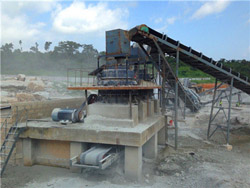
LUBRICANTS FOR HIGH-PERFORMANCE GRINDING
Coolants used for conventional grinding of hard materials. Since hard metals and cermets are still today processed on conventional machines with rubber or resinoid bonded tools, PDF On Jul 1, 2011, Sirsendu Mahata and others published Coolants and their Role in Grinding Find, read and cite all the research you need on (PDF) Coolants and their Role in Grinding ResearchGate
احصل على السعر
Application of coolants during tool-based machining A review
The typical application of coolants for grinding operations are water-based oils, chemical fluids and emulsion with a concentration of 1:25 and 1:60 mix Further investigations in the fields of fluid dynamic processes in supply nozzles and in the grinding zone are the key to optimization of cooling and lubrication Friction, Cooling and Lubrication in Grinding ScienceDirect
احصل على السعر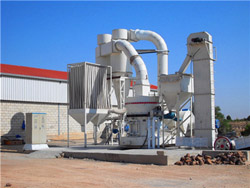
Coolant and Lubrication in Machining SpringerLink
Through-tool coolant helps in chip disposal in deep-hole drilling and grinding operations. Specially designed pumps and leak-proof seals to prevent damage A comprehensive list of all known methods of cooling and lubrication of the grinding zone classified according to the physical state of the delivered medium with a Modern Approach to Delivery Coolants, Lubricants and
احصل على السعر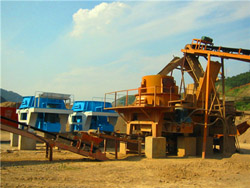
Experimental evaluation and surface integrity analysis of Nature
The cryogenic coolant system used in this work consisted of a jet of liquid nitrogen (LN 2), applied directly to the grinding wheel into a near zone between Grinding is usually performed with a grinding fluid or coolant. In order to provide the necessary lubrication and cooling capacity and achieve parts free of metallurgical defects while maintaining lower Critical Cooling for Gear Grinding Success Norton
احصل على السعر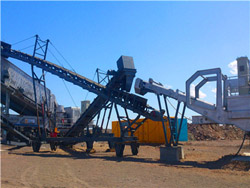
Approaches to tailor the cooling supply to the grinding process
In addition, the coolant velocity v cool can be adjusted to the circumferential speed of the grinding wheel so that the coolant does not need to be accelerated after the nozzle outlet in order to get into the contact zone. This is based on a tangential orientation of the coolant beam to the grinding wheel and orientation of both The heat produced from the machining operation can be dissipated easily, and flush away the chips at the same time. Flood coolant system offers the best performance in machining operation such as milling, grinding and drilling. In some applications, high pressure jets (above 1000 psi) may be used to deliver the coolants Application of coolants during tool-based machining A review
احصل على السعر
Intro to Grinding Methods, Machines and Tools Practical
Oftentimes grinding operations are compartmentalized by machinists and considered separate from typical cutting processes used in machine shops. Coolant use when grinding. Whether or not coolant is necessary for your grinding application will depend on how much heat is generated.I use a flow rate based upon the grinding power created during the process, because the more aggressive a cycle is, the more coolant is applied. With conventional abrasive wheels, a flow rate of 2 gpm/hp is effective. For superabrasive wheels, a flow rate close to 1 gpm/hp (3.8 L/min/hp) works well.In Grinding, Coolant Application Matters SME
احصل على السعر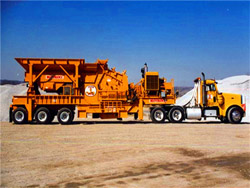
Grinding Machine: Parts, Working, Operations, & More [PDF]
#7 Coolant System. During grinding, the coolant system helps in keeping the workpiece and grinding wheel cool. Additionally, it facilitates in clearing away chips and debris. Read also: What is Shaper Machine and The 4 Major Types of Shaper Machines. Hardness Comparison of Abrasive Material. An abrasive is a second hardest material, Because the grinding process creates a lot of heat, flood coolant is most appropriate. However, it is equally important that the fluid be delivered where it is needed the most: at the point of cut. “The application [method] of the fluid is very important; it should apply the fluid to the interface where it is needed the most,” said Foster.Understanding Grinding Fluid Canadian Metalworking
احصل على السعر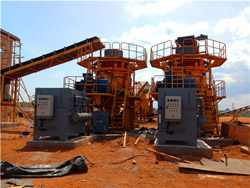
Coolant and Lubrication in Machining SpringerLink
Certain emulsifiable oils and synthetic fluids are formulated especially for grinding operations and are used in concentrations of 1 part concentrate in 25–60 parts water. An increase in the oil in the emulsion from 2.5 % to 10 % can improve the grinding ratio and surface finish and results in power saving.I use a flow rate based upon the grinding power created during the process, because the more aggressive a cycle is, the more coolant is applied. With conventional abrasive wheels, a flow rate of 2 gpm/hp is effective. For superabrasive wheels, a flow rate close to 1 gpm/hp (3.8 L/min/hp) works well.In Grinding, Coolant Application Matters SME
