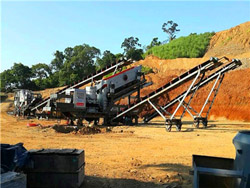
Effect of Ball-to-Powder Ratio on Morphology, Structure,
The rotation speed and ball milling time were selected as 400 r/min and 15 h, respectively. After ball milling, the powders with the size of 100-200 μm were screened Ball milling is a grinding method that grinds nanotubes into extremely fine powders. During the ball milling process, the collision between the tiny rigid balls in a concealed container Ball Milling an overview ScienceDirect Topics
احصل على السعر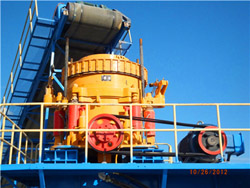
Ball milling: a green technology for the preparation and
The ball mill Ball milling is a mechanical technique widely used to grind powders into ne particles and blend materials.18 Being an environmentally-friendly, cost-effective Dried nanocrystal Nb powders, of high purity, with particle sizes, ranging from 8.5 to 14.3 nm, were synthesized by ball milling.Wet ball milling of niobium by using ethanol, determination
احصل على السعر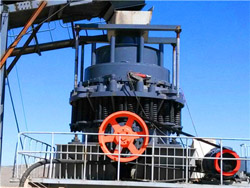
Effects of ball milling on powder particle boundaries and
Recently, increasing attention has been paid to nonferrous metal powder metallurgy materials, such as copper alloys and aluminum alloys [ 26, 27 ]. In fact, the different Commercial powders of magnesium were processed by high-energy ball milling (HEBM) using a two-stage composite process. The microstructural and Effects of two-step high-energy ball milling process and hot
احصل على السعر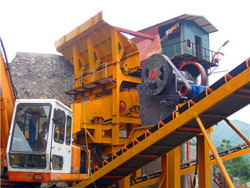
Powder Milling an overview ScienceDirect Topics
Controlling the powder-milling process. Prof. Dr. M. Sherif El-Eskandarany, in Mechanical Alloying (Third Edition), 2020 Abstract. As was pointed out in the last two chapters, This review found that ball milling is the best tool for reducing the particle size of recycled metal chips and creating new metal powders to enhance mechanical Producing Metal Powder from Machining Chips Using Ball Milling
احصل على السعر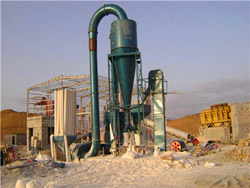
Electromagnetic Property Modulation of Flaky Ferromagnetic
After ball milling for 20 h, the alloy powders exhibited mainly α′ phase with a small amount of γ phase, which may be due to the small grain size or the residual stress generated during ball milling to stabilize the martensite phase . The whole ball-milling process caused the decay of the γ phase and the development/growth of the α′ phase.Ball milling is a mechanical technique widely used to grind powders into fine particles and blend materials. 18 Being an environmentally-friendly, cost-effective technique, it has found wide application in industry all over the Ball milling: a green technology for the
احصل على السعر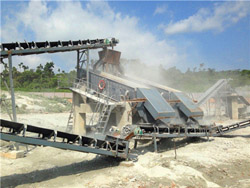
Effects of two-step high-energy ball milling process and hot
Commercial powders of magnesium were processed by high-energy ball milling (HEBM) using a two-stage composite process. The microstructural and morphological evolution of the powders was studied using scanning electron microscopy (SEM), energy-dispersive spectrometry (EDX), and X-ray diffraction (XRD). From the results obtained, it 2.1 Ball Milling. In this work, elemental powders of Al, Cu, Ti, Si, Mo, Co, Cr, Fe, Ni, V, W, and Ta (Alfa Aeser, India) having a particle size in the range of 10 to 150 μm with a minimum purity of 99 pct were subjected to high-energy ball milling.Ball milling was carried out using a Fritsch Pulverisette 5 planetary ball mill with tungsten carbide Effect of High-Energy Ball Milling in Toluene on the
احصل على السعر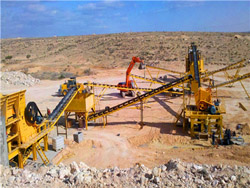
Mechanical Milling: A Superior Nanotechnological Tool for Fabrication
Fabrication of Al/SiC Nanocomposite Powders by Ball Milling . Due to the large thermal expansion coefficient difference between the two constituents, as well as the low wettability of molten Al metal (or Al alloys) and SiC, the traditional technique of liquid metallurgy, which is the least expensive method for composite fabrication, cannot beIn mechanical milling, powders of pure metals or intermetallic having homogeneous composition are milled in a ball mill whereas powders of different metals or alloys milled to produce amorphous powders is called as mechanical alloying (MA). Mechanical milling is mainly performed to reduce the grain size of the material to nanoscale.Nanomaterials through Powder Metallurgy: Production, Processing
احصل على السعر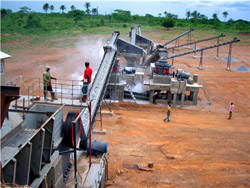
Advancing mechanochemical synthesis by combining milling
For example, ultrasound-assisted ball milling of Cu and Co powders gives face-centred cubic Cu–Co solid solutions within 5 h (9% Co incorporated) or 10 h (19% Co incorporated) of ultrasoundIn industry, it is well-known that high-energy ball milling is a simple, fast, and cost-effective green technology to produce micro- and submicron-sized powders. In the ball milling process, some process control agents (PCAs), such as solvent, surfactant, dispersant, and coupling agent, are usually added to reduce the occurrence of cold Microstructural Characteristics and Electrochemical
