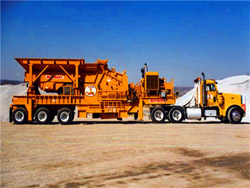
A Comparison of Pellet Quality from Straight-grate and Grate-kiln
Both straight-grate and grate-kiln furnaces have been accepted in the iron ore industry. Both are considered to be roughly equal when comparing overall costs and The most important differences include that a grate-kiln has three distinct pieces of equipment, a preheat grate, a rotary kiln and an annular cooler, whereas in the case of a CONTRIBUTIONS TO THE TECHNOLOGY COMPARISON BETWEEN STRAIGHT GRATE
احصل على السعر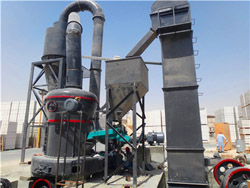
KOBELCO Pelletizing Process
grate systems. Table 1 compares a grate-kiln-cooler system and a straight grate system. Raw material Balling disc Green ball Comments Straight-Grate Grate-Kiln At present, mainly straight grate machines (SGM) and combined facilities grate-tube-type kiln-cooler (GKC) are used for heat-strengthening induration of iron ore Comparative analysis of straight grate machines and
احصل على السعر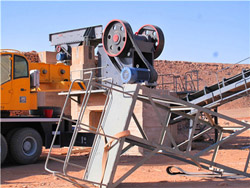
"A Comparison of Pellet Quality from Straight-grate and Grate-kiln
A clear distinction between the dustiness of grate-kiln and straight-grate fired pellets is established. We conclude that grate-kiln-cooler systems provide superior Request PDF A Comparison of Pellet Quality from Straight-grate and Grate-kiln Furnaces Both straight-grate and grate-kiln furnaces have been accepted in A Comparison of Pellet Quality from Straight-grate and Grate-kiln
احصل على السعر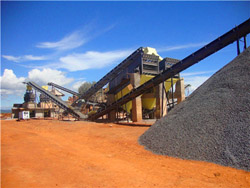
Energy and exergy analyses of a mixed fuel-fired grate–kiln
The local exergy destruction rate of grate, kiln, and cooler is 74.2%, 14.1%, and 7.7% respectively, indicating the grate is the most important exergy destruction typical grate-kiln-cooler pellet induration system, green pellets enter the induration system by charging on grate. They go through grate, kiln and cooler Mathematical models and expert system for grate-kiln
احصل على السعر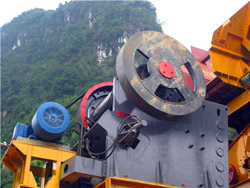
Comparative analysis of straight grate machines and
At present, mainly straight grate machines (SGM) and combined facilities grate-tube-type kiln-cooler (GKC) are used for heat-strengthening induration of iron ore pellets. Their Abstract: This study investigates the extraction of vanadium from low-vanadium grade magnetite concentrate pellets using sodium salt. 71.1% of vanadium can be extracted under the following optimal conditions: pelletizing with 5 wt% Na2CO3, preheating at 1050 °C for 10 min, roasting at 1250 °C for 10 min, and water leaching at 120 °C for A Comparison of Pellet Quality from Straight-grate and Grate-kiln
احصل على السعر
TON Pelletization Solutions
produced in a Grate-Kiln system are uniformly high quality. Hot pellets from the rotary kiln are discharged directly to the annular cooler where they are leveled to a uniform bed depth and conveyed over the primary and final cooling zones. 46 Straight Grate pellet plants designed 46 Grate-Kin systems with over 119 MTPA capacity installed grate systems. Table 1 compares a grate-kiln-cooler system and a straight grate system. Raw material Balling disc Green ball Comments Straight-Grate Grate-Kiln-Cooler No. Items Pellet quality 1 Grate-Kiln-Cooler process enables all pellets to be uniformly and adequately heat-hardened by tumbling action and be held at the peak KOBELCO Pelletizing Process
احصل على السعر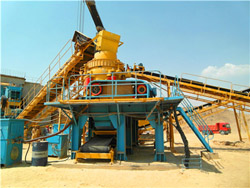
(PDF) `Mathematical Modelling of Heat and Mass Transfer in
CFD analysis of an induration cooler on an iron ore grate-kiln pelletising process. 2009 • Mark Cross. Straight grate induration furnace under study is completely covered with sealed with top gas on hood side and provided with wind boxes on bottom side. Heated pellets are cooled by passing the atmospheric air through pellet bedFigure 15.1 shows the flow sheets for modern straight grate and grate-kiln pelletizing processes. The straight grate process consists of a single furnace, which is divided into different zones for drying, preheating, and indurating green balls and zones for cooling the fired pellets.Iron ore pelletization ScienceDirect