احصل على السعر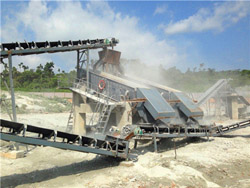
Experimental evaluation and surface integrity analysis of
The cost of finishing operations such as grinding is nearly 30% of the total manufacturing cost in a mechanical piece 1. or soluble oil as coolant fluid (WET) when grinding several steel plates.IC 3618 is a medium-duty synthetic coolant that is engineered for moderate-duty machining and grinding operations utilizing metals like carbon steel, alloy steels, stainless steel, aluminum alloys, copper, brass and bronze. It is formulated to be the ideal general-purpose metalworking fluid for use with ferrous and nonferrous metals, alike.Machining & Grinding Coolants International Chemical Company
احصل على السعر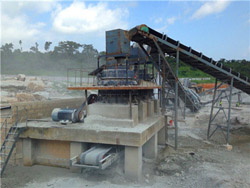
Metal-oxide based nanofluid application in turning and grinding
Grinding operation. From the literature studied, it was found that very limited works have been carried considering TiO 2 nanofluid in grinding operations. Rahmaan et al. [36] utilized titanium dioxide nanofluid in grinding of cast iron and found the increasing nature of grinding temperature and MRR with an increase in Table speed For traverse surface grinding that alternates between upcuts and downcuts, a large step over: 50% or more, for example, may induce heat generation. A 50% step over means that 50% of the first will Tips for Improved Surface Grinding Norton Abrasives
احصل على السعر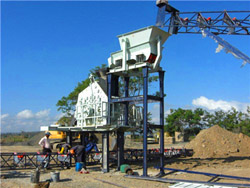
Coolant The Importance and Benefits of Filtering Coolant on
Cooling fluids are an integral part of metal cutting and grinding operations. The importance of maintaining coolant quality is often underestimated. Outlined are the reasons and benefits of filtering coolant as well as the effects of wear particles in machines and work pieces.The mechanical effect of an air jet (air barrier) on the liquid coolant flow in the device [] channel leads to a decrease in the size (width) of the contact of liquid coolant with the grinding wheel and workpiece.As a result, the heat transfer conditions change, because two more zones are formed: the heat exchange zone between the coolant and Study of Heat Transfer Conditions in the Cutting Zone When Grinding
احصل على السعر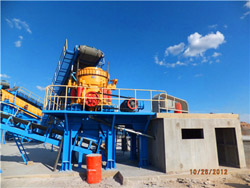
How to Select and Maintain Machine Coolant : Practical Machinist
Its versatile performance makes it suitable for a wide range of metal cutting and grinding operations for both ferrous and non-ferrous materials. JEI Full Synthetic Multi-Purpose Coolant VERSAKUT 7227. Order Now. Versakut 7227 is a multi-purposeful synthetic coolant for grinding, machining, milling, and other CNC applications.Using the cutting fluids plays a decisive role in prolonging the tool life, enhancing the machinability, and improving the machining sustainability during the grinding operations. 16, 17 The metalworking fluids could be delivered to the grinding zone in different ways, and the cooling/lubrication function was done by various techniques such Cooling and lubrication techniques in grinding: A state-of-the-art
احصل على السعر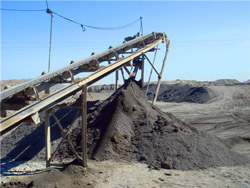
Shaping the Future. Together. Quaker Houghton
removal operations. HOCUT ® 795-H, HOCUT 795-B, HOCUT® 795-RHS, and numerous others satisfy the breadth of customer metal removal needs. QUAKERCOOL® 700 Series of products are high- performance, mineral oil free, chlorinated paraffin free microemulsion metalworking fluids for ferrous machining and grinding operations. Formulated toCoolant and Coolant Delivery A centerless grinding operation. Photo courtesy of Norton Saint-Gobain. Coolant is a key component to successful centerless grinding but is often overlooked. Many coolant delivery systems for centerless grinders are under engineered and are often neglected. The basic functions of grinding fluids are to:Tips for Trouble-Free Centerless Grinding SME
احصل على السعر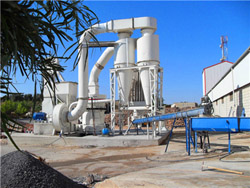
Application of nanofluids as cutting fluids in machining operations
Chetan et al. used Al 2 O 3 / water nano-lubricant in turning of Nickel-based alloy with AlTiN-coated tungsten carbide tool subjected to a deep cryogenic treatment.It is remarked that the cryogenic nano-coolant reduced the tool flank wear, cutting forces and many surface defects in the machined surface such as material re-deposition, material The Donaldson Torit® Dryflo® machine-mountable coolant mist collector use a three-stage filtration process to reduce machining mist to create a safe work environment. Grinding. Grinding operations employ abrasive grains in various forms for the removal of material and metal to produce of different types of surface finishes.Metalworking Donaldson Industrial Dust, Fume & Mist
احصل على السعر