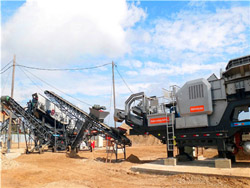
MODELLING OF IRON ORE PROCESSING IN
MODELLING OF IRON ORE PROCESSING IN TECHNOLOGICAL UNITS BASED ON THE HYBRID APPROACH Vladimir MORKUN*,Vitalii TRON*,Vadym ZYMOHLIAD* Figure is the diagram of the iron ore concentrate production and distribution system. Iron ores are mined Integrated Production and Distribution Planning for the
احصل على السعر
Iron ore sintering ScienceDirect
Physical characteristics Mineralogy Granulation Densification 15.1. Introduction Sintering is a thermal process of converting loose fine particles into a solid 4 Rheology variability and design examples. Designing iron ore tailings slurry pipeline systems for intermediate to high concentrations, where the slurry yield stress could be Pumping system design challenges for high-density iron
احصل على السعر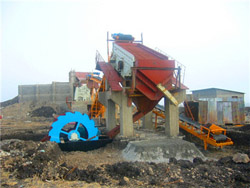
(PDF) Design of Comminution Circuit for Optimum
Design of Comminution Circuit for Optimum Performance of the Gravity Separation Unit at Itakpe Iron Ore Processing Plant, Nigeria Authors: Oyedele Ajaka Federal University of Technology,...Effective technology for a complex wasteless processing of the iron ores has been designed and includes three main components (plats): comminution plant, briquette plant, pigment plant. The...(PDF) Effective Processing of the Iron Ores
احصل على السعر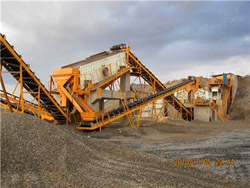
Iron Ore Processing, General SpringerLink
Making iron and steel from iron ore requires a long process of mining, crushing, separating, concentrating, mixing, agglomeration (sintering and pelletizing), Add in our advanced knowledge of iron-ore processing, ore behavior, and modeling design tools, and our clients get the most efficient and value-engineered bulk-materials handling Iron Ore Hatch Ltd
احصل على السعر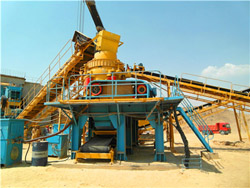
(PDF) Iron Ore Pelletizing Process: An Overview
Bentonite, an inorganic binder, has been the main binder used in the iron ore pelletizing. process since the beginning of pellet production in the 1950s. Bentonite promotes the forma-. tion ofDesign the plant: You will need to design your processing plant to optimize the recovery of iron ore and minimize waste. This will involve selecting equipment and designing processes for crushinghow to set up a iron ore processing plant LinkedIn
احصل على السعر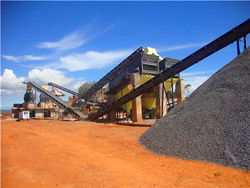
Full article: How green primary iron production in South
The production of iron and steel is one of the largest global sources of industrial greenhouse gas (GHG) emissions. South Africa (SA) could competitively export near-zero embodied GHG primary iron to steelmakers in leading decarbonizing markets. A green primary iron production process substitutes hydrogen for coke as the iron ore reductant.The magnetic component of the SLon cleaning unit is collected as the final iron ore concentrate. Plant results have demonstrated that an iron ore concentrate containing 67.1% Fe can be produced from run-of-mine ore containing 34.9% Fe, at a mass yield of 38.9% to the iron ore concentrate, an iron recovery of 74.7%, and a tailings grade Physical separation of iron ore: magnetic separation
احصل على السعر
Treatment of iron ore beneficiation plant process water by
Table 2 shows the concentrations of various metal ions and other water quality parameters present in process water collected from iron ore beneficiation plant followed by settling and filtration. It is observed from the results that the concentration of total Fe, Cr, Pb, Mn and turbidity are found to be 115.24 mg/L, 7.10 mg/L, 2.68 mg/L, 0.96 Hierro Peru Company has four major production processes: mining, mineral separation, pelletizing and transshipment. Its final products include blast furnace pellets, straight pellets, fine powder, crude fine powder and coarse-grained mine. From 2013 to 2016, the annual output of iron ore powder exceeded more than 10 million tons.Shougang Hierro Peru’s 10-Million-Ton Mineral
احصل على السعر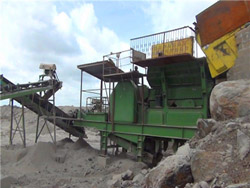
How to design an iron ore conveyor? LinkedIn
Here are the steps you can follow to design an iron ore conveyor: Determine the capacity requirements: The first step is to determine the amount of iron ore that needs to be transported over aRio Tinto Iron Ore's low-grade ore beneficiation plant in the Pilbara was commissioned in 1979. Initial engineering, design, and construction were undertaken by KBR (Kellogg Brown and Root) and Minenco (RTIO information provided to author, 2013). To evaluate an iron ore resource, develop processing routines for iron ore beneficiation, andOre Beneficiation an overview ScienceDirect Topics
احصل على السعر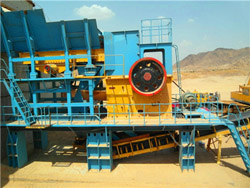
Pumping system design challenges for high-density iron
