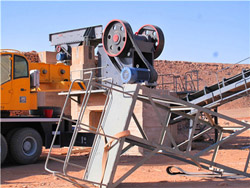
6 Points in the Production Process to Optimize
Three of the most important goals of any cement-making facility is to reduce product variation, extend quarry life, and meet The studies show that cement manufacturing plants have great potentials in providing peak-shaving and valley-filling in crushers and cement mills with up to 10% and Reducing energy consumption of a raw mill in cement industry
احصل على السعر
Industrial : Optimization for the Cement Industry ABB
cement mill operations in four ways: • More consistent quality (grade). The continual monitoring of the mill loading and the adjustment of the feed and separator In this study, the first and second law analysis of a raw mill is performed and certain measures are implemented in an existing raw mill in a cement factory in order to Reducing energy consumption of a raw mill in cement industry
احصل على السعر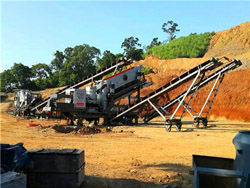
How can you reduce st in the production of cement ball mill
Here are some strategies and tips to help you reduce energy consumption in a cement ball mill: Optimize Ball Mill Operation : Ensure that key operating parameters Request PDF On Jun 1, 2012, Adem Atmaca and others published Reducing energy consumption of a raw mill in cement industry Find, read and cite all the research you Reducing energy consumption of a raw mill in cement industry
احصل على السعر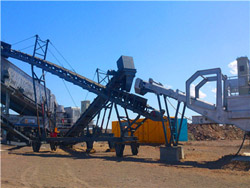
Technological Energy Efficiency Improvements in
Improving production technology is a good strategy to reduce the energy needs of a cement plant. The market offers a wide variety of alternative solutions; besides, the literature already provides reviews One option to significantly reduce greenhouse gas emissions from the cement industry is CO 2 Capture and Storage/Utilization (CCS/U). An alternative direct Measuring false air in cement production ABB
احصل على السعر
Energy-Efficient Technologies in Cement Grinding
1. Introduction. Cement is an energy-intensive industry in which the grinding circuits use more than 60 % of the total electrical energy consumed and account for most of the manufacturing cost [].The The environmental effect of cement production has been documented in many studies (Adesina 2020; Szabó et al. 2006;Timperley 2018). While suggestions have been proffered to reduce carbon dioxideReducing energy consumption of a raw mill in cement industry
احصل على السعر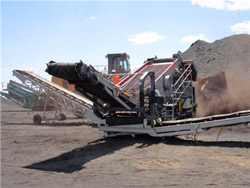
(PDF) Dust Emission Monitoring in Cement Plant Mills: A
Distribution of dust emissions at bag filters in the cement mill section no.1 (mill filterpoint A and separator filter-point B, Figure 1) of the analyzed cement plant.The raw materials are then ground in suitable ball mills/vertical roller mills (VRMs), both of which are common grinding mills, in order to achieve the targeted fine powder, Improving energy efficiency reduces CO 2 emissions from fuel and electricity uses and may reduce the cost of cement production. Improvements may be attained by usingFull article: An overview of alternative raw materials used in cement
احصل على السعر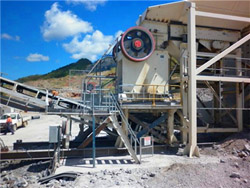
Reducing Machinery Noise in Cement Plants IEEE Xplore
Cement plant noise up to 106 dBA comes mainly from crushers, mills, kiln burners, and compressors. Control measures, including damping, enclosing, and insulating either source or workers, or providing workers with ear-protective devices are illustrated. Mill noise can be damped by massive foundations.Excessive MgO and CaF2 lead to the decrease of C3S and appearance of unconventional cement phases of α-C2S and γ-C2S in MS4 and MS5. Thus, the setting times of MS4 and MS5 are prolonged, and(PDF) MINIMIZATION OF CEMENT KILN DUST ResearchGate
احصل على السعر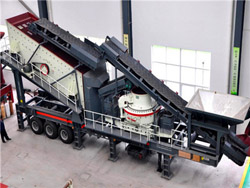
How to Reduce the Grinding Temperature of the Cement Ball Mill?