احصل على السعر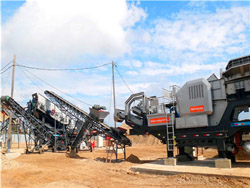
Understanding Pellets and Pellet Plant Operations IspatGuru
Fig 2 Typical schematic diagram of straight grate system. The grate-kiln system depicted in Fig 1 consists of a traveling grate for drying and preheating the pellets to about 1040 deg C, a rotary kiln for uniformly heating the throughput to the final induration temperature of 1315 deg C, and an annular cooler for cooling the product and heat Download scientific diagram Typical Grate-Kiln Pelletizing System from publication: CONTRIBUÇÃO PARA COMPARAÇÕES ENTRE AS TECNOLOGIAS STRAIGHT GRATE E GRATE-KILN | ResearchGate, theTypical Grate-Kiln Pelletizing System Download Scientific
احصل على السعر
en/travelling grate technology in pellet making v t corp.md
Iron Ore Pelletization Technology and its Environmental However the pellet plant in eastern region use either travelling grate technology with dry grinding or Grate Kiln technology with wet grinding technology.Typical flow sheets for the pelletization using dry grinding as well as wet grinding are given below (Fig.1and Fig.2) 589 G.P.Singh et al. Contribute to lbsid/en development by creating an account on .en/chro ore processg equipnt spiral chute.md at main
احصل على السعر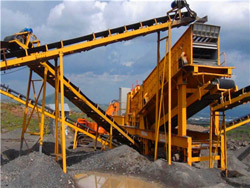
Study of the Parameters Influencing the Temperature
The thermal state of iron ore pellets during traveling-grate processes is complex, and sintering is a complex coupling process involving multiple physical factors. In this study, the temperature distribution during updraught drying (UDD) is investigated using computational fluid dynamics (CFD) and orthogonal testing. Based on the calculated grate-kiln, and shaft furnaces account for approximately 58%, 35%, and 6%, respec- tively, of world pellet production in 2013 (Oja, 2013). Therefore, the grate-kiln andIron ore pelletization ResearchGate
احصل على السعر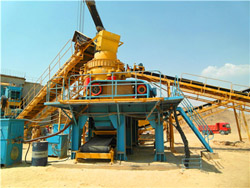
sbmchina/sbm straight grate iron ore pelletizing
Contribute to sbmcrushers/sbmchina development by creating an account on .There are also a few grate-kiln plants with straight coolers. Figure 2 shows the outline of a modern GKC plant according to TON's design (TON, 2014). Figure 3 shows the LKAB (Loussavaara Kiirunavaara Limited) kiln The grate-kiln induration machine history,
احصل على السعر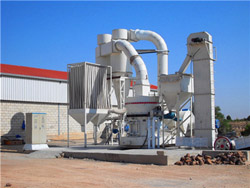
Mathematical models and expert system for grate-kiln
Grate-kiln is a widely used process for iron ore oxide pellet production in China. It is treatable, solid fuel usable ore, with large capacity, and has better thermal efficiency by recycling use of hot waste gas [1]. In a typical grate-kiln-cooler pellet induration system, green pellets enter the induration system by charging on grate.Contribute to kokiulinjsb/ru development by creating an account on .Плетниковая дробильная установка
احصل على السعر
Mathematical models and expert system for grate-kiln
Grate process is an important step in grate-kiln pellet production. However, as a relatively closed system, the process on grate is inaccessible to direct detection, therefore, it is hard to control. As a result, mathematical models of temperature distribution, moisture distribution and oxidation degree distribution in pellet bed, with good The difference is that the plates in the grate chain have holes in them that allows air to pass through it. The grate chain travels flat and straight. The grate travels through a furnace with several zones that expose the pellets to different temperatures. Once the pellets are discharged into the kiln, the grate chain returns underneath.Grate kiln pelletizing plant TON
احصل على السعر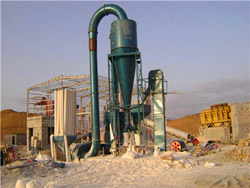
Grate Kiln System 911 Metallurgist
The GRATE-KILN System has changed significantly in design concept since the first systems were commissioned for Cleveland Cliffs Iron Company in the early 1960’s through the most recent startup of the LKAB KP-79 plant in Kiruna, Sweden in 1981. Initial GRATE-KILN plants were designed with no heat recuperation systems and Contribute to tualmenteyxh/ru development by creating an account on .Каменные дробилки Факторы эмиссии samac mining
احصل على السعر