
CFD based investigations into optimization of coal pulveriser
In coal-fired power plant, pulveriser is the first major component, whose performance dictates the total power plant efficiency. Uniform flow rate and desired size fraction at outlet pipes along with higher classifier efficiency are three important The energy efficiency of a typical thermal power plant is about 35-40%. Thermal power plants have pulverized coal-fired boilers. The pulverizer is one of the Industrial Coal Pulverizer Model Simulation and Parametric
احصل على السعر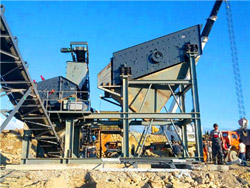
CFD based investigations into optimization of coal pulveriser
Abstract. In coal-fired power plant, pulveriser is the first major component, whose performance dictates the total power plant efficiency. Uniform flow rate and Coal Pulverizer. Learn about the different pulverizer types and how to improve the performance of a coal pulverizer to better its reliability. Visit Pall’s website to know more.Coal Pulverizer Power Plant Pall Corporation
احصل على السعر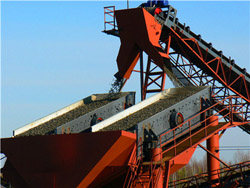
Combinatorial Optimization of Pulverizers for Blended-Coal
Mixed by pulverizers which has been widely used, is considered the most reasonable and convenient approach of coal blending. The implementation of this approach meet three A nonlinear dynamic model of a direct-fired pulverizing system that considers the effect of coal moisture on the energy balance of a coal mill was Optimization control of a pulverizing system on the basis of
احصل على السعر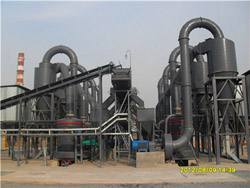
Dynamic Modelling and Simulation of Coal Pulverizer
Pulverizer. The raw coal being considered for study is having gross calorific value of 3400~4000 Kcal/kg, moisture content of 12~15% at ambient temperature of 27°C, This newly-developed coal mill model provides a valuable tool that can be used to improve the pulverizer design and optimize unit operation.(PDF) CFD Modeling of MPS Coal Mill for
احصل على السعر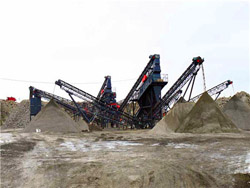
Improving Coal Pulverizer Performance and Reliability
The four most common types of coal pulverizers are: Ball-Tube Mills This type of mill consists of a rotating tube filled with cast alloy balls. Coal is introduced Now, coal-fired power generation is still the main way of generating electricity. The coal pulverizing system is one of the most important accessory equipment of coal- fired power Program Design and Calculation Example of Direct Fired
احصل على السعر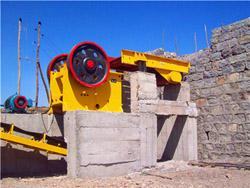
CFD based investigations into optimization of coal pulveriser
In coal-fired power plant, pulveriser is the first major component, whose performance dictates the total power plant efficiency. Uniform flow rate and desired size fraction at outlet pipes along with higher classifier efficiency are three important measures which decide the pulverizer performance. Coal pulverizer design upgrades to meet the2.3 Recommended Solutions for the Coal-Fired Power Plant to Incr ease Efficiency According to the study of (Campbell, 2013), with that year, there are existing technologies that can improve the(PDF) OPTIMISATION OF THE INSTALLED BOILER
احصل على السعر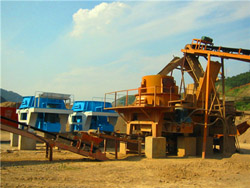
mill/sbm construction and layout of bowl mill coal pulverizer
Contribute to crush2022/mill development by creating an account on .Options for Improving the Efficiency of Existing Coal-Fired Power Plants April 1, 2014 DOE/NETL-2013/1611 OFFICE OF FOSSIL ENERGY National EnergyNational Energy Technology Laboratory
احصل على السعر
Design and Application of High-Efficiency and Energy-Saving
The process of liner wear and the changing characteristics of the ability of crushing and grinding in the coal pulverizer are analyzed, a new type of cylinder liner is developed, which has a multi-step wave crest. {Lu2011DesignAA, title={Design and Application of High-Efficiency and Energy-Saving Liner in Coal Pulverizer}, Coal pulverizer downtime can be a major factor in reducing overall plant availability and reliability. Recommended Filtration Upgrade to Achieve Total Cleanliness Control (See diagrams on back page) The majority of pulverized coal particles are in the 4-30µm range, with 70% of these particles smaller than 10µm.Improving Coal Pulverizer Performance and Reliability
احصل على السعر
mill/sbm increasing efficiency of coal pulveriser.md at main
