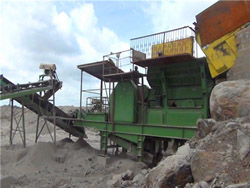
Extraction of Iron Metallurgy Blast Furnace and
Know How Extraction of Iron from its ore is carried out in the Blast Furnace, Concentration Of Ore And Purification. Learn about the reaction in the blast furnaceThe blast furnace Iron is extracted from iron ore in a huge container called a blast furnace. Iron ores such as haematite contain iron (III) oxide, Fe 2 O 3. The oxygen Redox, extraction of iron and transition metals Extracting
احصل على السعر
Special Issue "Iron Ore Reactions and Phenomena in a Blast Furnace"
Blast furnaces are charged with iron ores in the form of pellets, sinter and/or lump ore and metallurgical coke in separate layers from the top of the furnace. In this paper, a novel methodology is proposed to implement the grain model to predict iron ore reduction in blast furnace. The model considers the gas Modeling of iron ore reactions in blast furnace
احصل على السعر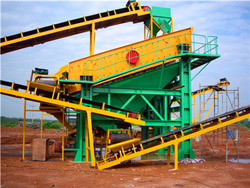
Ironmaking 101 From Ore to Iron with Blast Furnaces
In the upper region of the blast furnace where temperature range from 600 to 700 C. the iron ore or iron oxide is Abstract. The smelting of iron ore into metallic iron was first accomplished by primitive blast furnaces approximately three thousand years ago. Improvements in The Iron Blast Furnace: A Study in Chemical Thermodynamics
احصل على السعر
Blast furnace ironmaking and its ferrous burden quality
• integrated iron and steelmaking process, • Scrap/direct reduced iron (DRI) and electric arc furnace (EAF) process. The integrated iron and steelmaking route The production of iron from its ore involves an oxidation-reduction reaction carried out in a blast furnace. Iron ore is usually a mixture of iron and vast quantities of impurities such Iron Production Chemistry LibreTexts
احصل على السعر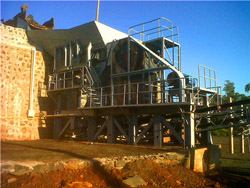
Minerals and iron-making reactions in blast furnaces
1. Introduction The blast furnace is an efficient high-temperature reactor in which hot reducing gases formed from the combustion of coke and supplementary fuels The main focus of this paper is studying the process monitoring and abnormality detection of the iron-making process in blast furnaces using PCA-based Process monitoring of iron-making process in a blast
احصل على السعر
23.2: Pyrometallurgy Chemistry LibreTexts
Iron that is obtained directly from a blast furnace has an undesirably low melting point (about 1100 °C instead of 1539 °C) because it contains a large amount of dissolved carbon. It contains other impurities (such as Si, S, Blast furnaces are charged with iron ores in the form of pellets, sinter and/or lump ore and metallurgical coke in separate layers from the top of the furnace. While descending, the ferrous burden materials encounter different kinds of reactions and phenomena inside the blast furnace, including reduction reactions, softening and meltingSpecial Issue "Iron Ore Reactions and Phenomena in a Blast Furnace"
احصل على السعر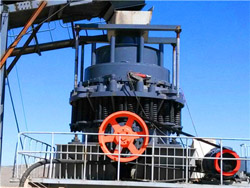
Extraction Of Iron PPT SlideShare
6. Occurrence of Iron Iron is very reactive and is found in nature in form of its oxides, carbonates and sulphates. The main ores are: i) Haematite (Fe2O3) ii) Magnetite (Fe3O4) iii) Iron Pyrites (FeS2) o The Blast Furnace Process. The blast furnace is a counter-current gas/solids reactor in which the descending column of burden materials [coke, iron ore and fluxes/additives] reacts with the ascending hot gases. The process is continuous with raw materials being regularly charged to the top of the furnace and molten iron and slag being tapped fromPig Iron Production Blast Furnace Route Metallics
احصل على السعر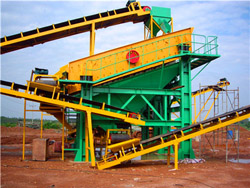
HIGH TEMPERATURE CHEMISTRY ROLE IN METAL PRODUCTION
The reduction and smelting of iron ore is done mainly in the iron blast furnace. The burden charged at the top of the furnace consists primarily of iron ore, flux and coke. The reducing gas carbon monoxide and the heat required for the smelting of the ore are generated at the bottom of the furnace by blowing preheated air into the coke bed.Extracting iron from iron ore using a Blast Furnace. Introduction. The common ores of iron are both iron oxides, and these can be reduced to iron by heating them with carbon in the form of coke. Coke is produced by heating coal in the absence of air. Coke is cheap and provides both the reducing agent for the reaction and also the heat sourceiron and steel chemguide
احصل على السعر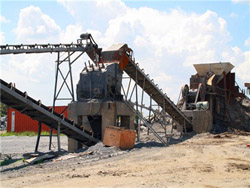
Ironmaking 101 From Ore to Iron with Blast Furnaces
Iron is mainly extracted from hematite (Fe 2 O 3) and magnetite ores. Natural or direct shipping iron ores contain between 50-70% iron and can be fed directly into the blast furnace. Fe 3 O 4 decomposes when heated to ferrous oxide (FeO) and ferric oxide (Fe 2 O 3) via Fe 3 O 4 → FeO + Fe 2 O 3. A specialized type of coal, called hard First, the iron ore, the raw materials for steel, comes from the Earth. Most iron ores — hematite, magnetite, limonite — contain an average of 60% of iron (Fe). Before the iron ores enter a blast furnace, it undergoes ‘sintering’ which turns the pristine iron ore into more compact and appropriate sizes.Blast Furnace Anatomy #1 To the Heart of Steelworks Operation