Method for reducing the temperature of grinding cement. 1. Reduce the temperature of the clinker. ①Strengthen material management, avoid clinker with high temperature into the grinding head bin, and prevent red material from entering the grinding. ②Spray water in the cooler to reduce the clinker temperature. ③Spray water on the clinker belt.to reduce the amount of portland cement clinker (the nodules produced in a cement kiln) used as a binder in concrete. For example, since the late 2000s, AASHTO M 85 allows up to 5 percent high-quality natural limestone to be interground with the clinker, which has the potential to lower the overall GHG emissions associated with portland Supplementary Cementitious Materials and Blended
احصل على السعر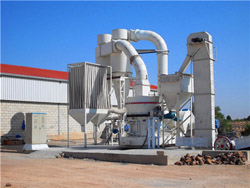
(PDF) Reducing the SO2 emission from a cement kiln
Quarrying drilling, blasting, hauling, Cement mill, fuel preparation, packaging, road cleaning, and stacks are the sources of particulate matter in the form of dust and carbon particles [19, 20A decrease in the cost of materials would undoubtedly result in significant savings in the entire cost of building production because it made up two-thirds of the cost . Cement in particular is responsible for about 42% of cost of building and the demand has proliferated dramatically by current construction boom [4,5,6]. Cement is produced inUtilization of sawdust composites in construction—a review
احصل على السعر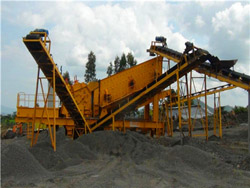
Review on vertical roller mill in cement industry & its
The need of the cement industry in the future is to reduce the specific energy consumption in grinding process [7] (Fig. 2). This study investigated a mathematical model for an industrial-scale vertical roller mill(VRM) at the Ilam Cement Plant in Iran. The model was calibrated using the initial survey's data, and the breakage rates Due to limitation of the mill’s rotational speed, the smallest ball size is usually restricted to about 15 mm. Cement grinding using stirred mills (Pilevneli and Azizli, 1999) indicates that using smaller media (5–8 mm range) improves grinding energy efficiency up to 50% using stirred mills. For specialized types of cement, which are finerCement grinding optimisation ScienceDirect
احصل على السعر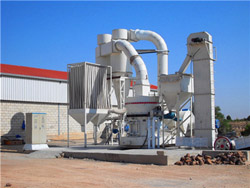
A comprehensive review on Advanced Process Control of cement
The clinker is then fed into a cement mill and ground into cement. Finally, the cement has been packed and is ready to be delivered. 2.1. This optimised fuzzy logic unit is used to compute the necessary MPC weights to improve efficiency and reduce energy consumption compared to the traditional human-based system. Economic MPC (EMPC) Carbon Capture and Storage (CCS) is the main strategy to reduce CO 2 emissions in more than 50%, but it requires a great financial investment and high energy quality, both of which greatly affect final cost of cement. Carbon Capture and Use (CCU) is an alternative to CCS to reuse CO 2 through chemical products.Sustainable alternatives to CO2 reduction in the cement
احصل على السعر
Cement grinding optimisation ScienceDirect
Cement production process typically involves: •. grinding limestone (and other raw materials to achieve the right chemical composition) to about 90% passing 90 μm in a dry circuit, •. making cement by the chemical reaction between the components of the ground mixture. This chemical reaction occurs at high temperature in a rotary kiln, •.Three of the most important goals of any cement-making facility is to reduce product variation, extend quarry life, and meet customer requirements. Today, there are many types of technologies available that can help cement production owners meet these goals as well as help improve product quality, boost efficiency, lower production 6 Points in the Production Process to Optimize Cement Making
احصل على السعر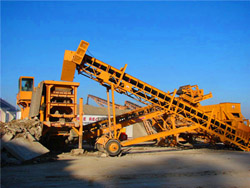
Dust Emission Monitoring in Cement Plant Mills: A Case
The cement factory where the measurements were made was located in Romania’s center-north and had a final section with two cement mills. Cement grinding was performed inside the cement mill workshop. This manufacturing phase’s product was cement—a powdery, finely ground material in closed-loop tubular ball mills (Figure 1). Introduction. The cement industry is classified as one of the more energy extensive industries that produce a huge amount of CO 2 in many countries in the world (e.g., EU [1] including UK [2], Egypt [3] representing the Middle East and Africa, and China [4, 5] representing Asia).. One way to increase efficiency and reduce costs, as well as Analysis of high clinker ratio of Portland Composite Cement (PCC)
احصل على السعر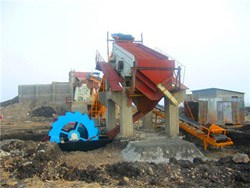
How can we decarbonise the mining and cement industries?
The first step will be to demonstrate industrial-scale clay calcination for use as a binder, a second step is to decarbonise this process using electrification and renewable energy. Clay is particularly interesting as it is abundant in growth regions, which also face a lack of good quality limestone. While new solutions to decarbonise the
احصل على السعر