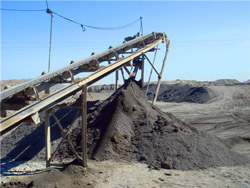
Overview of cement grinding: fundamentals, additives, technologies
PDF Grinding is an essential operation in cement production given that it permits to obtain fine powder which reacts quickly with water, sets in few Find, read and cite all the research youA cement mill (or finish mill in North American usage ) is the equipment used to grind the hard, nodular clinker from the cement kiln into the fine grey powder that is cement. Most cement is currently ground in ball mills and also vertical roller mills which are more effective than ball mills. Cement mill
احصل على السعر
The important role of vertical roller mills in the cement industry
GRMK vertical cement mill has the advantages of compact structure and small volume. It mainly includes high efficiency separator, grinding rollers, grinding table, hydraulic For the past three decades the vertical roller mill has emerged to be the preferred choice for grinding raw materials. With the grinding capacity of a vertical Review on vertical roller mill in cement industry & its
احصل على السعر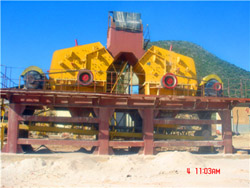
The important role of vertical mills in cement clinker grinding station
The working principle of vertical roller mills is based on two to four grinding rollers with shafts carried on hinged arms and riding on a horizontal grinding The increasing demand for “finer cement” products, and the need for reduction in energy consumption and green house gas emissions, reinforces the need for Cement grinding optimisation ScienceDirect
احصل على السعر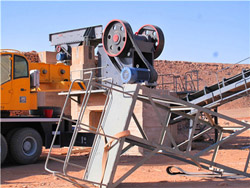
Effect of amine and glycol-based grinding aids utilization rate on
In this study, it is aimed to give a new viewpoint of choosing utilization rates and type of grinding aids (GA), taking into account cement-polycathoxylate ether Grinding of finished cement is performed in a single stage, intergrinding materials with very different grindabilities. This intergrinding process has many Resistance to Grinding and Cement Paste Performance of
احصل على السعر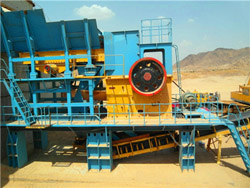
The influences and selection of grinding chemicals in
Today, grinding chemicals are reported as capacity improvers or in some cases strength enhancers. Cement grinding operations demand these chemicals in The advantages of using grinding aids in the cement industry on the performance of ball mills and air classifiers [1], as well as the effects of various dosages Effects of grinding aid dosage on circuit performance and cement
احصل على السعر
2 Major Roles of Limestone in Cement Manufacturing
Limestone plays two major roles in the cement manufacturing process, one is used as a raw material for cement clinker, and the other is used as a cement admixture. Limestone is one of the key raw materials of cement clinker. Around 80-90% of the raw material for the kiln feed is limestone. Limestone is also a favored mineral Tushar Khandhadia, General Manager Production, Udaipur Cement Works, discusses the role of grinding in ensuring optimised cement production and a high quality end product. How does the grinding process contribute to the production of high-quality cement?The quality of cement depends on its reactive properties and particle Grinding process is a critical stage in cement production
احصل على السعر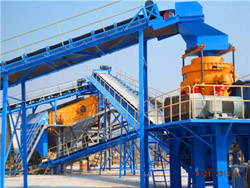
The influences and selection of grinding chemicals in cement grinding
The results implied that the production rate of the circuit and the 28-day strength of the cement could be increased by 24% and 3.5% respectively with the selection of an appropriate chemical. In addition, the use of chemicals may reduce the clinker consumption by 5% that is important regarding to CO2 emissions.This research focuses on investigating the effects of the three different grinding aids, consisting of a mixture of amine, glycol and polyol in different ratios, on the model parameters of a two-compartment cement ball mill and an air classifier. Within the content of this work, sampling campaigns were organized around a cement grinding Effects of grinding aids on model parameters of a cement ball
احصل على السعر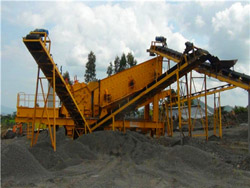
Roller press is well-accepted technology in India Indian Cement
In the case of cement grinding, again two technologies are being accepted –Vertical Roller Mill or Roller Press in semi-finish or finish grinding. Roller Press in finish grinding has the advantage of further saving of 3-4 Kwh/t as compared to Semi-finish grinding and Vertical Mill technology. With more acceptance of blended cement like The cement industry, an industry characterised by low margins, is responsible for approximately 7% of anthropogenic CO2 equivalent (CO2e) emissions and holds the highest carbon intensity of anyTowards a business case for CO2 mineralisation in the cement
