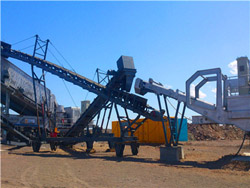
Modelling copper smelting the flash smelting plant, process and equipment
Modelling copper smelting the flash smelting plant, process and equipment Pekka Taskinen,Ari Jokilaakso,Daniel Lindberg & Jiliang Xia Pages 207-220 Received 08 The Flash Smelting had the lowest energy consumption with 10,784 MJ/t of anode copper and the Noranda Reactor the highest energy consumption with 13,072 Comparison of environmental performance of modern copper smelting
احصل على السعر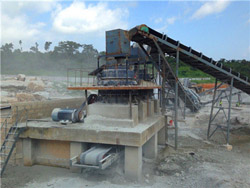
Dynamic modeling of copper flash smelting process at a
A dynamic model for quantifying the dynamic characteristic of matte grade in copper flash smelting process at a Copper Smelter in China has been developed. Based Copper Smelting Plants. We are proud of the size of our track record of delivery of MESCO’s copper smelting and refining technologies both in Japan and overseas. We have a wide range of plant designs available to Copper Smelting Plants MESCO
احصل على السعر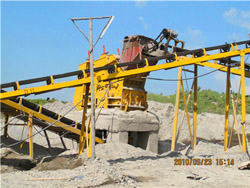
Modelling copper smelting–the flash smelting plant,
developers of a novel copper smelting technology faced, including a new approach of process chemistry, a specialised heat balance and its management, and the smelting Copper smelting plants separate elemental copper from copper concentrates through multiple sulphide oxidizing stages. The considered smelting process includes a Copper Smelting an overview ScienceDirect Topics
احصل على السعر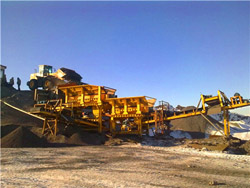
(PDF) Development of Bottom-Blowing Copper Smelting
Combining the plant operating data and the smelting mechanism of the copper concentrate, the role of the plume eye in bottom-blowing-enhanced smelting is COPPER flash smelting has been the leading technology for primary copper sulfide smelting [1] because of its low energy consumption and environmental Modelling copper smelting the flash smelting plant, process and equipment
احصل على السعر
Free Full-Text Copper Flash Smelting Process
Process control in flash smelting is based on mass and energy balance from which the operational parameters (oxygen coefficient, oxygen enrichment, and flux demand) are obtained to achieve matte and slag with defined The smelter’s specialised equipment comes from 11 different countries Canada, Finland, Germany, Australia, South Africa, the United Kingdom, China, Malaysia, Turkey, Indonesia and the Philippines. Zambia’s Advanced, World-Class Copper Smelter
احصل على السعر
(PDF) Development of Bottom-Blowing Copper Smelting
Bottom-blowing copper smelting technology was initiated and developed in China in the 1990s. The bottom-blown furnace is the key piece of equipment in the oxygen bottom-blown smelting processWaste electrical and electronic equipment (WEEE) represents a significant urban resource for precious metals. To maximize the recoveries and sustainable use of these metals, their behavior needs to be characterized in the secondary copper smelting of WEEE. The current study experimentally determined the distributions of gold, Precious metal recoveries in secondary copper smelting with
احصل على السعر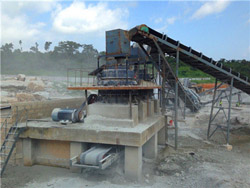
Easy Ways to Melt Copper Sciencing
Place the copper wires in the bottom of the crucible, and place the crucible on a cement slab. Put on all necessary safety equipment. Light the blowtorch. For this purpose, an industrial grade blowtorch such as oxy-acetylene is better than a propane torch because copper has a high melting point. Hold the crucible in place with tongs and directThe primary production of sulfide concentrates includes smelting to copper matte or blister copper, conversion of matte to blister copper, and refining to copper. Smelting, converting, and fire-refining can use a limited amount of secondary materials. Molten copper can effectively dissolve many metals, from valuable noble metals to Recycling Free Full-Text Primary Copper Smelter and
احصل على السعر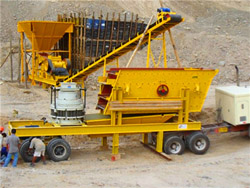
(PDF) OUTOTEC'S FULLY AUTOMATED SMELTER 2020 -THE VISION
At the Copper 2016 conference in Kobe, Japan, Outotec introduced a vision for the year 2020, wherein smelting would make use of four digital cornerstones: intelligent instruments, advanced processSO3 in the copper smelting flue gas not only causes serious corrosion in heat exchange and dust collection equipment but also increases the amount of sewage acid (waste acid or polluted acid from copper smelting). In this study, we attempted to reduce the damage by ejecting pyrite into the flue to suppress SO3 formation in the flue. First, the Suppressing SO3 formation in copper smelting flue gas by