احصل على السعر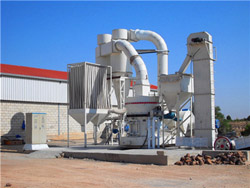
Iron processing Ores, Smelting, Refining Britannica
The most widely distributed iron-bearing minerals are oxides, and iron ores consist mainly of hematite (Fe2O3), which is red; magnetite (Fe3O4), which is the biggest being more than 1 metre (40 inches) across and the smallest about 1 millimetre (0.04 inch). The blast furnace, however, requires lumps between 7 and 25 millimetres, so the oreFormer AHM blast furnace in Port of Sagunt, Valencia, Spain. A blast furnace is a type of metallurgical furnace used for smelting to produce industrial metals, generally pig iron, but also others such as lead or copper. Blast refers to the combustion air being supplied above atmospheric pressure.. In a blast furnace, fuel (), ores, and flux are continuously Blast furnace
احصل على السعر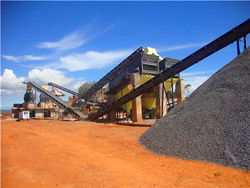
IGCSE Chemistry 0620 Unit 14 Extracting metals YouTube
IGCSE Chemistry 0620 Unit 14 Extracting metals Episode 2 Extracting iron in blast furnaceThis video explains about the following:- Extraction of ir...Chlorine in blast furnace gases is mainly from iron ores, additives (CaCl 2), pulverized coal, Then, this reference speculates some possible development tendency of blast furnace gas purification. Wang Y, Lei X, Deng L, et al. A review on utilization of combustible waste gas (I): blast furnace gas,A Review on Desulfurization Technologies of Blast Furnace Gases
احصل على السعر
Blast Furnace Encyclopedia
blast furnace • n. a smelting furnace in the form of a tower into which a blast of hot compressed air can be introduced from below. Such furnaces are used chiefly to make iron from a mixture of iron ore, coke, and limestone. The Oxford Pocket Dictionary of Current English. blast furnace, structure used chiefly in smelting [1].During the purification of iron in a blast furnace, the impurity tetraphosphorus decoxide, P4O10 (l)P4O10 (l), reacts with solid calcium oxide to produce molten calcium phosphate, or slag. Write the balanced equation for this reaction. Include physical states. equation: 6CaO (s)+P4O10 (l) 2Ca3 (PO4)2 (l)6CaO (s)+P4O10 (l) 2Ca3 (PO4)2 (l) If theAnswered: During the purification of iron in a bartleby
احصل على السعر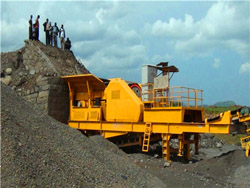
Blast furnace Definition, Temperature, Diagrams, & Facts
Blast furnaces produce pig iron from iron ore by the reducing action of carbon (supplied as coke) at a high temperature in the presence of a fluxing agent such as limestone.Ironmaking blast furnaces consist of several zones: a crucible-shaped hearth at the bottom of the furnace; an intermediate zone called a bosh between the hearth and the stack; a vertical The blast furnace and direct reduction processes have been the major iron production routes for various iron ores (i.e. goethite, hematite, magnetite, maghemite, siderite, etc.) in the past few decades, but the challenges of maintaining the iron and steel-making processes are enormous. The challenges, such as cumbersome production Recent Trends in the Technologies of the Direct Reduction and
احصل على السعر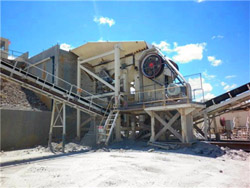
gcse 2. Blast furnace extraction of iron recycling, steel making
2a. Extraction of Iron in a blast furnace. Sadly, now shut down! Raw Materials. Iron Ore e.g. haematite ore (iron(III) oxide) the source of iron.. Fe 2 O 3; or magnetite ore. Fe 3 O 4; coke (carbon, C), both fuel and reducing agent.; hot air (for the oxygen in it) to burn the coke. O 2; limestone (calcium carbonate) to remove certain impurities like silica.Processing iron ore into pellets and making coke are responsible for about 20% of this route’s CO 2 emissions, with the blast furnace itself responsible for about 70%.Can industry decarbonize steelmaking? Chemical & Engineering
احصل على السعر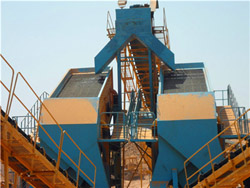
Blast Furnace Reactions SpringerLink
In the blast furnace process, iron ore and reducing agents (i.e. coke) are transformed into hot metal and slag, which is formed from the gangue of the ore and the ash of coke. Hot metal and liquid slag do not mix due to their density difference and remain separate from each other with the slag floating on top of the heavier liquid iron.Blast furnaces have grown considerably in size during the twentieth century. In the early days of the twentieth century, blast furnaces had a hearth diameter of 4–5 m and were producing around 100,000 THM per year, mostly from lump ore and coke. At the end of the twentieth century the biggest blast furnaces had between 14 and 15 m in hearth Blast Furnace an overview ScienceDirect Topics
احصل على السعر