
Iron Ore Pelletizing Process: An Overview IntechOpen
Binders are used in the pelletizing of iron ore aiming to improve the performance of the process in the following aspects [ 1, 4, This study illustrates the feasibility of pelletizing magnetite iron ore concentrate using four organic binders: KemPel, Alcotac CS, (PDF) Iron Ore Pelletizing Process: An Overview
احصل على السعر
Pelletizing
Pelletizing iron ore is undertaken due to the excellent physical and metallurgical properties of iron ore pellets. Iron ore pellets are spheres of typically 6–16 mm (0.24–0.63 in) to be used as raw material for blast furnaces. They typically contain 64–72% Fe and various additional material adjusting the chemical composition and the metallurgic properties of the pellets. Typically limestone, dolomiteA brief introduction to recent developments in iron ore pelletizing is provided in this chapter, including the world output of fired (PDF) Iron ore pelletization ResearchGate
احصل على السعر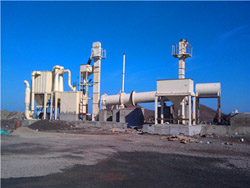
Iron Ore Pelletization: Part I. Fundamentals Taylor & Francis Online
The behavior of iron ore pellet binders is complex. Any pellet binder is subject to a handful of practical requirements: that it be readily dispersed through a Our iron ore pelletizing systems combine the best features of both technologies to provide the most modern plant and to produce pellets at the lowest cost and highest quality. Pellet plants sized from 1.2MTPA to Iron ore pelletizing TON
احصل على السعر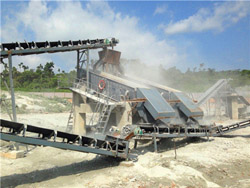
THE GROWING IMPORTANCE OF PELLETIZING FOR IRON
THE GROWING IMPORTANCE OF PELLETIZING FOR IRON ORE MINING AND IRON PRODUCTION Authors: Jose Murilo Mourao Independent Researcher In the last years, pelletizing has been A brief introduction to recent developments in iron ore pelletizing is provided in this chapter, including the world output of fired pellets, pellet production Iron ore pelletization ScienceDirect
احصل على السعر
Iron Ore Pelletizing Process: An Overview IntechOpen
The iron ore pelletizing process consists of three main steps: Pelletizing feed preparation and mixing: the raw material (iron ore concentrate, additives —anthracite, dolomite A brief introduction to recent developments in iron ore pelletizing is provided in this chapter, including the world output of fired pellets, pellet production Iron ore pelletization ScienceDirect
احصل على السعر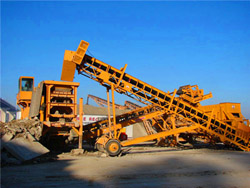
Dynamic simulation of pellet induration process in straight-grate
Keywords: mathematical modeling, pellet induration, straight grate, pellet shrinkage, iron ore pelletizing . 2 I. INTRODUCTION Production of pellet as a desirable feedstock for ironmaking furnaces has exceeded 300 Mt per year in 2005, accounting for about 24% of the iron ore processed globally (UNCTAD, 2006).Pelletizing of iron ore was started in the 1950s to facilitate the utilization of finely ground iron ore concentrates in steel production. For the pelletizing of iron ore there are two main types of processes namely, the straight travelling grate (STG) process and the grate kiln (GK) process. In the STG process, a stationary bed of pellets isIron Ore Pellets and Pelletization Process IspatGuru
احصل على السعر
(PDF) EVOLUTION AND GROWTH OF IRON ORE
In this scenario, the world pelletizing capacity grew from 350 Mt/year in 2000 to more than 600 Mt/year in 2020. ron ore products and the corresponding use in iron making. (4) TypicalIn this paper, an iron ore with high iron grade and low silicon content was used in pelletizing experiments. Specific surface areas were tested, and it would increase slowly and then have a rapid increase with the increasing of particle sizes. Thirty percentage of the high iron grade ore could be used when −200 meshes content of the orePelletizing of Iron Ore with High Iron Grade and Low Silicon
احصل على السعر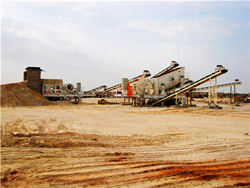
Assessment of iron ore pellets production using two charcoals
In Brazil iron ore pelletizing is an important economic activity, with a large volume of production and relevant thermal consumption (remarkably coal, heavy oil and gas), development of alternative fuels, such as eucalyptus charcoal, can generate relevant environmental, economic, technological and social benefits.The iron ore pelletizing process consists of three main steps: 1. Pelletizing feed preparation and mixing: the raw material (iron ore concentrate, additives anthracite, dolomite and binders are prepared in terms of particle size and chemical specifications, dosed, and mixed together to feed the pelletizing process; 2.Iron Ore Pelletizing Process: An Overview IntechOpen
احصل على السعر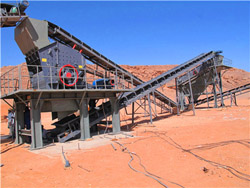
Review of Organic Binders for Iron Ore Agglomeration