احصل على السعر
5 Best Metal Melting Furnace Kits For Home Use (2023 Update)
This set comes with a sizable 10 KG crucible. To accommodate the vessel, Castmaster had to increase the size of the entire unit. While this may limit where you can use it, the larger size is beneficial for continuous metalwork. The lid features a wide hole, which you can easily use to feed the furnace as it heats up.Bottom-blowing copper smelting technology was initiated and developed in China in the 1990s. Injection of oxygen-enriched high-pressure gas strongly stirs the molten bath consisting of matte and slag. Metals Free Full-Text Development of Bottom
احصل على السعر
Dynamic modeling of copper flash smelting process at a
The flash smelting process is widely used throughout the world for copper production, accounting for about 50% of global capacity for primary copper production [1]. A Copper Smelter in China has operated an Outotec type flash smelter for about 30 years. Due to the sources of clean deposits are progressively depleted, the copper concentrateThe global amount of waste electrical and electronic equipment (WEEE) is growing fast. Non-ferrous metals represent a large portion of this waste, and they can be potentially recovered via black copper smelting. Alumina and magnesia, originating from the e-waste or fluxes, can be present in the feed of a secondary copper smelter in varying Slag Chemistry and Behavior of Nickel and Tin in Black Copper Smelting
احصل على السعر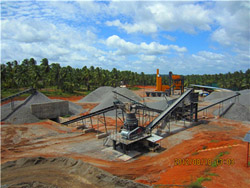
Transport Phenomena in Copper Bath Smelting and
smelting technologies have become the main copper matte production method today (Moskalyk and Alfantazi 2003). Copper production techniques have undergone a lot of development and new equipment and processes are still emer-ging, such as modern continuous copper smelting and con-The Kennecott Utah Copper Corporation (KUCC) uncoupled the smelting and converting steps in traditional smelting practice with the added capital cost and operating expense of introducing several additional unit operations such as matte granulation, matte storage, grinding, drying, material handling, and other ancillary Review of copper pyrometallurgical practice: today and tomorrow
احصل على السعر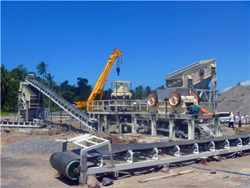
Recoveries of rare elements Ga, Ge, In and Sn from waste
Moreover, the copper-slag-spinel equilibrium systems are examined. The experiments were executed simulating high alumina-bearing copper scrap smelting in typical black copper smelting conditions of pO 2 = 10 −10 –10 −5 atm (1 atm = 1.01325 × 10 5 Pa) and T = 1300 °C. The experimental technique employed utilized a highly advancedDifferent types of metal-bearing wastes, such as WEEE (Waste Electrical and Electronic Equipment), are important urban minerals in modern society, and the efficient recycling and reuse of their metal values is of key interest. Pyrometallurgical copper smelting is one of the most prominent ways of treating WEEE, however, more accurate Behavior of Tin and Antimony in Secondary Copper Smelting
احصل على السعر
Recycling of tellurium via copper smelting processes
Various copper smelting processes are efficient and widely used ways of treating different kinds of copper-bearing wastes, such as waste electrical and electronic equipment (WEEE). With the reducing grade of primary copper ores and the increasing amount and complexity of electronic scrap, new elements are introduced into the Direct-to-blister copper smelting is an important smelting process due to its short process, low energy consumption and environmental protection. This study attempts to use high-grade chalcocite as the raw material for direct-to-blister smelting to realize the production of blister in a single furnace. The issues and required conditions of the Metals Free Full-Text Investigation on Direct-to-Blister Smelting
احصل على السعر
Copper Smelting an overview ScienceDirect Topics
Copper Production. W.G. Davenport, in Encyclopedia of Materials: Science and Technology, 2001 4 The Future. The major trend in copper smelting and converting is towards improved capture of the SO 2 that is evolved from oxidizing CuFeS 2 and other copper sulfide minerals. Improved SO 2 capture benefits the environment and the resulting H 2 SO 4
احصل على السعر