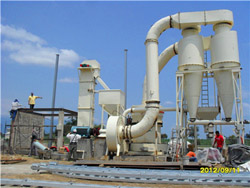
A new approach for recovering iron from iron ore tailings
Iron ore tailing Suspension magnetization roasting Iron recovery Magnetic conversion rate Phase transformation 1. Introduction In recent years, with the rapid Abstract: Conventional magnetic separation devices are widely used for the removal of tramp iron from a variety of feed materials and for the beneficiation of ferrous ores. Magnetic separation: A review of principles, devices, and applications
احصل على السعر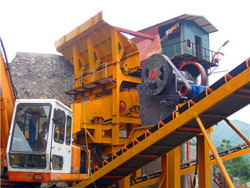
Improved iron recovery from low-grade iron ore by efficient
In this study, to improve iron recovery from low-grade iron ores, preconcentration was performed, followed by two separation processes, namely, reverse While magnetite ores are naturally suitable for magnetic separation, oxidized iron ores are much more difficult to recover using magnetic separation due to Physical separation of iron ore: magnetic separation
احصل على السعر
Metallurgical Testing for Iron Ore SGS
Other gravity separation equipment, such as shaking tables, Falcon and Knelson centrifugal separators, Mozley MGS units, and hydrosizers, are also available. • of magnetic separation equipment; preventing medium (mechanical) blockage; reducing magnetic inclusion and blockage; improving (magnetic) capture power and separation Journal of Physics: Conference Series PAPER OPEN
احصل على السعر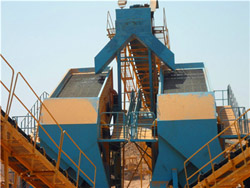
Developments in the physical separation of iron ore: magnetic
This chapter introduces the principle of how low-grade iron ores are upgraded to high-quality iron ore concentrates by magnetic separation. Magnetite is the This chapter introduces the principle of how low-grade iron ores are upgraded to high quality iron ore concentrates by magnetic separation. Magnetite is the Physical separation of iron ore: magnetic separation
احصل على السعر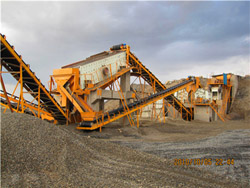
Separation and Recovery of Iron from Low-Grade Refractory Iron Ore
The low-grade iron ore fines contain weakly magnetic iron minerals such as hematite and siderite, which could not be separated effectively by low-intensity magnetic 2.4. Beneficiation methods. Beneficiation is a process where ore is reduced in size and valuable minerals are separated from the gangue minerals. Separation of valuable minerals from gangue minerals can be efficiently achieved by taking advantage of the differences in physical, surface, and magnetic properties.Iron ore beneficiation: an overview ScienceDirect
احصل على السعر
Beneficiation of Magnetically Separated Iron
Rough processing of iron ore employs dry methods which means that equipment is tuned to process large particles, but fine magnetic material less than a few tenths of a millimeter in size is not separated as SLon Magnetic Separator Co., Ltd. SLon is a state-controlled enterprise with high tech in the field of mineral processing industry, which integrates research, production and sales of magnetic SLon Magnetic Separator Co., Ltd.
احصل على السعر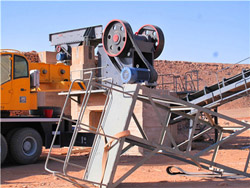
Fluidized magnetization roasting of refractory siderite-containing iron
Magnetization roasting is one of the most effective way of utilizing low-grade refractory iron ore. However, the reduction roasting of siderite (FeCO3) generates weakly magnetic wüstite, thus reducing iron recovery via weak magnetic separation. We systematically studied and proposed the fluidized preoxidation-low-temperature reduction The process stages are detailed, providing information on some characteristics of the magnetic separation equipment. The plant capacity is estimated based on technical and economic criteria. The 62% purity iron ore benchmark proposed to China was, on average, USD 121.50 per ton in 2014, according to a Reuters poll of 14 analysts Magnetic Separation and Enrichment of Fe–Ti Oxides from Iron
احصل على السعر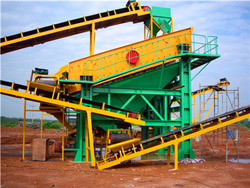
Magnetic Fluid Separation SpringerLink
Magnetic fluid separation is a separation method that takes magnetic fluid as the separating medium and makes different minerals suspended in layers in the magnetoelectric field and gravity field in accordance with their magnetic intensity (or electric property contrast) and density under the action of an external magnetic field, Iron ore tailings, which are important secondary resources, have outstanding latent application value in iron recovery. In this study, a pilot-scale experiment on the iron recovery from iron ore tailings was investigated using innovative technology of pre-concentration and suspension magnetization roasting (SMR), followed by magnetic A new approach for recovering iron from iron ore tailings
