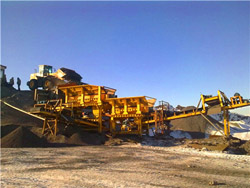
Rotary kiln process: An overview of physical mechanisms,
The heat and mass transport occurring through a rotary kiln has many industrial applications, such as organic or mineral materials manufacturing. The Abstract. Rotary kilns have been used successfully for many years to produce calcined coke for the aluminium industry and they offer a high level of automation, performance and Quality and Process Performance of Rotary Kilns and Shaft
احصل على السعر
Quality and Process Performance of Rotary Kilns and Shaft
This paper reports on the results of extensive work to explore the fundamental differences between TDS in shaft calciners and rotary kilns.Figure 1. Vertical shaft kiln. Rotary Kilns A rotary kiln, as shown diagramatically in Figure 2, is a long refractory-lined inclined tube slowly rotated to ensure the steady flow of solid material from the feeder KILNS thermopedia
احصل على السعر
The comparison between vertical shaft furnace and rotary kiln
Vertical shaft furnace for calcination is quite different from rotary kiln for calcination in the principle of calcination process, calcined coke quality, product Continuous kilns include belt- and conveyor-type, pusher-type, roller-hearth, rotary and tunnel kilns and are similar to a commercial baking oven—product Kilns 101 Understanding the Different Kiln Types Ceramic
احصل على السعر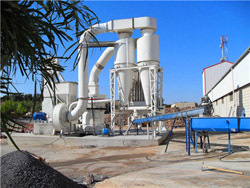
The comparison between vertical shaft furnace and rotary kiln
At present,the petroleum coke is mainly calcined by vertical shaft furnace or rotary kiln to meet the requirement of prebaked anode used for aluminium reduction in China.Vertical The rotary kiln is a slightly inclined steel cylinder that rests on supports (bearing rollers) with an interior lining; it is equipped with a rotating motor that induces a Rotary kiln process: An overview of physical mechanisms,
احصل على السعر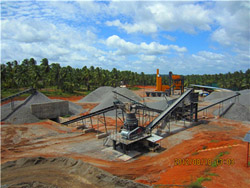
Rotary Kiln SpringerLink
The rotary kiln can be classified into cement kiln, metallurgical chemical kiln and lime kiln pursuant to different processed materials. Divided into dry-process and Vertical shaft kiln are indispensable tools in industrial processing, serving as the heart of various thermal processes. Two primary options often stand out regarding kilns: vertical shaft kiln (VSKs) and rotary kiln.Each type has unique advantages and disadvantages, making the selection a critical decision for industries ranging from cement Selection Guide on Vertical Shaft Kiln and Rotary Kiln
احصل على السعر
ROTARY KILN Plant Engineering Company Vietnam
The rotary kiln, which is a kind of heating furnace, is a cylindrical high efficiency rotary kiln. it is a steel rotating cylinder furnace in which refractory bricks are attached to inside. Difference between Kiln and Dryer. KILN. Sinter, burn, dry. Too much moisture is less efficient. Drying takes longer than a dryer. DRYER. LowThis inconsistency may be due to the differences in end-of-pipe treatment technologies adopted in the tested cement plant. Interestingly, the VOCs EFs offered by the US EPA was 0.09 g/kg-clinker (United States Environmental Protection Agency, 1995), which was between the EF values of the shaft kiln and rotary kiln tested in this study. ThisEmission characteristics and inventory of volatile
احصل على السعر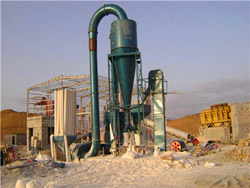
Rotary Kilns vs. Rotary Dryers: What’s the Difference?
