
Breakthrough in Clinker Grinding Massachusetts Institute of
Finish grinding of clinker and other cement ingredients reduces 25 mm clinker balls to particle sizes optimally ranging from 3 to 30 microns. The European This model enables the prediction of the electrical power consumption in clinker grinding (cement production), which contributes significantly to the cement (PDF) CONVENTIONAL CLINKER GRINDING -A NEW
احصل على السعر
(PDF) Clinker grinding process and cement properties
Grinding Aids reduce particle re-agglomeration during and after the milling process so improving the yield. Strength enhancers push clinker reactivity increasing the From the viewpoint of the clinker disintegration process, grinding efficiency is usually specified only within the percentage limits of one-tenth of a unit. Clinker Efficiency of grinding stabilizers in cement clinker
احصل على السعر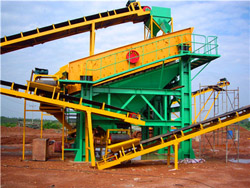
Effects and Control of Chemical Composition of Clinker
Therefore from the chart figure 9 below confirms that chemical composition of cement clinker are critical to energy consumption, because the grinding of cement Cement manufacturers purchasing clinker usually grind it as an addition to their own clinker at their cement plants. Manufacturers also ship clinker to grinding plants in Cement clinker
احصل على السعر
Cement Clinker an overview ScienceDirect Topics
Therefore, the stability temperature range of the mineral is quite narrow (1200–1298°C). When the transitional mineral exists in the clinker, it appears to be of light green colour. The effect of clinker grinding aids (GAs) on mill performance and cement properties is currently quantified in real-scale grinding plants. In fact, laboratory-grinding Quantifying the effect of clinker grinding aids under
احصل على السعر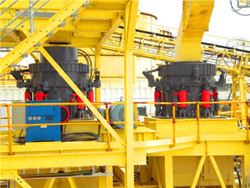
Portland Cement Clinker SpringerLink
The field of Portland cement clinker marked in the system CaO–Al 2 O 3 –SiO 2 lies in principle inside the triangle C 3 S–C 2 S–C 3 A (Fig. 2.15). Fe 2 O 3 was taken together with Al 2 O 3 . All compositions which are laying on left side of the line linking C 3 S with the eutectic T will contain at 1470 °C two solid phases C 3 S and C and the melt.A portland cement clinker, a natural pozzolan, and a granulated blast furnace slag (GBFS) were used to obtain blended cements that contain 25% mineral additives.Effect of grinding time on the particle size distribution
احصل على السعر
low capacity clinker grinder
low capacity clinker grinders low capacity clinker grinders As a leading global manufacturer of crushing and milling equipment, TY (low capacity clinker grinders) offer advanced, rational solutions for any size-reduction requirements, including quarry, aggregate, grinding production and complete plant plan.wty cement clinker should be grinder. wty cement clinker should be grinder Foxing Heavy Machinery. wty cement clinker should be grinder,wty cement clinker should be grinder German Clinker Heavy Industries Plants Dandot Cement Plant was installed in 1982 by State Cement Corporation of Pakistan The plant was supplied and erected by M low capacity clinker grinders
احصل على السعر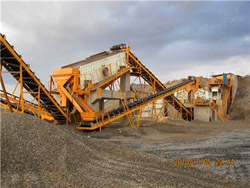
Cement Grinding Plant Overview Cement Grinding Unit AGICO Cement
To reduce transportation costs, the layout of cement production is to build a cement clinker production line in the mining area and establish a cement grinding plant near the cement sales market. If the clinker production line is built near the city, for every 1t of clinker produced, about 1.6t of cement raw material is needed, and the Abstract. This research focused the role to study the effects and ways to control the chemical composition of clinker for better cement production. Cement is a substance produced by grinding a mixture of a clay and limestone and heating to a temperature of 1450°C, in which the chemical transformation occurs inside the kiln to Effects and Control of Chemical Composition of Clinker for Cement
احصل على السعر
Comparison between grinding of cement clinker with and
Figure 1 shows the typical comparison between grinding of cement clinker with and without a grinding aid in a laboratory mill. As discussed in the literature [1,2,4], there was significant effectAs a general rule, there should be less than 25% of clinker that is below 1mm in size. Coarse clinker is more of an issue for ball mills. Some cement groups use a formula, such as Bond’s, to calculate the maximum ball size required in a ball mill, based on the average size of the clinker feed. However, one drawback with this approach is thatClinker size and cement grinding GCP Applied Technologies