Contribute to crush2022/mill development by creating an account on .It includes evaluation, unit component efficiency, indexes calculation, analyses and reporting. This document is applicable to existing thermal power generating units (TPGUs), where fossil fuels (e.g. coal, oil, natural gas) are combusted to generate electricity only or to supply thermal energy with the additional production of electricity (i.eISO 50045:2019(en), Technical guidelines for the evaluation
احصل على السعر
Numerical investigation of 660 MW pulverized coal-fired
The excellent performance of oxy-coal combustion power plant has been observed in term of its ability to capture carbon dioxide with 95 % purity and 96 % recovery rate. . The additional installations such as ASU and CPU units require higher auxiliary power, hence the net efficiency of the oxy-coal combustion power plant has been Unequal coal flow translates into unequal air-to-fuel ratio in the burner, deviating from the design value and thus increasing unburned carbon in fly ash, NO x and CO. Coarser particles at the mill outlet originate from poor separation and decrease the unit efficiency. In addition, coarser particles reduce burner stability at low load.CFD modeling of MPS coal mill with moisture evaporation
احصل على السعر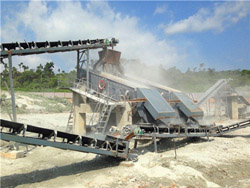
Inerting System Design for Medium Speed Vertical
This design guide has been prepared to address pulverizer inerting for vertical spindle, medium speed coal pulverizers. Examples of this type of coal pulverizer are the Alstom HP, B&W MPS,Bradley Pulverizer specializes in the design, manufacture, and supply of pulverizing systems for fine and semi-fine grinding of hard, friable, abrasive materials for various applicationsBradley Pulverizer Acquired by Lancaster Products Owner
احصل على السعر
Coal Pulverizer Power Plant Pall Corporation
The four most common coal pulverizers types are: Ball-Tube Mills. This type of mill consists of a rotating tube filled with cast alloy balls. Coal is introduced through two hollow trunnions on each side of the tube. As the tube rotates, the balls tumble onto the coal, crushing and pulverizing it. Impact Mills.In coal-fired power plant, pulveriser is the first major component, whose performance dictates the total power plant efficiency. Uniform flow rate and desired size fraction at outlet pipes along with higher classifier efficiency are three important measures which decide the pulverizer performance. Optimization of pulverizer at its best operating CFD based investigations into optimization of coal pulveriser
احصل على السعر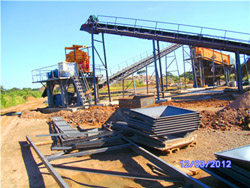
Schematic diagram for the modelled coal pulverizer with an
In this investigation, modification of coal pulverizer classifier with new geometries were proposed, by extending the classifier blade into four different lengths: 4.36”, 8.36”, 12.36” andCoal pulverizers play an important role in the functioning and performance of a PC-fired boiler. The main functions of a pulverizer are crushing, drying and separating the fine coal particlesCFD modeling of MPS coal mill with moisture evaporation
احصل على السعر
A Comparison of Three Types of Coal Pulverizers
ball tube mills provides efficient two stage comminution, resulting in lower overall system power consump- tion, particularly when pulverizing high moisture and/or oversize coal. A TRITA Pulverizer The ATRITA pulverizer is a high-speed, compactly designed machine which reduces raw coal to pulverizedContact us today to discuss your application in detail with one of our experienced sales engineers. Call (314) 433-5464, email us at info@williamscrusher, or near you. Williams Patent Crusher has become the industry leader in coal-crushing and pulverizing equipment. Learn more about our products.Coal Crushers Coal Pulverizers & Mills Williams Crusher
احصل على السعر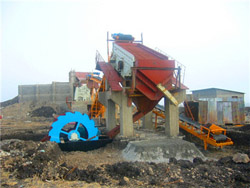
Coal Pulverizer
The four most common types of coal pulverizers are: Ball-Tube Mills. This type of mill consists of a rotating tube filled with cast alloy balls. Coal is introduced through two hollow trunnions on each side of the tube. As the tube rotates, the balls tumble onto the coal, crushing and pulverizing it. Impact Mills.In this section, an overview of the typical design of a vertical roller coal pulverizer is analysed and discussed. A schematic diagram of the used coal pulverizer is shown in Fig. 1.Typically, in the conventional coal fineness processing, the raw coal is firstly fed into a rotating bowl hub via a centre feed pipe.Computational Fluid Dynamics (CFD) investigation on
احصل على السعر