Review of Organic Binders for Iron Ore Agglomeration J.A. Halt, S. Komar Kawatra . Department of Chemical Engineering . Michigan Technological University . Houghton, MI 49931 ©[email protected] . Date Last Edited: 5/22/2013 . Introduction Iron ore pellets are one type of iron-rich, intermediate product used during primary iron and Deposit formation in the coal-fired rotary kiln is frequently found in the production of fluxed iron ore pellets by the grate-kiln process and affects normal production. In this paper, the effects of pellet basicity (CaO/SiO2 mass ratio) on the simulated deposit formation were investigated. The results show that the porosity of deposits samples increases from 30.8 Effects of Pellet Basicity on the Simulated Deposit Formation in
احصل على السعر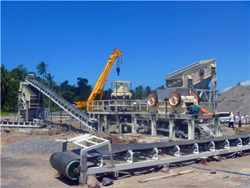
Iron Ore Pelletizing Process: An Overview Semantic Scholar
The iron ore production has significantly expanded in recent years, owing to increasing steel demands in developing countries. However, the content of iron in ore deposits has deteriorated and low-grade iron ore has been processed. The fines resulting from the concentration process must be agglomerated for use in iron and steelmaking. Iron ore pellets not only have excellent metallurgical and mechanical properties but are also essential raw materials for improving iron and steel smelting in the context of the increasing global depletion of high-grade iron ore resources. Organic polymers, as important additive components for the production of high-quality pellets, Polymers Free Full-Text A Review on the Effect of the MDPI
احصل على السعر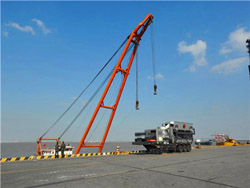
Iron ore pelletization ScienceDirect
Abstract. A brief introduction to recent developments in iron ore pelletizing is provided in this chapter, including the world output of fired pellets, pellet production processes, preparation of pellet feed, inorganic and organic binders, and new additives. Throughout the chapter, the authors have used a difficult pellet feed, that is, aThe transformation from traditional iron- and steelmaking technologies to green H2-based new technologies will require an improvement in the quality and purity of iron ore burden materials. Iron ore pellets are essential inputs for producing direct reduced iron (DRI), but the conventional binders, used in iron ore pelletizing, introduce gangue Sustainability Free Full-Text Developing Iron Ore Pellets Using
احصل على السعر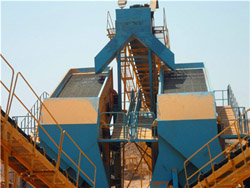
High-grade iron ore, metallics in focus to enable DRI, low
Pelletizing iron ore uses energy at the pellet plant, and the more concentrated the ore feedstock the greater the need for beneficiation, grinding and sorting, with additional energy, equipment, water and in some cases chemicals used.Top charging of mostly reduced iron ore pellets is readily represented in our automated spread sheet calculations. The steps are; 1. calculation of DRI pellet enthalpies at 25°C and 930°C, the top-segment–bottom-segment division temperature; 2. specification that the DRI pellets are not oxidized nor reduced while descending through the topIron Ore Pellet an overview ScienceDirect Topics
احصل على السعر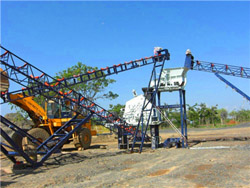
What Are Iron Ore Pellets and How to Make Them? Fote Machinery
By adding water to the top of the disc, iron fines are spun up along with other fines, forming pellets. The pellets are automatically graded according to particle size until 8 -16 mm pellets are discharged. Upon balling, they are dried, hardened at high temperatures of 1200-1300°C, and then cooled.Regional growth of iron ore pelletizing sinc e 1950. (1-3) With the expected depleti on of direct charge iron ores and high quality sinter fines,(PDF) GUIDELINES FOR SELECTING PELLET PLANT TECHNOLOGY
احصل على السعر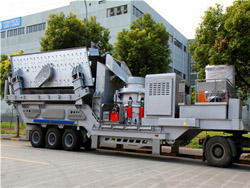
Iron Ore Pelletizing Essential in Meeting Future Steel Needs
Iron ore pelletizing, or balling, is the process of transforming fines into spherical granules anywhere from 8 16mm in size via tumble-growth (agitation) agglomeration using either a disc pelletizer (pan granulator) or rotary drum. Why Pelletizing is an agglomeration process which converts very fine grained iron ore into balls of a certain diameter range (normally 8mm to 20 mm, also known as pellets. These pellets are suitable for blast furnace and direct reduction processes.Understanding Pellets and Pellet Plant Operations IspatGuru
احصل على السعر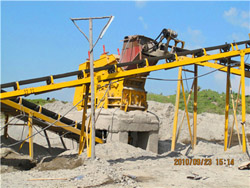
Iron ore pellets for blast furnace a technical guide.
Iron ore pellets are a man-made iron-riched ore. The pellet production method was invented in Sweden in 1912, and then began to be used in the United States in 1946 by shaft furnace. It was originally developed primarily for the efficient use of taconite mines. Taconite ore only contains about 35% iron, and this low-grade iron ore can only At present around 6–7% of iron ore slimes, out of total production, are being generated and accumulated at iron ore mine sites of National Mineral Development Corporation Limited, India. The accumulated slimes of finer size and relatively inferior grade should be utilized in an economical way for sustainable mining. These slimes can be Preparation of Iron Ore Micro-pellets and Their Effect on
احصل على السعر