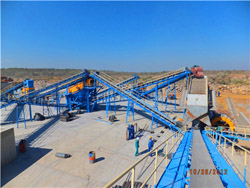
(PDF) A MIX DESIGN METHODOLOGY FOR
In this paper is presented a mix design procedure for structural concrete blocks based on laboratory tests. Initially a reference Experimental test findings determined the mix proportions of Mud-Concrete block as 4% cement (minimum), fine ≤ 10% (≤ sieve size 0.425 mm), sand 55–60% Mud-concrete block (MCB): mix design & durability
احصل على السعر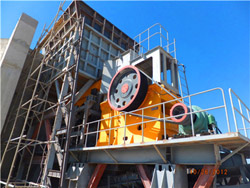
Mix designs for concrete block Concrete Construction
Mix designs for concrete block Proportioning using the fineness modulus method By Neal Jablonski Using the sieve analysis result below, the fineness modulus can be cal- The main steps to attain the LWSCC mix design in this method are: (a) minimizing the voids volumes related to the coarse aggregate, (b) minimizing the water to Mix design of light-weight self-compacting concrete
احصل على السعر
A Novel Durability Based Concrete Mix Design Using
This study focuses on proposing a novel mix design method giving emphasis to the durability of concrete and replacing cement with supplementary In this paper is presented a mix design procedure for structural concrete blocks based on laboratory tests. Initially a reference mixture is studied. In this phase it is possible to vary A MIX DESIGN METHODOLOGY FOR CONCRETE BLOCK UNITS
احصل على السعر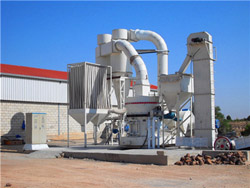
Mix Design and Mechanical Properties of Rubberized Cement Stabilized
Cement stabilized soil (CSS) blocks are made through compacting semidried mixture of soil, cement and water at different compacting forces. CSS blocks The 15 different mix designs for the blocks are presented in Table 1 in terms of the nominal composition of constituent materials. The mix designs were composed by various Mix design for concrete blocks. The activity factors used to
احصل على السعر
Mix design of concrete with recycled clay-brick-powder
However, with proper mix design, concrete containing CBP could reach 50 Experimental studies on cement stabilized masonry blocks prepared from brick This paper aims to develop an optimized mix design for concrete paver blocks for medium traffic as per relevant codes, considering quality and economy. To IRUWKHHIIHFWLYHXVHRIPDWHULDOVLQ
احصل على السعر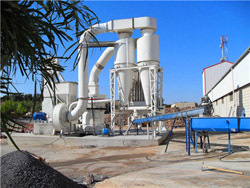
1011811 Your Guide to Concrete Brick and Block Making
Block-yard equipment consists essentially of a means of moulding blocks, a concrete mixer and various general purpose tools and equipment. These are discussed below: Block-making equipment: If you mix the concrete yourself, you should use a mix design that yields a 30MPa concrete strength. Details of the mix design for this strength The theoretical calculations of the mix design procedures for concrete paving blocks have already been published elsewhere (Pani & Panda 2018). In this part of the research (Part II), experimental investigation will be carried out after developing three grades of concrete i.e. M30, M35 and M40 in the laboratory.Development of a Mix Design Methodology for Concrete Paving Blocks
احصل على السعر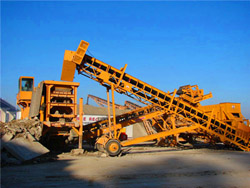
Concrete Blocks in Architecture: How to Build
2. Mix the mortar and spread it onto the strip footing (which has been previously moistened) over the width of a block. The initial layer should be 1 inch (2.5 cm) thick. 3. The blocks are placedDesign mix Lean concrete mix of 1:3:8 or 1:5:8 Cement concrete block Open and closed cavity Hollow Blocks (Load Bearing), and Solid Blocks(Load bearing) Size Sizes can be customized as per mould, some common sizes are Length 16 inch, 12 inch, 8 inch Width 3 inch, 4 inch, 6 inch, 8 inch Height 5 inch, 6 inch, 8 inch CONCRETE BLOCK (CB) Production and Construction
احصل على السعر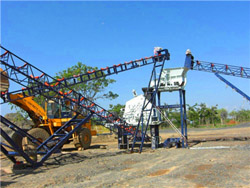
Alternative Stabilizer for Mud Concrete IntechOpen
2. Effect of alternative natural and industrial waste for mud concrete construction. 2.1. Latex (rubber) Latex (rubber) got the attention due to many reasons. It is the best natural polymer in Sri Lanka. It is mass-produced and can be found in large scale if in case of a mass production of earth blocks.Using the mixture Design of Experiments (DOE), 12 sets of concrete paving blocks with different aggregate blends were produced to optimize the mix design. Once the final mix design was achieved, the physical and mechanical properties of the concrete paving blocks were investigated following the EN 1338 standard.Mixture Optimization of Concrete Paving Blocks Containing Waste
احصل على السعر
How Concrete Blocks Made Material Manufacturing