احصل على السعر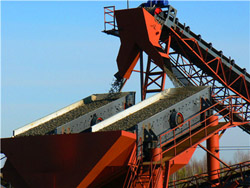
Particle morphology control of metal powder with
The effect of ball size on copper powder particle morphology in dry-type milling was studied using a planetary ball mill. Spherical copper powders were obtained by ball milling at a high rotation speed and with a ball diameter of 1 mm. The experimental results suggest that the particle size and morphology can be controlled by changing theThis study investigates the effect of using ethanol as the process control agent during the wet ball milling of niobium (Nb). Dried nanocrystal Nb powders, of high purity, with particle sizesWet ball milling of niobium by using ethanol, determination
احصل على السعر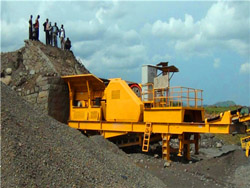
Nanomaterials Free Full-Text Mechanical
(a) STEM-BFI of WC nanocrystalline powders obtained after 20 h of the milling time and then ball milled with 7 wt. % (10Co/4Cr) powders for 50 h, using a high energy ball mill. The corresponding X-ray The temperature during ball milling is a critical parameter that impacts both the milling process and the quality of the resulting powders. Ball milling is commonly performed at ambient temperature or under cryogenic conditions [75,141,142]. The optimal milling temperature depends on several factors, including the material being milled, theProducing Metal Powder from Machining Chips Using Ball Milling
احصل على السعر
Parametric study on four station ball mill for synthesis of
A planetary type ball mill is economical, simple to operate, and ideally suited for small-quantity batch type synthesis of powders and alloys and for reactive processing of powders. The size of the jar and balls, rotational speed, milling duration, ball-to-powder ratio, jar material, milled material, and temperature are the most importantThe ball milling of commercial strontium hexaferrite powder for up to 42 h allows a particle size reduction down to 400 nm. Conventional PXRD indicates that the ball-milled samples were singleMagnetic properties of ball-milled SrFe12O19 particles
احصل على السعر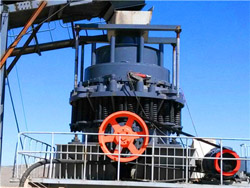
Materials Development Using High-Energy Ball Milling:
High-energy ball milling (HEBM) is a treatment of powders, which uses the action of the milling media to mix, disperse, activate and form composite structures [1–4]. The milling devices exist in various designs. Usually, they are divided into two groups: low-energy and high-energy mills [5]. The processes occurring during HEBM are deformation,The Inonotus obliquus fine grinding powders were prepared by pulverising the coarse powder with planetary ball mill for different time. The results showed that the yields of polysaccharides increased from 41.08 mg g −1 (coarse powder) to 319.62 mg g −1,and the yields of polyphenols were also increased fourfold in ball-milled powders asBall milling improves extractability and antioxidant
احصل على السعر
High-energy ball milling of WC-10Co: Effect of the milling
A Fritsch planetary ball milling machine, Pulverisette 7 Premium line has been utilized to mix the powders. WC-Co vials and balls were employed to avoid contamination. For each milling, the ball-to-powder ratio was kept constant at 4:1 and the milling time was set at 6 h (three separated steps of 2 h effective milling each) [62].Microstructure Characterizations of GO/CZC Composite Powder. Figure 2 shows the SEM images of GO/CZC powders after different ball milling times. The raw CZC powders in Fig. 2(a) exhibit spherical shapes with smooth surfaces. Some deformed CZC powders with relative rough surface were observed when the ball milling times increased Effects of Ball Milling Times on Microstructure and
احصل على السعر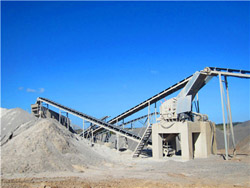
Effect of Ball-to-Powder Ratio on Morphology, Structure,
After ball milling, the powders with the size of 100-200 μm were screened out and selected as the research object for analyzing the morphology and flowability of the resultant powders. In this work, the morphology and cross section of both precursor powder and ball-milled powder were observed by FESEM (VEGAIIXMU, Tescan Company, High-energy ball milling was then performed in a Retsch Emax using stainless steel balls of 5 mm diameter and a vessel with a volume of 75 ml. The vessel was filled with a ball-to-powder ratio of 5:1 with milling carried out at 1000 rpm for 7 h, producing approximately 7.5 g of milled powder. XRD patterns of pristine powders correspondingHigh-energy ball milling of intermetallic Ti-Cu alloys for the
احصل على السعر