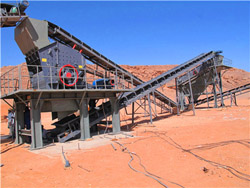
Energy-Efficient Technologies in Cement Grinding
In this chapter an introduction of widely applied energy-efficient grinding technologies in cement grinding and description of the In this chapter an introduction of widely applied energy-efficient grinding technologies in cement grinding and description of the operating principles of the related [PDF] Energy-Efficient Technologies in Cement Grinding
احصل على السعر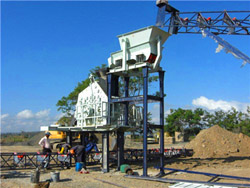
Overview of cement grinding: fundamentals,
Grinding is an essential operation in cement production given that it permits to obtain fine powder which reacts quickly with There are four stages in the manufacture of portland cement: (1) crushing and grinding the raw materials, (2) blending the materials in the correct proportions, (3) burning the Cement Extraction, Processing, Manufacturing Britannica
احصل على السعر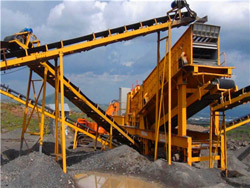
Energy and cement quality optimization of a cement grinding circuit
Within the study, it was aimed to optimize both the energy utilization and the product quality of a conventional cement grinding circuit during CEM I 42.5R cement Abstract: As a world-wide leader in grinding solutions for the cement industry and understanding the changing needs of cement producers and how to tailor Grinding process optimization IEEE Xplore
احصل على السعر
Trends and developments in green cement and concrete
The cement industry faces a number of challenges that include depleting fossil fuel reserves, scarcity of raw materials, perpetually increasing demand for cements The increasing demand for “finer cement” products, and the need for reduction in energy consumption and green house gas emissions, reinforces the need for Cement grinding optimisation ScienceDirect
احصل على السعر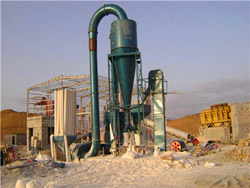
Advanced grinding in the cement industry Request PDF
This paper is concerned with a comparative analysis of modern cement grinding systems, namely, combined grinding (Comflex®), high-pressure roll mill (HPRM) With the introduction of the high compression machines such as High Pressure Grinding Rolls (HPGR), Vertical Roller Mills (VRM) and Horomills, efficiency of the grinding circuits was improved in terms of energy and downstream effects. Among these devices, vertical roller mills have an important position in cement and mining industry.Operational parameters affecting the vertical roller mill
احصل على السعر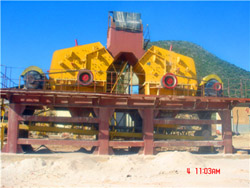
High Pressure Grinding Roll AGICO Cement Plant
Capacity: 100 ~ 1450 T/P. SEND INQUIRY. AGICO CLM Series high pressure grinding rolls (HPGR) are efficient and energy-saving crushing equipment that can be widely used in crushing and grinding operations in Vertical roller mills (VRM) are widely used to grind, dry, and select powders from various materials in the cement, electric power, metallurgical, chemical, and nonmetallic ore industries. For the sectors above, the VRM is a powerful and energy-intensive grinding field [1], [2]. It is used to grind slag, nonmetallic ore, and other block A cement Vertical Roller Mill modeling based on the
احصل على السعر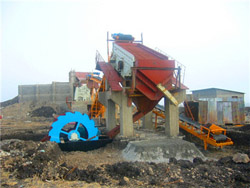
Roller press is well-accepted technology in India Indian Cement
In the case of Slag grinding, the acceptance of roller press in finish grinding is well recognised. It offers the distinct advantage of saving of about 6-7 Kwh/t as compared to Vertical Roller Mill at 4200 Blaine. KHD has sold 27 Sag Grinding Circuits and maintains about 70 % market share in slag grinding in India.A ball mill is a type of grinder widely utilized in the process of mechanochemical catalytic degradation. It consists of one or more rotating cylinders partially filled with grinding balls (made(PDF) Grinding in Ball Mills: Modeling and Process Control
احصل على السعر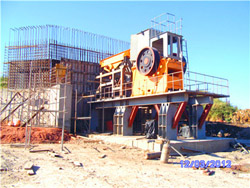
Process to utilize crushed steel slag in cement industry
To improve the utilization efficiency of steel slag in cement industry, cement clinkers are prepared by simulated multi-phased clinker sintering technology with crushed steel slag (without grinding). The results show that after high temperature treatment, the inert components and tough phases of steel slag such as iron phase, calcium ferrite Grinding is an abrasive machining process that uses a grinding wheel or abrasive belt as the cutting tool. It is commonly used to remove material from a workpiece, to produce a smooth finish on the surface of the workpiece, or to remove burrs from the surface. Grinding can be performed wet or dry, and can be performed on a variety of What is Grinding ? Working Principles & Applications in