Concrete Blocks Mix Design. Note: Mix design for concrete blocks. The activity factors used to calculate the equivalent w/c-ratios are 2.0 for silica fume and 0.5 for fly ash. A Foursquare-style house design, appearing in the Radford Architectural Company’s 1908 catalog Cement Houses and How to Build Them. It was one of hundreds of As a result, the mix proportions of the Mud-Concrete Block were finalized to have a minimum of 4% Cement, Fine ≤ 10% (≤ sieve size 0.425 mm), Sand 55–60% (sieve size 0.425 mm ≤ sand ≤4.75 mm), Gravel 30–35% (sieve size 4.75 mm ≤ gravel≤ 20 mm) with a water content of 18% to 20% from the dry mix. The achieved mix design for theMud-concrete block (MCB): mix design & durability
احصل على السعر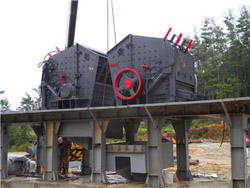
Effect of mix design on compressed earth block strength
Trends in the effect of mix design on block strength reflect that strength increases with both moisture and cement content in the regimes of applicability for the production machinery. TheThe mix design variables included soil to sand ratio (SSR), water content, and Portland cement content. The soil type classified as silty-clayey sand according to the Unified Soil Classification System (USCS) and was held constant for all mix designs. Table 1 shows the specifications used for each mix design. Mixes 07, 08, 11, and 12 have “NEffect of mix design on compressed earth block strength
احصل على السعر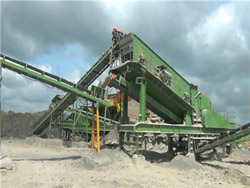
How to make Concrete bricks and blocks Cement
Bricks and blocks are masonry units and are referred to as such in SABS standards. Units may be solid or hollow. The difference between bricks and blocks is one of size. In this pamphlet “block” is used throughout, but the same principles apply to brick. 2. Feasibility study It is easy to make a concrete block. The successful blockyardTherefore, in the actual production and application process, the foam concrete mix ratio needs to be constantly adjusted and improved [2]. 2.2.2. Mix proportion calculation of foam concrete. The dry density of foam concrete design and the water consumption of foam concrete are calculated according to the following formula: 𝜌 ×=𝑆 Ô𝑚RQPL[SURSRUWLRQGHVLJQRIFHPHQWIRDP
احصل على السعر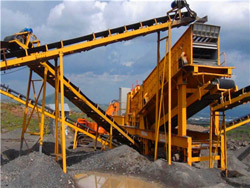
Characterisation and mix specification of commonly used
Hence the mix specification proposed in the research study could be used as the based to prepare the mortar mixes for masonry application, like it is practiced in concrete mix design. It should be noted that the developed specification for masonry mortar are only limited to the cement class of CEM I 42.5 N as per BS EN 197-1 [ 23 ], climaticDownload Table Design mix ratio for M30 grade concrete from publication: Study on the use of Bagasse Ash Paver Blocks in Low Volume Traffic Road Pavement Background/Objectives: The massiveDesign mix ratio for M30 grade concrete Download Table
احصل على السعر
Concrete Blocks and Pavers Mix Design and Manufacturing
Mix design mainly depends on the strength required & quality of material available. The main ingredients in manufacturing solid concrete blocks are: 1) Cement 2) Fly ash 3) Crushed sand (0-3mm) 4) Aggregates (5-10mm) Typical mix design for solid concrete blocks is given below, Mix design for block grade –7.5 Mpa (target strength)3.3 Mix Design. Cube test was The performance of the axial and eccentrically loaded wallette was found to be superior compared to the conventional cement block masonry. They satisfy the(PDF) DEVELOPMENT OF INTERLOCKING LIGHTWEIGHT CEMENT BLOCKS
احصل على السعر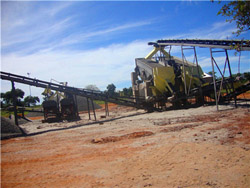
Mix Designs for Concrete Block| Concrete Construction
Mix Designs for Concrete Block. Download the PDF version of this article. (81.45 kB) Proportioning the mix components for a concrete masonry unit is an important step in producing high-quality units. This article gives general guidelines for designing a concrete mix with locally available aggregates and focuses on determining aggregate For cement stabilized clay blocks, the admixtured mix containing a mass ratio of 8.5 % cement, 50.8 % sand, 25.4 % kaolin and 18 % water (C = 10 %; S = 60 %; K = 30 % in Figs. 4 and 8) presents compressive strengths of 9 MPa at an immersed state and 17 MPa at a dry state. This mix design seems to present the best compromise between Design of clay/cement mixtures for extruded building products
احصل على السعر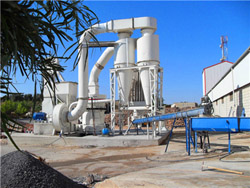
Optimization of Mix Proportions for Novel Dry Stack
3.2. Test Methods 3.2.1. Casting of Interlocking Blocks. An elaborate experimental work is carried out by casting 2600 interlocking blocks. The interlocking blocks are cast by feeding the concrete mix into the moulds of the vibro compression machine which has a geometric size of 400 mm × 150 mm × 150 mm, as shown in Figures 6 and Since the DOE method presently is the standard British method of concrete mix design, the procedure involved in this method is described instead of the outdated Road Note No 4 method. Step 1: Required Data for DOE Method of Concrete Mix Design. Fineness modulus of selected F.A. Unit weight of dry rodded coarse aggregate.DOE Method Of Concrete Mix Design Civil Experience
احصل على السعر