
Raw Mill Raw Mill In Cement Plant AGICO Cement Raw Mill
Cement ball mill and cement vertical mill are two raw mills commonly used in cement plants. As the main cement equipment in the cement production line, the two cement raw mills Raw mix, high grade limestone, sand and iron ore are transported from their bins to raw mills for drying and further fine grinding. The raw mill is either a Ball mill with Review on vertical roller mill in cement industry & its
احصل على السعر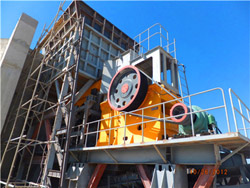
Thermodynamic Performance Analysis of a Raw Mill System in a Cement Plant
The cement production process has different steps, including (1) grinding and blending raw materials, (2) heating these materials to very high temperatures in the 1. Introduction Cement production in the world is currently about 1.6 billion ton per year. About 2% of the electricity produced in the whole world is used during the Reducing energy consumption of a raw mill in cement industry
احصل على السعر
OK™ Raw and Cement Mill FLSmidth
Our best-in-class OK™ Mill is a globally successful vertical roller mill solution for grinding raw material, cement and slag. Its cutting-edge design features consistently deliver the We analyzed a raw mill and investigated the first law and second law efficiency values. Performance assessment of a raw mill indicates that the grinding Reducing energy consumption of a raw mill in cement industry
احصل على السعر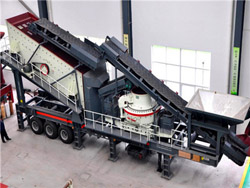
Energy and exergy analyses of a raw mill in a cement production
, Zuhal Oktay c 4 Add to Mendeley https://doi/10.1016/j.applthermaleng.2005.11.016Get rights and content Abstract The material efficiency values for a raw mill, pyro-processing tower, rotary kiln, clink cooler, and cement mill are determined to be 36.69%, 34.24%, 39.24%, Analysis of material flow and consumption in cement
احصل على السعر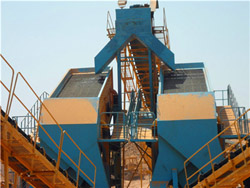
Cement Mill Cement Ball Mill Vertical Cement
low cost easy to control wide applications Cement mill in cement plant Cement mill is the core equipment for grinding material after clinker production. Generally, the cement mill can be called cement grinding The raw mill machine functions as a main material grinder in the initial milling process such as limestone, silica stone, clay, and iron sand to become raw mix. To find out the frequency of damage(PDF) Analysis of Raw Mill Machines Maintenance
احصل على السعر
OK™ Raw and Cement Mill FLSmidth
Our best-in-class OK™ Mill is a globally successful vertical roller mill solution for grinding raw material, cement and slag. Its cutting-edge design features consistently deliver the highest quality products with the greatest efficiency. It is affordable to install and cost effective to operate over your cement plant’s lifetime.The study indicates that for a dry type cement production process, the carbon dioxide emission intensity for kiln feed preparation process is about 5.4 kg CO 2 per ton cement produced. In this study, the raw mill of a cement plant is considered and its performance based on the first and second laws of thermodynamics is investigated.Reducing energy consumption of a raw mill in cement industry
احصل على السعر
Modeling of energy consumption factors for an
the vertical roller raw mill circuits (line 2) in the Ilam cement plant. e critical operating parameters gathered during the standard operation are summarized in Table 1. Variables were monitoredRaw Mill Feeding. In the value stream map of cement manufacturing the raw mill feeding is an intermediate activity between Pre-homogenization and raw milling, and has not been discussed separately by most of the authors. However, in my opinion it remains and must remain as of pivotal importance, so far as the quality assurance is considered.Raw Mill Feeding Cement Plant Optimization
احصل على السعر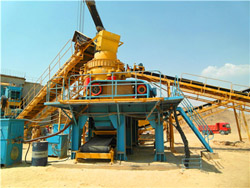
Reducing energy consumption of a raw mill in cement industry
The study indicates that for a dry type cement production process, the carbon dioxide emission intensity for kiln feed preparation process is about 5.4 kg CO 2 per ton cement produced. In this study, the raw mill of a cement plant is considered and its performance based on the first and second laws of thermodynamics is investigated.Raw mill is mainly used for grinding cement raw meal in the cement factory production process. It is also suitable for metallurgical, chemical, electric power and other industrial mining enterprises to grind various ores and other grindable materials. Cement raw meal is a mixture of various raw materials before cement calcination.Cement Raw Mill in Cement Plant for Cement Raw Meal
احصل على السعر
8VLQJ$VSHQ 3OXV6LPXODWRU IOPscience
