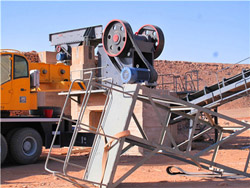
Preparation of reduced iron powder for powder
The Höganäs method is considered the most effective method for producing reduced iron powder (RIP). However, this method does not remove The Höganäs method is considered the most effective method for producing reduced iron powder (RIP). However, this method does not remove Preparation of reduced iron powder for powder metallurgy from
احصل على السعر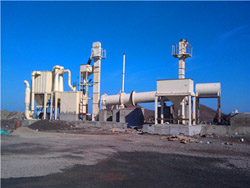
Preparation of high-purity reduced iron powder by Höganäs
Then, using the ultra-pure magnetite concentrate as raw material, high-purity reduced iron powder with Fe grade of 99.06% was prepared by Höganäs process, Hence, we conducted a thermodynamic analysis of different iron ores (hematite and magnetite) reduced by H 2 at 300–1700 K to study the phase-composition variation with temperature.Thermodynamic analysis and experimental verification
احصل على السعر
On Reduction of Iron from Magnetite by Gaseous Reducing Agents
Abstract. The chemical process of iron reduction from magnetite by gaseous reducing agents is the basis of MIDREX technology implemented at the Oskol Preparation of reduced iron powder for powder metallurgy from magnetite concentrate by direct reduction and wet magnetic separation Semantic Preparation of reduced iron powder for powder metallurgy from
احصل على السعر
Iron stored in ferritin is chemically reduced in the
Iron minerals containing iron cations in a low oxidation state, such as magnetite (Fe 3 O 4) and pure ferrous (Fe 2+) minerals (e.g. wustite), as well as zero Abstract. One possible route for ironmaking process is using a hydrogen-gas-based fluidized bed to produce direct reduced iron (DRI), which allows to use the natural magnetite directly in particle Review on the Oxidation Behaviors and Kinetics of
احصل على السعر
Preparation of reduced iron powder for powder metallurgy from magnetite
@article{Yao2021PreparationOR, title={Preparation of reduced iron powder for powder metallurgy from magnetite concentrate by direct reduction and wet magnetic separation}, author={Guangzheng Yao and Yongli Li and Q. Guo and Tao Qi and Zhancheng Guo}, journal={Powder Technology}, year={2021}, volume={392}, Abstract Iron ore, pellets, and sinter were reduced with hydrogen at 800 °C to understand the degree of reduction and the mineralogical aspects. The weight loss of goethite and limonite iron ore was noticed to be lower than that of magnetite and hematite varieties. X-ray diffractometry (XRD) indicated 100 pct Fe in the case of hematite, 93 pct Mineralogical Aspects of Reducing Lump Iron Ore, Pellets, and
احصل على السعر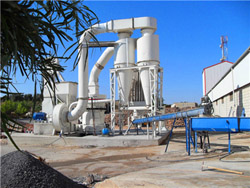
A LABORATORY STUDY OF THE REDUCTION OF IRON OXIDES BY
step, wustite appears as magnetite is consumed but wustite begins to be reduced while magnetite remains until the end. This late presence of magnetite contradicts the X-ray diffraction results and can be attributed to a lower sensitivity of the X-ray analysis. The reduction of wustite is the longest step of the whole reduction process.Analogously, when the magnetite is reduced to wüstite the reaction at the magnetite/wüstite interface can be expressed as: (5) F e 3 O 4 + F e 2 + + 2 e − → 4 F e O In contrast, oxygen atoms must diffuse from the iron/wüstite interface to the iron/gas interface once a dense iron layer forms, Fig. 2 (b) [6, 18].Then, hydrogen reacts with Hierarchical nature of hydrogen-based direct reduction of iron
احصل على السعر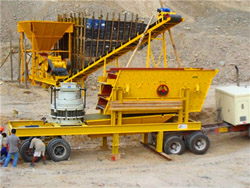
Production of Iron Powder by Solid-Phase Reduction of Fine Magnetite
However, when temperature increases above 570 °C, magnetite is reduced in the sequence Fe 3 O 4 → FeO → Fe, and internal diffusion processes are slowed down by a dense layer of hard-to-reduce wustite (FeO) and then as-reduced iron on the surface of particles .Iron-bearing phases and degrees of reduction are: ( a) Hematite (RD = zero); ( b) magnetite (RD ≈ 11 pct); ( c) wüstite (RD ≈ 30 pct); and ( d) metallic iron (RD ≈ 89 pct) Compressive strength of laboratory samples and industrial DRI pellets with sample mean (cross marker) and 95 pct confidence interval (gray area).Strength of Direct Reduced Iron Following Gas-Based Reduction
احصل على السعر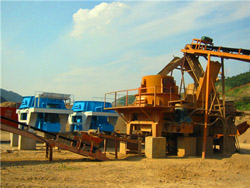
Upgrading Metals Via Direct Reduction from Poly-metallic Titaniferous
Magnetite sinter and pellets are sometimes used as feed in iron-making processes, while direct reduction of magnetite-coal/coke composite pellets show good metallisation over indirect reduction. On the other hand, the reduction of ilmenite followed by leaching of the reduced phase and smelting for the production of pig iron and titanium They stated that magnetite was only reduced to elemental iron by admixture of hydrogen to the methane feed. 8 3 Fe 2 O 3 + CH 4 ⇌ 2 Fe 3 O 4 + CO + 2 H 2. Cetinkaya and Eroglu (2017) investigated the reduction behavior of hematite in undiluted methane at 800–1200 K. The purpose of the study was to establish the process Clean iron production through direct reduction of mineral iron
