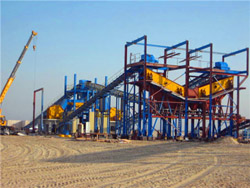
Flotation data for the design of process plants Part 1 AusIMM
Practical design considerations such as flotation time, type, number and size of flotation cells, and the means of froth transport are all important and appropriate test work can Flotation cells. Maintaining recovery and ensuring availability and sustainability while keeping costs under control is challenging. Our flotation solutions maximize your return on investment by enabling gains Flotation TON
احصل على السعر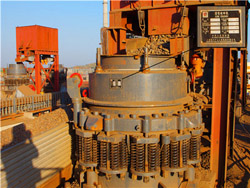
Technological assessments on recent developments in fine and
This flotation cell drastically reduces the mining industry’s water and energy consumption by increasing the flotation's upper particle size limit. More detailed Diagram of a cylindrical flotation cell with camera and light used in image analysis of the froth surface. Froth flotation is a process for selectively separating hydrophobic Froth flotation
احصل على السعر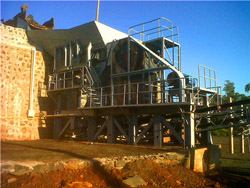
New approach for flotation process modelling and simulation
P. Vallejos a,R. Grau b,A. Yañez b Add to Mendeley https://doi/10.1016/j.mineng.2020.106482 Get rights and content Abstract The aim of The use of the combined FCSMC and cell flotation process showed promising results for a producing grade of 48.24 g/t gold with 96.13% recovery. The Combined Column and Mechanical Flotation Cell Process for the
احصل على السعر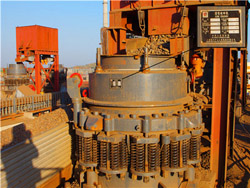
Minerals Free Full-Text Design of Cell-Based
The flotation circuit treats 1000 tons per hour of ore containing 0.1% of chalcopyrite (10 tons per hour) on average. The downstream smelter is specified the minimum concentrate grade of 25%. This paper discusses the design and implementation of an automated flotation cell system for a mineral processing plant. The system utilizes advanced Design of an Automated Flotation Cell for Laboratory Operations
احصل على السعر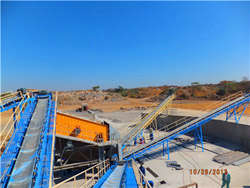
Flotation data for the design of process plants Part 1 AusIMM
Flotation data for the design of process plants Part 1 testing and design procedures R. C. Dunne*1, G. S. Lane2, G. D. Richmond3 and J. Dioses2 This paper discusses the methods used in the design of flotation plants, including benchscale batch and locked cycle tests and pilot plant trials. The methods used to establish appropriateIn order to increase the recovery of PGMs by flotation, it is necessary to optimise the liberation of the key minerals in which the platinum group elements (PGEs) are contained which include sulphides, arsenides, tellurides, and ferroalloys among others, while at the same time ensuring the optimal depression of gangue minerals. In order to Minerals Free Full-Text Challenges Related to the Processing
احصل على السعر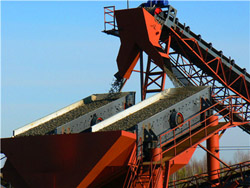
Minerals Special Issue : Design, Modeling,
Mechanical, column, and pneumatic flotation cells (Jameson, Imhoflot TM and Reflux TM flotation cells); Impact of operation parameters on designing flotation cells (gas hold-up, superficial gas velocity, bubble For instance, TON’s state-of-the-art Optimizing Control System (OCS-4D™) uses APC methods to optimize set points throughout the plant. This helps to maximize mineral recovery within plant physical and metallurgical constraints. Since 1990, TON has provided optimizing control systems for grinding and flotation circuits with How to maximize ore and grade recovery through flotation
احصل على السعر
Minerals Free Full-Text Residence Time Distribution
This short communication presents residence time distribution (RTD) measurements and modeling in a 16 m3 Siemens flotation cell, as the first RTD characterization in an industrial-scale pneumatic cell. The Siemens cell was installed as a pre-rougher machine in a Cu-Mo selective plant. This plant recovered molybdenite as Flotation Plant. The actual process of concentrating the minerals by flotation is but one of a sequence of operations, The labor, of course, will vary with the size of the plant. At one plant consisting of 60 cells, two men per shift operate the entire plant, equivalent to a cost of 1¼c. per ton.Flotation 911 Metallurgist
احصل على السعر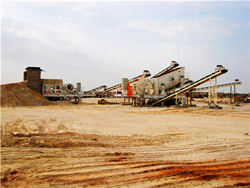
Minerals Special Issue : Recent Advances in Flotation Process
This paper presents a characterization of the different minerals recovered along industrial flotation circuits. Plant sampling campaigns, performed in a copper industrial concentrator in Chile, provided the data for the study. Two rougher flotation banks consisting of cells of 130 m 3 and 300 m 3, were evaluated.Mineral carrying rates across the pulp-froth interface in the range of 1.4-3.2 tph/m 2 and bubble surface coverage between 7 and 22 %, have been determined in large rougher flotation cells (100DESIGN OF FLOTATION CIRCUITS WITH CONVENTIONAL FLOTATION CELLS
