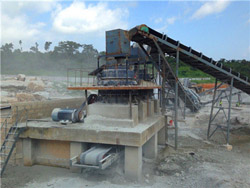
Exploring the Challenges and Advances in Concentrating Ultrafine
The processing of ultrafine particles is being increasingly studied for better use of mineral resources and especially reduction of tailings generation. It involves the adoption of the mass concentration value corresponding to the height of the slurry/supernatant interface after 24 hours of rest in a conventional (PDF) Thickeners in iron ore processing ResearchGate
احصل على السعر
Iron Ore Characterization Techniques in Mineral Processing
Iron ore concentrates have been generated utilizing the conventional beneficiation process and also by the approach of reduction roasting-magnetic separation.In mineral processing plants, thickening is intended to remove the water content of pulp so that the mineral processing products meet the requirements of the Thickening of Mineral Processing Products SpringerLink
احصل على السعر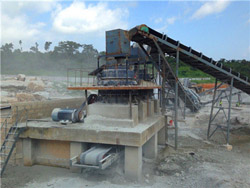
Minerals Free Full-Text Recovering Iron from Iron
Abstract. Iron ore tailings (IOTs) are a form of solid waste produced during the beneficiation process of iron ore concentrate. In this paper, iron recovery from IOTs was studied at different points during a ABSTRACT. This chapter deals with reagents that have been used in processing a variety of iron ores, especially low-grade types. The emphasis is on applications of various Reagents in Iron Ore Processing 19 Reagents in Mineral
احصل على السعر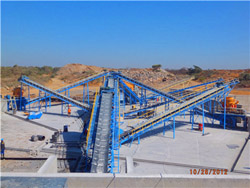
Iron Ore Processing, General
The iron ore processing industry produces usable concentrations of iron-bearing material by removing nonferrous rock (gangue) from low-grade ore. In the United States, Crushing, a form of comminution, one of the unit operations of mineral processing. In the field of extractive metallurgy, mineral processing is the process of separating commercially valuable minerals from their ores. [1] Depending on the processes used in each instance, it is often also known as ore dressing or ore milling .Mineral processing
احصل على السعر
Mineral and metal processing Arkema Global
Greater value at every stage of the operation. We help generate greater value from your operations at every stage of mineral processing including mineral suspension and slurry handling, flotation and other enrichment The Sino Iron project started its first full year of commercial operation in 2017 produced and exported approximately 17 million wet metric tons of iron ore concentrate (Citic 2018 Annual Report). In 2018, Sino Iron shipped more than 19 million wet metric tons to CITIC’s special steel plants and other Chinese and Asian steel mills Comminution and classification technologies of iron ore
احصل على السعر
Dry beneficiation of iron ore Mineral Processing
The haematite ore in South Africa is processed in a dry process to a HQ lump ore with 64 % iron content and a sintered fine ore with 63.5 % iron content. For fine ore beneficiation, wet processes are used. Capacity at the Minas Rio is to be increased from 26.5 Mta capacity to 28 Mta in the forthcoming years.McLanahan’s director of process engineering for mineral processing, Scott O’Brien, explained the rationale for using this approach to dewatering. O’Brien said while using a thickener on its own will enable an operator to recover 80%-90% of the water in a slurry, the underflow will still contain enough water to make it difficult to handleDewatering: An Increasingly Important Mineral Process E & MJ
احصل على السعر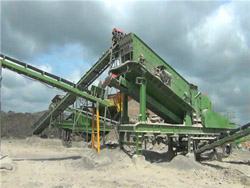
Physical separation of iron ore: magnetic separation ScienceDirect
An iron ore concentrate containing 64.6% Fe can be produced using this flow sheet from a run-of-mine ore containing 51.1% Fe at a mass yield of 69.6% to the iron ore concentrate, The magnetic product of the roll magnetic separators may reach 25–40% Fe, which is then fed to mineral processing plants.In this paper the bench and full-scale flocculation behavior of iron ore tailings is investigated in order to improve the dewatering performance of tailings thickeners of an iron beneficiation plant. In the batch settling tests, the effect of flocculant dosage (5–20 g/t solid), slurry solids concentration (3–12 %), pH (4–12), andImproving flocculation and dewatering performance of iron
احصل على السعر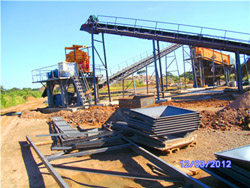
Iron ore beneficiation: an overview ScienceDirect
