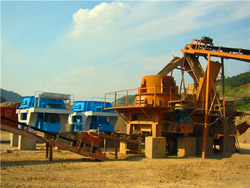
Grinding process within vertical roller mills: experiment and
Four grinding circuits are used with different materials: vertical mills (Loesche) for coal and cement feed; vertical roller mills for cement clinkers; and ball mills Vertical grinding is an indispensable key equipment for cement industry grinding system, the performance of the vertical mill depends on the design of its internal Solid Edge’s Application in Vertical Mill Design Springer
احصل على السعر
TON Vertimills
In a nutshell, TON Vertimills® ofer the most optimum equipment solution for the circuit. The Vertimill® is capable of handling feed sizes up to 6 mm and grinding to The modular vertical roller mill for grinding cement raw material, cement clinker, and additives with an installed power of up to 12,000 kW was specifically Grinding process optimization IEEE Xplore
احصل على السعر
LM Vertical Grinding Mill-TY Industrial
LM Vertical Grinding Mill integrates crushing, drying, grinding, separating and transport. The structure is simple while the layout is compact. Its occupational area is about 50% of that of the ball-milling Vertical roller mills (VRM) have found applications mostly in cement grinding operations where they were used in raw meal and finish grinding stages and in power Operational parameters affecting the vertical roller mill
احصل على السعر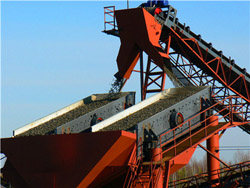
Review on vertical roller mill in cement industry & its
With the grinding capacity of a vertical roller mill and the ability to dry, grind and sort in a single unit, the vertical roller mill offers a definite advantage over the ball Grinding balls are an indispensable grinding medium in vertical grinding mills, grinding ore powder to target size. Some were severely worn and unrounded by Predicting the effect of operating and design variables in grinding
احصل على السعر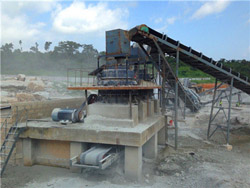
Vertical roller mills: The new leader in grinding
The two most common compressive comminution technologies are the high pressure grinding roller (HPGR) and the vertical-roller-mill (VRM). For now, the HPGR has already presented in a This work concentrates on the energy consumption and grinding energy efficiency of a laboratory vertical roller mill (VRM) under various operating parameters. For design of experiments (DOE), the response surface method (RSM) was employed with the VRM experiments to systematically investigate the influence of operating parameters on Analysis and Optimization of Grinding Performance of Vertical
احصل على السعر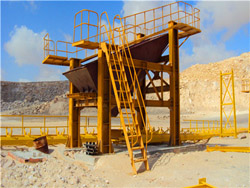
An investigation of performance characteristics
Vertical Coal Mill (VCM) is equipment for grinding and pulverizing coal into micron size. Rotary kilns then use the powders as fuel burners. The VCM has a housing section equipped with a liningThe HIGmill™ comprises a mill body, shaft with grinding rotors, shell mounted stator rings, gearbox, and drive. The grinding chamber is filled up to 70% with inert ceramic grinding media beads. Rotors stir the charge and grinding takes place between beads by attrition. The number of rotors (grinding stages) depends on the application and Stirred mills TON
احصل على السعر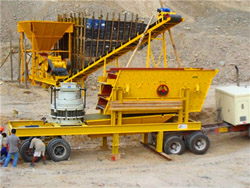
Polygonal concave wear and irregular packing behavior of grinding
Vertical grinding mills are widely used in ore crushing and cement industries for processing industrial powders (Radziszewski, 2013, Mazzinghy et al., 2017, Breitung-Faes and Kwade, 2019, de Oliveira et al., 2021). The equipment contents generally include materials to be processed, grinding balls and water.1. The temperature of the slurry at the pre -scattered stage is not high, but once the horizontal sand mill began, the temperature of the slurry in the grinding cavity exceeds the protection temperature, so that the sand mill was stopped. In the case, we can appropriately increase the speed of the feed pump, thereby shortening the stay of the How to choose the right vertical sand mill & horizontal sand mill?