احصل على السعر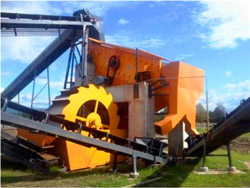
A critical review on natural surfactants and their potential for
Until now, the use of microbial biomass and naturally occurring BioS for mineral flotation has been evaluated mainly at the laboratory scale (micro-flotation cell). Successful industrialization of bio-flotation will require the evaluation of several variables, namely biomass availability, production cost and subsequent extraction, the ore-BioS Flotation Cells: The innovation target points of mineral processing plant. Flotation is a versatile, surface wettability-based separation process, using by mineral processing and chemical engineers for the separation and concentration of variety of different minerals in an aqueous suspensions or solutions, coal enrichment, precipitates and etcFlotation Cells: The innovation target points of mineral processing plant
احصل على السعر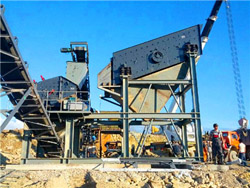
Minerals Free Full-Text Design of Cell-Based
The design of cell-based flotation circuits is often completed in two distinct phases, namely circuit structure identification and equipment sizing selection. While recent literature studies have begun to Flotation performance is influenced by many hydrodynamic variables, such as impeller speed, airflow rate, and cell geometry. These variables’ effects and interactions remain unsatisfactorily explored, especially concerning scaling-up procedures. As an innovative approach, this study considered factorial-designed experiments to Influence of hydrodynamic variables on scaling up of mechanical
احصل على السعر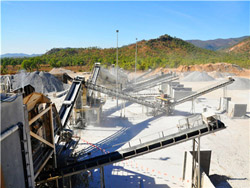
Modelling for froth flotation control: A review ScienceDirect
Although image analysis techniques have numerous advantages such as their consistency across all cells monitored, the possibility of linking to plant data, and a high frequency of measurements (Forbes, 2007), some features, such as the estimation of mineral concentration in the froth phase have not been fully implemented yet at Bubble loads were measured on the first primary cleaner cell of an operating flotation plant using a bubble load meter with a 20mm riser diameter. A bubble load value of 10.58grams/liter was obtained.(PDF) On Limits to Flotation Cell Size ResearchGate
احصل على السعر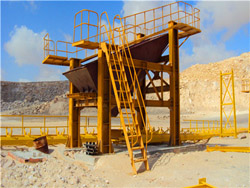
Minerals Free Full-Text On Limits to Flotation Cell Size MDPI
Mechanical cells have seen an exponential increase in size over the past 60 years. However, a possible size limitation due to carrying capacity constraints has been raised. Taking a Cu porphyry case, a cell sizing exercise is used to show that possible size limitation due to carrying capacity can be tested using available techniques. A range of Prasad 1969 Mineral processing plant design and cost estimation. 2015), while the use of operational cost variables can help in designing the capacity of flotation cells (Arfania et al.,(PDF) Cost modelling for flotation machines ResearchGate
احصل على السعر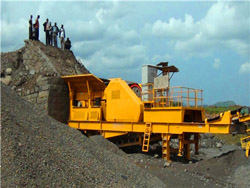
Minerals Free Full-Text Digitalization Solutions in the Mineral
The next-generation froth flotation cells feature smart sensors and sensing elements. and allow for sharing real-time data with our customers. As a final product, the virtual mineral processing plant of the GTK Mintec pilot plant will be built based on the best practices and experiences. Author Contributions. Conceptualization,The pressure for saving water by closing the water loops in mineral processing is increasing continuously. The drivers for higher recirculating rates include water scarcity in dry areas, environmental legislation that is becoming stricter in most countries, limitations set for wet tailings management and the increased demands for social Minerals Free Full-Text Improving Nickel Recovery in Froth
احصل على السعر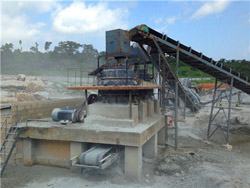
Froth Images from Flotation Laboratory Test in Magotteaux Cell
Froth flotation is a widely used method for the concentration of sulfide minerals. The structure of the superficial froth is an indicator of the performance of froth flotation alongside with the operational conditions in which this process is carried out. The aim of this study is to explore how the different operational conditions that can be With higher concentration rates and a simple and efficient flowsheet, the FCSMC has been successfully industrialized for flotation circuits of minerals such as coal and copper ores in China. 21−23 However, there have been relatively few studies on the flotation behavior of columns and cells in gold mineral flotation, particularly concerning Combined Column and Mechanical Flotation Cell Process for the
احصل على السعر