احصل على السعر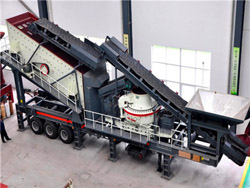
Review on the Oxidation Behaviors and Kinetics of Magnetite
One possible route for ironmaking process is using a hydrogen-gas-based fluidized bed to produce direct reduced iron (DRI), which allows to use the natural magnetite directly in particle scale. The magnetite particles are oxidized during the preheating stage before being charged into the reduction unit.The magnetite concentrate used in this study was collected from an ore dressing plant in China; its chemical composition is listed in Table 1.As can be seen from Table 1, the primary element was Fe, and the grade of iron was 64.86%, which is much lower than that of high-purity magnetite and iron scale.The predominant impurity was Preparation of reduced iron powder for powder metallurgy from magnetite
احصل على السعر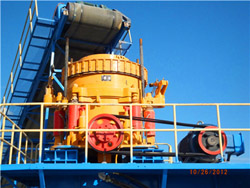
Metals Free Full-Text Parameter Optimization for
Hydrogen-based direct reduced iron (HyDRI) produced by fluidized bed has great potential for achieving the target of net-zero carbon in steelmaking. However, when magnetite ores were used as feedstock, However, studies have shown that when the magnetite is reduced by hydrogen at the temperature of 600–800 °C, the dense metallic iron is formed around the particles’ outer layer, significantly reducing the reaction rate. There is no such hindrance when magnetite is reduced to metallic iron in one step at low temperatures [35, 39, 44, Kinetics and microstructural changes during fluidized reduction of
احصل على السعر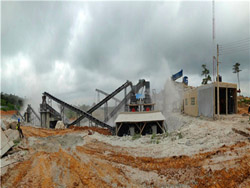
Direct Reduction of Ferrous Oxides to form an Iron
The reduced iron powder is the most widely used material in powder metallurgy industry. The direct reduction process has commonly been used by many companies to obtain metallic iron powder by the Enter green steel which sees renewable hydrogen used as an alternate reducing agent to create Direct Reduced Iron in an electric arc furnace powered by renewables. The processed magnetite concentrate, which is ultimately a high-quality iron ore product, comes into this process because it enables the use of hydrogen as a SA’s Whyalla steelworks hits green steel milestone with first batch
احصل على السعر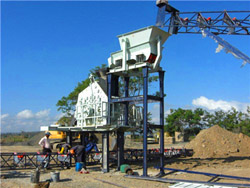
Iron phosphate mediated magnetite synthesis: a bioinspired
Fig. 1 (a) Raman spectra of the ferric phosphate obtained at pH 3 (black), the mixed-valence iron phosphate obtained at pH 6 (red), the ferrous phosphate obtained at pH 6 (blue), the aged final product obtained at pH 12 (pink), and magnetite crystals synthesized as control (green). The band at 670 cm −1 (#) is typical for magnetite, while the band at The hematite transformed to magnetite in the interval of temperature 375–550 °C, many long and cross linking cracks occurred in sinter during this process and lead to serious reduction degradation. The increase of metallic iron content leads to the degradation of sinter got decreased slightly during the stage of temperature above 650 Reduction Behaviors of Sinter Made from Magnetite Springer
احصل على السعر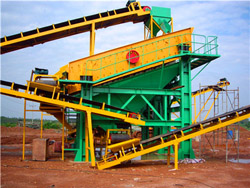
Optimization of the Iron Ore Direct Reduction Process through
Whereas hematite is readily reduced into magnetite as previously reported, magnetite remains present over most of the height, being slowly reduced in the Contrecoeur case and almost not changing in the Gilmore case until the gas inlet. Conversion to wustite and iron only occurs at the zone bottom, with 60% wustite Magnetization roasting is one of the most effective way of utilizing low-grade refractory iron ore. However, the reduction roasting of siderite (FeCO 3) generates weakly magnetic wüstite, thus reducing iron recovery via weak magnetic separation.We systematically studied and proposed the fluidized preoxidation-low-temperature reduction Fluidized magnetization roasting of refractory siderite-containing iron
احصل على السعر
Kinetics of reduction of iron oxides by H ScienceDirect
The reduction of hematite in magnetite by H 2 is characterized by an apparent activation energy of about 76 kJ/mol. 2. The reduction path of magnetite to iron is function of the reaction temperature. At temperatures lower than 420 °C, Fe 3 O 4 is reduced directly to iron. At 450 < T < 570 °C, magnetiteHowever, owing to its high ferric iron content (Fe 3+ /∑Fe), magnetite fractionation should lead to more reduced magma compositions, which is inconsistent with the oxidized compositions of Fe-depleting magmatic series. Alternatively, Fe depletion can be driven by the fractionation of Fe-rich silicates, particularly garnet (Green and Recycling reduced iron at the base of magmatic orogens
احصل على السعر