احصل على السعر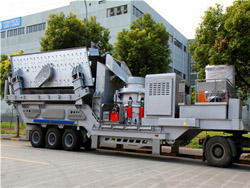
LM1100 Vertical Roller Mill Grinding Mill Equipment for Sale
GK vertical roller mill is with advantages of high grinding efficiency, low power consumption, big feeding size, product fineness easy to adjust, simple processing, small land occupation, low noise, small dust, easy maintenance, low operation cost, less wear-resistant materials.Abstract: As a world-wide leader in grinding solutions for the cement industry and understanding the changing needs of cement producers and how to tailor solutions to meet those needs. Optimizing output, improving efficiency, and reducing CO2 emissions while keeping investment costs to a minimum are common challenges that the Grinding process optimization IEEE Xplore
احصل على السعر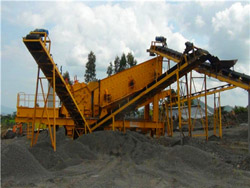
Vertical Mill Mining, Crushing, Grinding, Beneficiation
Vertical mills grind material through grinding between grinding rollers and material bed with 40%-50% less power consumption comparing with ball mill, Land occupation and construction area can be 50% less comparing with ball mill system reducing construction cost by about 70%. 3. Simple and stable operation.The advantages of the vertical roller mill include a high level of grinding efficiency combined with reduced energy consumption. For raw materials and cement clinker, the vertical roller mill is an excellent grinding solution because of the relatively lower cost of installation, ease of operation and maintenance, energy efficiency and productVertical Roller Mills FLSmidth
احصل على السعر
Difference between cement vertical mill and ball mill
Compared with the ball mill, the vertical mill can save 30% -40% of energy consumption, and has low vibration, which is a low energy consumption. Energy Saving and Noise Reduction When the vertical mill is in operation, the grinding roller does not directly contact the grinding disc, and the vibration is small, the noise is low, and the The present work applies the mechanistic mill model approach originally developed for ball mills by the UFRJ research group to the description of batch grinding in a pilot-scale vertical stirred mill. The model is used in its original form (Carvalho and Tavares, 2013) and predictions are compared to grinding of two materials at differentMechanistic modeling and simulation of a batch vertical stirred mill
احصل على السعر
Advantages and disadvantages of vertical roller mill
Vertical roller mill (vertical grinding mill) is mainly suitable for ultra-fine powder processing of non-inflammable and non-explosive brittle materials with medium and low hardness and Moh’s hardness of 6. The main disadvantages of vertical roller mills are: (1) Since the finished product is sent by the wind, the composition of the finished product composition Vertical Stirred Mill (VRMTM) have a scaleup of factor of 1:1 when applied to test work (Larson M 2011, Paz 2019, Paz 2021, Harbort 2016, Gurnett 2019). The reason that the scaleup is 1:1 is that the same feed size and media size distribution is utilised in a miniature scaled mill. The vertical gravity induced mill is sized based on BondRECENT DEVELOPMENTS IN COARSE GRINDING USING
احصل على السعر
Roller mills: Precisely reducing particle size with greater
microns. The roller mill’s ability to reduce materials to a uniform particle size provides more control of product characteristics and minimizes waste, as shown in Figure 1. The mill’s controlled reduction action requires less energy than other grinding methods, improving production effi-ciency and saving energy dollars.Unique Flute Geometry and Wide Land on the Cutting Edge Tough Cutting Edge Extremely High Milling Speed ・The “One-Pass” Grinding Guarantees Excellent Surface Even on the Perpendicular Wall ・Vertical MC(BT40) Conditions 0 50 100 150 0 10 20 30 Cutting length(m) Wear in R (μm) Competitor A Cutting Length Only 5m End Mill Training Nachi America
احصل على السعر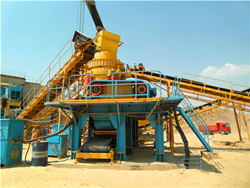
Performance Comparison of the Vertical and Horizontal
The mill also has vertical arrangement. VXP Mill is a product of FLSmidth company and is vertically oriented stirred media mill. The mill is often used in flotation concentrate regrind and precious metals tailings retreatment where the feed size is typically 200 m [11,12]. HIG Mill is a recently developed technology by TON-Outotech company.A cement Vertical Roller Mill modeling based on the number of breakages. Vertical roller mills (VRM) are widely used to grind, dry, and select powders from various materials in the cement, electric power, metallurgical, chemical, and nonmetallic ore industries. For the sectors above, the VRM is a powerful and energy-intensive grinding Operational parameters affecting the vertical roller mill
احصل على السعر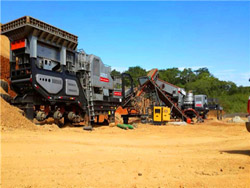
land vertical grinding mill
The power ingesting of a grinding process is 50-60% in the cement production power consumption. The Vertical Roller Mill (VRM) reduces the power consumption for cement grinding approximately 30-40% associated with other grinding mills. The process variables in cement grinding process using VRM are strongly nonlinear and
احصل على السعر