simulator was used for the thermodynamic performance of a raw mill (RM) and raw materials preparation unit in a cement plant in Nigeria using actual operating d ata. The raw mill has a capacity of 240,000 kilogram- material per hour. Also, 7.6 Role, Planning & Control. Traditionally, maintenance has responded to problems and failures identified by operators. Increasingly, however, with the development of more sophisticated monit. Cement Plant Operation Handbook Free ebook download as PDF File (.pdf), Text File (.txt) or read book online for free.Cement Plant Operation Handbook PDF Mill (Grinding) Cement
احصل على السعر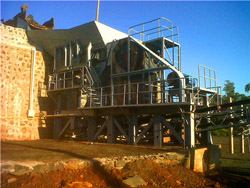
Thermodynamic Performance Analysis of a Raw Mill System in a Cement Plant
The exergy destruction rate and exergy efficiency were obtained by using the mass and energy and exergy balance equations. The exergy destruction rate and exergetic performance of the raw mill system in the cement plant were calculated to be 2940 kW and 34.67%, respectively. In addition, the system design parameters that affected the The cement manufacturing process involves the extraction and processing of raw materials, such as limestone, clay, and shale, which are then heated in a kiln at high temperatures to form clinker(PDF) Cement Manufacturing Process and Its Environmental
احصل على السعر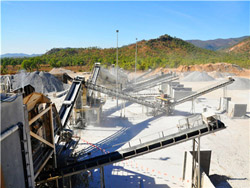
Vertical Roller Mills FLSmidth
For raw materials and cement clinker, the vertical roller mill is an excellent grinding solution because of the relatively lower cost of installation, ease of operation and maintenance, energy efficiency and product quality. Further, our vertical roller mill solution for cement grinding has an ability to dry, grind and separate within a singleDistribution of dust emissions at bag filters in the cement mill section no.1 (mill filterpoint A and separator filter-point B, Figure 1) of the analyzed cement plant.(PDF) Dust Emission Monitoring in Cement Plant Mills: A
احصل على السعر
Heat Integration in a Cement Production IntechOpen
The kiln has an operation capacity of 90 t/h and upper bound of 110 t/h. A total of 57 t/h of the clinker is produced inside the kiln. For the heating of the raw mill, kiln raw meal, and a coal mill, hot flue gases from the kiln are deployed. Gases exit from a preheating tower with a temperature at about 370°C.β [1 − α; p 2; n − p − 1 2] = (1–α) th quantile of β [p 2; n − p − 1 2] distribution. For α = 0.05, the number of outliers is 44 among 280 data corresponding to an upper limit control U C L M a h a l a n o b i s = 4.55 as illustrated in Fig. 3.The results of these outliers have been carefully analyzed by a process expert from the cement plant. Efficient machine learning model to predict fineness, in a vertical raw
احصل على السعر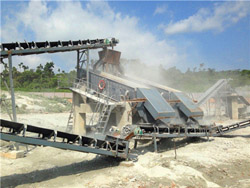
Review on vertical roller mill in cement industry & its
Now a days Cement plants are producing 75–80% PPC & 20–25% OPC due to high market demand of PPC. Production of PPC is cheaper and it's market rate is also lower than OPC by nearly 25 rupees per bag, so general consumer are attracted towards PPC cement. Cement companies also want to produce more and more PPC grade.The energy consumption of the total grinding plant can be reduced by 20–30 % for cement clinker and 30–40 % for other raw materials. The overall grinding circuit efficiency and stability are improved. The maintenance cost of the ball mill is reduced as the lifetime of grinding media and partition grates is extended. 2.5.Energy-Efficient Technologies in Cement Grinding IntechOpen
احصل على السعر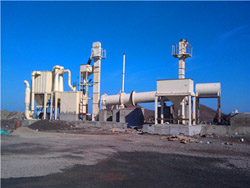
A Survey and Analysis on Electricity Consumption of Raw Material Mill
In the whole process of cement production, the electricity consumption of a raw material mill accounts for about 24% of the total. Based on the statistics of the electricity consumption of the raw material mill system of 1005 production lines in China between 2014 and 2019, it is found that the average electricity consumption of the raw material The objective of this study is to perform energy and exergy analysis of a raw mill (RM) and raw materials preparation unit in a cement plant in Turkey using the actual operational data. The RM has a capacity of 82.9 ton-material hourly. Both energy and exergy efficiencies of the RM are investigated for the plant performance analysis andEnergy and exergy analyses of a raw mill in a cement production
احصل على السعر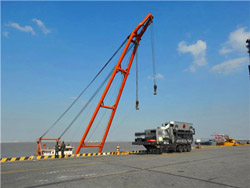
Ventilation Prediction for an Industrial Cement Raw Ball Mill
In the cement industry, grinding is one of the most consuming energy stages in the production units. Around 65% of the total used electrical energy in a cement plant has to be utilized to grind raw materials, coal, and clinker [1,2].Through the process, many variables can affect the efficiency and productivity of this dry grinding procedure,
احصل على السعر