احصل على السعر
PROCESS CONTROL FOR CEMENT GRINDING IN VERTICAL
The power ingesting of a grinding process is 50-60% in the cement production power consumption. The Vertical Roller Mill (VRM) reduces the power consumption for cement grinding approximately 30-40% associated with other grinding mills. The process variables in cement grinding process using VRM are strongly nonlinear and having large timeThe ambition to save energy during the production leads to the deeper investigation to grinding cement in finish mode with roller presses also. Tests were conducted in several plants with different cement compositions and the cement properties were evaluated. The same cement composition was also produced with roller press-ball Roller press:Efficient grinding solutions Indian Cement Review
احصل على السعر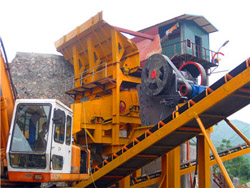
Towards Sustainability: Slag Grinding Circuits Indian Cement
In the case of slag grinding, acceptance of roller press in finish grinding is well recognised. It offers a distinct advantage of saving of about 6-7 Kwh/t as compared to Vertical Roller Mill at 4200 Blaine. KHD has sold 27 Sag Grinding Circuits and maintains about 70% market share in slag grinding in India.Finished grinding may consume 25-50 kWh/t cement, depending on the feed material grindability, additives used, plant design and especially the required cement fineness. The grinding process absorbs more energy due to the losses attributable to heat generated during grinding, friction wear, sound noise and vibration.Blended Cement Grinding: Energy Intake and Fineness
احصل على السعر
XRF Analysis of Cement X-Ray Fluorescence
The XRF analysis of cement is fast, convenient, simple, and nondestructive. But the realization of accurate results in all cement production stages requires correct sample preparation. It could be The need of the cement industry in the future is to reduce the specific energy consumption in grinding process [7] (Fig. 2). Grinding systems in the cement industry play a crucial role in particle size distribution and particle shape. This affects the reaction of the clinker and the temperature dependence of the dehydrated gypsum whichReview on vertical roller mill in cement industry & its performance
احصل على السعر
Modernizing cement manufacturing in China leads to substantial
China has witnessed a construction boom and thus an enormous amount of cement use in the past decades. At the same time, cement manufacturing technology has been upgraded rapidly. Here, based onData from published literature and laboratory tests regarding use of limestone in portland cement are reviewed. Emphasis is placed on amounts of 5% or less. The effects of interground and blended(PDF) The Use of Limestone in Portland Cement: A State
احصل على السعر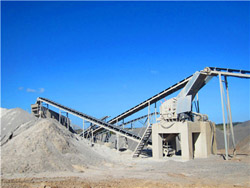
New cement grinding line from CEMTEC Cement Lime Gypsum
The new grinding line is based on a CEMTEC ball mill with a diameter of 5.0 m and a length of 15.75 m. It will have a 6500 kW motor that operates in closed circuit with a CEMTEC CTC-200 high-efficiency separator. With a nominal capacity of 120 tph of CEM I-52.5 at 4700 cm 2 /g (according to Blaine), the plant will also produce other cementGypsum in Cement G. Frigione CEMENTIR, Cementerie del Tirreno, Napoli, Italy CONTENTS 1 2 3 Introduction Grindability and Granulometric Distribution Influence on Hydration 3.1 Hydration of C3S and C2S 3.2 Hydration of C3A 3.3 Hydration of G+AF 3.4 Hydration of Portland Cement 4 Influence on Rheological Behaviour 4.1 Gypsum in Cement ScienceDirect
احصل على السعر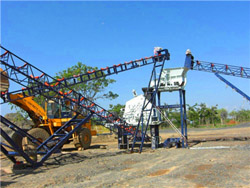
AUTOMATION AND CONTROL IN CEMENT INDUSTRIES
UNESCO EOLSS SAMPLE CHAPTERS CONTROL SYSTEMS, ROBOTICS, AND AUTOMATION Vol. XIX Automation and Control in Cement Industries Keviczky L. ©Encyclopedia of Life Support Systems (EOLSS) Figure 4. Typical cement grinding mill A closed circuit consists of three main parts: the ball mill itself, the elevator lifting theCement production line process, producing 1 ton silicate cement need to grind 3 ton materials (including raw materials, fuel, clinker, mixed materials, gypsum). According to statistics, dry method cement production lines grinding operations need to consume above 60% motive power, which raw material grinding accounts for above instruction manual of cement production line process
احصل على السعر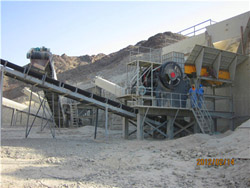
The important role of vertical roller mills in the cement industry
It is widely used in clinker grinding production of cement plant and slag grinding plant. CHAENG can provide various types of vertical cement mills with productivity of 50-250t/h. The biggest advantage of CHAENG is to have a large casting base and large machining workshops, which greatly shortens the delivery cycle of cement vertical mill.
احصل على السعر