The iron ore process plants typically aim to manage the output solids concentration through the operation of the tailings thickener/s. Thickened tailings systems, due to the relatively high slurry concentration, can Designing iron ore tailings slurry pipeline systems for intermediate to high concentrations, where the slurry yield stressFig. 11 shows the simplified process flow sheet of the first industrial plant in Kwinana, Australia. The iron ore fines are preheated by the Circoheat™ system of Outotec using a part of the hot offgas from the smelter. The pre-heating system consists of a circulating fluidized bed reactor with two stages of cyclones. The iron ore is not onlyRecent status of fluidized bed technologies for producing iron
احصل على السعر
Moving towards deep underground mineral resources
High-density minerals such as iron ore, pyrite and Pb–Zn mineralisation can also be mapped using gravimetric methods. Gravity affects the management of waste reject as with the ore feed to the mill plant. Drifts, raises and ramps can be optional in this design to transport and place the waste as backfill. Designing a support system isIron ore processing is influenced by a variety of factors to var-ying extents. Among them, the following groups of factors are Technological processes of ore-concentrating plants involve multi-staged crushing and grinding to prepare ore for subsequent separation [17, 32]. As in the case of designing a mathematical model of the grind-MODELLING OF IRON ORE PROCESSING IN
احصل على السعر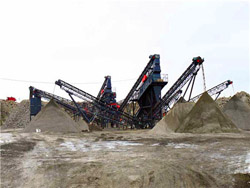
How to design an iron ore mine? LinkedIn
Here are some general steps to consider when designing an iron ore mine: 1.Conduct geological surveys: Before designing a mine, you need to have a good understanding of the deposit's geologyThe world’s largest producers rely on Mineral Technologies for iron ore processing solutions. From Canada’s Labrador Trough region, across India, Brazil and Africa, to Australia’s iron rich Pilbara, our teams deliver unrivalled expertise in fine iron ore beneficiation. Mineral Technologies can assist you to deliver a comprehensive rangeIron ore beneficiation Commodities Mineral Technologies
احصل على السعر
MINE TAILINGS FACILITIES: OVERVIEW AND INDUSTRY
Ore milled 18 800 000 000 tonnes Ore produced 10 180 000 000 tonnes Tailings 8 850 000 000 tonnes Figure 3. Estimate of the volume of tailings and waste rock produced in 2016 in relationship to ore production (c.f. plastic waste weight and volume) Copper 46% Gold 21% Iron 9% Coal 8% Phosphate 4% Lead zinc 3% Nickel 2% The installation in 1948 of a Humphreys spiral concentrator section at the Hill-Trumbull plant of The Cleveland-Cliffs Iron Co. is the latest commercial method on the Mesabi Range being used for the recovery of fine iron ore. In two stages of concentration 84 spirals treat approximately 120 long tons per hour of minus 1/8 in. ore.Humphreys Spiral Concentrator 911 Metallurgist
احصل على السعر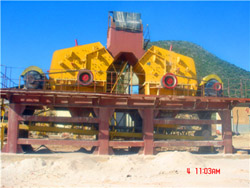
Comminution and classification technologies of iron ore
Vale, the largest iron ore company in world, is developing its S11D project, located in the Amazon region of northern Brazil (Carajas), which is expected to produce 90 million Mtpa of iron ore (Carter, 2011). In designing the innovative, modular ore crushing and screening plant for SD11, Vale was faced with the challenge of coping with theDesigning an efficient and economic mineral processing plant begins with the choice of the best and most economic comminution circuit based on ore properties and concentrate end-user's specifications.A Possible Comminution Circuit for the Iron Ore Plant Since
احصل على السعر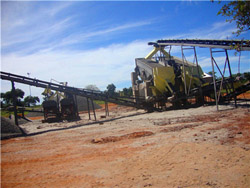
Brad Eckley Rig Electrician Hazardous Area Specialists
Brad Eckley 点赞. An EEHA Inspector and Electrical Supervisor with +15 years’ post trade experience in the installation, commissioning, maintenance and detailed inspection (hazardous or non-hazardous) of a wide array of E&I systems and equipment used to operate complex continuous processing plant within the oil and gas, mining and refiningTHE IRON AND STEEL INDUSTRY AND ITS CURRENT DEVELOPMENT (i) Iron and Steel Processes . 1. The raw materials for iron and steel making are iron ore, coal or wood . charcoal, limestone, natural gas and a variety of other materials such as fluxes, oil, etc., as well as air and water. A considerable amount of steel (approximatelyENVIRONMENTAL ASPECTS OF IRON AND STEEL
احصل على السعر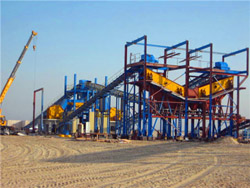
BENEFICIATION OF IRON ORE National Institute of
Iron ore sample found is a part of banded iron ore formation. Hematite and goethite are major constituents of iron ore samples. Hematite in the ore sample occurs as specularite with inter granular micro-pore spaces. Goethite is profuse and occurs as colloform product in cavities in addition with the weaker bedding planes.
احصل على السعر