2.4. Beneficiation methods. Beneficiation is a process where ore is reduced in size and valuable minerals are separated from the gangue minerals. Separation of valuable minerals from gangue minerals can be efficiently achieved by taking advantage of the differences in physical, surface, and magnetic properties.Water balance of a high-density thickener in an iron ore concentrator plant. The most common problems in thickener operations include the presence of suspended solids in the recovered water and the density or percentage of solids of the thickener discharge outside the set targets. These problems are classified according to whether they areMost common problems in thickener operations (part 1)
احصل على السعر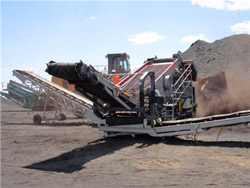
Hematite Processing by Flotation 911 Metallurgist
Direct shipping of high grade iron ore, as the major iron mineral as low as 25% Fe can be treated with “Sub-A” Flotation to produce concentrates that average better than 62% Fe with less than 9% SiO2 and with a high recovery. Thickening and Filtering Hematite Concentrate.Iron ore concentrate was obtained directly with a roughing, On July 14, 2009, Xinhai signed a deal with customers to undertake one-stop mineral processing service about Liaoning Anshan 500t/d iron ore beneficiation iron ore processing plant, iron ore mining process,
احصل على السعر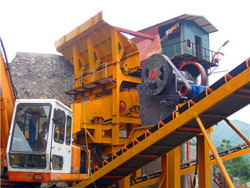
(PDF) Understanding the Thickening Process
PDF On Jan 1, 2006, B J Gladman and others published Understanding the Thickening Process Find, read and cite all the research you need on ResearchGateUsed for tailings thickening to recover water in iron ore beneficiation and palletization plants. DK SET P 3282: Anionic polyacrylamide: Used for tailings and concentrate thickening to recover water in iron ore beneficiation and palletization plants: DK SET P 700/ P 700(2)/PN 6150: Nonionic polyacrylamideMining, Mineral Processing and Metallurgy
احصل على السعر
Four Kinds of Hematite Ore Dressing Processes, Which One
The mineral form is dominated by iron oxide. According to its composition, hematite ore can be divided into four varieties, including ilmenite, aluminum hematite, magnesium hematite and hydrohematite.12.7 Ore to Concentrate and Metal. Mineral processing or mineral beneficiation or upgradation involves handling of three primary types of ROM ore material which has been blasted, fragmented and brought out from in situ position. These materials can be used directly or by simple or complex processing and even applying extractive metallurgy likeMineral Processing an overview ScienceDirect Topics
احصل على السعر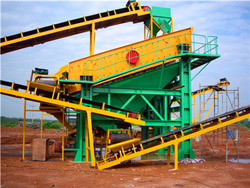
Magnetizing Reduction and Magnetic Separation Studies on Low-Grade Iron
The role of high-quality iron ore and concentrate as a raw material is very critical to get the best quality iron and steel [1]. Juniper Publishers Juniper Journals 3700 Park View Ln #12B, Irvine, California 92612, USA. ISSN: 2689-4629. (1992) Magnetizing reduction of iron ores. Mineral Processing and Extractive Metallurgy Review 11(1-2How a Thickener Works. Thickening or dewatering may be defined as the removal of a portion of the liquid from a pulp or slime made up of a mixture of finely divided solids and liquids. The early methods of thickening employed plain, flat-bottomed tanks into which the pulp was fed until the tank was full. The solids were then allowed to How a Thickener Works 911 Metallurgist
احصل على السعر
Comminution and liberation response of iron ore types in a low
Much of the remaining iron ore resources in Brazil consist of low-grade itabirite ores. Accordingly, a typical beneficiation circuit includes a four-staged crushing/screening plant, followed by grinding in a closed-circuit ball mill, desliming in hydrocyclones and final ore mineral concentration via multistage reverse flotation and Shandong 500t/d Copper Lead and Zinc Ore Bulk Flotation Project. Ore Property: Shandong client commissioned Xinhai Mine Research Institute to conduct ore dressing experiment after collected 50kg samples on the scene. After tested the ore properties of sample ore, Xinhai lab concluded that the main metal minerals of the project were copper, lead, zinc, copper ore processing plant, copper flotation plant, copper
احصل على السعر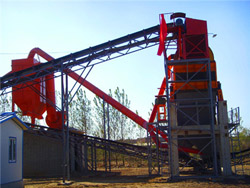
Improving efficiency of iron ore thickening and deslurrying
Finely grinded iron ore powder of 100 (149 µm) and 200 (74 µm) mesh sizes were passed via shaking table and magnetic separator subsequently. The iron ore was successfully upgraded from 28.27 wt.% to 36.51 wt.% at 100 mesh and 38.70 wt.% at 200 mesh via shaking table, thus achieving a maximum of 10% upgraded iron ore.
احصل على السعر