احصل على السعر
Detroit clinker grinder Indian Cement Review
The Detroit Clinker Grinder is built for tough operating environments. The rugged construction consists of rigidly stiffened rolled steel housing. The cast Ni-Hard completely lines the grinder enclosure, wear plates and grinder plates. Also, the grinder teeth are Ni-Hard cast and are bolted for easy maintenance. The seals are designed to As a general rule, there should be less than 25% of clinker that is below 1mm in size. Coarse clinker is more of an issue for ball mills. Some cement groups use a formula, such as Bond’s, to calculate Clinker size and cement grinding GCP Applied
احصل على السعر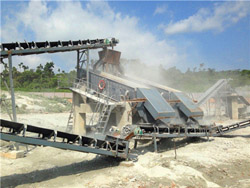
Clinker size and cement grinding GCP Applied Technologies
As a general rule, there should be less than 25% of clinker that is below 1mm in size. Coarse clinker is more of an issue for ball mills. Some cement groups use a formula, such as Bond’s, to calculate the maximum ball size required in a ball mill, based on the average size of the clinker feed. However, one drawback with this approach is thatFinish grinding of clinker and other cement ingredients reduces 25 mm clinker balls to particle sizes optimally ranging from 3 to 30 microns. The European Cement Research Academy (ECRA) estimates that up to 70% of the power consumed in cement production is for material size reduction. Increasing the efficiency of particle size Breakthrough in Clinker Grinding Massachusetts Institute of
احصل على السعر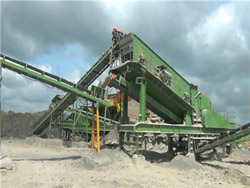
CLINKER GRINDING IN CEMENT PRODUCTION
Value KS K = 92 % indicates that clinker is medium grinded, KS K > 92% easy to grind, KS K <92% hard to grind. The lower value KS K, the larger the clinker. Typical KS K values in Portland cement clinker are 0.8-0.98, or 80-98%. The value KS K of ordinary PortlandThe main focus of this Special Issue is to present the latest and innovative research to provide a deeper understanding of accessing even lower Portland clinker cements, as well as outline future challenges to achieve these goals. Among others, the following topics should be considered: Reactivity and microstructure development; Materials Special Issue : Advances in Low-Clinker Cements MDPI
احصل على السعر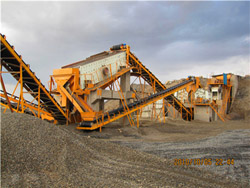
Some tests on the grinding of cement clinker with a Hardinge Conical
duction here; its use as a preliminary grinder is limited • • Coming now to the ball mill, we are reaching the ex perimental stage of milling as applied to cement clinker. Ball mills . and . pebble mills have been used in a number of plants. ~hie . mill in its simplest conception consists of a cylinder revolTingThe energy consumption of the total grinding plant can be reduced by 20–30 % for cement clinker and 30–40 % for other raw materials. The overall grinding circuit efficiency and stability are improved. The maintenance cost of the ball mill is reduced as the lifetime of grinding media and partition grates is extended. 2.5.Energy-Efficient Technologies in Cement Grinding IntechOpen
احصل على السعر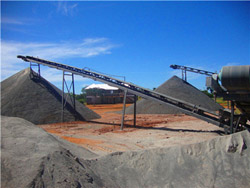
wty cement clinker should be grinder
wty cement clinker should be grinder. Comprehensive understanding of grinding aids Sika. however, possible if the cement is stored for weeks at above 50 °C temperature. This can occur if silos are filled with hot cement. Mostly adsorption of grinding aids is reversible.Indeed, a new Alliance for Low-Carbon Cement & Concrete launched on 30 May in Brussels aims to deliver a zero-carbon cement and concrete value chain by 2040. Supported by Bill Gates’s Breakthrough Energy, an inaugural study modelled a decreasing clinker-to-cement ratio in Europe from 78% in 2020 to 60%, 50% or 40% by 2050, Decarbonising cement: Why the hold-up? Energy Monitor
احصل على السعر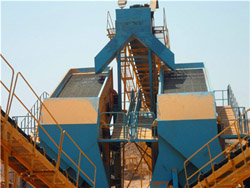
Clinker size and cement grinding GCP Applied Technologies
As a general rule, there should be less than 25% of clinker that is below 1mm in size. Coarse clinker is more of an issue for ball mills. Some cement groups use a formula, such as Bond’s, to calculate the maximum ball size required in a ball mill, based on the average size of the clinker feed.
احصل على السعر