احصل على السعر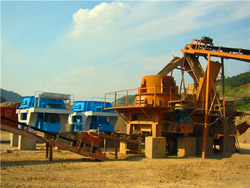
Magnetic Separation SpringerLink
In mineral processing, magnetic separation is usually employed for three purposes: Ejection of iron and other similar materials present in the p stream to protect equipment against wear or damage, Separation of valuable magnetic minerals, Removal of magnetic impurities [ 12, 13 ].*Corresponding author: morkunv@gmail Increasing efficiency of iron ore magnetic separation by using ultrasonic technologies Vladimir Morkun1,*, Natalia Morkun1, Vitalii Tron1, Vladimir Golik 2, and Arkadii Davidkovich3 1Kryvyi Rih National University, Automation, Computer Science and Technology Department, 11 Vitalii Matusevich Str., Increasing efficiency of iron ore magnetic separation by
احصل على السعر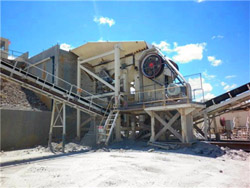
Comminution and classification technologies of iron ore
Most of the high-grade hematite iron ores are typically subjected to simple dry processes of crushing and classification to meet the size specifications required for direct shipping ore (DSO). This involves multistages of crushing and screening to obtain lump (−31.5 + 6.3 mm) and fines (approximately −6.3 mm) products.Other gravity separation equipment, such as shaking tables, Falcon and Knelson centrifugal separators, Mozley MGS units, and hydrosizers, are also available. • Magnetic and Electrostatic Separation A full range of magnetic separators is available for iron ore testing, from low intensity drum separators to high gradient/high intensity Metallurgical Testing for Iron Ore SGS
احصل على السعر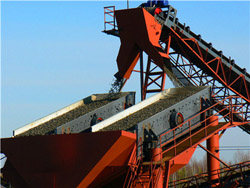
Minerals Free Full-Text Parameter Optimization
Iron is a common ferrous metal that has wide application in various fields, including metallurgy, chemical industry, and the manufacture of mechanical equipment [1,2].Hematite (α-Fe 2 O 3), an iron mineral Oolitic hematite is an iron ore resource with complex refractory characteristics, abundant reserves, and significant recycling value. Various magnetization roasting technologies and types of equipment, such as shaft furnace roasting, rotary kiln A study of microwave reductive roasting followed by magnetic separation for a metallic ironRecycling iron from oolitic hematite via microwave
احصل على السعر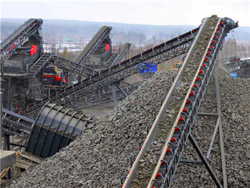
Performance assessment of an innovative precise low-intensity magnetic
1. Introduction. Iron ore resources are a significant material basis for the development of the steel industry. Currently, global steel production is predominantly supported by iron ore sources such as high-grade hematite, goethite, and magnetite (Fe 3 O 4) deposits (Han et al., 2021, Xue et al., 2022).Although magnetite contains the highest 17 小时之前1. Single Magnetite: Most of the iron minerals in a single magnetite ore are magnetite.The ore composition is simple, and the weak magnetic separation process is often used:. When the grinding particle size is more than 0.2mm, most iron ore magnetic separation plants often adopt a one-stage grinding magnetic separation process;; Magnetite Beneficiation, Equipment Mineral Processing
احصل على السعر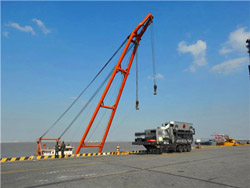
Types of Mining Magnetic Separators Mineral Processing
Mining magnetic separator is common equipment in mineral processing. And magnetic separation is the main method of iron ore dressing. What minerals are required for magnetic separation? Common Iron Minerals are magnetite (strong magnetic minerals), hematite (weak magnetic minerals), Limonite, specularite, siderite (all weak VPHGMS equipment is commercially available in capacities ranging from 10 to 1000 m 3 /h iron ore slurry input and is, Developments in the physical separation of iron ore: magnetic separation. Iron Ore Mineral. Process. Environ. Sustain. (2015), pp. 283-307, 10.1016/B978-1-78242-156-6.00009-5.Pilot-scale magnetic recovery of vivianite from
احصل على السعر
Home [slonmagnetics]
SLon provides high intensity (1.8T) VPHGMS and coarse particle VPHGMS which could process 2-5mm large particle materials. SLon offer magnetic separation solution for many minerals and applications. Compared to HGMS+reverse flotation, the new technology HGMS+Centrifuge is much cheaper and environmentally friendly.This separation process produced a concentrate containing 56.20% Fe and 1.79% Mn with iron and manganese recoveries of 56.83% and 66.73%, respectively. A magnetic separation test from an unleached ore sample was also carried out as a benchmark. To the best of our knowledge, this is the first time that a magnetic separation Separation of Fe and Mn from Manganiferous Iron Ores via
احصل على السعر