISO 4700:2007 ) which has been technically revised to provide clarification in 7.2 when using automatic equipment.ISO 4700:2015(en), Iron ore pellets for blast furnace and
احصل على السعر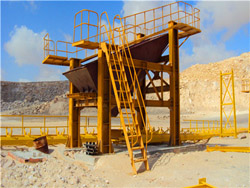
Breakage of green iron ore pellets ScienceDirect
Abstract. Mechanical degradation of green iron ore pellets prior to induration is a concern and can result in return of material to discs or drums or contamination of the feed to the induration furnace during pelletization. The work investigates the effects of pellet size, drop height, impact angle and type of surface on The dry crushing strength (DCS) of the dried pellet was measured using a weighing balance and a mild steel compression plate. The average value of maximum weight (in kg) applied by the MS plate on individual 10 dry pellets placed on the weighing balance till it crumbled was taken as the DCS value. The considered iron ore green Mineralogical investigation on preheating studies of high LOI iron ore
احصل على السعر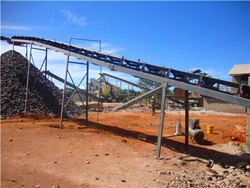
Sintering of the pellets of Egyptian iron ore with lime
The preparation of fluxed iron ore pellets with high basicity (1.17) is possible without sticking at indura- tion temperature up to 1300°C with the help of lime as an ef-One example is Umadevi et al. (2011), who carried out basket trials with iron ore pellets with basicity ranging from 0.08 to 1.15 in order to understand the effect of adding limestone on the microstructural, physical and metallurgical properties of iron ore pellets. In their study, the Tumble Index (TI) and the Cold Crushing Strength (CCSEffect of adding limestone on the metallurgical properties of iron ore
احصل على السعر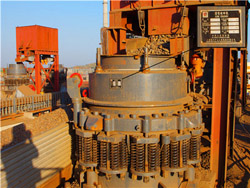
Mechanical strengths of green pellet. Download Scientific
The acceptable minimum drop number of green pellets is 4 from a height of 46 cm according to [3]. The compressive strength of industrial green pellets lies generally between 1.0 and 2.0 kg/pelletProduction of iron oxide pellets from iron ore fines in-volves different operations like drying of ore fines to re-move the moisture and grinding to get the required fine-ISIJ International, Vol. 47 (2007), No. 1, pp. 67–72 Prediction of Iron Ore Pellet Strength Using Artificial Neural Network ModelPrediction of Iron Ore Pellet Strength Using Artificial
احصل على السعر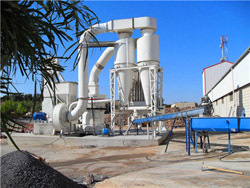
Amenability of Reduced Iron Ore Pellets to Mechanical
iron ore pellets that results from weakening of the micro-scopic structure during reduction. In this study the authors analyzed the hardness and cold crushing strength of pellets under different levels of reduction. That study demonstrated that a sharp drop in both crushing strength and hardness occurs at reductions as low as 10%. It alsoThe effect of lime addition in hematite iron ore pellets on its physico-chemical as well as mechanical properties with respect to blast furnace requirement was studied in a laboratory scale with varying basicity i.e. 0-2.0.Increasing addition lime produced more calcium-alumino-silicate phases (slag) as evidenced by SEMEDAX analysis.The Effect of Additives and Reductants on the Strength of Reduced Iron
احصل على السعر