Rotary dryers are used for drawing moisture out of a material. As such, they typically operate at temperatures between 800º 1400ºF. In contrast, rotary kilns are used to cause a chemical reaction or phase change, requiring them to operate at much higher temperatures, typically between 1000º 3000ºF. Some moisture reduction may Kilns are heated by horizontal space burners with gas, liquid, or solid fuel. A rotary kiln is a cylindrical steel tube lined with insulating brick. The large ones can be as long as 760 feet with a diameter of 25 feet. The kiln turns on a horizontal axis Furnaces and Kilns Visual Encyclopedia of Chemical
احصل على السعر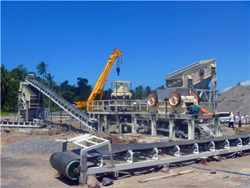
Quality and Process Performance of Rotary Kilns and
The differences in density between shaft calcined coke and rotary kiln coke are relatively small at low VM (9-10%) but increase as the green coke VM increases. Some high VM (>13.5%), fine particle size green cokes calcined in a rotary kiln can give mercury apparent densities as low as 1.67-1.70 g/cc. Such lowtogether with clay or shale are mixed and fed to a large rotary kiln at temperatures up to 1427°C (2600°F). The mix can be taken through several preheater and pre-calciner stages before being charged into the rotary kiln. Kilns are normally fired with pulverized coal or gas at one end. Raw materials are fed to the kiln at the back end, furthestCement, lime and gypsum manufacturing processes
احصل على السعر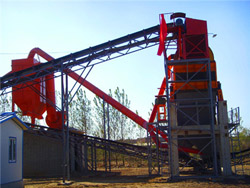
Differences between Vertical Lime Kiln and Rotary Lime Kiln
Comparison of the Two Designs. The main difference between the two designs is the method of limestone movement. In a vertical kiln, the limestone moves downwards due to gravity, while in a rotary kiln, the limestone moves due to the rotation of the kiln. This fundamental difference affects the way in which the heat is transferred to theRotary Kiln At the core of the sintering process, the kiln shell is a long cylinder made of steel, with a typical length ranging between 60-100 m and weighing around 1000t. Despite this impressive mass, the kiln shell is a giant with feet of clay, exposed to harsh environmental conditions. The inner partComparison of lime kiln types Blitzco
احصل على السعر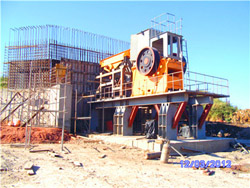
(PDF) STRESS STATE IN ROTARY KILN SUPPORT
Abstract. In the paper stress analysis of rotary kiln support rollers is conducted. Stress state in the support rollers is caused by temperature gradient, shrink-fit connection between shaft andThe rotary kiln is a slightly inclined steel cylinder that rests on supports (bearing rollers) with an interior lining; it is equipped with a rotating motor that induces a turning motion. Such a gas/solid contactor was invented in the cement industry at the beginning of the 19th century. The advent of the rotary kiln is closely tied to theRotary kiln process: An overview of physical mechanisms,
احصل على السعر
Thermal Desulfurization of Petroleum Coke for Anode
Petroleum Coke, Anodes, Shaft Calcining, Sulphur, Desulfurization. 1. Introduction. Thermal desulfurization (TDS) of petroleum coke is a well-studied phenomenon and a recent paper discussed the differences between TDS in a rotary kiln and a shaft calciner [1]. The heat-up rate in a rotary kiln calciner is much higher (~50. oThe reduction process inside the ore pre-reduction rotary kiln involves a series of physicochemical reactions, and in-depth understanding of the reduction behavior is helpful to improve the product quality and productivity. This paper reports a three-dimensional steady state mathematical model based on computational fluid dynamics, Metals Free Full-Text Numerical Analysis on Characteristics of
احصل على السعر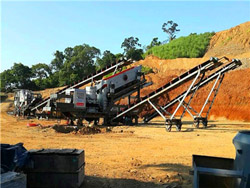
CONTRIBUTIONS TO THE TECHNOLOGY COMPARISON
between 6 and 10cm in height, whereas the green pellet height is typically between 30 to 45cm. In the grate-kiln system, the bed height is 12 to 23 cm on the preheat grate and 60 to 100 cm on the cooler. The tumbling charge in the rotary kiln does not contribute significantly to the overall pressure drop of the system.5 Modern plants use vibratory conveyors to transport the CPC on to conveyor belts leading to storage. 2.3. Differences between shaft and rotary kiln calcining technologiesCB01 Petroleum coke shaft calcining technology final
احصل على السعر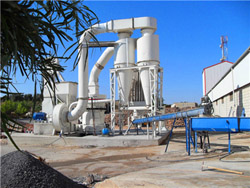
Rotary kiln handbook_new PDF SlideShare
3. THE ROTARY KILN HANDBOOK FEECO International was founded in 1951 as an engineering and equipment manufacturer. We quickly became known as the material experts, able to solve all sorts of material processing and handling problems, and now serve nearly every industry, from energy and agriculture, to mining and minerals.The differences between rotary kiln and shaft calciners have been described previously [7]. Rain Carbon operated a small 20 kt/yr shaft calciner in China from 2009-2015.Quality and Process Performance of Rotary Kilns and Shaft
احصل على السعر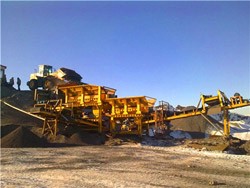
Kiln vs flash calciner FLSmidth
The rotary kiln system is well suited for converting larger particle sizes and the integration of the cyclone preheater greatly improves specific energy consumption over just a straight kiln. It also reduces the size of the kiln and makes treatment of off gases very simple because the heat is removed prior to treatment.
احصل على السعر