احصل على السعر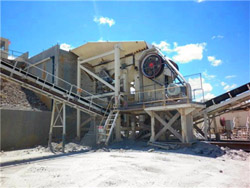
separators thecementgrindingoffice
Separators in the cement industry. Also called: Cage separators or High Efficiency Separators. These separators has been developed in the beginning of the eighties (O'Sepa from Onoda Cement). As the second generation, the air flow required for the separation is produced by an external fan. The separator material feed is carried out The cement industry has been working on different alternatives to lower the CO 2 emissions, The most common dry grinding systems in the industry are ball mills, vertical roller mills and high-pressure roller press. Basic principles of hybrid alkaline cements. Chem. Mater. Res., 4 (2013), pp. 12-14. Google ScholarA review: Alkali-activated cement and concrete
احصل على السعر
Cement Grinding LinkedIn
Cement grinding using Grate Discharge principles developed in the ore milling industry applied to the cement industry. This experience plus the years of manufacturing know how unquestionablyOne of the most significant developments for the cement industry dates back to 1931, when an attempt was made to mix carbon black in concrete to make a darker middle lane on U.S. Route 1, in AvonCement Finish Milling (Part 1: Introduction & History)
احصل على السعر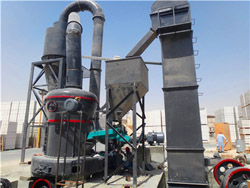
Cement Extraction, Processing, Manufacturing Britannica
There are four stages in the manufacture of portland cement: (1) crushing and grinding the raw materials, (2) blending the materials in the correct proportions, (3) burning the prepared mix in a kiln, and (4) grinding the burned product, known as “ clinker ,” together with some 5 percent of gypsum (to control the time of set of the cement).The vertical cement mill is large-scale cement grinding machine. With advantages of energy-efficient and stable quality, vertical roller mill is widely applied to many industries, such as cement, power, metallurgy, chemical and nonmetallic mining industry and etc. As a typical type of Cement Mill, vertical cement mill set crushing, drying, grinding, grading Vertical Cement Mill, Vertical Roller Mill AGICO Cement Plant
احصل على السعر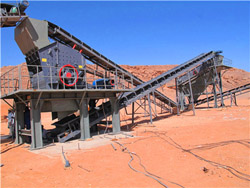
Application of Vertical Roller Mill in Cement Production
Conclusion. In conclusion, the application of vertical roller mill technology in the cement industry has revolutionized the way cement is produced. VRMs are more energy-efficient, eco-friendly, and produce a more consistent product compared to traditional grinding mills. They are also more suitable for use in urban areas due to their lowerTel.: +49-241-80-28183; fax: +49-241-80-22293. E-mail address: [email protected] Abstract The efficient processing of innovative materials, the further development of grinding tools and machine concepts as well as an increasing economic and environmental pressure are current challenges in grinding technology.High Performance Grinding ScienceDirect
احصل على السعر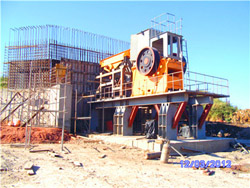
Raw Mill, Cement Raw Mill, Raw Mill In Cement Plant Cement
cement ball mill. Application: limestone, clay, coal, feldspar, calcite, talc, iron ore, copper, phosphate, graphite, quartz, slag. Capacity: 0.65-615T/H. The cement ball mill usually can be applied to raw meal grinding or cement grinding. Besides, the cement ball mill also can be used for metallurgical, chemical, electric power, other miningAbstract The results of industrial tests of ShKh15steel grinding balls with diameters of 25, 30, and 35 mm of 5th hardness group as per GOST (State Standard) 7524–2015 at AO Kharkiv Pilot Cement Plant during grinding of cement in the second chamber of a cement mill are presented. It is shown that the use of ShKh15 steel Efficiency of Using Small Diameter Grinding Balls for Cement Grinding
احصل على السعر
Cement Raw Meal & Homogenization Process in The Cement Industry
The raw meal preparation process of the cement industry includes four links: mining, pre-homogenization, grinding, and homogenization, which form the homogenization chain of raw meal preparation. Raw meal homogenization is the most important process link of the four, accounting for 40% of the homogenization task.
احصل على السعر